Application of 10bar Vacuum High Pressure Gas Quenching Furnace in Heat Treatment of Die Casting Molds
Die casting molds are critical components in the manufacturing industry, particularly in the production of complex metal parts. The performance and longevity of these molds are heavily influenced by the heat treatment processes they undergo. One of the most advanced and effective methods for heat treating die casting molds is the use of a 10bar vacuum high pressure gas quenching furnace. This article delves into the intricacies of this technology, its applications, benefits, and comparisons with other heat treatment methods.
Introduction to Vacuum High Pressure Gas Quenching
Vacuum high pressure gas quenching (HPGQ) is a specialized heat treatment process that combines the benefits of vacuum furnaces with the rapid cooling capabilities of high pressure gas quenching. This method is particularly effective for materials that require precise control over the cooling rate to achieve desired mechanical properties. The 10bar vacuum high pressure gas quenching furnace operates by heating the material in a vacuum environment to prevent oxidation and then rapidly cooling it using high pressure gas, typically nitrogen or helium, at pressures up to 10 bar.
Principles of 10bar Vacuum High Pressure Gas Quenching
The 10bar vacuum high pressure gas quenching furnace operates on several key principles:
-
Vacuum Environment: The furnace operates in a vacuum to prevent oxidation and contamination of the material during heating. This ensures that the material retains its purity and mechanical properties.
-
High Pressure Gas Quenching: After heating, the material is rapidly cooled using high pressure gas. The high pressure increases the cooling rate, allowing for more precise control over the microstructure and mechanical properties of the material.
-
Uniform Heating and Cooling: The furnace is designed to provide uniform heating and cooling, ensuring that the material is treated evenly throughout. This is crucial for achieving consistent mechanical properties.
-
Precise Temperature Control: The furnace is equipped with advanced temperature control systems that allow for precise regulation of the heating and cooling rates. This is essential for achieving the desired microstructure and mechanical properties.
Applications in Die Casting Molds
Die casting molds are subjected to high temperatures and pressures during the casting process, which can lead to wear, thermal fatigue, and other forms of degradation. The 10bar vacuum high pressure gas quenching furnace is particularly well-suited for the heat treatment of die casting molds due to its ability to achieve high hardness, wear resistance, and dimensional stability.
-
High Hardness: The rapid cooling rates achieved with high pressure gas quenching allow for the formation of a fine-grained microstructure, which results in high hardness. This is crucial for die casting molds, as it enhances their resistance to wear and abrasion.
-
Wear Resistance: The fine-grained microstructure also improves the wear resistance of the molds, extending their service life and reducing the need for frequent maintenance and replacement.
-
Dimensional Stability: The uniform heating and cooling provided by the furnace ensure that the molds retain their dimensional stability, which is essential for producing high-quality castings with consistent dimensions.
-
Corrosion Resistance: The vacuum environment prevents oxidation and contamination, enhancing the corrosion resistance of the molds. This is particularly important for molds used in corrosive environments.
Comparison with Other Heat Treatment Methods
To understand the advantages of the 10bar vacuum high pressure gas quenching furnace, it is useful to compare it with other common heat treatment methods. The following table provides a detailed comparison:
Feature | 10bar Vacuum HPGQ Furnace | Oil Quenching | Salt Bath Quenching | Air Quenching |
---|---|---|---|---|
Cooling Rate | Very High | High | High | Low |
Oxidation Prevention | Excellent | Poor | Poor | Poor |
Uniformity | Excellent | Fair | Fair | Poor |
Dimensional Stability | Excellent | Fair | Fair | Poor |
Corrosion Resistance | Excellent | Poor | Poor | Poor |
Environmental Impact | Low | High | High | Low |
Cost | High | Low | Low | Low |
Maintenance | Moderate | High | High | Low |
Oil Quenching
Oil quenching is a traditional heat treatment method that involves immersing the heated material in oil to achieve rapid cooling. While it can achieve high cooling rates, it has several drawbacks:
- Oxidation: The material is exposed to air during heating, leading to oxidation and contamination.
- Uniformity: The cooling rate can vary significantly across the material, leading to non-uniform properties.
- Environmental Impact: The use of oil can have environmental implications, including disposal and potential contamination.
