CNC Precision Machining of Quadratic Curved Surface Punches
CNC precision machining of quadratic curved surface punches is a critical process in advanced manufacturing, particularly in industries requiring high-accuracy forming tools. These punches, characterized by their complex geometric features, are commonly used in metal stamping, deep drawing, and precision forming applications. The machining process involves precise material removal using computer numerical control (CNC) technology to achieve high dimensional accuracy, surface quality, and geometric fidelity.
This article explores the scientific and engineering principles behind CNC machining of quadratic curved surface punches, including toolpath generation, cutting strategies, material considerations, surface finishing, and quality control. Additionally, it provides comparative analysis through detailed tables, highlighting machining parameters, tool materials, and achievable tolerances.
Mathematical Representation of Quadratic Curved Surfaces
A quadratic curved surface is defined by a second-degree polynomial equation in three-dimensional space. The general form of such a surface is:
Ax2+By2+Cz2+Dxy+Exz+Fyz+Gx+Hy+Iz+J=0Ax^2 + By^2 + Cz^2 + Dxy + Exz + Fyz + Gx + Hy + Iz + J = 0where A,B,C,D,E,F,G,H,I,A, B, C, D, E, F, G, H, I,
and JJ are constants that define the shape of the surface. Common quadratic surfaces encountered in precision machining include:- Elliptic Paraboloids: z=Ax2+By2z = Ax^2 + By^2
- Hyperbolic Paraboloids: z=Ax2−By2z = Ax^2 - By^2
- Ellipsoids: x2a2+y2b2+z2c2=1\frac{x^2}{a^2} + \frac{y^2}{b^2} + \frac{z^2}{c^2} = 1
- Hyperboloids: x2a2+y2b2−z2c2=1\frac{x^2}{a^2} + \frac{y^2}{b^2} - \frac{z^2}{c^2} = 1
Each type of quadratic surface requires a unique approach to CNC machining due to differences in curvature and material removal dynamics.
CNC Machining Strategies for Quadratic Curved Surface Punches
1. Toolpath Generation
Toolpath planning is crucial for achieving precise quadratic surfaces. Several common toolpath strategies include:
- Z-Level Machining (Contour Milling): Best for steep surfaces, where the tool follows horizontal slices.
- Spiral Machining: Ensures smooth transitions and is often used for axisymmetric curved surfaces.
- Adaptive Milling: Uses variable step-down depths to optimize tool engagement and minimize tool wear.
- Five-Axis Machining: Allows complex tool angles to maintain optimal contact with the surface.
2. Tool Selection and Cutting Conditions
The choice of cutting tool directly affects the machining accuracy and efficiency. Table 1 compares different tool materials used for machining quadratic curved punches.
Table 1: Comparison of Cutting Tool Materials
Tool Material | Hardness (HRC) | Wear Resistance | Thermal Conductivity (W/m·K) | Application Suitability |
---|---|---|---|---|
Carbide | 88-92 | High | 84 | General machining, high-speed cutting |
CBN (Cubic Boron Nitride) | 95+ | Very High | 120 | Hard materials (e.g., hardened steel) |
PCD (Polycrystalline Diamond) | 90-100 | Extremely High | 600 | Non-ferrous metals, composites |
High-Speed Steel (HSS) | 60-65 | Medium | 30 | Low-cost applications, softer metals |
Optimal cutting conditions depend on material type, tool geometry, and machine capabilities. The following table outlines recommended cutting parameters for machining quadratic surfaces in different materials.
Table 2: Recommended Cutting Parameters
Material | Spindle Speed (RPM) | Feed Rate (mm/min) | Depth of Cut (mm) | Cooling Method |
---|---|---|---|---|
Aluminum | 12,000 - 24,000 | 500 - 1,500 | 0.1 - 0.5 | Air or mist coolant |
Steel (Hardened) | 3,000 - 8,000 | 100 - 400 | 0.05 - 0.2 | Emulsion coolant |
Titanium | 2,000 - 6,000 | 50 - 200 | 0.05 - 0.3 | High-pressure coolant |
Inconel | 1,500 - 4,000 | 30 - 150 | 0.02 - 0.1 | Flood coolant |
Surface Finishing and Accuracy Control
Achieving a high-quality surface finish is critical in precision machining. Several finishing techniques are employed:
- Ball-end Milling: Used for finishing freeform surfaces with minimal tool marks.
