Over-Positioning in Die Casting Mold Design: Causes, Effects, and Improvement Measures
Die casting is a manufacturing process that involves forcing molten metal under high pressure into a mold cavity. The mold—also known as a die—is typically made of hardened tool steel and is designed to produce precise, high-quality metal parts. One of the critical challenges in die casting mold design is over-positioning, a phenomenon that can lead to various defects and inefficiencies in the casting process. This article delves into the causes and effects of over-positioning and explores a range of improvement measures to mitigate this issue, providing a comprehensive scientific overview supported by detailed tables and comparisons.
Understanding Over-Positioning
Over-positioning in die casting refers to the excessive or improper positioning of the mold components, which can lead to misalignment, increased wear and tear, and reduced part quality. This issue arises from various factors, including design flaws, manufacturing inaccuracies, and operational errors. Over-positioning can manifest in several ways, such as misaligned cores, improperly fitted inserts, and excessive clearances between mold components.
Causes of Over-Positioning
-
Design Flaws: Inadequate design considerations, such as poor tolerance specifications, inappropriate material selection, and insufficient structural support, can lead to over-positioning. Designers may overlook critical aspects like thermal expansion, stress distribution, and alignment requirements, resulting in a suboptimal mold design.
-
Manufacturing Inaccuracies: Precision in manufacturing is crucial for die casting molds. Any deviations in machining, assembly, or finishing processes can contribute to over-positioning. For instance, improper machining tolerances, misaligned assembly jigs, and inadequate surface finishing can all lead to misalignment and excessive positioning.
-
Operational Errors: During the die casting process, operational factors such as incorrect clamping forces, uneven temperature distribution, and improper lubrication can exacerbate over-positioning issues. Operators must ensure that the mold is correctly aligned and secured before each casting cycle to minimize these errors.
Effects of Over-Positioning
Over-positioning can have several detrimental effects on the die casting process and the final product quality. Some of the key impacts include:
-
Reduced Part Quality: Misaligned mold components can result in dimensional inaccuracies, surface defects, and poor finish quality. These issues can compromise the functionality and aesthetics of the cast parts, leading to increased rejection rates and rework.
-
Increased Wear and Tear: Excessive positioning can accelerate the wear and tear of mold components, reducing their lifespan and increasing maintenance costs. Misaligned cores and inserts can cause uneven stress distribution, leading to premature failure of critical mold elements.
-
Process Inefficiencies: Over-positioning can disrupt the smooth operation of the die casting process, resulting in longer cycle times, increased downtime, and reduced productivity. Misaligned molds can also lead to incomplete filling, air entrapment, and other casting defects, further impacting process efficiency.
-
Safety Concerns: In severe cases, over-positioning can pose safety risks to operators and equipment. Misaligned molds can cause excessive pressure buildup, leading to mold breakage or even explosions. Proper alignment and positioning are essential for ensuring a safe and efficient die casting process.
Improvement Measures
Addressing over-positioning in die casting mold design requires a multifaceted approach that encompasses design optimization, manufacturing precision, and operational best practices. The following sections outline various improvement measures to mitigate over-positioning issues.
Design Optimization
- Tolerance Specification: Accurate tolerance specification is crucial for ensuring proper alignment and positioning of mold components. Designers should consider the thermal expansion, stress distribution, and alignment requirements when specifying tolerances. Table 1 provides a comparison of typical tolerance ranges for different mold components.
Mold Component | Typical Tolerance Range | Optimal Tolerance Range |
---|---|---|
Cores | ±0.05 mm to ±0.1 mm | ±0.02 mm to ±0.05 mm |
Inserts | ±0.05 mm to ±0.1 mm | ±0.02 mm to ±0.05 mm |
Cavities | ±0.05 mm to ±0.1 mm | ±0.02 mm to ±0.05 mm |
Ejector Pins | ±0.05 mm to ±0.1 mm | ±0.02 mm to ±0.05 mm |
- Material Selection: Choosing the right material for mold components is essential for minimizing over-positioning. Materials with high wear resistance, thermal stability, and dimensional accuracy should be preferred. Table 2 compares the properties of commonly used mold materials.
Material | Wear Resistance | Thermal Stability | Dimensional Accuracy |
---|---|---|---|
Tool Steel | High | High | High |
Stainless Steel | Medium | High | Medium |
Aluminum | Low | Medium | Medium |
Copper Alloys | Medium | High | Medium |
- Structural Support: Adequate structural support is necessary to prevent misalignment and excessive positioning. Designers should incorporate reinforcing ribs, support pillars, and other structural elements to enhance the rigidity and stability of the mold.
Manufacturing Precision
- Machining Tolerances: Precise machining is critical for achieving the desired tolerances and minimizing over-positioning. Advanced machining techniques, such as CNC milling, EDM, and laser cutting, should be employed to ensure high accuracy and consistency. Table 3 compares the machining tolerances achievable with different techniques.
