Design and Manufacture of Die Casting Molds for Housing Parts
Die casting is a manufacturing process that involves forcing molten metal under high pressure into a mold cavity. This process is widely used for producing complex shapes with high dimensional accuracy and a smooth surface finish. One of the critical components in die casting is the mold, which determines the final shape and quality of the cast part. This article delves into the design and manufacture of die casting molds, with a specific focus on housing parts.
Introduction to Die Casting Molds
Die casting molds are precision-engineered tools designed to withstand the high pressures and temperatures involved in the die casting process. These molds are typically made from high-strength tool steels and are designed to produce thousands of parts before requiring maintenance or replacement. The design of a die casting mold involves several key considerations, including the geometry of the part, the material properties, the cooling system, and the ejection mechanism.
Material Selection for Die Casting Molds
The choice of material for die casting molds is crucial as it directly affects the durability, performance, and cost of the mold. Common materials used for die casting molds include:
- H13 Tool Steel: This is one of the most commonly used materials for die casting molds due to its excellent wear resistance, high strength, and good thermal conductivity.
- P20 Tool Steel: This material is preferred for its good machinability and lower cost compared to H13. However, it has lower wear resistance and strength.
- Stainless Steel: Used in applications where corrosion resistance is required, although it is less common due to its higher cost and lower thermal conductivity.
- Beryllium Copper: This material is used for specific components within the mold, such as cores and inserts, due to its excellent thermal conductivity and wear resistance.
Table 1: Comparison of Common Die Casting Mold Materials
Material | Wear Resistance | Strength | Thermal Conductivity | Machinability | Cost |
---|---|---|---|---|---|
H13 Tool Steel | High | High | Good | Fair | Moderate |
P20 Tool Steel | Moderate | Moderate | Fair | Good | Low |
Stainless Steel | Moderate | Moderate | Poor | Fair | High |
Beryllium Copper | High | High | Excellent | Fair | High |
Design Considerations for Die Casting Molds
The design of a die casting mold involves several critical considerations to ensure the production of high-quality parts. These considerations include:
- Part Geometry: The shape and dimensions of the housing part must be accurately represented in the mold design. This includes consideration of draft angles, parting lines, and undercuts.
- Runner and Gate System: The runner and gate system is designed to efficiently deliver molten metal to the mold cavity. The design must ensure uniform filling and minimize turbulence to avoid defects.
- Cooling System: An effective cooling system is essential to control the temperature of the mold and ensure uniform solidification of the molten metal. This involves the design of cooling channels and the selection of cooling media.
- Ejection Mechanism: The ejection mechanism is designed to remove the cast part from the mold without damaging it. This typically involves the use of ejector pins and sleeves.
- Venting: Proper venting is crucial to allow air to escape from the mold cavity during filling, preventing the formation of porosity and other defects.
Table 2: Key Design Considerations for Die Casting Molds
Consideration | Description | Importance |
---|---|---|
Part Geometry | Accurate representation of part shape and dimensions | High |
Runner and Gate System | Efficient delivery of molten metal to the mold cavity | High |
Cooling System | Control of mold temperature and uniform solidification | High |
Ejection Mechanism | Removal of cast part without damage | High |
Venting | Allowance for air escape to prevent defects | High |
Manufacturing Process of Die Casting Molds
The manufacturing process of die casting molds involves several steps, each requiring precision and attention to detail. The key steps include:
- Mold Design: The initial step involves creating a detailed design of the mold using computer-aided design (CAD) software. This design includes all the critical features and dimensions of the mold.
- Material Selection: Based on the design requirements, the appropriate material for the mold is selected. This decision is influenced by factors such as wear resistance, thermal conductivity, and cost.
- Machining: The mold is machined from the selected material using high-precision CNC machines. This process involves milling, drilling, and turning operations to create the mold cavity, runner system, and cooling channels.
- Heat Treatment: The mold is subjected to heat treatment to enhance its mechanical properties, such as hardness and wear resistance. This typically involves processes such as quenching and tempering.
- Finishing: The final step involves finishing operations such as polishing and coating to achieve the desired surface finish and improve the mold's performance.
