Hard Spots and Hard Metal Impurity Phases in Aluminum Die Castings
Aluminum die casting is a widely used manufacturing process that involves forcing molten aluminum into a steel mold under high pressure. This process is known for its ability to produce complex shapes with high dimensional accuracy and good surface finish. However, the quality of aluminum die castings can be compromised by the presence of hard spots and hard metal impurity phases, which can significantly impact the mechanical properties and performance of the cast components. This article provides a comprehensive overview of hard spots and hard metal impurity phases in aluminum die castings, their causes, detection methods, and strategies for mitigation.
Introduction to Aluminum Die Casting
Aluminum die casting is a versatile and efficient method for producing a wide range of components, from small intricate parts to large structural components. The process involves several key steps:
- Melting: Aluminum alloys are melted in a furnace to achieve a homogeneous liquid state.
- Injection: The molten aluminum is injected into a steel die under high pressure, typically ranging from 1,000 to 20,000 psi.
- Solidification: The molten aluminum solidifies rapidly within the die, forming the desired shape.
- Ejection: The solidified casting is ejected from the die and subjected to further processing, such as trimming and finishing.
The rapid solidification and high cooling rates in die casting can lead to the formation of microstructural defects, including hard spots and hard metal impurity phases. These defects can have detrimental effects on the mechanical properties, corrosion resistance, and overall performance of the castings.
Hard Spots in Aluminum Die Castings
Hard spots, also known as hard phases or hard inclusions, are localized regions within the aluminum die casting that exhibit higher hardness compared to the surrounding matrix. These spots are typically composed of intermetallic compounds or oxides that form during the solidification process. The formation of hard spots can be attributed to several factors, including:
- Alloy Composition: The presence of certain alloying elements, such as iron (Fe), manganese (Mn), and silicon (Si), can promote the formation of hard intermetallic compounds. For example, in aluminum-silicon (Al-Si) alloys, the presence of Fe can lead to the formation of hard Fe-rich intermetallics, such as Al5FeSi and Al15(Fe,Mn)3Si2.
- Cooling Rate: The high cooling rates in die casting can result in the formation of non-equilibrium phases, which can contribute to the formation of hard spots.
- Impurities: The presence of impurities, such as oxides and inclusions, can act as nucleation sites for the formation of hard spots.
Hard Metal Impurity Phases in Aluminum Die Castings
Hard metal impurity phases are distinct from hard spots and are typically composed of metallic elements that are not intentionally added to the aluminum alloy. These impurities can originate from various sources, including:
- Raw Materials: Impurities can be introduced through the raw materials used in the melting process, such as scrap aluminum or master alloys.
- Melting and Casting Equipment: Wear and tear of melting and casting equipment can introduce impurities, such as iron, chromium, and nickel, into the molten aluminum.
- Die Material: The steel die itself can be a source of impurities, particularly if the die is not properly maintained or if it contains residual material from previous castings.
Common hard metal impurity phases in aluminum die castings include:
- Iron-rich Phases: Iron is a common impurity in aluminum alloys and can form various intermetallic compounds, such as Al3Fe, Al6Fe, and Al5FeSi.
- Chromium-rich Phases: Chromium can form hard intermetallic compounds, such as Al7Cr and Al13Cr2.
- Nickel-rich Phases: Nickel can form intermetallic compounds, such as Al3Ni and Al3Ni2.
Table 1: Common Hard Spots and Hard Metal Impurity Phases in Aluminum Die Castings
Phase | Composition | Hardness (HV) | Cause |
---|---|---|---|
Al5FeSi | Al-Fe-Si | 800-1000 | Fe impurity, high cooling rate |
Al15(Fe,Mn)3Si2 | Al-Fe-Mn-Si | 700-900 | Fe and Mn impurities |
Al3Fe | Al-Fe | 600-800 | Fe impurity |
Al6Fe | Al-Fe | 700-900 | Fe impurity |
Al7Cr | Al-Cr | 900-1100 | Cr impurity |
Al13Cr2 | Al-Cr | 1000-1200 | Cr impurity |
Al3Ni | Al-Ni | 800-1000 | Ni impurity |
Al3Ni2 | Al-Ni | 900-1100 | Ni impurity |
Al2O3 | Al-O | 1500-2000 | Oxide impurity |
Detection of Hard Spots and Hard Metal Impurity Phases
The detection of hard spots and hard metal impurity phases in aluminum die castings is crucial for quality control and ensuring the performance of the cast components. Various techniques can be employed for the detection of these defects, including:
- Metallography: Metallographic examination involves preparing a cross-section of the casting and examining it under a microscope. This technique allows for the identification of hard spots and impurity phases based on their morphology and distribution.
