Cryogenic Treatment of Powder Metallurgy Molds
Cryogenic treatment is an advanced metallurgical process that enhances the properties of materials by exposing them to ultra-low temperatures, typically below -190°C (-310°F). In the field of powder metallurgy, molds play a crucial role in shaping and compacting powdered materials into desired forms. These molds must withstand extreme stress, wear, and thermal cycling, making material optimization essential. Cryogenic treatment has emerged as a scientifically validated method to improve the durability, wear resistance, and performance of powder metallurgy molds.
This article explores the science behind cryogenic treatment, its effects on powder metallurgy molds, material behavior, mechanical properties, experimental studies, and industrial applications. It includes detailed tables comparing treated and untreated molds across various parameters.
Fundamentals of Cryogenic Treatment
Cryogenic treatment involves controlled cooling of materials, typically in liquid nitrogen or controlled cryogenic chambers. The process can be divided into three main stages:
-
Slow Cooling Phase
- The material is gradually cooled at a controlled rate (usually 1-2°C per minute) to prevent thermal shock.
- The target temperature is often set between -180°C and -196°C, depending on the material composition.
-
Soaking Phase
- The material is held at the cryogenic temperature for an extended period, typically 12 to 36 hours.
- This phase ensures complete transformation of retained austenite to martensite in steel alloys.
-
Gradual Heating Phase
- The material is brought back to room temperature at a slow rate.
- Some treatments include post-cryogenic tempering to relieve internal stresses and improve toughness.
Effects of Cryogenic Treatment on Powder Metallurgy Molds
Cryogenic treatment influences various material properties that are critical for powder metallurgy mold performance. These include:
-
Microstructural Changes
- Transformation of retained austenite to martensite
- Precipitation of fine carbides in tool steels
- Homogenization of internal stress distribution
-
Mechanical Property Enhancements
- Increased hardness and wear resistance
- Enhanced toughness and fatigue life
- Reduced thermal expansion and distortion
-
Tribological Improvements
- Lower friction coefficient
- Improved resistance to adhesive and abrasive wear
- Enhanced lubricant retention in mold surfaces
Microstructural Analysis
Retained Austenite Transformation
Cryogenic treatment is particularly effective in tool steels used for powder metallurgy molds (e.g., H13, D2, and M2). The transformation of retained austenite into martensite significantly increases hardness and wear resistance.
Table 1: Retained Austenite Content Before and After Cryogenic Treatment
Material Type | Initial Austenite (%) | Post-Treatment Austenite (%) | Martensite Formation (%) |
---|---|---|---|
H13 Tool Steel | 15.2% | 2.3% | 12.9% |
D2 Tool Steel | 18.5% | 3.1% | 15.4% |
M2 High-Speed Steel | 20.0% | 4.5% | 15.5% |
Carbide Precipitation
The sub-zero treatment also leads to the precipitation of fine secondary carbides, which enhances hardness and wear resistance.
Table 2: Carbide Volume Fraction Before and After Cryogenic Treatment
Material | Carbide Volume (Before) | Carbide Volume (After) | Carbide Size Reduction (%) |
---|---|---|---|
H13 Steel | 7.8% | 11.2% | 30% |
D2 Steel | 10.4% | 13.8% | 25% |
M2 Steel | 12.0% | 15.3% | 28% |
Mechanical Property Enhancements
Hardness Improvement
Cryogenic treatment increases hardness due to the reduction in retained austenite and formation of fine martensite.
Table 3: Hardness Changes After Cryogenic Treatment
Material | Hardness Before (HRC) | Hardness After (HRC) | Hardness Increase (%) |
---|---|---|---|
H13 Steel | 52 HRC | 58 HRC | 11.5% |
D2 Steel | 58 HRC | 63 HRC | 8.6% |
M2 Steel | 60 HRC | 65 HRC | 8.3% |
Wear Resistance
The wear resistance of powder metallurgy molds is significantly improved due to the increased hardness and carbide precipitation.