Salt Bath Quenching
Salt bath quenching involves immersing the heated material in a molten salt bath to achieve rapid cooling. While it can achieve high cooling rates, it also has several drawbacks:
- Oxidation: Similar to oil quenching, the material is exposed to air during heating, leading to oxidation and contamination.
- Uniformity: The cooling rate can vary significantly across the material, leading to non-uniform properties.
- Environmental Impact: The use of molten salts can have environmental implications, including disposal and potential contamination.
Air Quenching
Air quenching involves cooling the heated material in air. While it is a simple and low-cost method, it has several drawbacks:
- Cooling Rate: The cooling rate is relatively low, which can lead to a coarse-grained microstructure and reduced mechanical properties.
- Oxidation: The material is exposed to air during heating and cooling, leading to oxidation and contamination.
- Uniformity: The cooling rate can vary significantly across the material, leading to non-uniform properties.
Benefits of 10bar Vacuum High Pressure Gas Quenching
The 10bar vacuum high pressure gas quenching furnace offers several key benefits for the heat treatment of die casting molds:
-
High Cooling Rates: The high pressure gas quenching allows for very high cooling rates, which are essential for achieving a fine-grained microstructure and high hardness.
-
Oxidation Prevention: The vacuum environment prevents oxidation and contamination, ensuring that the material retains its purity and mechanical properties.
-
Uniform Heating and Cooling: The furnace provides uniform heating and cooling, ensuring consistent mechanical properties throughout the material.
-
Dimensional Stability: The uniform heating and cooling ensure that the molds retain their dimensional stability, which is crucial for producing high-quality castings.
-
Corrosion Resistance: The vacuum environment enhances the corrosion resistance of the molds, which is particularly important for molds used in corrosive environments.
-
Environmental Benefits: The use of high pressure gas quenching eliminates the need for oil or molten salts, reducing the environmental impact of the heat treatment process.
Case Studies
Several case studies have demonstrated the effectiveness of the 10bar vacuum high pressure gas quenching furnace in the heat treatment of die casting molds.
Case Study 1: High-Strength Aluminum Alloy Molds
In one case study, high-strength aluminum alloy molds were heat treated using a 10bar vacuum high pressure gas quenching furnace. The molds were heated to a temperature of 530°C and then rapidly cooled using high pressure nitrogen gas at 10 bar. The results showed a significant improvement in hardness, wear resistance, and dimensional stability compared to molds treated using traditional oil quenching methods.
Case Study 2: Tool Steel Molds
In another case study, tool steel molds were heat treated using a 10bar vacuum high pressure gas quenching furnace. The molds were heated to a temperature of 1050°C and then rapidly cooled using high pressure helium gas at 10 bar. The results showed a significant improvement in hardness, wear resistance, and corrosion resistance compared to molds treated using traditional salt bath quenching methods.
Case Study 3: Stainless Steel Molds
In a third case study, stainless steel molds were heat treated using a 10bar vacuum high pressure gas quenching furnace. The molds were heated to a temperature of 1050°C and then rapidly cooled using high pressure nitrogen gas at 10 bar. The results showed a significant improvement in hardness, wear resistance, and dimensional stability compared to molds treated using traditional air quenching methods.
Technical Specifications
The technical specifications of a typical 10bar vacuum high pressure gas quenching furnace are as follows:
Parameter | Specification |
---|---|
Maximum Temperature | 1200°C |
Maximum Pressure | 10 bar |
Vacuum Level | 10^-3 mbar |
Heating Rate | Up to 20°C/min |
Cooling Rate | Up to 100°C/sec |
Chamber Size | Variable (depending on model) |
Gas Type | Nitrogen, Helium |
Power Supply | 3-phase, 400V, 50Hz |
Control System | PLC with touchscreen HMI |
Safety Features | Over-temperature protection, vacuum leak detection, emergency stop |
Operational Procedures
The operational procedures for using a 10bar vacuum high pressure gas quenching furnace are as follows:
-
Loading: The material to be heat treated is loaded into the furnace chamber.
-
Vacuum Pumping: The chamber is evacuated to a vacuum level of 10^-3 mbar to prevent oxidation and contamination.
-
Heating: The material is heated to the desired temperature using electrical heating elements. The heating rate is carefully controlled to ensure uniform heating.
-
Soaking: The material is held at the desired temperature for a specified period to allow for complete transformation of the microstructure.
-
Gas Quenching: The material is rapidly cooled using high pressure gas at pressures up to 10 bar. The cooling rate is carefully controlled to achieve the desired microstructure and mechanical properties.
