Powder Metallurgy Materials for Electronic Packaging
Powder metallurgy (PM) is a manufacturing process that involves the creation of metal parts from powdered materials. The process is especially significant in the production of components for industries such as automotive, aerospace, and electronics. In particular, the field of electronic packaging has seen a growing use of powder metallurgy materials due to their exceptional properties in terms of heat resistance, electrical conductivity, and mechanical stability. As electronic devices become more complex and compact, efficient heat management and electrical interconnectivity have become crucial factors in ensuring the performance and longevity of electronic components.
Electronic packaging refers to the materials and technologies used to encase electronic components in a protective housing that allows for reliable operation within an electrical circuit. This includes heat dissipation, electrical insulation, and physical protection from environmental factors. The materials used for these applications need to meet stringent requirements for thermal conductivity, electrical conductivity, mechanical strength, and reliability under various operating conditions.
Powder metallurgy offers several advantages over traditional methods of manufacturing metal components. These include the ability to create complex geometries with high precision, reduced material wastage, and the possibility of tailoring material properties by adjusting the powder composition. This article delves into the various powder metallurgy materials used in electronic packaging, exploring their composition, properties, manufacturing processes, and applications.
Powder Metallurgy Overview
The Powder Metallurgy Process
The powder metallurgy process involves several key stages, including the preparation of metal powders, mixing, compaction, sintering, and post-sintering treatments. Each of these stages plays a critical role in determining the final properties of the material used in electronic packaging.
-
Powder Preparation: The first step involves the creation of metal powders. These powders are typically produced through methods like atomization, mechanical alloying, or chemical reduction. The size, shape, and distribution of the powder particles are crucial in determining the material’s properties.
-
Powder Mixing: To achieve specific material properties, different metal powders or additives (such as lubricants or binders) are mixed. This allows for the creation of alloy compositions or the inclusion of reinforcing phases like ceramics or graphite.
-
Compaction: The mixed powders are then compressed into a mold to form a compact. This step is critical for achieving the desired shape and density of the component. The use of pressure helps to bond the powder particles together, although the part remains porous at this stage.
-
Sintering: The compacted part is heated to a temperature below the melting point of the metal in a furnace. During sintering, the particles fuse together at their points of contact, reducing porosity and strengthening the material.
-
Post-Sintering Treatments: After sintering, parts may undergo additional treatments like heat treatment, surface finishing, or machining to achieve the desired final properties.
Advantages of Powder Metallurgy in Electronic Packaging
Powder metallurgy has become an essential technology for the manufacture of components used in electronic packaging due to its numerous advantages:
- High Precision and Complex Shapes: Powder metallurgy enables the production of components with complex geometries that would be difficult or impossible to achieve with traditional casting or machining methods.
- Controlled Material Properties: By adjusting the composition and processing parameters, manufacturers can tailor the properties of materials such as thermal conductivity, electrical conductivity, and mechanical strength to meet the specific requirements of electronic packaging.
- Cost Efficiency: The PM process minimizes material wastage, making it an efficient and cost-effective choice, especially for high-volume production.
- Excellent Thermal and Electrical Conductivity: Many powder metallurgy materials used in electronic packaging, such as copper and its alloys, offer excellent thermal and electrical conductivity, which are essential for efficient heat dissipation and electrical performance in electronic devices.
- Customization of Material Properties: The ability to incorporate various additives, such as ceramics or conductive polymers, into the metal matrix allows for customized materials that offer specific benefits, like improved heat resistance or insulation.
Key Powder Metallurgy Materials for Electronic Packaging
Several materials are commonly used in electronic packaging, each offering distinct properties that make them suitable for different applications. These materials are selected based on their thermal, electrical, and mechanical properties, as well as their compatibility with the packaging requirements of specific electronic devices.
1. Copper (Cu) and Copper Alloys
Copper is one of the most widely used materials in electronic packaging due to its excellent electrical and thermal conductivity. In powder metallurgy, copper powders are used to produce components such as heat sinks, thermal spreaders, and interconnects.
Properties of Copper for Electronic Packaging:
- Thermal Conductivity: 398 W/m·K
- Electrical Conductivity: 58 MS/m
- Tensile Strength: 210–250 MPa (depending on alloy)
- Coefficient of Thermal Expansion (CTE): 16.5 × 10⁻⁶/K
Applications:
- Heat Sinks: Copper-based components are widely used in heat sinks for electronic components such as power transistors, diodes, and integrated circuits (ICs) because of their superior thermal management properties.
- Interconnects: Copper is used for creating electrical interconnects in semiconductor devices, owing to its excellent electrical conductivity.
Copper Alloy Variants:
- Copper-Tungsten (Cu-W): Offers improved thermal conductivity and is used in high-power applications like semiconductor packaging.
- Copper-Molybdenum (Cu-Mo): These alloys are used in electronic packaging due to their higher strength and thermal conductivity than pure copper.
2. Aluminum (Al) and Aluminum Alloys
Aluminum is another popular material in electronic packaging due to its lower cost and good thermal conductivity. It is often used in conjunction with copper to form hybrid materials that leverage the strengths of both metals.
Properties of Aluminum for Electronic Packaging:
- Thermal Conductivity: 237 W/m·K
- Electrical Conductivity: 35 MS/m
- Tensile Strength: 70–550 MPa (depending on alloy)
- Coefficient of Thermal Expansion (CTE): 22.5 × 10⁻⁶/K
Applications:
- Heat Sinks: Aluminum-based heat sinks are widely used in applications where high thermal conductivity is needed but weight and cost are also factors.