Table 3: Manufacturing Steps for Die Casting Molds
Step | Description | Tools/Techniques Used |
---|---|---|
Mold Design | Detailed design of the mold using CAD software | CAD software (e.g., SolidWorks, AutoCAD) |
Material Selection | Selection of appropriate material based on design requirements | Material properties database |
Machining | Precision machining of the mold | CNC machines, milling, drilling, turning |
Heat Treatment | Enhancement of mechanical properties | Quenching, tempering |
Finishing | Achievement of desired surface finish | Polishing, coating |
Cooling System Design
The cooling system is a critical component of the die casting mold, as it directly affects the quality and productivity of the casting process. An effective cooling system ensures uniform solidification of the molten metal, reducing the risk of defects such as porosity and warpage. The design of the cooling system involves the following considerations:
- Cooling Channels: The placement and design of cooling channels are crucial for effective heat removal. These channels are typically machined into the mold and connected to a cooling circuit.
- Cooling Media: The selection of the cooling media, such as water or oil, depends on the required cooling rate and the properties of the molten metal.
- Flow Rate: The flow rate of the cooling media must be carefully controlled to ensure uniform cooling and prevent hot spots.
- Temperature Control: The temperature of the cooling media must be maintained within a specific range to ensure consistent cooling and prevent thermal shock to the mold.
Table 4: Cooling System Design Considerations
Consideration | Description | Importance |
---|---|---|
Cooling Channels | Placement and design of cooling channels for effective heat removal | High |
Cooling Media | Selection of cooling media based on required cooling rate | High |
Flow Rate | Control of cooling media flow rate for uniform cooling | High |
Temperature Control | Maintenance of cooling media temperature for consistent cooling | High |
Ejection Mechanism Design
The ejection mechanism is designed to remove the cast part from the mold without damaging it. This mechanism typically involves the use of ejector pins and sleeves, which are activated at the end of the casting cycle. The design of the ejection mechanism involves the following considerations:
- Ejector Pins: The placement and design of ejector pins are crucial for effective part ejection. These pins must be positioned to apply uniform pressure on the part and avoid damage.
- Ejector Sleeves: Ejector sleeves are used to guide the ejector pins and ensure smooth operation. The design must consider the clearance and alignment of the sleeves.
- Ejection Force: The ejection force must be carefully controlled to ensure the part is removed without damage. This involves the design of the ejection mechanism and the selection of the actuation system.
- Timing: The timing of the ejection mechanism must be synchronized with the casting cycle to ensure the part is ejected at the correct time.
Table 5: Ejection Mechanism Design Considerations
Consideration | Description | Importance |
---|---|---|
Ejector Pins | Placement and design of ejector pins for effective part ejection | High |
Ejector Sleeves | Design of ejector sleeves for smooth operation | High |
Ejection Force | Control of ejection force to prevent part damage | High |
Timing | Synchronization of ejection mechanism with casting cycle | High |
Venting System Design
Proper venting is crucial to allow air to escape from the mold cavity during filling, preventing the formation of porosity and other defects. The design of the venting system involves the following considerations:
- Vent Channels: The placement and design of vent channels are crucial for effective air escape. These channels must be positioned to allow air to escape without interfering with the flow of molten metal.
- Vent Size: The size of the vent channels must be carefully controlled to ensure effective venting without allowing molten metal to escape.
- Vent Location: The location of the vent channels must be strategically placed to ensure air can escape from all areas of the mold cavity.
- Vent Material: The material used for the vent channels must be compatible with the molten metal and the mold material to prevent contamination and wear.
Table 6: Venting System Design Considerations
Consideration | Description | Importance |
---|---|---|
Vent Channels | Placement and design of vent channels for effective air escape | High |
Vent Size | Control of vent channel size for effective venting | High |
Vent Location | Strategic placement of vent channels for complete air escape | High |
Vent Material | Selection of vent channel material for compatibility and durability | High |
Quality Control and Inspection
Quality control and inspection are critical steps in the manufacturing process of die casting molds. These steps ensure that the mold meets the required specifications and performs as intended. The key quality control and inspection steps include:
- Dimensional Inspection: The dimensions of the mold are inspected using precision measuring tools to ensure they meet the design specifications.
- Surface Finish Inspection: The surface finish of the mold is inspected to ensure it meets the required standards for smoothness and uniformity.
- Functional Testing: The mold is subjected to functional testing to ensure it performs as intended under operating conditions. This includes testing the cooling system, ejection mechanism, and venting system.
