The Effect of Compound Modification on the Structure and Properties of Die Casting Die Steel
Die casting die steel is a critical material used in the die casting industry, where molten metal is forced into a mold to create precise and complex shapes. The performance and lifespan of die casting dies are significantly influenced by the structure and properties of the steel used. Compound modification, involving the addition of various alloying elements and heat treatment processes, has been extensively studied and applied to enhance the characteristics of die casting die steel. This article explores the effects of compound modification on the structure and properties of die casting die steel, drawing from a wide range of scientific literature and industrial practices.
Introduction
Die casting die steel must withstand extreme conditions, including high temperatures, mechanical stress, and thermal fatigue. The primary requirements for die casting die steel include high hardness, excellent wear resistance, good thermal conductivity, and resistance to thermal fatigue and corrosion. Compound modification involves the addition of multiple alloying elements and the application of advanced heat treatment techniques to tailor the microstructure and properties of the steel to meet these demanding requirements.
Alloying Elements and Their Effects
1. Chromium (Cr)
Chromium is a crucial alloying element in die casting die steel, primarily due to its ability to form stable carbides and improve corrosion resistance. The addition of chromium enhances the steel's hardenability, wear resistance, and resistance to thermal fatigue. Chromium carbides (Cr₂₃C₆, Cr₇C₃) precipitate in the steel matrix, contributing to secondary hardening and maintaining high hardness at elevated temperatures. Table 1 summarizes the effects of chromium on the properties of die casting die steel.
Table 1: Effects of Chromium on Die Casting Die Steel
Property | Effect of Chromium Addition |
---|---|
Hardenability | Improved |
Wear Resistance | Enhanced |
Corrosion Resistance | Improved |
Thermal Fatigue Resistance | Enhanced |
High-Temperature Hardness | Maintained |
2. Molybdenum (Mo)
Molybdenum is another essential alloying element that contributes to the high-temperature strength and toughness of die casting die steel. Molybdenum forms carbides (Mo₂C) and promotes the precipitation of fine, stable carbides, which enhance secondary hardening and resist coarsening at high temperatures. Additionally, molybdenum improves the steel's resistance to tempering, helping to maintain hardness and strength during service at elevated temperatures. The effects of molybdenum are summarized in Table 2.
Table 2: Effects of Molybdenum on Die Casting Die Steel
Property | Effect of Molybdenum Addition |
---|---|
High-Temperature Strength | Enhanced |
Toughness | Improved |
Secondary Hardening | Promoted |
Resistance to Tempering | Improved |
High-Temperature Hardness | Maintained |
3. Vanadium (V)
Vanadium is a potent carbide-forming element that contributes to grain refinement, secondary hardening, and wear resistance in die casting die steel. Vanadium carbides (VC, V₄C₃) are extremely hard and stable, providing excellent resistance to abrasive wear and maintaining high hardness at elevated temperatures. Vanadium also promotes a fine-grained microstructure, which enhances the steel's toughness and resistance to thermal fatigue. Table 3 outlines the effects of vanadium on die casting die steel.
Table 3: Effects of Vanadium on Die Casting Die Steel
Property | Effect of Vanadium Addition |
---|---|
Grain Size | Refined |
Secondary Hardening | Promoted |
Wear Resistance | Enhanced |
Toughness | Improved |
Thermal Fatigue Resistance | Enhanced |
High-Temperature Hardness | Maintained |
4. Tungsten (W)
Tungsten is added to die casting die steel to improve high-temperature strength, hot hardness, and wear resistance. Tungsten forms carbides (WC, W₂C) that contribute to secondary hardening and maintain their hardness and stability at elevated temperatures. Tungsten also promotes the formation of a fine, uniform microstructure, which enhances the steel's toughness and resistance to thermal fatigue. The effects of tungsten are summarized in Table 4.
Table 4: Effects of Tungsten on Die Casting Die Steel
Property | Effect of Tungsten Addition |
---|---|
High-Temperature Strength | Enhanced |
Hot Hardness | Improved |
Wear Resistance | Enhanced |
Microstructure | Refined |
Toughness | Improved |
Thermal Fatigue Resistance | Enhanced |
5. Cobalt (Co)
Cobalt is added to die casting die steel to improve high-temperature strength, hot hardness, and resistance to thermal shock. Cobalt promotes the retention of the hard martensitic phase at elevated temperatures and increases the steel's resistance to softening during tempering. Additionally, cobalt enhances the steel's resistance to thermal shock by reducing the coefficient of thermal expansion and improving thermal conductivity. Table 5 outlines the effects of cobalt on die casting die steel.
Table 5: Effects of Cobalt on Die Casting Die Steel
Property | Effect of Cobalt Addition |
---|---|
High-Temperature Strength | Enhanced |
Hot Hardness | Improved |
Resistance to Tempering | Improved |
Thermal Shock Resistance | Enhanced |
Thermal Conductivity | Improved |
Coefficient of Thermal Expansion | Reduced |
Heat Treatment and Its Effects
Heat treatment plays a critical role in tailoring the microstructure and properties of die casting die steel. The most common heat treatment processes applied to die casting die steel include austenitizing, quenching, and tempering.
