Design and Improvement of the Die Casting Mold for the PQ35 Engine Bracket
Material Selection for Die Casting
Material selection is critical to ensure the engine bracket’s performance and manufacturability. Aluminum alloys, particularly Al-Si-Mg (e.g., A356), are commonly used due to their lightweight properties, excellent castability, and mechanical strength.
Key Properties of Al-Si-Mg Alloy:
Property | Value | Unit |
---|---|---|
Density | 2.67 | g/cm³ |
Ultimate Tensile Strength | 250–310 | MPa |
Yield Strength | 130–180 | MPa |
Elongation at Break | 5–12 | % |
Thermal Conductivity | 151–165 | W/m·K |
The combination of these properties makes Al-Si-Mg alloys ideal for engine brackets, offering a balance between strength and thermal performance.
Initial Mold Design
The die casting mold design process begins with defining geometric and functional requirements for the PQ35 engine bracket. Initial designs typically rely on Computer-Aided Design (CAD) software, such as CATIA or SolidWorks, to visualize and simulate the mold structure.
Design Elements:
-
Cavity and Core: The mold’s cavity and core are shaped to reflect the engine bracket's precise geometry. Multi-cavity molds may be considered to enhance production efficiency.
-
Gate System: Optimal placement and sizing of gates ensure uniform metal flow, reducing air entrapment and defects.
-
Ejection System: A robust ejection mechanism facilitates the safe removal of cast parts without causing deformation.
-
Cooling Channels: Incorporating cooling channels ensures uniform cooling rates, minimizing thermal stresses and warping.
-
Venting System: Proper venting minimizes gas porosity by allowing trapped air and gases to escape during casting.
Challenges in Die Casting for PQ35 Engine Bracket
Despite advancements in die casting technology, several challenges persist in manufacturing the PQ35 engine bracket:
-
Thermal Fatigue: Repeated heating and cooling cycles lead to thermal fatigue in the mold material, reducing mold life.
-
Dimensional Precision: Achieving tight tolerances is critical for engine bracket functionality but is often challenging due to shrinkage and warping.
-
Porosity: Gas entrapment during the casting process can lead to porosity, compromising the mechanical integrity of the bracket.
-
Wear and Tear: The abrasive nature of molten aluminum alloys can cause rapid wear on mold surfaces, necessitating frequent maintenance.
Improvements in Mold Design
Addressing these challenges requires a multi-faceted approach involving material optimization, advanced simulation techniques, and innovative design modifications.
1. Enhanced Mold Materials:
High-performance tool steels, such as H13 or H21, are commonly used for die casting molds due to their excellent thermal and mechanical properties. Coatings like PVD (Physical Vapor Deposition) or CVD (Chemical Vapor Deposition) can further enhance mold life by reducing wear and thermal fatigue.
Comparative Table of Mold Materials:
Material | Hardness (HRC) | Thermal Conductivity (W/m·K) | Thermal Fatigue Resistance |
H13 Tool Steel | 45–50 | 28 | High |
H21 Tool Steel | 40–45 | 26 | Medium |
PVD-Coated H13 | 48–53 | 25 | Very High |
2. Optimized Gate and Runner Design:
Simulation software, such as MAGMASOFT or ProCAST, can optimize gate and runner designs to ensure uniform metal flow and reduce defects. Implementing a fan-shaped gate system has shown significant improvements in filling patterns and reduced air entrapment.
3. Advanced Cooling Systems:
Conformal cooling channels, created using additive manufacturing, provide uniform cooling and minimize thermal stresses. These channels closely follow the mold geometry, offering better heat dissipation compared to conventional straight-line channels.
4. Vacuum-Assisted Casting:
Incorporating vacuum systems during casting can significantly reduce gas porosity. By evacuating air from the mold cavity, the likelihood of defects is minimized, leading to superior part quality.
Performance Evaluation
Improvements in mold design are evaluated through extensive testing and analysis, focusing on key performance indicators such as:
-
Dimensional Accuracy: Measurements using Coordinate Measuring Machines (CMM) ensure the bracket meets geometric tolerances.
-
Mechanical Properties: Tensile and fatigue tests confirm the part’s structural integrity.
-
Porosity Analysis: X-ray inspection and density measurements assess internal defects.
Performance Comparison:
Parameter | Initial Mold | Improved Mold |
Dimensional Tolerance (±mm) | 0.5 | 0.3 |
Porosity (%) | 2.5 | 0.8 |
Mold Life (Cycles) | 80,000 | 120,000 |
Cooling Time (s) | 25 | 18 |
Sustainability Considerations
Die casting molds for the PQ35 engine bracket must align with sustainable manufacturing practices. Strategies include:
-
Material Recycling: Using recycled aluminum alloys reduces environmental impact while maintaining material properties.
-
Energy Efficiency: Optimized cooling systems and process automation lower energy consumption.
-
Waste Minimization: Improved gating systems minimize scrap generation, enhancing material utilization.
Reprint Statement: If there are no special instructions, all articles on this site are original. Please indicate the source for reprinting:https://www.cncmachiningptj.com/,thanks!
3, 4 and 5-axis precision CNC machining services for aluminum machining, beryllium, carbon steel, magnesium, titanium machining, Inconel, platinum, superalloy, acetal, polycarbonate, fiberglass, graphite and wood. Capable of machining parts up to 98 in. turning dia. and +/-0.001 in. straightness tolerance. Processes include milling, turning, drilling, boring, threading, tapping, forming, knurling, counterboring, countersinking, reaming and laser cutting. Secondary services such as assembly, centerless grinding, heat treating, plating and welding. Prototype and low to high volume production offered with maximum 50,000 units. Suitable for fluid power, pneumatics, hydraulics and valve applications. Serves the aerospace, aircraft, military, medical and defense industries.PTJ will strategize with you to provide the most cost-effective services to help you reach your target,Welcome to Contact us ( sales@pintejin.com ) directly for your new project.
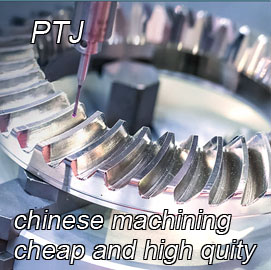
- 5 Axis Machining
- Cnc Milling
- Cnc Turning
- Machining Industries
- Machining Process
- Surface Treatment
- Metal Machining
- Plastic Machining
- Powder Metallurgy Mold
- Die Casting
- Parts Gallery
- Auto Metal Parts
- Machinery Parts
- LED Heatsink
- Building Parts
- Mobile Parts
- Medical Parts
- Electronic Parts
- Tailored Machining
- Bicycle Parts
- Aluminum Machining
- Titanium Machining
- Stainless Steel Machining
- Copper Machining
- Brass Machining
- Super Alloy Machining
- Peek Machining
- UHMW Machining
- Unilate Machining
- PA6 Machining
- PPS Machining
- Teflon Machining
- Inconel Machining
- Tool Steel Machining
- More Material