The Effect of Silicon on the Interaction Between Die Casting Molds and Aluminum Alloys
Die casting is a manufacturing process that involves forcing molten metal under high pressure into a mold cavity. This process is widely used for producing complex shapes with high dimensional accuracy and smooth surface finishes. Aluminum alloys are commonly used in die casting due to their excellent castability, low density, and good mechanical properties. One of the critical elements in aluminum alloys is silicon, which plays a significant role in the interaction between the molten metal and the die casting mold. This article explores the effect of silicon on this interaction, focusing on various scientific aspects and providing detailed comparisons through tables.
Introduction to Die Casting and Aluminum Alloys
Die casting is a versatile process that can produce parts with intricate shapes and thin walls. The process involves injecting molten metal into a steel mold under high pressure, which allows for rapid solidification and precise control over the final product's dimensions. Aluminum alloys are particularly suitable for die casting due to their low melting point, good fluidity, and excellent mechanical properties.
Aluminum alloys used in die casting typically contain silicon as a primary alloying element. Silicon improves the fluidity of the molten metal, reduces shrinkage during solidification, and enhances the mechanical properties of the cast part. The most common aluminum-silicon alloys used in die casting include A356, A380, and A413, each with varying silicon content.
The Role of Silicon in Aluminum Alloys
Silicon is a crucial element in aluminum alloys for several reasons:
-
Improved Fluidity: Silicon reduces the viscosity of the molten aluminum, making it easier to fill the mold cavity completely and uniformly. This is particularly important for casting complex shapes with thin sections.
-
Reduced Shrinkage: Silicon forms a eutectic mixture with aluminum, which solidifies at a lower temperature than pure aluminum. This eutectic mixture helps to reduce shrinkage during solidification, minimizing the risk of porosity and improving the dimensional stability of the cast part.
-
Enhanced Mechanical Properties: Silicon precipitates in the aluminum matrix, forming hard particles that strengthen the alloy. This precipitation hardening mechanism improves the tensile strength, yield strength, and hardness of the cast part.
-
Corrosion Resistance: Silicon can form a protective oxide layer on the surface of the aluminum alloy, enhancing its corrosion resistance.
Interaction Between Die Casting Molds and Aluminum Alloys
The interaction between the die casting mold and the molten aluminum alloy is complex and involves several physical and chemical processes. The mold, typically made of tool steel, must withstand high temperatures, pressures, and the corrosive effects of the molten metal. Silicon in the aluminum alloy influences this interaction in several ways:
-
Wetting and Adhesion: Silicon affects the wetting behavior of the molten aluminum on the mold surface. Good wetting is essential for complete filling of the mold cavity and for achieving a smooth surface finish. However, excessive wetting can lead to adhesion of the molten metal to the mold, making it difficult to eject the cast part.
-
Thermal Conductivity: Silicon increases the thermal conductivity of the aluminum alloy, which affects the heat transfer between the molten metal and the mold. Efficient heat transfer is crucial for rapid solidification and for maintaining the dimensional accuracy of the cast part.
-
Chemical Reactions: Silicon can react with the mold material, forming intermetallic compounds that can adhere to the mold surface. These compounds can affect the surface quality of the cast part and reduce the lifespan of the mold.
-
Residual Stresses: The differential thermal expansion and contraction of the mold and the cast part can lead to residual stresses. Silicon influences the thermal expansion coefficient of the aluminum alloy, affecting the magnitude of these stresses.
Detailed Comparison of Aluminum-Silicon Alloys
To understand the effect of silicon on the interaction between die casting molds and aluminum alloys, it is essential to compare different aluminum-silicon alloys. The following table provides a detailed comparison of the most common die casting aluminum alloys:
Property | A356 | A380 | A413 |
---|---|---|---|
Silicon Content (wt%) | 7.0 | 8.5 | 12.0 |
Melting Range (°C) | 555-615 | 540-600 | 520-580 |
Density (g/cm³) | 2.68 | 2.71 | 2.64 |
Thermal Conductivity (W/mK) | 150 | 120 | 90 |
Tensile Strength (MPa) | 220 | 320 | 280 |
Yield Strength (MPa) | 140 | 160 | 120 |
Elongation (%) | 7 | 3 | 2 |
Hardness (HB) | 60 | 85 | 70 |
Corrosion Resistance | Good | Fair | Poor |
Castability | Excellent | Excellent | Excellent |
Machinability | Good | Good | Fair |
A356 Alloy
A356 is an aluminum-silicon alloy with a silicon content of approximately 7.0 wt%. It is widely used in die casting due to its excellent castability and good mechanical properties. The alloy has a melting range of 555-615°C and a density of 2.68 g/cm³. Its thermal conductivity is relatively high at 150 W/mK, which promotes efficient heat transfer during solidification.
A356 exhibits good tensile strength (220 MPa) and yield strength (140 MPa), making it suitable for applications requiring high strength and ductility. The alloy also has good corrosion resistance and machinability, making it a versatile choice for various die casting applications.
A380 Alloy
A380 is another popular aluminum-silicon alloy used in die casting, with a silicon content of about 8.5 wt%. It has a melting range of 540-600°C and a density of 2.71 g/cm³. The thermal conductivity of A380 is slightly lower than that of A356, at 120 W/mK, but it still provides efficient heat transfer during solidification.
A380 offers higher tensile strength (320 MPa) and yield strength (160 MPa) compared to A356, making it suitable for applications requiring superior mechanical properties. However, its corrosion resistance and machinability are fair, which may limit its use in certain applications.