-
Unloading: The material is unloaded from the furnace chamber after cooling.
Maintenance and Safety
Proper maintenance and safety procedures are essential for the effective operation of a 10bar vacuum high pressure gas quenching furnace.
-
Maintenance: Regular maintenance includes cleaning the furnace chamber, inspecting and replacing heating elements, and checking the vacuum and gas systems. Preventive maintenance schedules should be followed to ensure the longevity and reliability of the furnace.
-
Safety: Safety features include over-temperature protection, vacuum leak detection, and emergency stop buttons. Operators should be trained in the safe operation of the furnace and emergency procedures.
Future Trends
The future of vacuum high pressure gas quenching technology holds promise for further advancements and applications.
-
Advanced Materials: As new materials are developed, the need for advanced heat treatment methods will increase. Vacuum high pressure gas quenching is well-suited for treating advanced materials with complex microstructures and mechanical properties.
-
Automation: The integration of automation and artificial intelligence can enhance the precision and efficiency of the heat treatment process. Automated control systems can optimize heating and cooling rates, ensuring consistent and high-quality results.
-
Sustainability: The focus on sustainability and environmental impact will drive the development of more efficient and eco-friendly heat treatment methods. Vacuum high pressure gas quenching, with its low environmental impact, is well-positioned to meet these demands.
Conclusion
The 10bar vacuum high pressure gas quenching furnace represents a significant advancement in the heat treatment of die casting molds. Its ability to achieve high cooling rates, prevent oxidation, and ensure uniform heating and cooling makes it an ideal choice for enhancing the hardness, wear resistance, and dimensional stability of die casting molds. As the demand for high-quality and durable molds continues to grow, the application of this technology will play a crucial role in meeting the needs of the manufacturing industry.
In summary, the 10bar vacuum high pressure gas quenching furnace offers a range of benefits, including high cooling rates, oxidation prevention, uniform heating and cooling, dimensional stability, corrosion resistance, and environmental benefits. Its effectiveness has been demonstrated through various case studies, and its future holds promise for further advancements and applications. With proper maintenance and safety procedures, this technology can significantly enhance the performance and longevity of die casting molds, contributing to the overall efficiency and sustainability of the manufacturing process.
Reprint Statement: If there are no special instructions, all articles on this site are original. Please indicate the source for reprinting:https://www.cncmachiningptj.com/,thanks!
3, 4 and 5-axis precision CNC machining services for aluminum machining, beryllium, carbon steel, magnesium, titanium machining, Inconel, platinum, superalloy, acetal, polycarbonate, fiberglass, graphite and wood. Capable of machining parts up to 98 in. turning dia. and +/-0.001 in. straightness tolerance. Processes include milling, turning, drilling, boring, threading, tapping, forming, knurling, counterboring, countersinking, reaming and laser cutting. Secondary services such as assembly, centerless grinding, heat treating, plating and welding. Prototype and low to high volume production offered with maximum 50,000 units. Suitable for fluid power, pneumatics, hydraulics and valve applications. Serves the aerospace, aircraft, military, medical and defense industries.PTJ will strategize with you to provide the most cost-effective services to help you reach your target,Welcome to Contact us ( sales@pintejin.com ) directly for your new project.
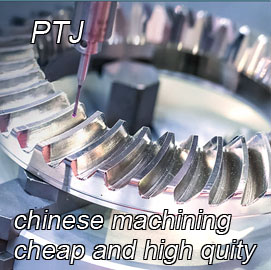
- 5 Axis Machining
- Cnc Milling
- Cnc Turning
- Machining Industries
- Machining Process
- Surface Treatment
- Metal Machining
- Plastic Machining
- Powder Metallurgy Mold
- Die Casting
- Parts Gallery
- Auto Metal Parts
- Machinery Parts
- LED Heatsink
- Building Parts
- Mobile Parts
- Medical Parts
- Electronic Parts
- Tailored Machining
- Bicycle Parts
- Aluminum Machining
- Titanium Machining
- Stainless Steel Machining
- Copper Machining
- Brass Machining
- Super Alloy Machining
- Peek Machining
- UHMW Machining
- Unilate Machining
- PA6 Machining
- PPS Machining
- Teflon Machining
- Inconel Machining
- Tool Steel Machining
- More Material