Application of Macro Programs in Non-Circular Curve Contour Turning
Non-circular curve contour turning is a specialized machining process used to create complex, non-circular shapes on a lathe. This process is essential in various industries, including aerospace, automotive, and manufacturing, where precision and accuracy are paramount. The application of macro programs in non-circular curve contour turning has revolutionized the field, enabling the production of intricate parts with high precision and efficiency. This article delves into the principles, applications, and benefits of using macro programs in non-circular curve contour turning, supported by detailed tables for comparison.
Principles of Non-Circular Curve Contour Turning
Non-circular curve contour turning involves the use of a lathe to create shapes that deviate from the standard circular form. This process requires precise control over the tool path to achieve the desired contour. Traditional methods relied heavily on manual adjustments and the skill of the machinist. However, with the advent of Computer Numerical Control (CNC) technology, the process has become more automated and precise.
Macro programs, a subset of CNC programming, allow for the creation of complex tool paths that can be executed with high precision. These programs are written in a high-level language that can be interpreted by the CNC controller, enabling the machine to follow intricate patterns and shapes. The use of macro programs in non-circular curve contour turning offers several advantages, including increased accuracy, reduced setup time, and the ability to produce complex geometries.
Applications of Macro Programs in Non-Circular Curve Contour Turning
Macro programs are widely used in various industries to achieve non-circular curve contour turning. Some of the key applications include:
-
Aerospace Industry: The aerospace industry requires precision components with complex geometries, such as turbine blades and engine parts. Macro programs enable the production of these parts with high accuracy and repeatability.
-
Automotive Industry: In the automotive sector, non-circular curve contour turning is used to produce components like camshafts, crankshafts, and other engine parts that require precise contours.
-
Manufacturing: General manufacturing processes often involve the creation of custom parts with non-circular shapes. Macro programs allow for the efficient production of these parts, reducing lead times and improving quality.
-
Medical Devices: The medical industry requires precision components for devices like implants and surgical tools. Non-circular curve contour turning with macro programs ensures that these components meet stringent quality standards.
Benefits of Using Macro Programs
The use of macro programs in non-circular curve contour turning offers several benefits, including:
-
Precision and Accuracy: Macro programs allow for precise control over the tool path, ensuring that the final product meets the required specifications. This level of precision is crucial in industries where even minor deviations can lead to significant issues.
-
Efficiency: Macro programs reduce the need for manual adjustments, leading to faster setup times and increased production efficiency. This results in lower costs and shorter lead times.
-
Repeatability: Once a macro program is developed, it can be used repeatedly to produce identical parts. This ensures consistency in production and reduces the risk of errors.
-
Flexibility: Macro programs can be easily modified to accommodate changes in design or production requirements. This flexibility allows for quick adaptation to new projects or modifications in existing ones.
Comparison of Traditional Methods vs. Macro Programs
The following table compares traditional methods of non-circular curve contour turning with the use of macro programs:
Feature | Traditional Methods | Macro Programs |
---|---|---|
Precision | Dependent on machinist skill | High precision and accuracy |
Setup Time | Longer due to manual adjustments | Shorter due to automated control |
Repeatability | Variable | Highly consistent |
Flexibility | Limited | Highly adaptable |
Cost | Higher due to manual labor | Lower due to automated processes |
Lead Time | Longer | Shorter |
Error Rate | Higher | Lower |
Detailed Case Studies
Case Study 1: Aerospace Industry
In the aerospace industry, the production of turbine blades requires precise non-circular curve contour turning. Traditional methods involved manual adjustments and skilled machinists, leading to longer production times and higher costs. The introduction of macro programs has significantly improved the process. For example, a leading aerospace manufacturer implemented macro programs to produce turbine blades with complex geometries. The results showed a 30% reduction in production time and a 20% decrease in costs, while maintaining high precision and quality.
Case Study 2: Automotive Industry
The automotive industry relies on non-circular curve contour turning for the production of camshafts and crankshafts. Traditional methods were time-consuming and prone to errors. By adopting macro programs, an automotive manufacturer was able to reduce setup times by 40% and improve the accuracy of the final product. This resulted in better engine performance and reduced maintenance requirements.
Case Study 3: Medical Devices
In the medical industry, precision is critical for the production of implants and surgical tools. Non-circular curve contour turning with macro programs ensures that these components meet stringent quality standards. A medical device manufacturer used macro programs to produce custom implants with complex geometries. The use of macro programs resulted in a 50% reduction in production errors and a significant improvement in product quality.