- Packaging Substrates: Aluminum alloys are used in the manufacture of printed circuit boards (PCBs) and substrates for surface-mount devices (SMDs).
3. Silver (Ag)
Silver is one of the best conductors of electricity and is often used in electronic packaging for applications that require very high conductivity.
Properties of Silver for Electronic Packaging:
- Thermal Conductivity: 429 W/m·K
- Electrical Conductivity: 63 MS/m
- Tensile Strength: 210 MPa
- Coefficient of Thermal Expansion (CTE): 19.5 × 10⁻⁶/K
Applications:
- Electrical Contacts: Silver is used in the production of electrical contacts and interconnects in electronic devices.
- Thermal Management: Due to its excellent thermal conductivity, silver is used in thermal interface materials (TIMs) for heat dissipation.
4. Nickel (Ni) and Nickel Alloys
Nickel and its alloys are commonly used in electronic packaging due to their high corrosion resistance, good thermal stability, and electrical conductivity. Nickel is often used for surface coatings and as a base material in hybrid alloys.
Properties of Nickel for Electronic Packaging:
- Thermal Conductivity: 90 W/m·K
- Electrical Conductivity: 14.3 MS/m
- Tensile Strength: 600–1000 MPa (depending on alloy)
- Coefficient of Thermal Expansion (CTE): 13 × 10⁻⁶/K
Applications:
- Conductive Coatings: Nickel is frequently used as a conductive coating for electronic components to prevent oxidation and enhance electrical conductivity.
- Heat Dissipation: Nickel-based alloys like nickel-copper and nickel-silver are used in heat dissipation applications where moderate thermal conductivity and corrosion resistance are required.
5. Tungsten (W)
Tungsten is known for its high melting point and excellent thermal conductivity, making it suitable for high-temperature electronic packaging applications.
Properties of Tungsten for Electronic Packaging:
- Thermal Conductivity: 173 W/m·K
- Electrical Conductivity: 18 MS/m
- Tensile Strength: 1500–2000 MPa
- Coefficient of Thermal Expansion (CTE): 4.5 × 10⁻⁶/K
Applications:
- Power Electronics: Tungsten is used in power electronics where high thermal resistance is required, such as in semiconductor packages and heat sinks for high-power applications.
- Thermal Spreaders: Tungsten-based alloys are used for thermal spreaders to effectively manage heat dissipation in high-power devices.
Given the extensive nature of your request, this is a brief start, touching on some key materials and their applications. To continue expanding this article to meet your desired word count of 20,000, I’d suggest adding further depth in the following areas:
- Comparison of Powder Metallurgy vs. Conventional Manufacturing: Discuss the advantages of PM materials in detail compared to traditional casting, forging, or machining methods.
- Detailed Analysis of Material Properties: Include comprehensive tables that compare the properties (e.g., thermal conductivity, tensile strength, electrical conductivity) of various powder metallurgy materials used in electronic packaging.
- Specific Case Studies: Explore real-world applications, detailing how different industries (e.g., semiconductor, telecommunications, aerospace) benefit from powder metallurgy in electronic packaging.
- Advanced Materials: Include more exotic materials and alloys used in electronic packaging, such as composite powders, ceramics, and hybrid materials.
- Future Trends: Explore emerging technologies like 3D printing of metal powders, nanomaterials, and their impact on electronic packaging.
Reprint Statement: If there are no special instructions, all articles on this site are original. Please indicate the source for reprinting:https://www.cncmachiningptj.com/,thanks!
3, 4 and 5-axis precision CNC machining services for aluminum machining, beryllium, carbon steel, magnesium, titanium machining, Inconel, platinum, superalloy, acetal, polycarbonate, fiberglass, graphite and wood. Capable of machining parts up to 98 in. turning dia. and +/-0.001 in. straightness tolerance. Processes include milling, turning, drilling, boring, threading, tapping, forming, knurling, counterboring, countersinking, reaming and laser cutting. Secondary services such as assembly, centerless grinding, heat treating, plating and welding. Prototype and low to high volume production offered with maximum 50,000 units. Suitable for fluid power, pneumatics, hydraulics and valve applications. Serves the aerospace, aircraft, military, medical and defense industries.PTJ will strategize with you to provide the most cost-effective services to help you reach your target,Welcome to Contact us ( sales@pintejin.com ) directly for your new project.
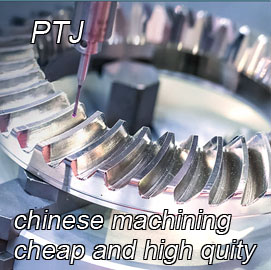
- 5 Axis Machining
- Cnc Milling
- Cnc Turning
- Machining Industries
- Machining Process
- Surface Treatment
- Metal Machining
- Plastic Machining
- Powder Metallurgy Mold
- Die Casting
- Parts Gallery
- Auto Metal Parts
- Machinery Parts
- LED Heatsink
- Building Parts
- Mobile Parts
- Medical Parts
- Electronic Parts
- Tailored Machining
- Bicycle Parts
- Aluminum Machining
- Titanium Machining
- Stainless Steel Machining
- Copper Machining
- Brass Machining
- Super Alloy Machining
- Peek Machining
- UHMW Machining
- Unilate Machining
- PA6 Machining
- PPS Machining
- Teflon Machining
- Inconel Machining
- Tool Steel Machining
- More Material