The Sub-Thermal Carbonitriding Of Iron-Based Powder Metallurgy Parts
The sub-thermal carbonitriding of iron-based powder metallurgy parts is an advanced heat treatment process that modifies the surface properties of these parts by introducing carbon and nitrogen into the material at lower temperatures. This process is specifically designed to improve the hardness, wear resistance, and fatigue strength of the surface without significantly altering the core properties of the part. The term "sub-thermal" refers to the fact that the process occurs at temperatures lower than those typically associated with traditional carbonitriding, which generally operates at higher temperatures, usually above 800°C. Sub-thermal carbonitriding is typically conducted in the range of 400-600°C, a temperature window that is particularly advantageous for iron-based powder metallurgy (PM) parts, as it avoids the risk of sintering and preserves the integrity of the porosity that is inherent to these materials.
Background of Iron-Based Powder Metallurgy Parts
Iron-based powder metallurgy parts are commonly used in various industrial applications due to their excellent mechanical properties, cost-effectiveness, and versatility in production. These parts are created by compacting metal powders, such as iron, along with various alloying elements, into a desired shape and then sintering them at a high temperature to create a solid material. This method allows for the production of complex geometries and parts with specific properties that may be difficult or impossible to achieve through traditional casting or machining methods.
The typical applications of iron-based powder metallurgy parts include automotive components (such as gears, bearings, and bushings), electrical components (such as transformers and magnetic parts), and aerospace parts. These parts benefit from the unique characteristics of powder metallurgy, such as the ability to tailor material properties by adjusting the composition and processing conditions.
Carbonitriding Process Overview
Carbonitriding is a surface hardening process that involves the simultaneous diffusion of carbon and nitrogen into the surface of a material, typically steel, to enhance its hardness, wear resistance, and fatigue strength. The process is carried out at temperatures below the transformation temperature of the steel, typically in the range of 750-950°C. However, in sub-thermal carbonitriding, the temperatures are deliberately kept lower, generally between 400°C and 600°C, to achieve specific material properties without compromising the underlying structure of the part.
The process involves exposing the iron-based powder metallurgy part to a gaseous atmosphere containing both carbon and nitrogen sources. The carbon source is usually a hydrocarbon gas, such as methane or propane, while the nitrogen source is typically ammonia. The gases are introduced into a sealed furnace, where they dissociate into their atomic components. The atomic carbon and nitrogen atoms then diffuse into the surface of the part, forming hard compounds such as iron carbides and iron nitrides.
The temperature range of sub-thermal carbonitriding ensures that the process does not reach the higher temperatures that would cause grain growth, shrinkage, or sintering of the iron-based powder metallurgy parts. This allows for a more controlled diffusion process and the retention of the material's porosity, which is essential for certain applications that require high surface-area-to-volume ratios, such as porous bearings and filters.
Mechanisms of Sub-Thermal Carbonitriding
The fundamental mechanisms of sub-thermal carbonitriding involve the diffusion of carbon and nitrogen into the surface layers of the part. Carbon and nitrogen atoms diffuse into the surface of the part through a process known as "ion implantation." During the treatment, atomic species are generated by the dissociation of the carbon and nitrogen gases at the furnace temperature. These atoms then migrate into the surface of the iron-based material, where they interact with the metal's crystal lattice.
At the temperatures used in sub-thermal carbonitriding, the atomic carbon and nitrogen atoms combine with iron atoms to form iron carbide (Fe₃C) and iron nitride (Fe₄N) compounds. These compounds provide enhanced surface hardness and wear resistance, which are particularly beneficial for parts that undergo sliding or rolling contact. Additionally, the introduction of nitrogen into the surface can result in the formation of a thin, dense oxide layer, further improving corrosion resistance.
The diffusion of carbon and nitrogen is not uniform across the material surface. The concentration of these elements typically decreases with increasing depth from the surface. The gradient of carbon and nitrogen concentration can be tailored by adjusting the process parameters, such as temperature, time, and gas composition, to achieve the desired surface hardness profile.
Benefits of Sub-Thermal Carbonitriding for Iron-Based PM Parts
Sub-thermal carbonitriding offers several advantages for iron-based powder metallurgy parts, particularly in the context of improving their surface properties without compromising their internal structure or material integrity. Some of the key benefits include:
-
Enhanced Surface Hardness: The formation of iron carbide and iron nitride compounds during the carbonitriding process results in a significant increase in surface hardness. This is particularly beneficial for parts that are subject to wear, such as gears and bearings, as it improves their performance and lifespan.