- Hardness Testing: Hardness testing, such as Vickers or Brinell hardness testing, can be used to identify regions of higher hardness within the casting. This method is particularly useful for detecting hard spots.
- X-ray Diffraction (XRD): XRD can be used to identify the crystalline phases present in the casting. This technique is effective for identifying hard metal impurity phases based on their characteristic diffraction patterns.
- Energy-Dispersive X-ray Spectroscopy (EDS): EDS can be used to determine the chemical composition of hard spots and impurity phases. This technique is often used in conjunction with scanning electron microscopy (SEM) to provide detailed information about the microstructure.
- Computed Tomography (CT): CT scanning can be used to non-destructively examine the internal structure of the casting. This technique is particularly useful for detecting hard spots and impurity phases that are not visible on the surface.
Table 2: Comparison of Detection Techniques for Hard Spots and Hard Metal Impurity Phases
Technique | Description | Advantages | Limitations |
---|---|---|---|
Metallography | Microscopic examination of cross-sections | Visual identification of defects | Destructive, time-consuming |
Hardness Testing | Measurement of localized hardness | Quick and non-destructive | Limited to surface defects |
X-ray Diffraction | Identification of crystalline phases | High accuracy in phase identification | Requires sample preparation, destructive |
EDS | Chemical composition analysis | Detailed chemical information | Requires SEM, limited spatial resolution |
Computed Tomography | Non-destructive internal examination | Non-destructive, 3D visualization | Expensive, limited resolution |
Impact of Hard Spots and Hard Metal Impurity Phases on Casting Performance
The presence of hard spots and hard metal impurity phases can have significant impacts on the performance of aluminum die castings. These defects can affect various properties, including:
- Mechanical Properties: Hard spots and impurity phases can act as stress concentrators, leading to reduced ductility and toughness. They can also initiate cracks and promote fatigue failure.
- Corrosion Resistance: The presence of hard spots and impurity phases can create galvanic cells, leading to increased susceptibility to corrosion.
- Machinability: Hard spots and impurity phases can cause excessive tool wear and reduce the machinability of the casting.
- Surface Finish: The presence of hard spots and impurity phases can result in a poor surface finish, affecting the aesthetic and functional properties of the casting.
Table 3: Impact of Hard Spots and Hard Metal Impurity Phases on Casting Performance
Property | Impact of Hard Spots | Impact of Hard Metal Impurity Phases |
---|---|---|
Mechanical Properties | Reduced ductility and toughness, increased fatigue failure | Reduced strength and toughness, increased fatigue failure |
Corrosion Resistance | Increased susceptibility to galvanic corrosion | Increased susceptibility to galvanic corrosion |
Machinability | Excessive tool wear, reduced machinability | Excessive tool wear, reduced machinability |
Surface Finish | Poor surface finish, aesthetic and functional issues | Poor surface finish, aesthetic and functional issues |
Mitigation Strategies for Hard Spots and Hard Metal Impurity Phases
To minimize the formation of hard spots and hard metal impurity phases in aluminum die castings, various mitigation strategies can be employed:
- Alloy Composition Control: Careful control of the alloy composition can help reduce the formation of hard spots. This includes minimizing the content of impurity elements, such as Fe, Mn, and Cr.
- Melt Treatment: Melt treatment techniques, such as degassing and fluxing, can be used to remove impurities and reduce the formation of hard spots and impurity phases.
- Die Design and Maintenance: Proper die design and maintenance can help minimize the introduction of impurities from the die material. This includes regular cleaning and inspection of the die.
- Process Control: Optimizing the die casting process parameters, such as melt temperature, injection pressure, and cooling rate, can help reduce the formation of hard spots and impurity phases.
- Post-Casting Treatments: Post-casting treatments, such as heat treatment and hot isostatic pressing (HIP), can be used to modify the microstructure and reduce the impact of hard spots and impurity phases.
