Die Casting Mold Design for Radiator Parts
Die casting is a manufacturing process that involves forcing molten metal under high pressure into a mold cavity. This process is particularly suitable for creating complex shapes with high dimensional accuracy and smooth surfaces, making it ideal for the production of radiator parts. The design of die casting molds for radiator parts is a critical aspect that significantly influences the quality, efficiency, and cost-effectiveness of the manufacturing process. This article delves into the intricate details of die casting mold design for radiator parts, covering various aspects such as mold materials, design considerations, cooling systems, and more.
Introduction to Die Casting
Die casting is a versatile process that can produce parts with thin walls, complex shapes, and fine details. The process involves injecting molten metal into a mold under high pressure, which is then cooled and solidified to form the desired part. The most common metals used in die casting include aluminum, zinc, and magnesium, each offering unique properties suitable for different applications.
Radiator Parts and Die Casting
Radiators are essential components in various industries, including automotive, aerospace, and HVAC systems. They are designed to transfer heat from one medium to another, typically from a liquid to air. Die casting is particularly advantageous for manufacturing radiator parts due to its ability to produce intricate shapes with high precision and repeatability. Common radiator parts produced through die casting include heat sinks, fins, and brackets.
Mold Materials
The selection of mold materials is crucial in die casting as it directly affects the durability, thermal conductivity, and overall performance of the mold. Common materials used for die casting molds include:
-
Tool Steel: Known for its high strength, wear resistance, and ability to withstand high temperatures, tool steel is a popular choice for die casting molds. It ensures longevity and consistent performance over numerous casting cycles.
-
Stainless Steel: Offers excellent corrosion resistance and is suitable for applications where the mold is exposed to corrosive environments. However, it may not be as durable as tool steel under high-pressure conditions.
-
Beryllium Copper: Provides exceptional thermal conductivity, making it ideal for molds that require rapid heat dissipation. It is often used in combination with other materials to enhance cooling efficiency.
Table 1: Comparison of Mold Materials
Material | Strength | Wear Resistance | Thermal Conductivity | Corrosion Resistance | Cost |
---|---|---|---|---|---|
Tool Steel | High | High | Moderate | Moderate | Moderate |
Stainless Steel | Moderate | Moderate | Low | High | High |
Beryllium Copper | Moderate | Moderate | High | Moderate | High |
Design Considerations
The design of a die casting mold for radiator parts involves several critical considerations to ensure optimal performance and part quality. These considerations include:
-
Mold Cavity Design: The cavity design must accurately replicate the shape and dimensions of the radiator part. Precise machining techniques, such as CNC milling and EDM (Electrical Discharge Machining), are employed to achieve the required tolerances.
-
Gating System: The gating system controls the flow of molten metal into the mold cavity. It includes the sprue, runner, and gate, which must be designed to ensure uniform filling and minimize turbulence. Proper gating design helps prevent defects such as porosity and cold shuts.
-
Venting System: Venting is essential to allow air and gases to escape from the mold cavity during the filling process. Inadequate venting can lead to trapped gases, resulting in porosity and surface defects. Venting channels must be strategically placed and sized to ensure efficient gas removal.
-
Ejection System: The ejection system facilitates the removal of the cast part from the mold. It includes ejector pins and sleeves that push the part out of the cavity. The design must ensure that the part is ejected without damage and that the ejection forces are evenly distributed.
-
Cooling System: Effective cooling is crucial for controlling the solidification process and achieving uniform part properties. Cooling channels are integrated into the mold to circulate coolant, typically water or oil. The design of the cooling system must consider the thermal properties of the mold material and the casting alloy.
Cooling System Design
The cooling system plays a pivotal role in die casting, as it influences the solidification rate, part quality, and cycle time. Key aspects of cooling system design include:
-
Cooling Channel Layout: The layout of cooling channels must be optimized to ensure uniform cooling throughout the mold. This involves strategic placement of channels to target hot spots and areas prone to thermal stress.
-
Coolant Flow Rate: The flow rate of the coolant must be carefully controlled to achieve the desired cooling effect. Too high a flow rate can lead to excessive cooling and thermal shock, while too low a flow rate can result in inadequate cooling and prolonged cycle times.
-
Coolant Temperature: The temperature of the coolant must be maintained within a specific range to ensure consistent cooling performance. Temperature control systems, such as chillers and heat exchangers, are employed to regulate coolant temperature.