-
Improved Wear Resistance: The diffusion of carbon and nitrogen into the surface layer creates a harder, more wear-resistant surface, which is ideal for components that experience abrasive contact or sliding wear. This is especially important for iron-based PM parts, which may otherwise suffer from poor wear resistance due to their inherent porosity.
-
Fatigue Strength: The carbonitriding process can significantly improve the fatigue strength of iron-based powder metallurgy parts. The increased surface hardness and the presence of compressive residual stresses introduced by the treatment enhance the material's resistance to crack initiation and propagation under cyclic loading.
-
Retention of Porosity: Unlike conventional heat treatment processes that might cause the sintered powder structure to collapse or densify, sub-thermal carbonitriding is designed to preserve the material's porosity. This is particularly beneficial for parts that require a high surface-area-to-volume ratio, such as porous bearings, filters, and medical implants.
-
Enhanced Corrosion Resistance: The introduction of nitrogen into the surface can result in the formation of a passive oxide layer that provides additional corrosion resistance, which is essential for parts exposed to harsh environments, such as automotive or aerospace components.
-
Low Temperature Processing: Since sub-thermal carbonitriding occurs at lower temperatures than traditional carbonitriding, it avoids some of the problems associated with high-temperature treatments, such as grain growth, distortion, or loss of dimensional accuracy. This makes it particularly suitable for components with complex geometries or parts that are sensitive to temperature-induced changes in shape.
Factors Influencing the Sub-Thermal Carbonitriding Process
Several factors influence the outcome of the sub-thermal carbonitriding process, including:
-
Temperature: The temperature at which the carbonitriding process is carried out directly affects the rate of diffusion of carbon and nitrogen into the surface of the part. Higher temperatures generally result in faster diffusion rates, leading to deeper case depths and harder surfaces. However, temperatures that are too high can result in undesirable effects, such as sintering or grain growth.
-
Time: The duration of the treatment also plays a crucial role in determining the depth of the case and the level of surface hardness. Longer treatment times allow for greater diffusion of carbon and nitrogen, leading to a deeper case and higher surface hardness. However, excessively long treatment times can lead to overcarburization or nitride formation, which can adversely affect the material's properties.
-
Gas Composition: The composition of the carbon and nitrogen gases used during the carbonitriding process influences the amount of carbon and nitrogen that diffuses into the part. Typically, a mixture of methane or propane (for carbon) and ammonia (for nitrogen) is used. The ratio of these gases can be adjusted to achieve the desired surface composition and hardness profile.
-
Atmosphere Control: The control of the furnace atmosphere is crucial to achieving consistent results in the carbonitriding process. Maintaining a stable atmosphere and ensuring uniform distribution of gases are critical for obtaining a uniform case depth and hardness across the part.
-
Part Geometry and Size: The shape and size of the part being treated can influence the effectiveness of the carbonitriding process. For example, larger parts may experience non-uniform heating or gas exposure, leading to variations in surface hardness. Additionally, parts with intricate geometries may be more prone to distortion or incomplete treatment.
-
Cooling Rate: The cooling rate after the carbonitriding treatment can also affect the material properties. Slow cooling can lead to the formation of residual stresses, while rapid cooling (quenching) may cause cracking or distortion. Therefore, controlling the cooling rate is essential to achieving optimal results.
Tables for Comparison
The following tables summarize the differences between sub-thermal carbonitriding and conventional carbonitriding, as well as the impact of various process parameters on the surface properties of iron-based powder metallurgy parts.
