Application of Brass Casting Process Materials in Automobile Engine Radiators
The development and improvement of automobile engine radiators have long been associated with the continual quest for materials that offer superior heat dissipation, durability, and resistance to corrosion. Brass, an alloy primarily composed of copper and zinc, has found widespread use in various automotive applications, including engine components, heat exchangers, and particularly, in engine radiators. Its unique combination of mechanical properties, ease of casting, and resistance to corrosion has made it an ideal candidate for radiator manufacturing, particularly in applications requiring high thermal conductivity and the ability to withstand harsh operating conditions.
The brass casting process, a method of shaping molten brass into desired forms, has been pivotal in the production of automobile engine radiators. Radiators serve a crucial function in maintaining the optimal operating temperature of the engine by dissipating excess heat through coolant circulation. To achieve this, radiators must be constructed from materials that exhibit high thermal conductivity, strength, and resistance to corrosion due to the continuous exposure to high temperatures, pressurized fluids, and environmental factors such as road salts and water.
This article delves into the brass casting process used in the manufacturing of automobile engine radiators, examining its materials, properties, and benefits, as well as comparing it with other materials such as aluminum and steel commonly used in radiator production. The aim is to provide a comprehensive understanding of why brass casting remains a key process in the automotive industry for radiator production.
Properties of Brass in the Context of Automobile Engine Radiators
Brass, as a casting material, offers a number of beneficial properties that make it suitable for use in automobile engine radiators. The key properties that are particularly relevant to this application include:
-
Thermal Conductivity: Brass has excellent thermal conductivity, though not as high as pure copper. However, its thermal properties are well-suited for heat exchange applications like radiators. The specific heat capacity and thermal conductivity ensure that heat generated by the engine is effectively transferred to the coolant.
-
Corrosion Resistance: Brass exhibits good resistance to corrosion, which is essential when exposed to the harsh operating conditions of an engine radiator. The presence of zinc in brass provides enhanced resistance to oxidation and corrosion, particularly in moist environments where rust formation is a concern.
-
Ductility and Formability: Brass is a highly ductile material that can be easily cast into complex shapes. This is particularly important in the manufacturing of radiator components that require intricate geometries for optimal performance and fluid flow.
-
Strength and Durability: Brass alloys are generally strong and maintain their structural integrity at high temperatures, ensuring that the radiator can withstand the stresses and pressures within the engine compartment without failure.
-
Cost-Effectiveness: Compared to pure copper and some other high-performance materials, brass is relatively cost-effective while still providing good mechanical properties. This makes it a viable choice for mass production of radiators.
-
Ease of Casting: Brass is easier to cast than many other metals due to its lower melting point and favorable flow characteristics when molten. This reduces the energy required for casting and makes it easier to form intricate designs.
Brass Casting Process
The brass casting process involves pouring molten brass into molds to form the desired radiator components. The casting process can be broken down into several stages:
-
Preparation of Materials: The first step in the brass casting process is preparing the raw materials. Brass is typically made by alloying copper with zinc, though other elements like lead, tin, or iron may be added to modify the properties. The specific proportions of copper and zinc depend on the desired characteristics of the final product.
-
Mold Design: A mold is designed based on the radiator's component specifications. In the case of automobile radiators, these components may include the tank, core, and fins, all of which require careful consideration of material flow and cooling rates.
-
Melting and Pouring: The brass alloy is melted in a furnace, and once it reaches the desired temperature (typically between 900°C to 1000°C), it is poured into the prepared mold. During this stage, it is crucial to control the temperature and pouring rate to avoid defects in the cast parts.
-
Cooling and Solidification: As the molten brass cools, it begins to solidify into the shape of the mold. The cooling rate is important to control to ensure that the brass solidifies evenly and that no defects like shrinkage cavities or cracks form.
-
Finishing: After the cast parts have cooled and solidified, they are removed from the mold. Any excess material is trimmed, and surface imperfections are smoothed out through various finishing techniques, such as grinding or polishing. In some cases, parts may undergo further treatment, such as heat treatment, to enhance their mechanical properties.
-
Inspection and Testing: Once finished, the cast brass components are subjected to rigorous inspection and testing to ensure that they meet the required standards. This can include visual inspections, dimensional checks, and tests for material strength, corrosion resistance, and thermal conductivity.
Comparative Analysis of Brass, Aluminum, and Steel in Radiator Manufacturing
Brass is not the only material used in the manufacture of automobile engine radiators. Two other common materials, aluminum and steel, also see widespread use. Each material has its own set of advantages and limitations when it comes to radiator construction.