-
Cooling Channel Geometry: The geometry of cooling channels, including their diameter, length, and spacing, must be designed to optimize coolant flow and heat transfer. Computational fluid dynamics (CFD) simulations are often used to analyze and optimize cooling channel geometry.
Table 2: Cooling System Design Parameters
Parameter | Description |
---|---|
Cooling Channel Layout | Strategic placement of channels to target hot spots and ensure uniform cooling |
Coolant Flow Rate | Controlled flow rate to achieve desired cooling effect |
Coolant Temperature | Maintained within a specific range for consistent cooling performance |
Cooling Channel Geometry | Optimized diameter, length, and spacing for efficient coolant flow and heat transfer |
Mold Maintenance and Longevity
Proper maintenance is essential to extend the lifespan of die casting molds and ensure consistent part quality. Key maintenance practices include:
-
Regular Cleaning: Molds must be regularly cleaned to remove residue, scale, and other contaminants that can affect part quality and mold performance. Cleaning methods include chemical cleaning, ultrasonic cleaning, and manual scrubbing.
-
Inspection and Repair: Periodic inspections are necessary to identify and address wear, damage, and other issues that can compromise mold performance. Repairs may involve welding, machining, or replacing worn components.
-
Lubrication: Proper lubrication of moving parts, such as ejector pins and slides, is crucial to reduce friction and wear. Lubricants must be compatible with the mold material and the casting alloy to prevent contamination.
-
Thermal Management: Effective thermal management helps prevent thermal fatigue and prolongs mold life. This involves monitoring and controlling mold temperature, optimizing cooling system performance, and using thermal barriers to protect sensitive areas.
Table 3: Mold Maintenance Practices
Practice | Description |
---|---|
Regular Cleaning | Removal of residue, scale, and contaminants using chemical, ultrasonic, or manual methods |
Inspection and Repair | Identification and addressing of wear, damage, and other issues through welding, machining, or replacement |
Lubrication | Reduction of friction and wear through proper lubrication of moving parts |
Thermal Management | Prevention of thermal fatigue through temperature monitoring, cooling system optimization, and use of thermal barriers |
Advanced Technologies in Die Casting Mold Design
Advancements in technology have significantly enhanced the capabilities and efficiency of die casting mold design. Some of the key technologies include:
-
Computer-Aided Design (CAD): CAD software enables precise and detailed mold design, allowing for the creation of complex geometries and intricate features. It also facilitates simulation and analysis of mold performance.
-
Finite Element Analysis (FEA): FEA is used to simulate the behavior of the mold under various conditions, such as thermal stress, pressure, and deformation. This helps in identifying potential issues and optimizing mold design.
-
Rapid Prototyping: Techniques such as 3D printing and stereolithography allow for the quick and cost-effective production of mold prototypes. This enables testing and validation of mold designs before full-scale production.
-
Automation and Robotics: Automated systems and robotics are increasingly used in die casting to enhance precision, consistency, and efficiency. Automated mold handling, part ejection, and quality inspection systems improve overall productivity and reduce human error.
Table 4: Advanced Technologies in Die Casting Mold Design
Technology | Description |
---|---|
Computer-Aided Design (CAD) | Precise and detailed mold design, simulation, and analysis of mold performance |
Finite Element Analysis (FEA) | Simulation of mold behavior under thermal stress, pressure, and deformation |
Rapid Prototyping | Quick and cost-effective production of mold prototypes for testing and validation |
Automation and Robotics | Enhanced precision, consistency, and efficiency through automated mold handling, part ejection, and quality inspection |
Environmental Considerations
Die casting, like any manufacturing process, has environmental implications that must be considered. Key environmental considerations include:
-
Energy Efficiency: Optimizing the die casting process to reduce energy consumption is essential for sustainability. This involves efficient use of resources, minimizing waste, and implementing energy-saving technologies.
-
Waste Management: Proper management of waste materials, including scrap metal, coolant, and lubricants, is crucial to minimize environmental impact. Recycling and reuse of materials can significantly reduce waste.
-
Emission Control: Controlling emissions from the die casting process, such as fumes and gases, is important for air quality and worker safety. Ventilation systems and emission control technologies help mitigate these issues.
-
Sustainable Materials: Using sustainable and recyclable materials in die casting molds and parts contributes to environmental sustainability. This includes the use of recycled metals and eco-friendly coolants.
