Semi-Solid Metal Processing Technology and Its Application in the Automotive Industry
Semi-solid metal processing (SSM) technology has emerged as a highly effective method in manufacturing components with enhanced mechanical properties and superior surface finish. This advanced processing method is based on the manipulation of metal alloys in a semi-solid state, which is between their liquid and solid phases, offering distinct advantages in terms of both the material's properties and the cost-efficiency of production. SSM has gained significant attention in industries such as automotive, aerospace, and electronics due to its potential to create parts with improved strength-to-weight ratios, reduced waste, and intricate shapes that are difficult to achieve through traditional manufacturing processes.
In the automotive industry, semi-solid metal processing plays a crucial role in the production of lightweight, high-strength parts for vehicles, contributing to the overall performance, fuel efficiency, and safety of the vehicle. The application of SSM in automotive manufacturing is particularly important as manufacturers strive to meet regulatory requirements for emissions and fuel economy while maintaining or enhancing the performance of vehicles.
This article explores the semi-solid metal processing technology, its principles, advantages, and challenges, and provides an in-depth analysis of its application within the automotive sector. It also offers a detailed comparison of the various semi-solid processing methods and outlines the technological advancements that continue to shape this field.
1. The Fundamentals of Semi-Solid Metal Processing Technology
Semi-solid metal processing involves the controlled manipulation of metal alloys in a semi-solid state. The semi-solid state is characterized by the presence of both solid particles (usually in the form of dendrites or globules) and a liquid matrix, which allows for the unique combination of moldability (as in casting) and strength (as in solid forming processes). The metal alloys most commonly used in SSM are aluminum, magnesium, and zinc, with aluminum alloys being the most predominant due to their desirable properties such as light weight, high strength, and corrosion resistance.
The SSM process is typically achieved through one of several methods, including:
- Thixoforming: This method involves heating the alloy to a temperature where it partially melts, forming a slurry of solid particles suspended in a liquid phase. The slurry is then injected into a mold under pressure.
- Rheocasting: In this process, the molten metal is rapidly cooled to create a semi-solid slurry, which is then transferred to a mold and solidified under pressure.
- Compocasting: This technique combines SSM and conventional casting, where a preform is created through casting and then further processed in a semi-solid state to improve its material properties.
These processes differ in their approach to achieving a semi-solid state, but all share the advantage of minimizing defects such as porosity, shrinkage, and thermal gradients, which are often encountered in traditional casting methods.
2. Advantages of Semi-Solid Metal Processing
SSM technology offers several advantages that make it particularly well-suited to the automotive industry, including:
-
Improved Mechanical Properties: Parts produced through semi-solid processing exhibit enhanced mechanical properties, such as higher tensile strength, better fatigue resistance, and improved corrosion resistance, compared to those made via conventional casting methods.
-
Better Dimensional Accuracy: SSM allows for the production of complex and intricate shapes with minimal need for further machining, reducing material waste and ensuring a better surface finish.
-
Lower Production Costs: By reducing the need for secondary operations (such as machining and welding) and minimizing scrap material, SSM can lower overall production costs.
-
Enhanced Fatigue Resistance: The fine-grain structure produced in the semi-solid state leads to parts with superior fatigue resistance, an essential property for automotive components that are subject to repeated loading and stress cycles.
-
Reduced Defects: SSM processes such as thixoforming and rheocasting significantly reduce common casting defects like porosity, shrinkage, and voids, which can compromise the integrity and performance of automotive parts.
3. Semi-Solid Metal Processing Techniques
Thixoforming
Thixoforming, one of the most widely studied and applied techniques in semi-solid metal processing, uses a carefully controlled heating process to convert a metal alloy into a semi-solid slurry with a desirable microstructure. The slurry consists of solid metal globules suspended in a liquid phase. These globules, typically in the range of 40 to 60 microns, provide the material with the flowability necessary for forming complex shapes, while maintaining the strength properties typical of solid metal. Thixoforming can be performed using die-casting machines, which apply pressure to the slurry to fill the mold cavity.
The key steps in thixoforming include:
- Preheating: The metal is heated to a temperature just below its liquidus point, typically between 570°C and 650°C for aluminum alloys, resulting in a semi-solid slurry.
- Molding: The slurry is injected into a die, where it is compacted under pressure to form the desired shape.
- Solidification: After molding, the part cools and solidifies to achieve the final product.
Thixoforming has found widespread use in the production of automotive components, particularly for structural parts such as engine blocks, chassis components, and transmission housings.
Rheocasting
Rheocasting is another method for producing semi-solid metal components. It involves rapidly cooling molten metal using shear forces to generate a semi-solid slurry. This slurry is then injected into molds, where it solidifies under pressure. Unlike thixoforming, which requires precise heating to a specific temperature, rheocasting focuses more on the mechanical manipulation of the molten metal to form the semi-solid structure.