Machining Technique | Achievable Tolerance Range |
---|---|
CNC Milling | ±0.01 mm to ±0.05 mm |
EDM | ±0.005 mm to ±0.02 mm |
Laser Cutting | ±0.01 mm to ±0.05 mm |
Grinding | ±0.005 mm to ±0.02 mm |
-
Assembly Jigs: Proper assembly jigs are essential for ensuring accurate alignment and positioning of mold components during assembly. Custom-designed jigs should be used to maintain precise tolerances and minimize misalignment.
-
Surface Finishing: High-quality surface finishing is crucial for reducing friction, improving wear resistance, and enhancing dimensional accuracy. Techniques such as polishing, honing, and coating should be employed to achieve the desired surface finish.
Operational Best Practices
-
Clamping Forces: Appropriate clamping forces are essential for securing the mold and preventing misalignment during the casting process. Operators should ensure that the clamping forces are within the specified range to avoid excessive stress and deformation.
-
Temperature Control: Uniform temperature distribution is critical for maintaining dimensional accuracy and preventing thermal distortion. Operators should monitor and control the temperature of the mold and the molten metal to ensure consistent casting conditions.
-
Lubrication: Proper lubrication is essential for reducing friction, improving wear resistance, and enhancing the lifespan of mold components. Operators should use high-quality lubricants and ensure that all moving parts are adequately lubricated before each casting cycle.
Case Studies and Comparative Analysis
To illustrate the effectiveness of the improvement measures discussed, let's examine a few case studies and perform a comparative analysis. Table 4 presents a comparison of over-positioning issues and their resolution in different die casting applications.
Case Study | Industry | Over-Positioning Issue | Improvement Measures | Outcome |
---|---|---|---|---|
1 | Automotive | Misaligned cores | Redesigned cores with tighter tolerances, improved assembly jigs | Reduced misalignment, improved part quality |
2 | Aerospace | Excessive wear on inserts | Changed insert material to tool steel, enhanced structural support | Increased insert lifespan, reduced maintenance costs |
3 | Electronics | Incomplete filling | Optimized clamping forces, improved temperature control | Complete filling, reduced cycle times |
4 | Consumer Goods | Surface defects | Enhanced surface finishing, used high-quality lubricants | Improved surface finish, reduced rejection rates |
Conclusion
Over-positioning in die casting mold design is a complex issue that can significantly impact part quality, process efficiency, and safety. By understanding the causes and effects of over-positioning, designers, manufacturers, and operators can implement a range of improvement measures to mitigate this issue. Design optimization, manufacturing precision, and operational best practices are essential for ensuring accurate alignment, minimizing wear and tear, and enhancing the overall efficiency of the die casting process. Through continuous research, innovation, and collaboration, the die casting industry can overcome the challenges of over-positioning and achieve higher levels of precision, quality, and productivity.
Reprint Statement: If there are no special instructions, all articles on this site are original. Please indicate the source for reprinting:https://www.cncmachiningptj.com/,thanks!
3, 4 and 5-axis precision CNC machining services for aluminum machining, beryllium, carbon steel, magnesium, titanium machining, Inconel, platinum, superalloy, acetal, polycarbonate, fiberglass, graphite and wood. Capable of machining parts up to 98 in. turning dia. and +/-0.001 in. straightness tolerance. Processes include milling, turning, drilling, boring, threading, tapping, forming, knurling, counterboring, countersinking, reaming and laser cutting. Secondary services such as assembly, centerless grinding, heat treating, plating and welding. Prototype and low to high volume production offered with maximum 50,000 units. Suitable for fluid power, pneumatics, hydraulics and valve applications. Serves the aerospace, aircraft, military, medical and defense industries.PTJ will strategize with you to provide the most cost-effective services to help you reach your target,Welcome to Contact us ( sales@pintejin.com ) directly for your new project.
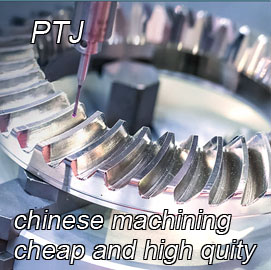
- 5 Axis Machining
- Cnc Milling
- Cnc Turning
- Machining Industries
- Machining Process
- Surface Treatment
- Metal Machining
- Plastic Machining
- Powder Metallurgy Mold
- Die Casting
- Parts Gallery
- Auto Metal Parts
- Machinery Parts
- LED Heatsink
- Building Parts
- Mobile Parts
- Medical Parts
- Electronic Parts
- Tailored Machining
- Bicycle Parts
- Aluminum Machining
- Titanium Machining
- Stainless Steel Machining
- Copper Machining
- Brass Machining
- Super Alloy Machining
- Peek Machining
- UHMW Machining
- Unilate Machining
- PA6 Machining
- PPS Machining
- Teflon Machining
- Inconel Machining
- Tool Steel Machining
- More Material