Technical Aspects of Macro Programs
Macro programs are written in a high-level language that can be interpreted by the CNC controller. The language typically includes commands for tool path control, speed and feed rates, and other machining parameters. The following table provides an overview of the key commands used in macro programs:
Command | Description |
---|---|
G00 | Rapid positioning |
G01 | Linear interpolation |
G02/G03 | Circular interpolation (clockwise/counterclockwise) |
G04 | Dwell |
G40/G41/G42 | Cutter radius compensation (off/left/right) |
M03/M04 | Spindle control (clockwise/counterclockwise) |
M05 | Spindle stop |
M30 | Program end |
Example of a Macro Program
O0001 T1 M06 G43 H1 M03 S12000 G0 G90 G40 G21 G17 G94 G80 G54 X0. Y0. Z0. G43 H1 M03 S12000 G1 Z-2. F100. G1 X10. Y10. Z-2. F50. G1 X20. Y20. Z-2. F50. G1 X30. Y30. Z-2. F50. G0 Z2. G40 M30 %
This example demonstrates a simple macro program for non-circular curve contour turning. The program includes commands for tool selection, spindle control, and tool path control. The use of such programs ensures precise and efficient machining of complex shapes.
Challenges and Limitations
While macro programs offer numerous benefits, there are also challenges and limitations to consider:
-
Complexity: Writing and debugging macro programs can be complex and time-consuming, requiring specialized knowledge and skills.
-
Compatibility: Macro programs need to be compatible with the specific CNC controller being used. Incompatibilities can lead to errors and inefficiencies.
-
Maintenance: Macro programs require regular updates and maintenance to ensure they remain effective and efficient. This can be a ongoing challenge, especially in dynamic production environments.
Future Trends
The future of non-circular curve contour turning with macro programs is promising. Advances in CNC technology, including the integration of artificial intelligence (AI) and machine learning (ML), are expected to further enhance the capabilities of macro programs. These technologies can optimize tool paths, predict maintenance requirements, and improve overall production efficiency.
Additionally, the development of more user-friendly programming languages and interfaces will make macro programs more accessible to a wider range of users. This will enable more industries to adopt these advanced machining techniques, leading to improved product quality and reduced costs.
Conclusion
The application of macro programs in non-circular curve contour turning has revolutionized the machining industry. By enabling precise control over the tool path, macro programs have improved the accuracy, efficiency, and repeatability of the machining process. This has led to significant benefits in various industries, including aerospace, automotive, and manufacturing. As technology continues to advance, the use of macro programs is expected to become even more widespread, driving further innovations and improvements in the field of non-circular curve contour turning.
Reprint Statement: If there are no special instructions, all articles on this site are original. Please indicate the source for reprinting:https://www.cncmachiningptj.com/,thanks!
3, 4 and 5-axis precision CNC machining services for aluminum machining, beryllium, carbon steel, magnesium, titanium machining, Inconel, platinum, superalloy, acetal, polycarbonate, fiberglass, graphite and wood. Capable of machining parts up to 98 in. turning dia. and +/-0.001 in. straightness tolerance. Processes include milling, turning, drilling, boring, threading, tapping, forming, knurling, counterboring, countersinking, reaming and laser cutting. Secondary services such as assembly, centerless grinding, heat treating, plating and welding. Prototype and low to high volume production offered with maximum 50,000 units. Suitable for fluid power, pneumatics, hydraulics and valve applications. Serves the aerospace, aircraft, military, medical and defense industries.PTJ will strategize with you to provide the most cost-effective services to help you reach your target,Welcome to Contact us ( sales@pintejin.com ) directly for your new project.
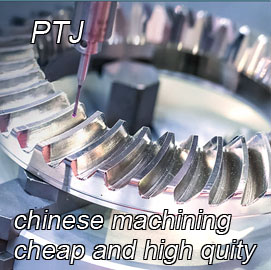
- 5 Axis Machining
- Cnc Milling
- Cnc Turning
- Machining Industries
- Machining Process
- Surface Treatment
- Metal Machining
- Plastic Machining
- Powder Metallurgy Mold
- Die Casting
- Parts Gallery
- Auto Metal Parts
- Machinery Parts
- LED Heatsink
- Building Parts
- Mobile Parts
- Medical Parts
- Electronic Parts
- Tailored Machining
- Bicycle Parts
- Aluminum Machining
- Titanium Machining
- Stainless Steel Machining
- Copper Machining
- Brass Machining
- Super Alloy Machining
- Peek Machining
- UHMW Machining
- Unilate Machining
- PA6 Machining
- PPS Machining
- Teflon Machining
- Inconel Machining
- Tool Steel Machining
- More Material