What Is Powder Metallurgy Porous Material
Powder metallurgy (PM) porous materials are a class of engineered materials characterized by their controlled porosity, achieved through the consolidation and sintering of metal powders. These materials exhibit a unique combination of mechanical strength, permeability, and tailored microstructure, making them essential for various industrial applications such as filtration, fluid control, sound absorption, and thermal insulation.
1. Introduction to Powder Metallurgy Porous Materials
Powder metallurgy involves the production of components by compacting metal powders into a desired shape and then sintering them at elevated temperatures to achieve bonding between particles. By adjusting powder characteristics, compaction pressure, and sintering conditions, manufacturers can control the porosity, pore size distribution, and mechanical properties of the final product.
Porous materials fabricated through powder metallurgy are distinct from conventional solid metals due to their controlled voids, which influence material properties such as density, thermal conductivity, permeability, and mechanical behavior. These materials can be engineered with open, closed, or interconnected porosity, depending on the intended application.
2. Classification of Powder Metallurgy Porous Materials
Powder metallurgy porous materials can be classified based on their composition, structure, and function:
2.1. Based on Composition
- Metallic porous materials: These include porous stainless steel, bronze, titanium, aluminum, and nickel-based materials.
- Composite porous materials: These are made from mixtures of metals and ceramics, such as metal-ceramic sintered filters or cermets.
2.2. Based on Porosity Structure
- Open-cell (interconnected) porous materials: These allow fluid or gas flow through the structure, making them ideal for filtration applications.
- Closed-cell porous materials: These consist of isolated pores that do not connect, enhancing thermal insulation and mechanical damping properties.
- Graded porosity materials: These exhibit variations in pore size and distribution within the material, improving performance for specific engineering applications.
2.3. Based on Function
- Filtration materials: Used in gas and liquid filtration due to their permeability and uniform pore distribution.
- Structural materials: Employed in lightweight structural applications, offering high strength-to-weight ratios.
- Energy absorption materials: Used in shock absorption and sound dampening due to their ability to dissipate energy.
3. Manufacturing Methods for Porous Powder Metallurgy Materials
The production of porous materials via powder metallurgy involves multiple techniques, each influencing the final microstructure and properties.
3.1. Conventional Pressing and Sintering
In this method, metal powders are compacted into a mold under controlled pressure, forming a "green body" that is then sintered at high temperatures to achieve particle bonding. The level of porosity is controlled by adjusting the powder size, compaction pressure, and sintering time.
3.2. Metal Injection Molding (MIM) with Space Holders
MIM techniques allow the incorporation of temporary space holders that create controlled porosity when removed during sintering.
3.3. Additive Manufacturing (3D Printing)
Advanced 3D printing techniques such as selective laser melting (SLM) and electron beam melting (EBM) enable precise control of pore architecture for customized porous structures.
3.4. Electrochemical Deposition
In this method, metal ions are deposited onto a pre-designed porous template, which is subsequently removed, leaving behind a porous metallic structure.
3.5. Freeze-Casting
This technique leverages ice as a template, allowing directional solidification and controlled porosity after sublimation.
4. Microstructural Characteristics of Powder Metallurgy Porous Materials
The performance of porous PM materials is governed by their microstructure, which includes parameters such as pore size, distribution, connectivity, and shape.
4.1. Pore Size and Distribution
Pore size affects permeability and filtration efficiency. Materials with fine, uniform pores are ideal for precision filtration, while larger pores enhance fluid flow.
4.2. Pore Connectivity
Interconnected porosity allows fluid transport, making these materials suitable for wicking and filtration applications. Closed porosity enhances mechanical strength and insulation properties.
4.3. Sintering Effects on Porosity
Sintering temperature and time influence pore coalescence and densification. High sintering temperatures reduce porosity but improve mechanical integrity.
5. Mechanical Properties of Powder Metallurgy Porous Materials
Mechanical performance depends on porosity level, material composition, and processing conditions.