Table 1: Comparison of Sub-Thermal and Conventional Carbonitriding
Property | Sub-Thermal Carbonitriding | Conventional Carbonitriding |
---|---|---|
Temperature Range | 400-600°C | 750-950°C |
Case Depth | Shallow (< 0.3 mm) | Deep (> 1 mm) |
Surface Hardness | Moderate (HV 600-750) | High (HV 800-1000) |
Preservation of Porosity | Retained | Lost |
Fatigue Strength Improvement | Moderate | High |
Corrosion Resistance | Moderate | High |
Application Suitability | Wear-resistant components with complex geometries | High-strength parts requiring deep case hardening |
Table 2: Effect of Process Parameters on Carbonitriding
Parameter | Low Temperature (400°C) | High Temperature (600°C) |
---|---|---|
Carbon Diffusion Rate | Slow | Fast |
Nitrogen Diffusion Rate | Slow | Fast |
Case Depth | Shallow (< 0.2 mm) | Deeper (> 0.5 mm) |
Surface Hardness | Moderate (HV 600-700) | High (HV 700-800) |
Fatigue Strength | Moderate | High |
Wear Resistance | Moderate | High |
Applications and Industry Relevance
Sub-thermal carbonitriding of iron-based powder metallurgy parts is particularly advantageous in industries where high-performance, wear-resistant components are required, but the preservation of the material's core properties and geometry is essential. Some of the key industries benefiting from this process include:
-
Automotive Industry: Gears, bushings, and bearings made from iron-based powder metallurgy parts can be treated using sub-thermal carbonitriding to improve wear resistance and fatigue strength without compromising the material's shape or dimensional accuracy.
-
Aerospace Industry: Components exposed to high stresses and harsh environmental conditions, such as turbine blades and landing gear parts, can benefit from the enhanced surface properties provided by sub-thermal carbonitriding.
-
Medical Devices: Medical implants and surgical tools made from powder metallurgy parts benefit from the corrosion resistance and biocompatibility that can be achieved through this treatment.
-
Electronics and Electrical Industry: Magnetic components, transformer cores, and other electrical parts can benefit from the improved wear resistance and mechanical properties provided by sub-thermal carbonitriding.
Conclusion
Sub-thermal carbonitriding is a valuable heat treatment process for iron-based powder metallurgy parts, offering a unique combination of surface hardness, wear resistance, and fatigue strength, while preserving the core properties of the material. The ability to control the diffusion of carbon and nitrogen at lower temperatures allows for precise manipulation of surface properties without compromising the material's geometry or porosity. As a result, this process is highly relevant in industries such as automotive, aerospace, and medical devices, where high-performance components are required. The ongoing optimization of process parameters and the development of advanced monitoring techniques will continue to enhance the effectiveness and versatility of sub-thermal carbonitriding for various industrial applications.
Reprint Statement: If there are no special instructions, all articles on this site are original. Please indicate the source for reprinting:https://www.cncmachiningptj.com/,thanks!
3, 4 and 5-axis precision CNC machining services for aluminum machining, beryllium, carbon steel, magnesium, titanium machining, Inconel, platinum, superalloy, acetal, polycarbonate, fiberglass, graphite and wood. Capable of machining parts up to 98 in. turning dia. and +/-0.001 in. straightness tolerance. Processes include milling, turning, drilling, boring, threading, tapping, forming, knurling, counterboring, countersinking, reaming and laser cutting. Secondary services such as assembly, centerless grinding, heat treating, plating and welding. Prototype and low to high volume production offered with maximum 50,000 units. Suitable for fluid power, pneumatics, hydraulics and valve applications. Serves the aerospace, aircraft, military, medical and defense industries.PTJ will strategize with you to provide the most cost-effective services to help you reach your target,Welcome to Contact us ( sales@pintejin.com ) directly for your new project.
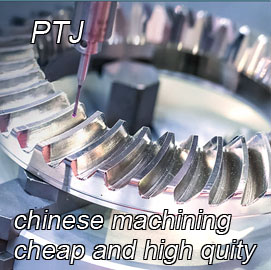
- 5 Axis Machining
- Cnc Milling
- Cnc Turning
- Machining Industries
- Machining Process
- Surface Treatment
- Metal Machining
- Plastic Machining
- Powder Metallurgy Mold
- Die Casting
- Parts Gallery
- Auto Metal Parts
- Machinery Parts
- LED Heatsink
- Building Parts
- Mobile Parts
- Medical Parts
- Electronic Parts
- Tailored Machining
- Bicycle Parts
- Aluminum Machining
- Titanium Machining
- Stainless Steel Machining
- Copper Machining
- Brass Machining
- Super Alloy Machining
- Peek Machining
- UHMW Machining
- Unilate Machining
- PA6 Machining
- PPS Machining
- Teflon Machining
- Inconel Machining
- Tool Steel Machining
- More Material