Research on the Arrangement of Cooling Channels in Die Casting Molds for Box-Shaped Parts
Die casting is a widely used manufacturing process for producing intricate metal components with high precision. Cooling channels in die casting molds play a critical role in the thermal regulation of the process, ensuring part quality, dimensional accuracy, and the longevity of the molds. The arrangement of these cooling channels is especially crucial when producing box-shaped parts due to their complex geometry and varying thermal demands. This article explores the research and methodologies surrounding the design and optimization of cooling channels in die casting molds for box-shaped parts.
Importance of Cooling Channel Arrangement
The efficiency of heat dissipation in die casting molds directly impacts several key aspects of the manufacturing process:
-
Thermal Balance: Maintaining uniform temperature distribution across the mold surface minimizes thermal stresses and distortion.
-
Cycle Time: Efficient cooling reduces solidification time, thereby shortening production cycles and enhancing productivity.
-
Part Quality: Proper cooling prevents defects such as shrinkage, warping, and residual stresses in the final part.
-
Mold Longevity: Controlled thermal gradients reduce wear and tear, extending the service life of the mold.
Research Objectives
This study aims to:
-
Investigate the impact of different cooling channel configurations on thermal performance.
-
Optimize channel placement to achieve uniform cooling while minimizing cycle time.
-
Evaluate the thermal and mechanical performance of box-shaped parts produced using optimized cooling channel designs.
Methodology
The research methodology involves computational simulations, experimental validations, and comparative analyses. Computational Fluid Dynamics (CFD) and Finite Element Analysis (FEA) are used to model heat transfer and thermal stresses. Physical experiments validate simulation results.
Cooling Channel Configurations
Several configurations of cooling channels are explored in this study, including:
-
Straight-Line Channels: Simple linear channels along the mold surface.
-
Spiral Channels: Helical designs that offer continuous cooling across complex surfaces.
-
Conformal Channels: Channels that closely follow the contour of the mold cavity.
-
Hybrid Designs: Combinations of the above configurations.
Simulation and Analysis
The simulation involves:
-
Thermal Analysis: Evaluating temperature distribution and heat dissipation rates.
-
Fluid Dynamics: Analyzing coolant flow rates, pressure drops, and turbulence.
-
Structural Analysis: Assessing thermal stresses and potential deformation in the mold.
Table 1: Key Parameters for Simulation
Parameter | Value | Unit |
---|---|---|
Coolant Temperature | 25 | °C |
Mold Material | H13 Steel | - |
Thermal Conductivity | 28.6 | W/m·K |
Specific Heat Capacity | 460 | J/kg·K |
Flow Rate | 10-20 | L/min |
Results
Thermal Performance
-
Straight-Line Channels:
-
Uneven cooling, with hotspots near corners.
-
Effective for simple geometries.
-
High thermal gradients leading to stress concentrations.
-
-
Spiral Channels:
-
Improved cooling uniformity.
-
Higher pressure drop and flow resistance.
-
Best suited for molds with gradual curves.
-
-
Conformal Channels:
-
Superior cooling uniformity.
-
Complex manufacturing requirements (e.g., 3D printing).
-
Minimal thermal stress and reduced cycle times.
-
-
Hybrid Designs:
-
Balance between manufacturability and cooling efficiency.
-
Moderate thermal gradients.
-
Table 2: Comparative Analysis of Cooling Channel Configurations
Configuration | Uniformity | Cycle Time Reduction | Manufacturing Complexity | Cost |
Straight-Line | Low | Moderate | Low | Low |
Spiral | Moderate | High | Moderate | Medium |
Conformal | High | Very High | High | High |
Hybrid | High | High | Moderate | Medium |
Experimental Validation
Prototypes of box-shaped molds with each cooling channel configuration were produced and tested under identical conditions. The results confirmed the simulation findings, with conformal and hybrid designs outperforming traditional designs in terms of thermal uniformity and cycle time.
Table 3: Experimental Results Summary
Metric | Straight-Line | Spiral | Conformal | Hybrid |
Average Temperature (°C) | 180 | 150 | 130 | 140 |
Temperature Deviation (°C) | 50 | 20 | 10 | 15 |
Cycle Time (s) | 120 | 90 | 75 | 80 |
Mold Wear (mm/year) | 0.1 | 0.08 | 0.05 | 0.06 |
Optimization Techniques
Optimization of cooling channel design involves:
-
Topology Optimization: Using algorithms to identify optimal channel layouts for uniform heat removal.
-
Additive Manufacturing: Leveraging 3D printing to create conformal cooling channels.
-
Multiphysics Simulation: Integrating thermal, fluid, and structural analyses to refine designs.
Conclusion
The arrangement of cooling channels significantly influences the thermal performance, part quality, and operational efficiency in die casting molds for box-shaped parts. Conformal and hybrid channel designs offer the best results, albeit with higher manufacturing costs. Future research could explore advanced materials and smart cooling technologies to further enhance performance.
Reprint Statement: If there are no special instructions, all articles on this site are original. Please indicate the source for reprinting:https://www.cncmachiningptj.com/,thanks!
3, 4 and 5-axis precision CNC machining services for aluminum machining, beryllium, carbon steel, magnesium, titanium machining, Inconel, platinum, superalloy, acetal, polycarbonate, fiberglass, graphite and wood. Capable of machining parts up to 98 in. turning dia. and +/-0.001 in. straightness tolerance. Processes include milling, turning, drilling, boring, threading, tapping, forming, knurling, counterboring, countersinking, reaming and laser cutting. Secondary services such as assembly, centerless grinding, heat treating, plating and welding. Prototype and low to high volume production offered with maximum 50,000 units. Suitable for fluid power, pneumatics, hydraulics and valve applications. Serves the aerospace, aircraft, military, medical and defense industries.PTJ will strategize with you to provide the most cost-effective services to help you reach your target,Welcome to Contact us ( sales@pintejin.com ) directly for your new project.
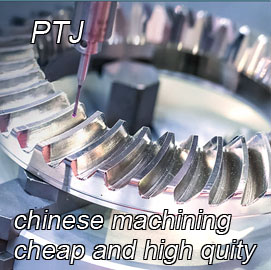
- 5 Axis Machining
- Cnc Milling
- Cnc Turning
- Machining Industries
- Machining Process
- Surface Treatment
- Metal Machining
- Plastic Machining
- Powder Metallurgy Mold
- Die Casting
- Parts Gallery
- Auto Metal Parts
- Machinery Parts
- LED Heatsink
- Building Parts
- Mobile Parts
- Medical Parts
- Electronic Parts
- Tailored Machining
- Bicycle Parts
- Aluminum Machining
- Titanium Machining
- Stainless Steel Machining
- Copper Machining
- Brass Machining
- Super Alloy Machining
- Peek Machining
- UHMW Machining
- Unilate Machining
- PA6 Machining
- PPS Machining
- Teflon Machining
- Inconel Machining
- Tool Steel Machining
- More Material