Property | High-Density PM Material | Low-Density PM Material |
---|---|---|
Density (g/cm³) | 6.5–8.0 | 2.0–5.5 |
Tensile Strength (MPa) | 300–800 | 50–200 |
Compressive Strength (MPa) | 400–1200 | 100–300 |
Elastic Modulus (GPa) | 50–200 | 5–30 |
6. Applications of Powder Metallurgy Porous Materials
Powder metallurgy porous materials serve a broad range of applications across multiple industries.
6.1. Filtration Systems
Porous metals such as sintered stainless steel and bronze are widely used for gas and liquid filtration due to their corrosion resistance and permeability.
6.2. Biomedical Applications
Porous titanium is used in orthopedic implants to promote bone ingrowth and improve biocompatibility.
6.3. Energy Storage
Nickel-based porous structures are employed as electrodes in batteries and fuel cells for improved electrochemical performance.
6.4. Acoustic and Thermal Insulation
Porous metal foams are effective in absorbing sound and insulating heat in industrial applications.
7. Comparison of Powder Metallurgy Porous Materials with Other Porous Materials
Material Type | Porosity (%) | Strength (MPa) | Applications |
---|---|---|---|
Sintered Metal | 10–40 | 100–800 | Filtration, energy storage, biomedical |
Polymer Foams | 30–90 | 0.1–10 | Insulation, cushioning |
Ceramic Foams | 50–95 | 10–200 | High-temperature insulation, catalysts |
Natural Materials | 20–80 | 5–50 | Biodegradable scaffolds |
8. Future Trends in Powder Metallurgy Porous Materials
The development of new manufacturing methods, such as 3D printing and hybrid sintering, will enable greater customization and functionalization of porous structures. Research on novel alloys and coatings aims to enhance durability and application-specific performance.
9. Conclusion
Powder metallurgy porous materials represent a critical class of engineered materials with tailored properties for diverse applications. By optimizing processing techniques and material compositions, researchers and manufacturers continue to push the boundaries of performance and functionality in this field.
This article provides a broad overview of powder metallurgy porous materials, but further advancements in materials science and manufacturing techniques will continue to expand their capabilities in the years to come.
Reprint Statement: If there are no special instructions, all articles on this site are original. Please indicate the source for reprinting:https://www.cncmachiningptj.com/,thanks!
3, 4 and 5-axis precision CNC machining services for aluminum machining, beryllium, carbon steel, magnesium, titanium machining, Inconel, platinum, superalloy, acetal, polycarbonate, fiberglass, graphite and wood. Capable of machining parts up to 98 in. turning dia. and +/-0.001 in. straightness tolerance. Processes include milling, turning, drilling, boring, threading, tapping, forming, knurling, counterboring, countersinking, reaming and laser cutting. Secondary services such as assembly, centerless grinding, heat treating, plating and welding. Prototype and low to high volume production offered with maximum 50,000 units. Suitable for fluid power, pneumatics, hydraulics and valve applications. Serves the aerospace, aircraft, military, medical and defense industries.PTJ will strategize with you to provide the most cost-effective services to help you reach your target,Welcome to Contact us ( sales@pintejin.com ) directly for your new project.
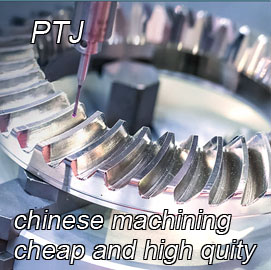
- 5 Axis Machining
- Cnc Milling
- Cnc Turning
- Machining Industries
- Machining Process
- Surface Treatment
- Metal Machining
- Plastic Machining
- Powder Metallurgy Mold
- Die Casting
- Parts Gallery
- Auto Metal Parts
- Machinery Parts
- LED Heatsink
- Building Parts
- Mobile Parts
- Medical Parts
- Electronic Parts
- Tailored Machining
- Bicycle Parts
- Aluminum Machining
- Titanium Machining
- Stainless Steel Machining
- Copper Machining
- Brass Machining
- Super Alloy Machining
- Peek Machining
- UHMW Machining
- Unilate Machining
- PA6 Machining
- PPS Machining
- Teflon Machining
- Inconel Machining
- Tool Steel Machining
- More Material