Die Casting Mold Cavity Cracking: Causes, Mechanisms, and Mitigation Strategies
Die casting is a manufacturing process that involves injecting molten metal into a mold cavity under high pressure. This process is widely used for producing complex metal parts with high dimensional accuracy and excellent surface finish. However, one of the critical challenges in die casting is the failure of the mold cavity due to cracking. This article delves into the causes, mechanisms, and mitigation strategies for die casting mold cavity cracking, providing a comprehensive understanding of this phenomenon.
Introduction to Die Casting
Die casting is a versatile process that can produce parts with intricate shapes and fine details. The process involves several key steps:
- Mold Preparation: The mold is prepared by cleaning and applying a release agent to facilitate the removal of the cast part.
- Melting: The metal is melted in a furnace and maintained at a specific temperature.
- Injection: The molten metal is injected into the mold cavity under high pressure.
- Cooling: The metal solidifies in the mold cavity.
- Ejection: The solidified part is ejected from the mold.
The mold, typically made of tool steel, is subjected to repeated thermal and mechanical stresses during the die casting process. These stresses can lead to the formation of cracks in the mold cavity, which can significantly impact the quality and dimensional accuracy of the cast parts.
Causes of Die Casting Mold Cavity Cracking
Several factors contribute to the cracking of die casting mold cavities. These factors can be broadly categorized into thermal, mechanical, and material-related causes.
Thermal Stresses
Thermal stresses arise from the rapid heating and cooling cycles experienced by the mold during the die casting process. The molten metal, injected at high temperatures, causes the mold to heat up rapidly. Subsequently, the mold cools down as the metal solidifies. This cyclic thermal loading can induce thermal fatigue, leading to the formation of cracks.
Mechanical Stresses
Mechanical stresses are generated by the high pressure used to inject the molten metal into the mold cavity. The pressure can cause localized deformation and stress concentration in the mold, particularly at sharp corners and edges. Repeated mechanical loading can result in fatigue cracking.
Material-Related Factors
The material properties of the mold, such as its thermal conductivity, strength, and toughness, play a crucial role in determining its resistance to cracking. Tool steels with higher thermal conductivity can dissipate heat more effectively, reducing thermal stresses. Similarly, materials with higher strength and toughness can better withstand mechanical stresses.
Mechanisms of Die Casting Mold Cavity Cracking
The mechanisms of die casting mold cavity cracking can be understood through the principles of fracture mechanics and fatigue. The following sections discuss the key mechanisms involved.
Thermal Fatigue
Thermal fatigue is a phenomenon where repeated thermal cycling causes the initiation and propagation of cracks. The thermal expansion and contraction of the mold material during heating and cooling cycles generate thermal stresses. These stresses can exceed the material's yield strength, leading to plastic deformation and the formation of microcracks. Over time, these microcracks coalesce and propagate, resulting in macroscopic cracks.
Mechanical Fatigue
Mechanical fatigue occurs due to the repeated application of mechanical stresses. The high pressure used in die casting can cause localized plastic deformation and stress concentration, particularly at sharp corners and edges. Repeated mechanical loading can initiate and propagate cracks, leading to fatigue failure.
Corrosion Fatigue
Corrosion fatigue is a combination of fatigue and corrosion, where the presence of a corrosive environment accelerates the initiation and propagation of cracks. In die casting, the molten metal and release agents can act as corrosive media, exacerbating the fatigue process.
Mitigation Strategies for Die Casting Mold Cavity Cracking
Several strategies can be employed to mitigate die casting mold cavity cracking. These strategies focus on reducing thermal and mechanical stresses, improving material properties, and optimizing the die casting process.
Thermal Management
Effective thermal management can reduce thermal stresses and prolong the life of the mold. Techniques such as mold cooling, preheating, and the use of thermal barrier coatings can help dissipate heat more effectively and reduce thermal gradients.
Mechanical Design Optimization
Optimizing the mechanical design of the mold can reduce stress concentration and improve fatigue resistance. This includes designing smooth transitions and avoiding sharp corners, using finite element analysis (FEA) to identify and mitigate stress concentration areas, and employing advanced manufacturing techniques to produce high-quality molds.
Material Selection
Selecting appropriate materials for the mold can enhance its resistance to cracking. Tool steels with high thermal conductivity, strength, and toughness are preferred. Additionally, the use of advanced materials such as high-speed steels and hot work tool steels can provide better performance.
Process Optimization
Optimizing the die casting process can reduce the likelihood of mold cavity cracking. This includes controlling the injection pressure, temperature, and speed to minimize thermal and mechanical stresses. Additionally, the use of release agents and lubricants can reduce friction and wear, prolonging the life of the mold.