Table 4: Mitigation Strategies for Hard Spots and Hard Metal Impurity Phases
Strategy | Description | Benefits | Challenges |
---|---|---|---|
Alloy Composition Control | Minimizing impurity elements | Reduced formation of hard spots | Requires precise control of alloy composition |
Melt Treatment | Degassing and fluxing to remove impurities | Reduced impurities and hard spots | Requires additional equipment and processes |
Die Design and Maintenance | Regular cleaning and inspection of the die | Minimized introduction of impurities | Requires regular maintenance and inspection |
Process Control | Optimizing process parameters | Reduced formation of hard spots and impurities | Requires precise control of process parameters |
Post-Casting Treatments | Heat treatment and HIP | Modification of microstructure, reduced impact of defects | Requires additional equipment and processes |
Case Studies and Examples
Several case studies and examples illustrate the challenges and solutions associated with hard spots and hard metal impurity phases in aluminum die castings:
- Automotive Components: In the automotive industry, aluminum die castings are widely used for components such as engine blocks, cylinder heads, and transmission cases. The presence of hard spots and impurity phases can lead to reduced mechanical properties and increased wear, affecting the performance and reliability of the components. Mitigation strategies, such as alloy composition control and melt treatment, have been successfully employed to reduce these defects.
- Aerospace Applications: In the aerospace industry, aluminum die castings are used for structural components, such as landing gear and airframe parts. The presence of hard spots and impurity phases can compromise the structural integrity and corrosion resistance of these components. Advanced process control and post-casting treatments, such as HIP, have been used to minimize these defects.
- Consumer Electronics: In the consumer electronics industry, aluminum die castings are used for housings and structural components. The presence of hard spots and impurity phases can affect the surface finish and aesthetic properties of the components. Precise control of the die casting process and regular die maintenance have been effective in reducing these defects.
Conclusion
Hard spots and hard metal impurity phases are significant challenges in aluminum die casting, affecting the mechanical properties, corrosion resistance, and overall performance of the cast components. Understanding the causes, detection methods, and mitigation strategies for these defects is crucial for improving the quality and reliability of aluminum die castings. Through careful control of alloy composition, melt treatment, die design and maintenance, process control, and post-casting treatments, the formation and impact of hard spots and hard metal impurity phases can be minimized. Continued research and development in this area will further enhance the understanding and mitigation of these defects, contributing to the advancement of aluminum die casting technology.
Reprint Statement: If there are no special instructions, all articles on this site are original. Please indicate the source for reprinting:https://www.cncmachiningptj.com/,thanks!
3, 4 and 5-axis precision CNC machining services for aluminum machining, beryllium, carbon steel, magnesium, titanium machining, Inconel, platinum, superalloy, acetal, polycarbonate, fiberglass, graphite and wood. Capable of machining parts up to 98 in. turning dia. and +/-0.001 in. straightness tolerance. Processes include milling, turning, drilling, boring, threading, tapping, forming, knurling, counterboring, countersinking, reaming and laser cutting. Secondary services such as assembly, centerless grinding, heat treating, plating and welding. Prototype and low to high volume production offered with maximum 50,000 units. Suitable for fluid power, pneumatics, hydraulics and valve applications. Serves the aerospace, aircraft, military, medical and defense industries.PTJ will strategize with you to provide the most cost-effective services to help you reach your target,Welcome to Contact us ( sales@pintejin.com ) directly for your new project.
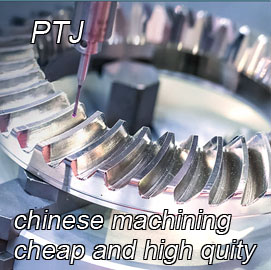
- 5 Axis Machining
- Cnc Milling
- Cnc Turning
- Machining Industries
- Machining Process
- Surface Treatment
- Metal Machining
- Plastic Machining
- Powder Metallurgy Mold
- Die Casting
- Parts Gallery
- Auto Metal Parts
- Machinery Parts
- LED Heatsink
- Building Parts
- Mobile Parts
- Medical Parts
- Electronic Parts
- Tailored Machining
- Bicycle Parts
- Aluminum Machining
- Titanium Machining
- Stainless Steel Machining
- Copper Machining
- Brass Machining
- Super Alloy Machining
- Peek Machining
- UHMW Machining
- Unilate Machining
- PA6 Machining
- PPS Machining
- Teflon Machining
- Inconel Machining
- Tool Steel Machining
- More Material