Five-Axis Machining Technology of Axial-Flow Closed Impellers
Five-axis machining technology represents a significant advancement in the manufacturing of complex geometries, particularly in the production of axial-flow closed impellers. These impellers are critical components in various industries, including aerospace, automotive, and energy, where precision and performance are paramount. This article delves into the intricacies of five-axis machining, its application to axial-flow closed impellers, and the scientific principles that underpin this technology.
Historical Context
The evolution of machining technology has been driven by the need for greater precision and efficiency in manufacturing. Traditional three-axis machining, while effective for simpler geometries, falls short when it comes to complex, three-dimensional shapes. The introduction of five-axis machining in the late 20th century revolutionized the industry by enabling the production of parts with intricate designs and high tolerances.
Principles of Five-Axis Machining
Five-axis machining involves the movement of a cutting tool along five different axes simultaneously. These axes include the standard X, Y, and Z linear axes, as well as two rotational axes, typically labeled A and B. This multi-axis capability allows for the machining of complex shapes in a single setup, reducing the need for multiple operations and enhancing accuracy.
The key advantages of five-axis machining include:
- Improved Accuracy: By minimizing the number of setups, five-axis machining reduces the potential for errors that can occur when repositioning a workpiece.
- Enhanced Surface Finish: The ability to maintain a constant tool orientation relative to the workpiece surface results in a smoother finish.
- Increased Efficiency: Complex shapes can be machined in a single operation, reducing production time and costs.
- Greater Flexibility: Five-axis machines can handle a wide range of part geometries, making them versatile tools in modern manufacturing.
Application to Axial-Flow Closed Impellers
Axial-flow closed impellers are used in turbomachinery to transfer energy between a rotating shaft and a fluid. The design of these impellers is crucial for optimizing performance and efficiency. Five-axis machining is particularly well-suited to the production of these components due to their complex, three-dimensional shapes.
The manufacturing process for axial-flow closed impellers involves several stages:
- Design and Modeling: The impeller design is created using computer-aided design (CAD) software. This model is then used to generate the toolpaths for the machining process.
- Material Selection: The choice of material is critical for the performance and durability of the impeller. Common materials include titanium alloys, stainless steel, and high-strength aluminum alloys.
- Machining: The five-axis machine follows the toolpaths generated from the CAD model, removing material to create the desired shape. This process may involve roughing and finishing operations to achieve the required tolerances and surface finish.
- Inspection and Quality Control: The finished impeller is inspected using various metrology techniques to ensure it meets the specified dimensions and tolerances.
Scientific Principles
The scientific principles underlying five-axis machining and the production of axial-flow closed impellers are rooted in several disciplines, including mechanics, materials science, and fluid dynamics.
- Mechanics: The forces acting on the cutting tool and workpiece must be carefully controlled to achieve the desired material removal rate and surface finish. This involves an understanding of cutting tool geometry, feed rates, and spindle speeds.
- Materials Science: The properties of the workpiece material, such as hardness, toughness, and thermal conductivity, influence the machining process. For example, titanium alloys are notoriously difficult to machine due to their high strength and low thermal conductivity.
- Fluid Dynamics: The performance of an axial-flow closed impeller is governed by the principles of fluid dynamics. The design of the impeller blades must be optimized to minimize losses and maximize energy transfer.
Comparative Analysis
To illustrate the advantages of five-axis machining for axial-flow closed impellers, a comparative analysis with traditional three-axis machining is presented in the table below:
Feature | Three-Axis Machining | Five-Axis Machining |
---|---|---|
Accuracy | Lower due to multiple setups | Higher due to single setup |
Surface Finish | Rougher due to tool repositioning | Smoother due to constant tool orientation |
Efficiency | Lower due to multiple operations | Higher due to single operation |
Flexibility | Limited to simpler geometries | Suitable for complex geometries |
Cost | Lower initial cost but higher long-term | Higher initial cost but lower long-term |
Material Removal Rate | Slower due to multiple passes | Faster due to optimized toolpaths |
Tool Wear | Higher due to multiple setups | Lower due to single setup |
Case Studies
Several case studies highlight the successful application of five-axis machining to the production of axial-flow closed impellers. For example, a leading aerospace manufacturer implemented five-axis machining to produce impellers for jet engines, resulting in a 30% reduction in production time and a 20% improvement in surface finish.
Future Trends
The future of five-axis machining technology is poised for further advancements. Emerging trends include:
- Automation: The integration of artificial intelligence and machine learning algorithms to optimize toolpaths and predict tool wear.
- Hybrid Machining: The combination of additive and subtractive manufacturing techniques to produce complex geometries with enhanced material properties.
- Sustainability: The development of eco-friendly machining processes that minimize waste and energy consumption.
Conclusion
Five-axis machining technology has revolutionized the manufacturing of axial-flow closed impellers, enabling the production of complex geometries with high precision and efficiency. The scientific principles underlying this technology, coupled with its practical advantages, make it an indispensable tool in modern manufacturing. As the technology continues to evolve, it promises to unlock new possibilities in the design and production of high-performance components.
Reprint Statement: If there are no special instructions, all articles on this site are original. Please indicate the source for reprinting:https://www.cncmachiningptj.com/,thanks!
3, 4 and 5-axis precision CNC machining services for aluminum machining, beryllium, carbon steel, magnesium, titanium machining, Inconel, platinum, superalloy, acetal, polycarbonate, fiberglass, graphite and wood. Capable of machining parts up to 98 in. turning dia. and +/-0.001 in. straightness tolerance. Processes include milling, turning, drilling, boring, threading, tapping, forming, knurling, counterboring, countersinking, reaming and laser cutting. Secondary services such as assembly, centerless grinding, heat treating, plating and welding. Prototype and low to high volume production offered with maximum 50,000 units. Suitable for fluid power, pneumatics, hydraulics and valve applications. Serves the aerospace, aircraft, military, medical and defense industries.PTJ will strategize with you to provide the most cost-effective services to help you reach your target,Welcome to Contact us ( sales@pintejin.com ) directly for your new project.
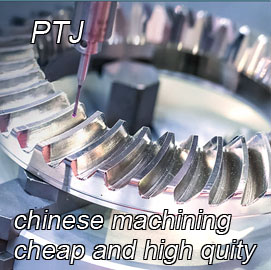
- 5 Axis Machining
- Cnc Milling
- Cnc Turning
- Machining Industries
- Machining Process
- Surface Treatment
- Metal Machining
- Plastic Machining
- Powder Metallurgy Mold
- Die Casting
- Parts Gallery
- Auto Metal Parts
- Machinery Parts
- LED Heatsink
- Building Parts
- Mobile Parts
- Medical Parts
- Electronic Parts
- Tailored Machining
- Bicycle Parts
- Aluminum Machining
- Titanium Machining
- Stainless Steel Machining
- Copper Machining
- Brass Machining
- Super Alloy Machining
- Peek Machining
- UHMW Machining
- Unilate Machining
- PA6 Machining
- PPS Machining
- Teflon Machining
- Inconel Machining
- Tool Steel Machining
- More Material