- Diamond Burnishing: Enhances surface smoothness and reduces roughness.
- Electropolishing: Chemical treatment to improve microfinish and corrosion resistance.
Table 3 compares the achievable surface roughness values with different finishing methods.
Table 3: Surface Roughness Comparison
Finishing Method | Surface Roughness (Ra, µm) | Application |
---|---|---|
Ball-end Milling | 0.4 - 1.6 | General precision machining |
Diamond Burnishing | 0.05 - 0.2 | High-gloss surfaces, wear reduction |
Electropolishing | 0.02 - 0.1 | Corrosion resistance, biomedical parts |
Quality Inspection and Metrology
To ensure the accuracy of machined quadratic punches, advanced metrology techniques are used, including:
- Coordinate Measuring Machines (CMMs): Provide high-precision 3D measurements.
- Laser Scanning: Captures detailed surface topography.
- Optical Interferometry: Measures nano-scale surface deviations.
Table 4 presents a comparison of precision measurement techniques.
Table 4: Comparison of Metrology Methods
Method | Accuracy (µm) | Speed | Application |
---|---|---|---|
CMM | ± 1 | Medium | Dimensional verification |
Laser Scanning | ± 5 | High | Complex freeform surfaces |
Interferometry | ± 0.01 | Low | Ultra-precise surface analysis |
Conclusion
CNC precision machining of quadratic curved surface punches is a sophisticated process that requires advanced toolpath planning, optimized cutting conditions, precise surface finishing techniques, and high-accuracy inspection methods. The choice of tool material, machining parameters, and finishing approach significantly influences the quality and performance of the final punch. By integrating multi-axis CNC technology and state-of-the-art metrology, manufacturers can achieve the required tolerances and surface finishes for high-performance applications in aerospace, automotive, and precision forming industries.
This comprehensive analysis, supported by detailed comparative tables, provides a scientific foundation for optimizing the machining of quadratic curved punches. Future advancements in CNC machining, such as AI-driven toolpath optimization and adaptive control systems, will further enhance precision, efficiency, and material utilization in this critical manufacturing process.
Reprint Statement: If there are no special instructions, all articles on this site are original. Please indicate the source for reprinting:https://www.cncmachiningptj.com/,thanks!
3, 4 and 5-axis precision CNC machining services for aluminum machining, beryllium, carbon steel, magnesium, titanium machining, Inconel, platinum, superalloy, acetal, polycarbonate, fiberglass, graphite and wood. Capable of machining parts up to 98 in. turning dia. and +/-0.001 in. straightness tolerance. Processes include milling, turning, drilling, boring, threading, tapping, forming, knurling, counterboring, countersinking, reaming and laser cutting. Secondary services such as assembly, centerless grinding, heat treating, plating and welding. Prototype and low to high volume production offered with maximum 50,000 units. Suitable for fluid power, pneumatics, hydraulics and valve applications. Serves the aerospace, aircraft, military, medical and defense industries.PTJ will strategize with you to provide the most cost-effective services to help you reach your target,Welcome to Contact us ( sales@pintejin.com ) directly for your new project.
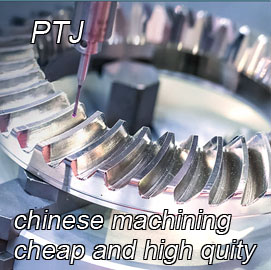
- 5 Axis Machining
- Cnc Milling
- Cnc Turning
- Machining Industries
- Machining Process
- Surface Treatment
- Metal Machining
- Plastic Machining
- Powder Metallurgy Mold
- Die Casting
- Parts Gallery
- Auto Metal Parts
- Machinery Parts
- LED Heatsink
- Building Parts
- Mobile Parts
- Medical Parts
- Electronic Parts
- Tailored Machining
- Bicycle Parts
- Aluminum Machining
- Titanium Machining
- Stainless Steel Machining
- Copper Machining
- Brass Machining
- Super Alloy Machining
- Peek Machining
- UHMW Machining
- Unilate Machining
- PA6 Machining
- PPS Machining
- Teflon Machining
- Inconel Machining
- Tool Steel Machining
- More Material