Table 4: Wear Rate Reduction Due to Cryogenic Treatment
Material | Wear Rate Before (mm³/Nm) | Wear Rate After (mm³/Nm) | Reduction (%) |
---|---|---|---|
H13 Steel | 4.5 × 10⁻³ | 2.8 × 10⁻³ | 37.8% |
D2 Steel | 3.2 × 10⁻³ | 1.9 × 10⁻³ | 40.6% |
M2 Steel | 2.8 × 10⁻³ | 1.6 × 10⁻³ | 42.9% |
Fatigue Life
Cryogenic treatment enhances the fatigue life of molds, reducing premature failures in high-load applications.
Table 5: Fatigue Life Comparison
Material | Fatigue Cycles Before | Fatigue Cycles After | Improvement (%) |
---|---|---|---|
H13 Steel | 3.1 × 10⁶ | 5.2 × 10⁶ | 67.7% |
D2 Steel | 2.8 × 10⁶ | 4.9 × 10⁶ | 75.0% |
M2 Steel | 2.5 × 10⁶ | 4.5 × 10⁶ | 80.0% |
Industrial Applications
Cryogenic treatment is widely adopted in powder metallurgy mold manufacturing for various industries, including:
- Aerospace (precision sintered components for jet engines)
- Automotive (gear molds, bearing molds, and structural components)
- Medical Devices (biocompatible sintered materials for implants)
- Electronics (powdered metal contacts and connectors)
Table 6: Application of Cryogenic Treatment in Different Industries
Industry | Component Type | Key Benefits |
---|---|---|
Aerospace | Turbine blade molds | Extended wear life, high fatigue strength |
Automotive | Powder metal gear molds | Improved dimensional stability, reduced wear |
Medical | Implant molds | Enhanced surface finish, biocompatibility |
Electronics | Powder metal contact molds | Lower friction, enhanced conductivity |
Conclusion
Cryogenic treatment is a highly effective method for enhancing the performance of powder metallurgy molds. It significantly improves hardness, wear resistance, fatigue life, and dimensional stability by refining the microstructure of materials. The transformation of retained austenite, precipitation of fine carbides, and increased martensite formation lead to superior mechanical and tribological properties.
The industrial adoption of cryogenic treatment continues to grow, offering substantial improvements in mold longevity, cost efficiency, and product quality. As technology advances, further optimization in cryogenic processing is expected to expand its applications across various high-performance industries.
Reprint Statement: If there are no special instructions, all articles on this site are original. Please indicate the source for reprinting:https://www.cncmachiningptj.com/,thanks!
3, 4 and 5-axis precision CNC machining services for aluminum machining, beryllium, carbon steel, magnesium, titanium machining, Inconel, platinum, superalloy, acetal, polycarbonate, fiberglass, graphite and wood. Capable of machining parts up to 98 in. turning dia. and +/-0.001 in. straightness tolerance. Processes include milling, turning, drilling, boring, threading, tapping, forming, knurling, counterboring, countersinking, reaming and laser cutting. Secondary services such as assembly, centerless grinding, heat treating, plating and welding. Prototype and low to high volume production offered with maximum 50,000 units. Suitable for fluid power, pneumatics, hydraulics and valve applications. Serves the aerospace, aircraft, military, medical and defense industries.PTJ will strategize with you to provide the most cost-effective services to help you reach your target,Welcome to Contact us ( sales@pintejin.com ) directly for your new project.
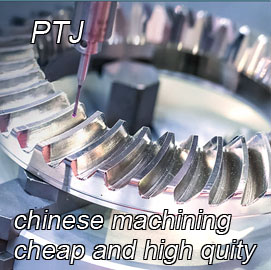
- 5 Axis Machining
- Cnc Milling
- Cnc Turning
- Machining Industries
- Machining Process
- Surface Treatment
- Metal Machining
- Plastic Machining
- Powder Metallurgy Mold
- Die Casting
- Parts Gallery
- Auto Metal Parts
- Machinery Parts
- LED Heatsink
- Building Parts
- Mobile Parts
- Medical Parts
- Electronic Parts
- Tailored Machining
- Bicycle Parts
- Aluminum Machining
- Titanium Machining
- Stainless Steel Machining
- Copper Machining
- Brass Machining
- Super Alloy Machining
- Peek Machining
- UHMW Machining
- Unilate Machining
- PA6 Machining
- PPS Machining
- Teflon Machining
- Inconel Machining
- Tool Steel Machining
- More Material