Table 5: Environmental Considerations in Die Casting
Consideration | Description |
---|---|
Energy Efficiency | Optimization of the die casting process to reduce energy consumption |
Waste Management | Proper management of waste materials, including scrap metal, coolant, and lubricants |
Emission Control | Control of emissions from the die casting process, such as fumes and gases |
Sustainable Materials | Use of sustainable and recyclable materials in die casting molds and parts |
Future Trends in Die Casting Mold Design
The future of die casting mold design is poised for significant advancements driven by technological innovations and sustainability goals. Some of the emerging trends include:
-
Additive Manufacturing: The integration of additive manufacturing techniques, such as 3D printing, is revolutionizing mold design and production. Additive manufacturing allows for the creation of complex mold geometries that are difficult or impossible to achieve with traditional methods.
-
Smart Manufacturing: The adoption of smart manufacturing technologies, including the Internet of Things (IoT), artificial intelligence (AI), and machine learning, is enhancing the efficiency and precision of die casting. These technologies enable real-time monitoring, data analysis, and predictive maintenance.
-
Lightweight Materials: The demand for lightweight materials in various industries, particularly automotive and aerospace, is driving the development of new alloys and composites for die casting. These materials offer improved strength-to-weight ratios and enhanced performance.
-
Sustainable Practices: Increasing emphasis on sustainability is leading to the adoption of eco-friendly practices in die casting. This includes the use of renewable energy sources, recycling of materials, and implementation of green manufacturing processes.
Table 6: Future Trends in Die Casting Mold Design
Trend | Description |
---|---|
Additive Manufacturing | Integration of 3D printing for complex mold geometries |
Smart Manufacturing | Adoption of IoT, AI, and machine learning for real-time monitoring and data analysis |
Lightweight Materials | Development of new alloys and composites for improved strength-to-weight ratios |
Sustainable Practices | Adoption of eco-friendly practices, including renewable energy and recycling |
Conclusion
The design of die casting molds for radiator parts is a multifaceted process that requires careful consideration of various factors, including mold materials, design parameters, cooling systems, and maintenance practices. Advancements in technology and a growing emphasis on sustainability are driving innovations in die casting mold design, enhancing efficiency, precision, and environmental responsibility. As the demand for high-quality, complex radiator parts continues to grow, the importance of optimized die casting mold design will only increase. By embracing advanced technologies and sustainable practices, the die casting industry can meet the challenges of the future and contribute to a more efficient and eco-friendly manufacturing landscape.
Reprint Statement: If there are no special instructions, all articles on this site are original. Please indicate the source for reprinting:https://www.cncmachiningptj.com/,thanks!
3, 4 and 5-axis precision CNC machining services for aluminum machining, beryllium, carbon steel, magnesium, titanium machining, Inconel, platinum, superalloy, acetal, polycarbonate, fiberglass, graphite and wood. Capable of machining parts up to 98 in. turning dia. and +/-0.001 in. straightness tolerance. Processes include milling, turning, drilling, boring, threading, tapping, forming, knurling, counterboring, countersinking, reaming and laser cutting. Secondary services such as assembly, centerless grinding, heat treating, plating and welding. Prototype and low to high volume production offered with maximum 50,000 units. Suitable for fluid power, pneumatics, hydraulics and valve applications. Serves the aerospace, aircraft, military, medical and defense industries.PTJ will strategize with you to provide the most cost-effective services to help you reach your target,Welcome to Contact us ( sales@pintejin.com ) directly for your new project.
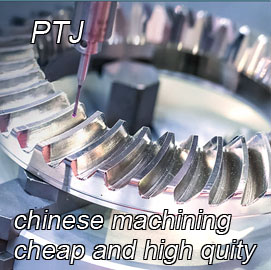
- 5 Axis Machining
- Cnc Milling
- Cnc Turning
- Machining Industries
- Machining Process
- Surface Treatment
- Metal Machining
- Plastic Machining
- Powder Metallurgy Mold
- Die Casting
- Parts Gallery
- Auto Metal Parts
- Machinery Parts
- LED Heatsink
- Building Parts
- Mobile Parts
- Medical Parts
- Electronic Parts
- Tailored Machining
- Bicycle Parts
- Aluminum Machining
- Titanium Machining
- Stainless Steel Machining
- Copper Machining
- Brass Machining
- Super Alloy Machining
- Peek Machining
- UHMW Machining
- Unilate Machining
- PA6 Machining
- PPS Machining
- Teflon Machining
- Inconel Machining
- Tool Steel Machining
- More Material