Design of a Special Fixture for Five-Axis Tire Mold Machining
The design of specialized fixtures for five-axis tire mold machining is a critical component in achieving precision, efficiency, and repeatability in tire mold manufacturing. Tire molds, which play a vital role in defining the final shape, tread pattern, and structural integrity of tires, demand intricate machining processes. A specialized fixture tailored to the unique requirements of five-axis machining can significantly enhance production outcomes. This article delves into the theoretical principles, practical considerations, and scientific methodologies involved in designing such fixtures.
Introduction to Five-Axis Machining
Five-axis machining is an advanced manufacturing technology that enables the simultaneous movement of cutting tools along five axes. Unlike traditional three-axis systems, five-axis machining facilitates the creation of complex geometries and intricate patterns, making it ideal for tire mold production. Key benefits of five-axis machining include:
-
Improved Surface Finish: The continuous movement reduces tool marks and ensures smooth surface transitions.
-
Reduced Setup Time: Multiple faces of the workpiece can be machined in a single setup.
-
Enhanced Precision: Reduced manual handling minimizes errors and improves dimensional accuracy.
The integration of a specialized fixture into this process is vital for maximizing these advantages.
Requirements for Tire Mold Fixtures
Designing a fixture for five-axis tire mold machining involves addressing specific requirements to ensure optimal performance. These requirements include:
-
Rigidity and Stability: The fixture must securely hold the mold without any deformation or movement during machining.
-
Accessibility: The design should allow unrestricted access to the mold for machining complex features.
-
Repeatability: The fixture must enable precise repositioning of the workpiece for consistent results.
-
Ease of Use: Simplified loading, unloading, and alignment processes improve operational efficiency.
-
Material Compatibility: The fixture material must withstand cutting forces, vibrations, and thermal effects without compromising performance.
Fixture Design Principles
The development of a specialized fixture begins with understanding the tire mold’s geometry, material, and machining requirements. Fundamental principles include:
-
Workpiece Analysis: Detailed study of the mold’s dimensions, tolerances, and features to determine clamping points.
-
Force Distribution: Ensuring uniform distribution of clamping forces to prevent distortion.
-
Dynamic Behavior: Analyzing vibrations and dynamic forces during machining to design a fixture that minimizes resonance.
-
Fixture Material Selection: Choosing materials with high strength-to-weight ratios, such as hardened steel or aluminum alloys.
-
Integration with Machine Tool: Ensuring compatibility with the machine’s kinematics and tooling system.
Types of Fixtures for Tire Mold Machining
1. Modular Fixtures
Modular fixtures consist of interchangeable components, allowing flexibility in adapting to various mold geometries. Advantages include:
-
Rapid reconfiguration for different workpieces.
-
Cost-effectiveness in low-volume production.
-
High adaptability to design changes.
2. Dedicated Fixtures
Dedicated fixtures are custom-designed for specific tire molds. Their advantages include:
-
Optimal precision and stability.
-
Reduced setup time for repetitive tasks.
-
Superior performance in high-volume production.
3. Vacuum-Based Fixtures
Vacuum fixtures use suction to hold the workpiece in place. They are particularly useful for:
-
Thin-walled molds prone to deformation.
-
Machining operations requiring unobstructed tool access.
Design Methodology
The design process for a five-axis tire mold fixture involves several stages:
1. Conceptual Design
The initial phase involves brainstorming and developing conceptual models. Tools such as CAD software are used to create digital mockups, incorporating:
-
Workpiece geometry.
-
Machine tool specifications.
-
Cutting tool paths.
2. Material Selection
Material properties, including hardness, tensile strength, and thermal conductivity, are evaluated. Common choices include:
Material | Hardness (HRC) | Tensile Strength (MPa) | Thermal Conductivity (W/mK) |
---|---|---|---|
Hardened Steel | 45-60 | 1200-2000 | 50 |
Aluminum Alloy | 30-40 | 400-600 | 150 |
Titanium Alloy | 35-45 | 800-1100 | 20 |
3. Structural Analysis
Finite Element Analysis (FEA) is employed to simulate the fixture’s performance under machining conditions. Key parameters include:
-
Stress distribution.
-
Deflection under load.
-
Vibration modes.
4. Prototyping and Testing
A physical prototype of the fixture is manufactured and tested under real machining conditions. Metrics such as positional accuracy, surface finish, and setup time are evaluated.