- Non-Destructive Testing: Non-destructive testing methods, such as ultrasonic testing and magnetic particle inspection, are used to detect internal defects and ensure the structural integrity of the mold.
Table 7: Quality Control and Inspection Steps
Step | Description | Tools/Techniques Used |
---|---|---|
Dimensional Inspection | Inspection of mold dimensions using precision measuring tools | Coordinate measuring machines (CMM), calipers |
Surface Finish Inspection | Inspection of mold surface finish for smoothness and uniformity | Surface profilometers, visual inspection |
Functional Testing | Testing of mold performance under operating conditions | Cooling system testing, ejection mechanism testing |
Non-Destructive Testing | Detection of internal defects and structural integrity | Ultrasonic testing, magnetic particle inspection |
Maintenance and Repair
Die casting molds are subject to wear and tear due to the high pressures and temperatures involved in the casting process. Regular maintenance and repair are essential to ensure the mold continues to perform as intended and produces high-quality parts. The key maintenance and repair steps include:
- Cleaning: Regular cleaning of the mold is essential to remove any buildup of material and ensure smooth operation.
- Inspection: Regular inspection of the mold is necessary to detect any signs of wear or damage and take corrective action.
- Repair: Any detected defects or damage must be repaired promptly to prevent further deterioration and ensure the mold continues to perform as intended.
- Replacement: In cases of severe wear or damage, replacement of the mold or specific components may be necessary to ensure continued performance.
Table 8: Maintenance and Repair Steps
Step | Description | Tools/Techniques Used |
---|---|---|
Cleaning | Regular cleaning of the mold to remove material buildup | Cleaning solutions, brushes, compressed air |
Inspection | Regular inspection of the mold for signs of wear or damage | Visual inspection, dimensional inspection |
Repair | Repair of detected defects or damage | Welding, machining, polishing |
Replacement | Replacement of the mold or specific components in cases of severe wear | New mold or components |
Case Studies
Case Study 1: Design and Manufacture of a Die Casting Mold for an Automotive Housing Part
Background: An automotive manufacturer required a die casting mold for producing a housing part for a new vehicle model. The part had complex geometry and required high dimensional accuracy and surface finish.
Design Considerations: The mold design involved the creation of a detailed CAD model, including the part geometry, runner and gate system, cooling system, ejection mechanism, and venting system. The material selected for the mold was H13 tool steel due to its excellent wear resistance and thermal conductivity.
Manufacturing Process: The mold was manufactured using high-precision CNC machines to create the mold cavity, runner system, and cooling channels. The mold was then subjected to heat treatment to enhance its mechanical properties and finished with polishing and coating to achieve the desired surface finish.
Quality Control and Inspection: The mold underwent dimensional inspection using a coordinate measuring machine (CMM) and surface finish inspection using a surface profilometer. Functional testing of the cooling system, ejection mechanism, and venting system was also conducted to ensure the mold performed as intended.
Results: The die casting mold produced high-quality housing parts with the required dimensional accuracy and surface finish. The mold performed reliably under operating conditions, and regular maintenance and inspection ensured its continued performance.
Case Study 2: Design and Manufacture of a Die Casting Mold for an Electronics Housing Part
Background: An electronics manufacturer required a die casting mold for producing a housing part for a new consumer electronics device. The part had intricate details and required a smooth surface finish.
Design Considerations: The mold design involved the creation of a detailed CAD model, including the part geometry, runner and gate system, cooling system, ejection mechanism, and venting system. The material selected for the mold was P20 tool steel due to its good machinability and lower cost.
Manufacturing Process: The mold was manufactured using high-precision CNC machines to create the mold cavity, runner system, and cooling channels. The mold was then subjected to heat treatment to enhance its mechanical properties and finished with polishing and coating to achieve the desired surface finish.
Quality Control and Inspection: The mold underwent dimensional inspection using a coordinate measuring machine (CMM) and surface finish inspection using a surface profilometer. Functional testing of the cooling system, ejection mechanism, and venting system was also conducted to ensure the mold performed as intended.
Results: The die casting mold produced high-quality housing parts with the required dimensional accuracy and surface finish. The mold performed reliably under operating conditions, and regular maintenance and inspection ensured its continued performance.
