Application of Information Management in the Powder Metallurgy Industry
Information management (IM) is an essential aspect of modern manufacturing industries, providing the backbone for efficient decision-making, operations, and innovation. In the powder metallurgy (PM) industry, which deals with the manufacturing of components by compacting and sintering metal powders, information management has emerged as a critical enabler of process optimization, quality control, and production efficiency. The effective use of information systems allows for the seamless integration of various stages in PM, from powder production and mixing to compaction, sintering, and post-processing.
This article examines the role of information management in the powder metallurgy industry, highlighting its impact on various operations such as process control, inventory management, supply chain coordination, quality assurance, and product traceability. Furthermore, it explores the technological advances that have facilitated the adoption of information management systems (IMS) in PM, including automation, data analytics, and cloud computing.
Evolution of Information Management in the Powder Metallurgy Industry
The history of information management in the powder metallurgy industry is deeply tied to the advancements in industrial automation and data processing. Early practices in PM were largely manual, relying on skilled workers to monitor and control various process parameters. However, as the demand for more complex and precise components increased, so did the need for more sophisticated information management systems.
Pre-Digital Era
Before the advent of digital technologies, the PM industry primarily relied on paper-based records, manual calculations, and direct observation of machinery. Operators would manually log parameters such as temperature, pressure, and time during sintering, compaction, and other critical processes. Although this approach allowed for some level of control, it was highly labor-intensive and prone to human error.
Digital Transformation and the Rise of Computerized Systems
The introduction of computers in the 1980s marked the beginning of a digital transformation in the powder metallurgy sector. Computerized systems allowed for real-time monitoring and data collection, enabling more precise control over the manufacturing process. Information management systems began to evolve, integrating data from various sources such as sensors, machines, and quality control equipment.
By the 1990s, the development of integrated software solutions, such as Manufacturing Execution Systems (MES) and Enterprise Resource Planning (ERP) systems, enabled manufacturers to track production schedules, inventory levels, and supply chain activities. These systems played a pivotal role in streamlining operations, reducing costs, and enhancing the overall efficiency of the production process.
The Modern Era: Big Data and Industry 4.0
In recent years, the PM industry has entered a new phase characterized by the widespread adoption of Industry 4.0 technologies, including the Internet of Things (IoT), machine learning, and cloud computing. These technologies have enabled the PM industry to collect and analyze vast amounts of data, improving predictive maintenance, process optimization, and product development. The integration of data from machines, operators, and supply chains allows manufacturers to achieve unprecedented levels of transparency and efficiency.
Key Applications of Information Management in Powder Metallurgy
1. Process Control and Optimization
One of the most critical applications of information management in powder metallurgy is process control. Powder metallurgy involves several complex stages, including powder production, blending, compaction, and sintering. Each of these stages requires precise control over a variety of parameters such as temperature, pressure, time, and material properties. Information management systems provide the necessary infrastructure to collect, analyze, and act on this data in real time, ensuring that each step in the production process is optimized for maximum quality and efficiency.
Role of Sensors and Data Acquisition
Sensors play a crucial role in process control by providing real-time data on key parameters. In powder metallurgy, common sensors include thermocouples for temperature monitoring, load cells for measuring pressure during compaction, and displacement sensors for tracking the movement of components during sintering. Information management systems integrate these sensors into a centralized network, allowing operators to monitor and control the entire process from a single interface.
Process Optimization Algorithms
Advanced algorithms, often powered by machine learning and artificial intelligence, enable the continuous optimization of powder metallurgy processes. These algorithms can predict the optimal settings for different process parameters based on historical data, reducing variability and improving overall product quality. For example, a machine learning model might predict the best sintering temperature for a specific batch of powder based on factors such as powder composition, part geometry, and environmental conditions.
2. Quality Assurance and Control
In the powder metallurgy industry, maintaining high-quality standards is essential for ensuring that components meet stringent performance requirements. Information management plays a vital role in quality assurance (QA) by enabling real-time monitoring of quality parameters and automating the detection of deviations from specifications.
Real-Time Monitoring and Feedback Loops
Quality control systems in PM often involve real-time monitoring of material properties, such as density, porosity, and tensile strength. Information management systems can integrate data from quality control instruments, such as X-ray fluorescence (XRF) analyzers and metallurgical microscopes, to automatically detect deviations from target values. When a deviation is detected, the system can trigger an immediate feedback loop, alerting operators to take corrective action before defects occur.
Statistical Process Control (SPC)
Statistical process control (SPC) techniques, which involve the use of control charts and other statistical tools, are widely used in the powder metallurgy industry to monitor the stability of production processes. Information management systems automate the collection and analysis of data for SPC, enabling operators to quickly identify trends and make data-driven decisions to maintain product quality.