Comparative Analysis of Mitigation Strategies
The following table provides a comparative analysis of various mitigation strategies for die casting mold cavity cracking:
Mitigation Strategy | Description | Advantages | Disadvantages |
---|---|---|---|
Thermal Management | Techniques such as mold cooling, preheating, and thermal barrier coatings. | Reduces thermal stresses and prolongs mold life. | Requires additional equipment and may increase cycle time. |
Mechanical Design Optimization | Designing smooth transitions and avoiding sharp corners. | Reduces stress concentration and improves fatigue resistance. | May require advanced manufacturing techniques and increase mold cost. |
Material Selection | Using tool steels with high thermal conductivity, strength, and toughness. | Enhances resistance to cracking and improves mold performance. | May increase material cost and require specialized heat treatment. |
Process Optimization | Controlling injection pressure, temperature, and speed. | Reduces thermal and mechanical stresses and improves part quality. | Requires precise control and may increase process complexity. |
Use of Release Agents | Applying release agents and lubricants to reduce friction and wear. | Prolongs mold life and improves part ejection. | May require frequent application and can affect part surface finish. |
Case Studies
Several case studies have been conducted to understand the failure of die casting mold cavities and the effectiveness of mitigation strategies. These studies provide valuable insights into the practical application of the strategies discussed.
Case Study 1: Thermal Management in Aluminum Die Casting
In a study conducted on aluminum die casting, the implementation of mold cooling and preheating techniques significantly reduced thermal stresses. The use of thermal barrier coatings further enhanced heat dissipation, resulting in a 30% increase in mold life.
Case Study 2: Mechanical Design Optimization in Zinc Die Casting
A zinc die casting operation optimized the mechanical design of the mold by eliminating sharp corners and using FEA to identify stress concentration areas. The optimized design reduced stress concentration by 25% and increased mold life by 20%.
Case Study 3: Material Selection in Magnesium Die Casting
In a magnesium die casting operation, the use of high-speed steel for the mold resulted in a 40% increase in mold life compared to conventional tool steel. The high thermal conductivity and strength of the high-speed steel reduced thermal and mechanical stresses, improving mold performance.
Case Study 4: Process Optimization in Copper Die Casting
A copper die casting operation optimized the injection pressure, temperature, and speed to minimize thermal and mechanical stresses. The optimized process parameters resulted in a 25% reduction in mold cavity cracking and improved part quality.
Case Study 5: Use of Release Agents in Lead Die Casting
In a lead die casting operation, the application of release agents and lubricants reduced friction and wear, prolonging mold life by 15%. The frequent application of release agents ensured smooth part ejection and improved surface finish.
Conclusion
Die casting mold cavity cracking is a critical challenge that can significantly impact the quality and dimensional accuracy of cast parts. Understanding the causes, mechanisms, and mitigation strategies for mold cavity cracking is essential for improving mold performance and extending mold life. Thermal management, mechanical design optimization, material selection, process optimization, and the use of release agents are effective strategies for mitigating mold cavity cracking.
Future research should focus on developing advanced materials and manufacturing techniques to further enhance mold performance. Additionally, the integration of sensors and real-time monitoring systems can provide valuable data for optimizing the die casting process and reducing mold cavity cracking.
Reprint Statement: If there are no special instructions, all articles on this site are original. Please indicate the source for reprinting:https://www.cncmachiningptj.com/,thanks!
3, 4 and 5-axis precision CNC machining services for aluminum machining, beryllium, carbon steel, magnesium, titanium machining, Inconel, platinum, superalloy, acetal, polycarbonate, fiberglass, graphite and wood. Capable of machining parts up to 98 in. turning dia. and +/-0.001 in. straightness tolerance. Processes include milling, turning, drilling, boring, threading, tapping, forming, knurling, counterboring, countersinking, reaming and laser cutting. Secondary services such as assembly, centerless grinding, heat treating, plating and welding. Prototype and low to high volume production offered with maximum 50,000 units. Suitable for fluid power, pneumatics, hydraulics and valve applications. Serves the aerospace, aircraft, military, medical and defense industries.PTJ will strategize with you to provide the most cost-effective services to help you reach your target,Welcome to Contact us ( sales@pintejin.com ) directly for your new project.
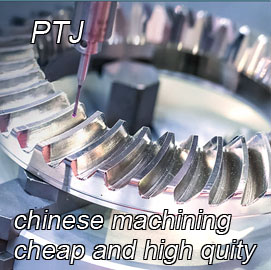
- 5 Axis Machining
- Cnc Milling
- Cnc Turning
- Machining Industries
- Machining Process
- Surface Treatment
- Metal Machining
- Plastic Machining
- Powder Metallurgy Mold
- Die Casting
- Parts Gallery
- Auto Metal Parts
- Machinery Parts
- LED Heatsink
- Building Parts
- Mobile Parts
- Medical Parts
- Electronic Parts
- Tailored Machining
- Bicycle Parts
- Aluminum Machining
- Titanium Machining
- Stainless Steel Machining
- Copper Machining
- Brass Machining
- Super Alloy Machining
- Peek Machining
- UHMW Machining
- Unilate Machining
- PA6 Machining
- PPS Machining
- Teflon Machining
- Inconel Machining
- Tool Steel Machining
- More Material