Advanced Features in Modern Fixtures
1. Automated Clamping Systems
Automated systems enhance precision and reduce setup time by using pneumatic, hydraulic, or electric actuators.
2. Adaptive Fixturing
Adaptive fixtures employ sensors and actuators to adjust clamping forces dynamically, accommodating variations in workpiece geometry.
3. Integrated Cooling Systems
Incorporating cooling channels within the fixture can dissipate heat generated during machining, preventing thermal distortion.
4. Smart Fixtures
IoT-enabled fixtures provide real-time monitoring of forces, vibrations, and temperatures, enabling predictive maintenance and quality assurance.
Comparison of Fixture Types
Feature | Modular Fixtures | Dedicated Fixtures | Vacuum Fixtures |
Adaptability | High | Low | Medium |
Precision | Medium | High | Medium |
Cost | Low | High | Medium |
Setup Time | Medium | Low | Low |
Application Versatility | High | Low | Medium |
Case Study: Implementation in Tire Mold Production
A tire manufacturer faced challenges with inconsistent machining accuracy and prolonged setup times. By designing a dedicated five-axis fixture with automated clamping and integrated cooling, the following improvements were achieved:
-
Cycle Time Reduction: 30% decrease in machining time.
-
Improved Accuracy: Dimensional tolerances improved by 20%.
-
Operator Efficiency: Setup time reduced from 40 minutes to 15 minutes.
Future Trends in Fixture Design
-
Additive Manufacturing: Using 3D printing to create lightweight, complex fixtures with optimized designs.
-
AI-Driven Optimization: Leveraging machine learning to analyze machining data and optimize fixture design in real time.
-
Sustainable Materials: Development of eco-friendly materials with high performance characteristics.
-
Virtual Simulation: Enhanced simulation tools for predicting fixture performance and optimizing designs before prototyping.
Conclusion
The design of a specialized fixture for five-axis tire mold machining is a multifaceted process that combines engineering principles, material science, and advanced manufacturing technologies. By addressing the unique challenges of tire mold production, such fixtures play a pivotal role in improving precision, efficiency, and overall product quality. Future advancements promise even greater capabilities, ensuring that tire mold machining continues to meet the evolving demands of the industry.
Reprint Statement: If there are no special instructions, all articles on this site are original. Please indicate the source for reprinting:https://www.cncmachiningptj.com/,thanks!
3, 4 and 5-axis precision CNC machining services for aluminum machining, beryllium, carbon steel, magnesium, titanium machining, Inconel, platinum, superalloy, acetal, polycarbonate, fiberglass, graphite and wood. Capable of machining parts up to 98 in. turning dia. and +/-0.001 in. straightness tolerance. Processes include milling, turning, drilling, boring, threading, tapping, forming, knurling, counterboring, countersinking, reaming and laser cutting. Secondary services such as assembly, centerless grinding, heat treating, plating and welding. Prototype and low to high volume production offered with maximum 50,000 units. Suitable for fluid power, pneumatics, hydraulics and valve applications. Serves the aerospace, aircraft, military, medical and defense industries.PTJ will strategize with you to provide the most cost-effective services to help you reach your target,Welcome to Contact us ( sales@pintejin.com ) directly for your new project.
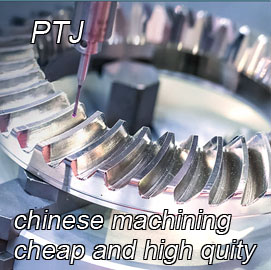
- 5 Axis Machining
- Cnc Milling
- Cnc Turning
- Machining Industries
- Machining Process
- Surface Treatment
- Metal Machining
- Plastic Machining
- Powder Metallurgy Mold
- Die Casting
- Parts Gallery
- Auto Metal Parts
- Machinery Parts
- LED Heatsink
- Building Parts
- Mobile Parts
- Medical Parts
- Electronic Parts
- Tailored Machining
- Bicycle Parts
- Aluminum Machining
- Titanium Machining
- Stainless Steel Machining
- Copper Machining
- Brass Machining
- Super Alloy Machining
- Peek Machining
- UHMW Machining
- Unilate Machining
- PA6 Machining
- PPS Machining
- Teflon Machining
- Inconel Machining
- Tool Steel Machining
- More Material