Table 1: Comparative Properties of Brass, Aluminum, and Steel
Property | Brass | Aluminum | Steel |
---|---|---|---|
Thermal Conductivity | Moderate (120 W/m·K) | High (205 W/m·K) | Low (50 W/m·K) |
Corrosion Resistance | High (resistant to rust and oxidation) | Moderate (susceptible to oxidation but can be coated) | Low (prone to rusting, requires coating) |
Strength | Moderate | Low (depending on alloy) | High (stronger than brass) |
Ductility | High (easy to form) | Moderate | Low (less ductile) |
Casting Ease | Easy (low melting point) | Moderate (requires higher melting temperature) | Difficult (requires higher melting point) |
Cost | Moderate | Low (more affordable) | Low to moderate |
Weight | Heavy (denser material) | Light (lower density) | Heavy (dense) |
Manufacturing Ease | High (excellent for casting) | High (easy to extrude, but harder to cast) | Low (less efficient for complex shapes) |
Table 2: Material Selection for Radiators Based on Operating Conditions
Operating Condition | Brass | Aluminum | Steel |
---|---|---|---|
High Temperature Resistance | Good (retains strength at high temperatures) | Excellent (can withstand higher temperatures) | Excellent (good strength retention) |
Corrosion Resistance in Moist Environments | Very Good (ideal for wet conditions) | Moderate (prone to corrosion without coatings) | Poor (rusts easily without coating) |
Ease of Casting | Very Good (ideal for casting intricate shapes) | Good (good for extrusions, but difficult for casting) | Poor (requires high heat and precision) |
Cost Efficiency | Moderate | Low (most cost-effective) | Low (affordable, but less efficient) |
Weight Considerations | Heavy (adds weight to the vehicle) | Light (saves on vehicle weight) | Heavy (adds weight to the vehicle) |
Advantages of Brass Casting in Engine Radiators
-
Durability: Brass radiators are known for their longevity, particularly in environments where corrosion is a concern. Unlike aluminum, brass can resist the effects of road salts and other harsh environmental factors, making it particularly useful in regions with extreme weather conditions.
-
Heat Transfer: While aluminum is a better conductor of heat, brass’s thermal properties are still sufficient for automotive applications. Brass has a higher heat capacity than steel, meaning it can store more heat before reaching critical temperatures.
-
Corrosion Resistance: Brass is highly resistant to corrosion, which is vital for radiators exposed to coolant, road salt, and other corrosive elements. This longevity and resistance to degradation help maintain the radiator’s efficiency over the life of the vehicle.
Conclusion
The brass casting process remains a critical method in the production of automobile engine radiators due to its combination of high thermal conductivity, corrosion resistance, and ease of fabrication. While alternatives such as aluminum and steel offer their own unique advantages, brass remains a strong contender due to its balance of properties and cost-effectiveness. The application of brass casting in the automotive industry continues to evolve, and with ongoing advancements in alloy composition and casting technology, it is likely that brass will continue to play an important role in the future of radiator manufacturing.
Reprint Statement: If there are no special instructions, all articles on this site are original. Please indicate the source for reprinting:https://www.cncmachiningptj.com/,thanks!
3, 4 and 5-axis precision CNC machining services for aluminum machining, beryllium, carbon steel, magnesium, titanium machining, Inconel, platinum, superalloy, acetal, polycarbonate, fiberglass, graphite and wood. Capable of machining parts up to 98 in. turning dia. and +/-0.001 in. straightness tolerance. Processes include milling, turning, drilling, boring, threading, tapping, forming, knurling, counterboring, countersinking, reaming and laser cutting. Secondary services such as assembly, centerless grinding, heat treating, plating and welding. Prototype and low to high volume production offered with maximum 50,000 units. Suitable for fluid power, pneumatics, hydraulics and valve applications. Serves the aerospace, aircraft, military, medical and defense industries.PTJ will strategize with you to provide the most cost-effective services to help you reach your target,Welcome to Contact us ( sales@pintejin.com ) directly for your new project.
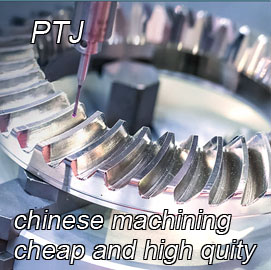
- 5 Axis Machining
- Cnc Milling
- Cnc Turning
- Machining Industries
- Machining Process
- Surface Treatment
- Metal Machining
- Plastic Machining
- Powder Metallurgy Mold
- Die Casting
- Parts Gallery
- Auto Metal Parts
- Machinery Parts
- LED Heatsink
- Building Parts
- Mobile Parts
- Medical Parts
- Electronic Parts
- Tailored Machining
- Bicycle Parts
- Aluminum Machining
- Titanium Machining
- Stainless Steel Machining
- Copper Machining
- Brass Machining
- Super Alloy Machining
- Peek Machining
- UHMW Machining
- Unilate Machining
- PA6 Machining
- PPS Machining
- Teflon Machining
- Inconel Machining
- Tool Steel Machining
- More Material