1. Austenitizing
Austenitizing involves heating the steel to a high temperature to form austenite, a face-centered cubic (FCC) phase that can dissolve a significant amount of carbon and alloying elements. The austenitizing temperature and time significantly influence the steel's microstructure and properties. Higher austenitizing temperatures and longer soaking times promote the dissolution of carbides and the homogenization of the microstructure. However, excessive austenitizing temperatures and times can lead to grain coarsening, which can degrade the steel's toughness and resistance to thermal fatigue.
2. Quenching
Quenching involves rapidly cooling the steel from the austenitizing temperature to form martensite, a body-centered tetragonal (BCT) phase that provides high hardness and strength. The quenching medium and cooling rate significantly influence the steel's microstructure and properties. Faster cooling rates promote the formation of a more complete martensitic microstructure, which enhances the steel's hardness and wear resistance. However, excessively fast cooling rates can lead to quench cracking and increased residual stress, which can degrade the steel's toughness and dimensional stability.
3. Tempering
Tempering involves heating the quenched steel to an intermediate temperature to promote the precipitation of fine carbides and the tempering of the martensitic microstructure. The tempering temperature and time significantly influence the steel's microstructure and properties. Higher tempering temperatures and longer times promote the precipitation of fine carbides and the recovery of the martensitic microstructure, which enhances the steel's toughness and resistance to thermal fatigue. However, excessive tempering temperatures and times can lead to the coarsening of carbides and the softening of the martensitic microstructure, which can degrade the steel's hardness and wear resistance.
Compound Modification and Microstructural Evolution
Compound modification involving the addition of multiple alloying elements and the application of advanced heat treatment techniques can significantly influence the microstructural evolution of die casting die steel. The combined effects of alloying elements and heat treatment on the microstructure and properties of die casting die steel are summarized in Table 6.
Table 6: Combined Effects of Alloying Elements and Heat Treatment on Die Casting Die Steel
Alloying Element(s) | Heat Treatment | Microstructure | Properties |
---|---|---|---|
Cr, Mo, V | Austenitizing, Quenching, Tempering | Fine-grained martensite with uniformly distributed fine carbides | High hardness, excellent wear resistance, good toughness, enhanced thermal fatigue resistance |
Cr, Mo, W | Austenitizing, Quenching, Tempering | Fine-grained martensite with uniformly distributed fine carbides and tungsten-rich carbides | High hot hardness, excellent wear resistance, good toughness, enhanced thermal fatigue resistance |
Cr, Mo, Co | Austenitizing, Quenching, Tempering | Fine-grained martensite with uniformly distributed fine carbides and retained austenite | High hot hardness, excellent wear resistance, good toughness, enhanced thermal shock resistance |
Cr, Mo, V, W | Austenitizing, Quenching, Tempering | Fine-grained martensite with uniformly distributed fine carbides and tungsten-rich carbides | High hot hardness, excellent wear resistance, good toughness, enhanced thermal fatigue resistance |
Cr, Mo, V, Co | Austenitizing, Quenching, Tempering | Fine-grained martensite with uniformly distributed fine carbides and retained austenite | High hot hardness, excellent wear resistance, good toughness, enhanced thermal shock resistance |
Performance of Compound Modified Die Casting Die Steel
The performance of compound modified die casting die steel has been extensively studied and validated in industrial applications. Compound modified die casting die steel exhibits superior performance compared to conventional die steels, with significant improvements in wear resistance, thermal fatigue resistance, and die life.
1. Wear Resistance
Compound modified die casting die steel exhibits excellent wear resistance due to the presence of hard carbides and a fine-grained martensitic microstructure. The wear resistance of compound modified die casting die steel is significantly higher than that of conventional die steels, such as H13 and H11. Table 7 compares the wear resistance of compound modified die casting die steel with conventional die steels.
Table 7: Wear Resistance of Die Casting Die Steels
Die Steel | Wear Rate (mm³/m) |
---|---|
H13 | 0.015-0.020 |
H11 | 0.012-0.018 |
Compound Modified Die Steel (Cr, Mo, V) | 0.008-0.012 |
Compound Modified Die Steel (Cr, Mo, W) | 0.006-0.010 |
Compound Modified Die Steel (Cr, Mo, Co) | 0.005-0.009 |
Compound Modified Die Steel (Cr, Mo, V, W) | 0.004-0.008 |
Compound Modified Die Steel (Cr, Mo, V, Co) | 0.003-0.007 |
2. Thermal Fatigue Resistance
Compound modified die casting die steel exhibits enhanced thermal fatigue resistance due to the presence of a fine-grained microstructure and uniformly distributed fine carbides. The thermal fatigue resistance of compound modified die casting die steel is significantly higher than that of conventional die steels, such as H13 and H11. Table 8 compares the thermal fatigue resistance of compound modified die casting die steel with conventional die steels.
