Powder Metallurgy of TiAl Intermetallic Compounds
Titanium aluminides (TiAl) are a class of intermetallic compounds primarily composed of titanium (Ti) and aluminum (Al), and they are known for their excellent high-temperature strength, oxidation resistance, and low density. These characteristics make TiAl alloys attractive materials for applications in the aerospace, automotive, and power generation industries, particularly in environments where traditional materials like nickel-based superalloys would be too heavy or costly. TiAl intermetallic compounds are considered to be some of the most promising alternatives for next-generation high-temperature materials.
Among the various processing methods employed to produce TiAl intermetallics, powder metallurgy (PM) stands out as a crucial technique. Powder metallurgy enables precise control over the composition, microstructure, and porosity of TiAl alloys, offering significant advantages in terms of cost-efficiency, mechanical performance, and material properties. Through the manipulation of powder size, processing parameters, and sintering conditions, it is possible to tailor the properties of TiAl alloys for specific applications, enhancing their performance in extreme conditions.
This article provides an extensive review of TiAl intermetallics produced by powder metallurgy, delving into their fundamental properties, processing methods, and applications. It aims to offer a comprehensive understanding of this important material system, highlighting the advantages and challenges of powder metallurgy in the development of TiAl alloys.
History and Development of TiAl Intermetallics
The development of titanium aluminides can be traced back to the 1950s when the concept of intermetallic compounds was first explored in the context of high-temperature applications. Early research focused on the binary Ti-Al system, which contains a range of phases, including the alpha2 (Ti₃Al) and gamma (TiAl) phases, which are of primary interest in the development of TiAl intermetallics.
TiAl alloys gained significant attention in the 1980s and 1990s as researchers began to understand the potential of these materials for high-temperature structural applications. Their low density, high melting point, and superior oxidation resistance at elevated temperatures positioned them as suitable candidates for turbine engines, jet propulsion, and other advanced aerospace systems. However, producing TiAl alloys with sufficient ductility at room temperature remained a significant challenge. To address this issue, researchers focused on controlling the microstructure and phase distribution within the material, leading to the development of near gamma TiAl alloys, which combine the high strength of gamma-TiAl with improved ductility at ambient temperatures.
Powder metallurgy methods, particularly the use of gas atomization, rapid solidification, and hot isostatic pressing (HIP), became critical in fabricating TiAl intermetallics with fine microstructures and enhanced mechanical properties. These methods allowed for the precise control of the alloy's composition and microstructure, enabling the production of TiAl alloys with superior performance characteristics.
Composition and Phases of TiAl Alloys
TiAl alloys exhibit a complex phase diagram with several distinct phases, each with its own set of properties. The primary phases in TiAl alloys include:
-
Alpha2 (Ti₃Al): The alpha2 phase is a high-temperature, ordered phase with a hexagonal close-packed (hcp) structure. It provides high strength and stability at elevated temperatures but is brittle at room temperature.
-
Gamma (TiAl): The gamma phase, with a face-centered cubic (fcc) structure, is the most commonly used phase in TiAl intermetallics. It offers excellent high-temperature strength, oxidation resistance, and low density, but it is prone to low ductility at room temperature.
-
Lamellar Structure: A common microstructure in TiAl alloys, the lamellar structure consists of alternating layers of alpha2 and gamma phases. This structure improves the material's mechanical properties, including strength and fracture toughness.
-
B2 Phase (TiAl₃): This phase, rich in aluminum, offers high hardness and oxidation resistance but has low ductility, making it less suitable for structural applications.
The composition of TiAl alloys can vary depending on the desired properties and application. The typical composition of a gamma-TiAl alloy is approximately 45-48% titanium and 45-50% aluminum, with small additions of other elements such as niobium (Nb), chromium (Cr), and vanadium (V) to enhance the material's properties.
Table 1: Common Phase Diagram and Compositions in Ti-Al Alloys
Composition (Ti-Al) | Major Phases Present | Characteristics | Applications |
---|---|---|---|
45-48% Ti, 45-50% Al | Gamma (TiAl), Alpha2 (Ti₃Al) | High temperature strength, oxidation resistance, low density | Aerospace, turbine engines |
50% Ti, 50% Al | Gamma (TiAl) | Low density, high strength, brittle at room temperature | Automotive, military |
60% Ti, 40% Al | B2 Phase (TiAl₃) | High hardness, oxidation resistance, low ductility | High-performance coatings |
Powder Metallurgy Processing of TiAl Intermetallics
Powder metallurgy (PM) is a key technique for producing TiAl intermetallics with tailored properties. The PM process involves several key steps: powder production, mixing, compaction, and sintering. Each step plays a crucial role in determining the final properties of the TiAl alloy.
1. Powder Production
The first step in powder metallurgy is the production of fine Ti and Al powders. Various techniques are used to produce powders with desired particle sizes and distributions, such as gas atomization, water atomization, and mechanical alloying.
-
Gas Atomization: Gas atomization involves the use of high-pressure gas to atomize a molten metal into fine droplets, which rapidly solidify into powder. This process produces powders with a relatively narrow particle size distribution and high purity, making it ideal for TiAl alloy production.
-
Water Atomization: In this method, water is used to rapidly cool molten metal, resulting in the formation of irregularly shaped powders. Water-atomized powders typically have a wider particle size distribution and can contain some oxide content, which may need to be removed during post-processing.