A413 Alloy
A413 is an aluminum-silicon alloy with a high silicon content of approximately 12.0 wt%. It has a melting range of 520-580°C and a density of 2.64 g/cm³. The thermal conductivity of A413 is the lowest among the three alloys, at 90 W/mK, which can affect the heat transfer during solidification.
A413 exhibits good tensile strength (280 MPa) and yield strength (120 MPa), but its elongation is relatively low at 2%. The alloy has poor corrosion resistance and fair machinability, which may limit its use in applications requiring high corrosion resistance and precise machining.
Scientific Studies on the Effect of Silicon
Several scientific studies have investigated the effect of silicon on the interaction between die casting molds and aluminum alloys. These studies have focused on various aspects, including wetting behavior, thermal conductivity, chemical reactions, and residual stresses.
Wetting Behavior
Wetting behavior is a critical factor in die casting, as it affects the filling of the mold cavity and the surface quality of the cast part. Silicon influences the wetting behavior of molten aluminum on the mold surface. Studies have shown that increasing silicon content improves the wetting behavior, leading to better filling of the mold cavity and a smoother surface finish. However, excessive silicon content can result in adhesion of the molten metal to the mold, making it difficult to eject the cast part.
Thermal Conductivity
Thermal conductivity plays a crucial role in the heat transfer between the molten aluminum and the mold. Efficient heat transfer is essential for rapid solidification and for maintaining the dimensional accuracy of the cast part. Silicon increases the thermal conductivity of aluminum alloys, which enhances heat transfer during solidification. However, the thermal conductivity of the alloy decreases with increasing silicon content, which can affect the solidification rate and the final properties of the cast part.
Chemical Reactions
Silicon can react with the mold material, forming intermetallic compounds that can adhere to the mold surface. These compounds can affect the surface quality of the cast part and reduce the lifespan of the mold. Studies have shown that increasing silicon content promotes the formation of intermetallic compounds, which can lead to increased adhesion and reduced mold life.
Residual Stresses
Residual stresses arise from the differential thermal expansion and contraction of the mold and the cast part. Silicon influences the thermal expansion coefficient of the aluminum alloy, affecting the magnitude of these stresses. Studies have shown that increasing silicon content reduces the thermal expansion coefficient, which can help to minimize residual stresses and improve the dimensional stability of the cast part.
Conclusion
The effect of silicon on the interaction between die casting molds and aluminum alloys is complex and multifaceted. Silicon improves the fluidity, reduces shrinkage, and enhances the mechanical properties of aluminum alloys. However, it also influences the wetting behavior, thermal conductivity, chemical reactions, and residual stresses during the die casting process.
Comparing different aluminum-silicon alloys, such as A356, A380, and A413, reveals the varying effects of silicon content on the properties and performance of the cast parts. A356 offers a good balance of mechanical properties, corrosion resistance, and machinability, making it a versatile choice for various die casting applications. A380 provides superior mechanical properties but has fair corrosion resistance and machinability. A413 has high silicon content, which improves fluidity and reduces shrinkage but may limit its use in applications requiring high corrosion resistance and precise machining.
Understanding the effect of silicon on the interaction between die casting molds and aluminum alloys is crucial for optimizing the die casting process and producing high-quality cast parts. Future research should focus on developing new aluminum-silicon alloys with improved properties and performance, as well as on advancing die casting technologies to enhance the efficiency and sustainability of the process.
Reprint Statement: If there are no special instructions, all articles on this site are original. Please indicate the source for reprinting:https://www.cncmachiningptj.com/,thanks!
3, 4 and 5-axis precision CNC machining services for aluminum machining, beryllium, carbon steel, magnesium, titanium machining, Inconel, platinum, superalloy, acetal, polycarbonate, fiberglass, graphite and wood. Capable of machining parts up to 98 in. turning dia. and +/-0.001 in. straightness tolerance. Processes include milling, turning, drilling, boring, threading, tapping, forming, knurling, counterboring, countersinking, reaming and laser cutting. Secondary services such as assembly, centerless grinding, heat treating, plating and welding. Prototype and low to high volume production offered with maximum 50,000 units. Suitable for fluid power, pneumatics, hydraulics and valve applications. Serves the aerospace, aircraft, military, medical and defense industries.PTJ will strategize with you to provide the most cost-effective services to help you reach your target,Welcome to Contact us ( sales@pintejin.com ) directly for your new project.
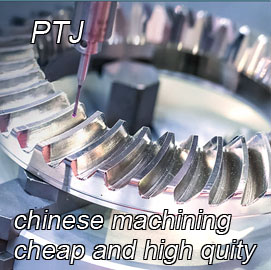
- 5 Axis Machining
- Cnc Milling
- Cnc Turning
- Machining Industries
- Machining Process
- Surface Treatment
- Metal Machining
- Plastic Machining
- Powder Metallurgy Mold
- Die Casting
- Parts Gallery
- Auto Metal Parts
- Machinery Parts
- LED Heatsink
- Building Parts
- Mobile Parts
- Medical Parts
- Electronic Parts
- Tailored Machining
- Bicycle Parts
- Aluminum Machining
- Titanium Machining
- Stainless Steel Machining
- Copper Machining
- Brass Machining
- Super Alloy Machining
- Peek Machining
- UHMW Machining
- Unilate Machining
- PA6 Machining
- PPS Machining
- Teflon Machining
- Inconel Machining
- Tool Steel Machining
- More Material