3. Supply Chain and Inventory Management
In powder metallurgy, the supply chain plays a critical role in ensuring that the right materials are available at the right time. Information management systems help streamline supply chain operations by providing real-time visibility into inventory levels, order status, and production schedules.
Material Tracking and Traceability
One of the key benefits of information management in PM is enhanced traceability. From the moment metal powders are sourced to their final use in a component, information systems track every step of the process. This traceability ensures that manufacturers can track the provenance of materials and verify compliance with industry standards, regulations, and customer specifications.
Just-In-Time (JIT) Inventory
Just-In-Time (JIT) inventory management, which aims to reduce inventory costs by ordering materials only when needed, is increasingly adopted in powder metallurgy. Information management systems play a crucial role in JIT by providing real-time data on material usage rates, order status, and supplier lead times. This allows manufacturers to reduce waste and minimize storage costs while maintaining the flexibility to respond to customer demands.
4. Research and Development (R&D) Support
The powder metallurgy industry is highly innovation-driven, with ongoing research into new materials, alloys, and manufacturing techniques. Information management systems provide a robust platform for supporting R&D activities by enabling the efficient collection, analysis, and sharing of experimental data.
Data-Driven Materials Research
R&D in powder metallurgy often involves experimenting with new powder compositions and processing techniques. Information management systems allow researchers to collect and analyze large datasets, helping them identify trends and correlations that might not be immediately apparent. By centralizing research data in a single platform, these systems facilitate collaboration between research teams and enable faster decision-making.
Simulation and Modeling Tools
Advanced simulation and modeling tools, which are integrated into information management systems, are commonly used in the powder metallurgy industry to predict the behavior of materials under different conditions. These tools can simulate various stages of the manufacturing process, including powder flow, compaction, and sintering, helping engineers optimize process parameters before moving to physical trials.
Challenges and Limitations of Information Management in Powder Metallurgy
While information management systems offer significant benefits to the powder metallurgy industry, there are also several challenges associated with their implementation and use.
1. High Initial Investment
The implementation of advanced information management systems in powder metallurgy often requires a significant initial investment in hardware, software, and training. Small and medium-sized enterprises (SMEs) may struggle to afford these costs, limiting their ability to fully leverage the benefits of digital transformation.
2. Data Security and Privacy Concerns
As information management systems in PM rely heavily on digital platforms and cloud computing, ensuring data security and privacy is a critical concern. Manufacturers must take steps to protect sensitive data, such as proprietary formulas, customer orders, and production schedules, from cyber threats and unauthorized access.
3. Integration with Legacy Systems
Many powder metallurgy companies continue to rely on legacy systems that may not be fully compatible with modern information management solutions. Integrating new systems with existing infrastructure can be a complex and time-consuming process, requiring specialized expertise and resources.
Reprint Statement: If there are no special instructions, all articles on this site are original. Please indicate the source for reprinting:https://www.cncmachiningptj.com/,thanks!
3, 4 and 5-axis precision CNC machining services for aluminum machining, beryllium, carbon steel, magnesium, titanium machining, Inconel, platinum, superalloy, acetal, polycarbonate, fiberglass, graphite and wood. Capable of machining parts up to 98 in. turning dia. and +/-0.001 in. straightness tolerance. Processes include milling, turning, drilling, boring, threading, tapping, forming, knurling, counterboring, countersinking, reaming and laser cutting. Secondary services such as assembly, centerless grinding, heat treating, plating and welding. Prototype and low to high volume production offered with maximum 50,000 units. Suitable for fluid power, pneumatics, hydraulics and valve applications. Serves the aerospace, aircraft, military, medical and defense industries.PTJ will strategize with you to provide the most cost-effective services to help you reach your target,Welcome to Contact us ( sales@pintejin.com ) directly for your new project.
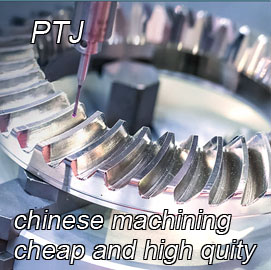
- 5 Axis Machining
- Cnc Milling
- Cnc Turning
- Machining Industries
- Machining Process
- Surface Treatment
- Metal Machining
- Plastic Machining
- Powder Metallurgy Mold
- Die Casting
- Parts Gallery
- Auto Metal Parts
- Machinery Parts
- LED Heatsink
- Building Parts
- Mobile Parts
- Medical Parts
- Electronic Parts
- Tailored Machining
- Bicycle Parts
- Aluminum Machining
- Titanium Machining
- Stainless Steel Machining
- Copper Machining
- Brass Machining
- Super Alloy Machining
- Peek Machining
- UHMW Machining
- Unilate Machining
- PA6 Machining
- PPS Machining
- Teflon Machining
- Inconel Machining
- Tool Steel Machining
- More Material