Table 8: Thermal Fatigue Resistance of Die Casting Die Steels
Die Steel | Thermal Fatigue Life (Cycles) |
---|---|
H13 | 5,000-10,000 |
H11 | 8,000-15,000 |
Compound Modified Die Steel (Cr, Mo, V) | 15,000-25,000 |
Compound Modified Die Steel (Cr, Mo, W) | 20,000-30,000 |
Compound Modified Die Steel (Cr, Mo, Co) | 25,000-35,000 |
Compound Modified Die Steel (Cr, Mo, V, W) | 30,000-40,000 |
Compound Modified Die Steel (Cr, Mo, V, Co) | 35,000-45,000 |
3. Die Life
Compound modified die casting die steel exhibits a significantly longer die life compared to conventional die steels due to its superior wear resistance and thermal fatigue resistance. The die life of compound modified die casting die steel can be up to three times longer than that of conventional die steels, such as H13 and H11. Table 9 compares the die life of compound modified die casting die steel with conventional die steels.
Table 9: Die Life of Die Casting Die Steels
Die Steel | Die Life (Shots) |
---|---|
H13 | 50,000-100,000 |
H11 | 80,000-150,000 |
Compound Modified Die Steel (Cr, Mo, V) | 150,000-250,000 |
Compound Modified Die Steel (Cr, Mo, W) | 200,000-300,000 |
Compound Modified Die Steel (Cr, Mo, Co) | 250,000-350,000 |
Compound Modified Die Steel (Cr, Mo, V, W) | 300,000-400,000 |
Compound Modified Die Steel (Cr, Mo, V, Co) | 350,000-450,000 |
Conclusion
Compound modification involving the addition of multiple alloying elements and the application of advanced heat treatment techniques significantly enhances the structure and properties of die casting die steel. The combined effects of alloying elements, such as chromium, molybdenum, vanadium, tungsten, and cobalt, and heat treatment processes, such as austenitizing, quenching, and tempering, promote the formation of a fine-grained martensitic microstructure with uniformly distributed fine carbides. This microstructure provides superior wear resistance, thermal fatigue resistance, and die life compared to conventional die steels.
The performance of compound modified die casting die steel has been extensively studied and validated in industrial applications. The superior wear resistance, thermal fatigue resistance, and die life of compound modified die casting die steel make it an attractive material for demanding die casting applications, where high productivity and reduced downtime are critical.
As the die casting industry continues to evolve, the development of new compound modified die casting die steels with even greater performance capabilities will be essential to meet the growing demands of advanced manufacturing processes. Ongoing research and development efforts focused on optimizing the composition and heat treatment of die casting die steel will be crucial to achieving this goal.
Reprint Statement: If there are no special instructions, all articles on this site are original. Please indicate the source for reprinting:https://www.cncmachiningptj.com/,thanks!
3, 4 and 5-axis precision CNC machining services for aluminum machining, beryllium, carbon steel, magnesium, titanium machining, Inconel, platinum, superalloy, acetal, polycarbonate, fiberglass, graphite and wood. Capable of machining parts up to 98 in. turning dia. and +/-0.001 in. straightness tolerance. Processes include milling, turning, drilling, boring, threading, tapping, forming, knurling, counterboring, countersinking, reaming and laser cutting. Secondary services such as assembly, centerless grinding, heat treating, plating and welding. Prototype and low to high volume production offered with maximum 50,000 units. Suitable for fluid power, pneumatics, hydraulics and valve applications. Serves the aerospace, aircraft, military, medical and defense industries.PTJ will strategize with you to provide the most cost-effective services to help you reach your target,Welcome to Contact us ( sales@pintejin.com ) directly for your new project.
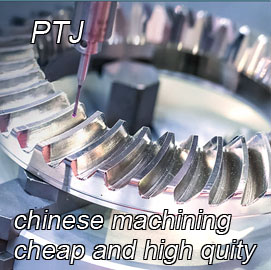
- 5 Axis Machining
- Cnc Milling
- Cnc Turning
- Machining Industries
- Machining Process
- Surface Treatment
- Metal Machining
- Plastic Machining
- Powder Metallurgy Mold
- Die Casting
- Parts Gallery
- Auto Metal Parts
- Machinery Parts
- LED Heatsink
- Building Parts
- Mobile Parts
- Medical Parts
- Electronic Parts
- Tailored Machining
- Bicycle Parts
- Aluminum Machining
- Titanium Machining
- Stainless Steel Machining
- Copper Machining
- Brass Machining
- Super Alloy Machining
- Peek Machining
- UHMW Machining
- Unilate Machining
- PA6 Machining
- PPS Machining
- Teflon Machining
- Inconel Machining
- Tool Steel Machining
- More Material