The key steps in rheocasting are:
- Molten Metal Preparation: The alloy is heated to a temperature above its liquidus point.
- Shear Induced Solidification: The molten metal is subjected to shear forces, often through a rotating impeller or mechanical stirrer, which promotes the formation of a semi-solid slurry.
- Molding and Solidification: The slurry is injected into a mold, where it solidifies under pressure.
Rheocasting is particularly useful for creating parts with a high degree of complexity and intricate details, making it suitable for automotive parts such as suspension components and lightweight structural elements.
4. Application of Semi-Solid Metal Processing in the Automotive Industry
The automotive industry benefits from the unique properties offered by semi-solid metal processing. As automakers face increasing pressure to reduce vehicle weight while maintaining or enhancing performance and safety, the use of semi-solid processed components provides a means to meet these challenges effectively.
Key Applications:
-
Engine Components: Thixoforming and rheocasting are commonly used for manufacturing engine blocks, cylinder heads, and other critical components. These parts benefit from the improved fatigue resistance and reduced porosity that semi-solid processing offers.
-
Transmission Parts: Semi-solid processing is used to produce lightweight transmission cases and housings, which require high-strength materials to handle the forces exerted during operation.
-
Chassis Components: Automotive suspension parts, subframes, and other structural components are made using semi-solid processing to achieve the optimal balance of strength and lightweight design.
-
Heat Exchangers: Parts such as radiators and cooling plates are often made using semi-solid processes, which allow for better thermal conductivity and durability under high-stress conditions.
5. Comparison of Semi-Solid Metal Processing Methods
Process | Material | Key Advantages | Key Applications | Challenges |
---|---|---|---|---|
Thixoforming | Aluminum, Magnesium | High precision, low porosity, complex shapes | Engine blocks, transmission housings | Requires precise temperature control, expensive dies |
Rheocasting | Aluminum, Zinc | Fast processing, complex geometries | Suspension parts, chassis components | Lower control over material properties compared to thixoforming |
Compocasting | Aluminum, Magnesium | Combines SSM with conventional casting | Automotive structural parts | Requires hybrid equipment, limited alloy choice |
Direct Squeeze Casting | Aluminum, Zinc | Low porosity, high surface quality | Small complex parts, brackets | Limited to smaller parts, costly setup |
Conclusion
Semi-solid metal processing technology has demonstrated significant potential in revolutionizing the production of automotive components. The various SSM techniques such as thixoforming, rheocasting, and compocasting offer distinct advantages in terms of material properties, production efficiency, and cost reduction. As automotive manufacturers continue to prioritize weight reduction, fuel efficiency, and performance, SSM provides a viable solution to meet these demands while ensuring high-quality, durable components. Furthermore, ongoing research and technological advancements are expected to expand the scope of semi-solid processing, enabling more complex and cost-effective manufacturing solutions for the automotive industry in the future.
Reprint Statement: If there are no special instructions, all articles on this site are original. Please indicate the source for reprinting:https://www.cncmachiningptj.com/,thanks!
3, 4 and 5-axis precision CNC machining services for aluminum machining, beryllium, carbon steel, magnesium, titanium machining, Inconel, platinum, superalloy, acetal, polycarbonate, fiberglass, graphite and wood. Capable of machining parts up to 98 in. turning dia. and +/-0.001 in. straightness tolerance. Processes include milling, turning, drilling, boring, threading, tapping, forming, knurling, counterboring, countersinking, reaming and laser cutting. Secondary services such as assembly, centerless grinding, heat treating, plating and welding. Prototype and low to high volume production offered with maximum 50,000 units. Suitable for fluid power, pneumatics, hydraulics and valve applications. Serves the aerospace, aircraft, military, medical and defense industries.PTJ will strategize with you to provide the most cost-effective services to help you reach your target,Welcome to Contact us ( sales@pintejin.com ) directly for your new project.
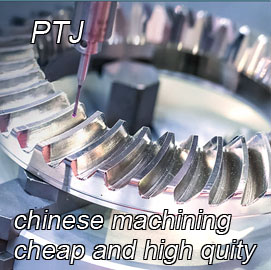
- 5 Axis Machining
- Cnc Milling
- Cnc Turning
- Machining Industries
- Machining Process
- Surface Treatment
- Metal Machining
- Plastic Machining
- Powder Metallurgy Mold
- Die Casting
- Parts Gallery
- Auto Metal Parts
- Machinery Parts
- LED Heatsink
- Building Parts
- Mobile Parts
- Medical Parts
- Electronic Parts
- Tailored Machining
- Bicycle Parts
- Aluminum Machining
- Titanium Machining
- Stainless Steel Machining
- Copper Machining
- Brass Machining
- Super Alloy Machining
- Peek Machining
- UHMW Machining
- Unilate Machining
- PA6 Machining
- PPS Machining
- Teflon Machining
- Inconel Machining
- Tool Steel Machining
- More Material