Conclusion
The design and manufacture of die casting molds for housing parts involve a complex interplay of material selection, design considerations, manufacturing processes, and quality control. Each step in the process requires precision and attention to detail to ensure the production of high-quality parts. By carefully considering the geometry of the part, the runner and gate system, the cooling system, the ejection mechanism, and the venting system, manufacturers can create die casting molds that meet the required specifications and perform reliably under operating conditions. Regular maintenance and inspection are essential to ensure the mold continues to perform as intended and produces high-quality parts.
Future Trends
The field of die casting mold design and manufacture is continually evolving, driven by advancements in technology and the increasing demand for high-quality, complex parts. Some of the future trends in this field include:
- Advanced Materials: The development of new materials with improved wear resistance, thermal conductivity, and machinability will enhance the performance and durability of die casting molds.
- Additive Manufacturing: The use of additive manufacturing techniques, such as 3D printing, will enable the creation of complex mold geometries that are difficult or impossible to achieve with traditional manufacturing methods.
- Simulation and Optimization: The use of advanced simulation and optimization tools will enable more accurate prediction of mold performance and the identification of potential issues before manufacturing.
- Automation and Robotics: The integration of automation and robotics in the manufacturing process will improve efficiency, reduce costs, and enhance the consistency and quality of die casting molds.
- Sustainability: The increasing focus on sustainability will drive the development of more environmentally friendly materials and manufacturing processes for die casting molds.
Table 9: Future Trends in Die Casting Mold Design and Manufacture
Trend | Description | Potential Impact |
---|---|---|
Advanced Materials | Development of new materials with improved properties | Enhanced performance and durability |
Additive Manufacturing | Use of 3D printing for complex mold geometries | Increased design flexibility |
Simulation and Optimization | Advanced tools for predicting mold performance | Improved accuracy and issue identification |
Automation and Robotics | Integration of automation and robotics in manufacturing | Improved efficiency, reduced costs |
Sustainability | Development of environmentally friendly materials and processes | Reduced environmental impact |
In conclusion, the design and manufacture of die casting molds for housing parts are critical processes that require a deep understanding of material properties, design considerations, manufacturing techniques, and quality control. By leveraging advancements in technology and adopting best practices, manufacturers can create die casting molds that meet the highest standards of quality and performance. The future of this field holds exciting possibilities for innovation and improvement, driven by the ongoing pursuit of excellence and sustainability.
Reprint Statement: If there are no special instructions, all articles on this site are original. Please indicate the source for reprinting:https://www.cncmachiningptj.com/,thanks!
3, 4 and 5-axis precision CNC machining services for aluminum machining, beryllium, carbon steel, magnesium, titanium machining, Inconel, platinum, superalloy, acetal, polycarbonate, fiberglass, graphite and wood. Capable of machining parts up to 98 in. turning dia. and +/-0.001 in. straightness tolerance. Processes include milling, turning, drilling, boring, threading, tapping, forming, knurling, counterboring, countersinking, reaming and laser cutting. Secondary services such as assembly, centerless grinding, heat treating, plating and welding. Prototype and low to high volume production offered with maximum 50,000 units. Suitable for fluid power, pneumatics, hydraulics and valve applications. Serves the aerospace, aircraft, military, medical and defense industries.PTJ will strategize with you to provide the most cost-effective services to help you reach your target,Welcome to Contact us ( sales@pintejin.com ) directly for your new project.
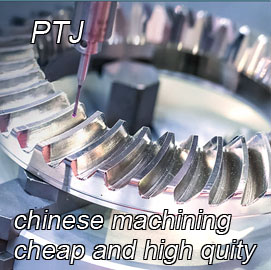
- 5 Axis Machining
- Cnc Milling
- Cnc Turning
- Machining Industries
- Machining Process
- Surface Treatment
- Metal Machining
- Plastic Machining
- Powder Metallurgy Mold
- Die Casting
- Parts Gallery
- Auto Metal Parts
- Machinery Parts
- LED Heatsink
- Building Parts
- Mobile Parts
- Medical Parts
- Electronic Parts
- Tailored Machining
- Bicycle Parts
- Aluminum Machining
- Titanium Machining
- Stainless Steel Machining
- Copper Machining
- Brass Machining
- Super Alloy Machining
- Peek Machining
- UHMW Machining
- Unilate Machining
- PA6 Machining
- PPS Machining
- Teflon Machining
- Inconel Machining
- Tool Steel Machining
- More Material