-
Mechanical Alloying: This technique involves the repeated deformation and cold welding of powder particles in a ball mill, leading to the formation of fine, well-mixed powders. Mechanical alloying can be used to produce TiAl alloys with fine microstructures and homogenous compositions.
2. Powder Mixing and Compaction
Once the powders are produced, they are mixed to create a homogenous blend of titanium and aluminum particles. The powder mixture is then compacted into green bodies, usually by pressing or using other techniques such as cold isostatic pressing (CIP). The compaction process influences the density and porosity of the green body, which in turn affects the final properties of the sintered part.
3. Sintering
Sintering is the final step in powder metallurgy, during which the green body is heated to a temperature just below its melting point to cause the powder particles to bond together. Sintering can be performed in various atmospheres, such as argon, vacuum, or hydrogen, to prevent oxidation and control the microstructure. The sintering temperature and time are critical parameters in achieving the desired mechanical properties, such as strength, ductility, and oxidation resistance.
Table 2: Effect of Sintering Parameters on TiAl Powder Metallurgy
Sintering Temperature (°C) | Sintering Time (hrs) | Relative Density (%) | Main Phases Formed | Mechanical Properties |
---|---|---|---|---|
1300 | 1 | 95 | Gamma (TiAl), Alpha2 (Ti₃Al) | High strength, low ductility |
1450 | 2 | 98 | Gamma (TiAl), Lamellar | Improved ductility, fracture toughness |
1500 | 4 | 99 | Gamma (TiAl), Lamellar, Alpha2 | High strength, excellent oxidation resistance |
Properties of TiAl Intermetallics
The mechanical, thermal, and chemical properties of TiAl intermetallic compounds are significantly influenced by the alloy composition, phase structure, and processing conditions. Below are the key properties of TiAl alloys produced by powder metallurgy:
-
High-Temperature Strength: TiAl alloys exhibit excellent strength at elevated temperatures, making them suitable for use in high-temperature environments, such as turbine blades and exhaust systems. Their low density also contributes to reduced fuel consumption in aerospace and automotive applications.
-
Oxidation Resistance: TiAl alloys have a natural oxide layer (TiO₂) that protects them from further oxidation at high temperatures, making them highly resistant to environmental degradation. This property is particularly important in aerospace and automotive applications, where exposure to high-temperature gases and combustion products is common.
-
Fracture Toughness and Ductility: While TiAl alloys generally exhibit high strength, their fracture toughness and ductility can be limited, particularly in the gamma phase. The lamellar microstructure, achieved through powder metallurgy processing, significantly enhances the material's fracture toughness and overall mechanical performance.
-
Density: The low density of TiAl alloys (approximately 3.9 g/cm³) makes them attractive for weight-sensitive applications, such as aerospace and automotive components, where reducing the weight of structural materials is a priority.
Applications of TiAl Intermetallics
TiAl alloys have found applications in a variety of industries due to their superior properties. Some notable applications include:
-
Aerospace Industry: TiAl alloys are used in turbine blades, vanes, and other high-temperature engine components, where their high strength-to-weight ratio and excellent oxidation resistance are critical.
-
Automotive Industry: TiAl alloys are being explored for use in turbochargers, exhaust valves, and other components that operate under high-temperature conditions.
-
Power Generation: TiAl alloys are used in gas turbines and other power generation equipment that require materials capable of withstanding extreme temperatures and mechanical stress.
-
Medical Industry: Due to their biocompatibility, TiAl alloys are being investigated for use in implants and prosthetics, particularly in applications requiring high strength and low density.
Reprint Statement: If there are no special instructions, all articles on this site are original. Please indicate the source for reprinting:https://www.cncmachiningptj.com/,thanks!
3, 4 and 5-axis precision CNC machining services for aluminum machining, beryllium, carbon steel, magnesium, titanium machining, Inconel, platinum, superalloy, acetal, polycarbonate, fiberglass, graphite and wood. Capable of machining parts up to 98 in. turning dia. and +/-0.001 in. straightness tolerance. Processes include milling, turning, drilling, boring, threading, tapping, forming, knurling, counterboring, countersinking, reaming and laser cutting. Secondary services such as assembly, centerless grinding, heat treating, plating and welding. Prototype and low to high volume production offered with maximum 50,000 units. Suitable for fluid power, pneumatics, hydraulics and valve applications. Serves the aerospace, aircraft, military, medical and defense industries.PTJ will strategize with you to provide the most cost-effective services to help you reach your target,Welcome to Contact us ( sales@pintejin.com ) directly for your new project.
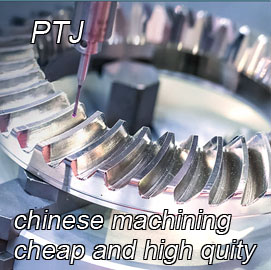
- 5 Axis Machining
- Cnc Milling
- Cnc Turning
- Machining Industries
- Machining Process
- Surface Treatment
- Metal Machining
- Plastic Machining
- Powder Metallurgy Mold
- Die Casting
- Parts Gallery
- Auto Metal Parts
- Machinery Parts
- LED Heatsink
- Building Parts
- Mobile Parts
- Medical Parts
- Electronic Parts
- Tailored Machining
- Bicycle Parts
- Aluminum Machining
- Titanium Machining
- Stainless Steel Machining
- Copper Machining
- Brass Machining
- Super Alloy Machining
- Peek Machining
- UHMW Machining
- Unilate Machining
- PA6 Machining
- PPS Machining
- Teflon Machining
- Inconel Machining
- Tool Steel Machining
- More Material