Ion Nitriding of H13 Steel for Aluminum Alloy Die Casting Molds
Ion nitriding, also known as plasma nitriding, is a surface hardening process that involves the diffusion of nitrogen into the surface of a metal to create a case-hardened surface. This process is particularly beneficial for H13 steel, which is widely used in the manufacturing of aluminum alloy die casting molds. H13 steel, also known as AISI H13 or DIN 1.2344, is a hot-work tool steel characterized by its high toughness, resistance to thermal fatigue, and excellent wear resistance. The combination of ion nitriding and H13 steel results in a material that is highly suitable for the demanding conditions of die casting molds.
Introduction to Ion Nitriding
Ion nitriding is a thermochemical treatment process that uses a glow discharge plasma to introduce nitrogen into the surface of a metal. The process is carried out in a vacuum chamber where a high voltage is applied to create a plasma. The plasma consists of ionized nitrogen and hydrogen, which are accelerated towards the metal surface. The nitrogen ions diffuse into the metal, forming a hardened layer known as the nitrided case.
The primary advantages of ion nitriding over other nitriding methods include:
- Uniformity: The process ensures a uniform nitrided layer, even on complex geometries.
- Precision: The depth of the nitrided layer can be precisely controlled.
- Environmental Friendliness: The process does not require the use of hazardous chemicals, making it more environmentally friendly.
- Efficiency: The process can be completed in a shorter time compared to traditional nitriding methods.
Properties of H13 Steel
H13 steel is a chromium-molybdenum-vanadium alloy that is specifically designed for hot-work applications. Its chemical composition typically includes:
- Carbon (C): 0.32-0.45%
- Chromium (Cr): 4.75-5.50%
- Molybdenum (Mo): 1.10-1.75%
- Vanadium (V): 0.80-1.20%
- Silicon (Si): 0.80-1.20%
- Manganese (Mn): 0.20-0.50%
The unique combination of these elements provides H13 steel with the following properties:
- High Toughness: The steel exhibits excellent toughness, which is crucial for withstanding the thermal and mechanical stresses encountered in die casting.
- Thermal Fatigue Resistance: H13 steel can withstand repeated heating and cooling cycles without significant degradation.
- Wear Resistance: The steel's hardness and microstructure contribute to its superior wear resistance.
- Machinability: Despite its high hardness, H13 steel can be machined relatively easily in its annealed state.
Ion Nitriding Process for H13 Steel
The ion nitriding process for H13 steel involves several key steps:
- Preparation: The steel is cleaned to remove any surface contaminants that could interfere with the nitriding process. This typically involves degreasing and ultrasonic cleaning.
- Loading: The cleaned steel is loaded into the vacuum chamber of the ion nitriding furnace.
- Evacuation: The chamber is evacuated to create a vacuum, ensuring that the process is free from atmospheric contaminants.
- Heating: The steel is heated to the desired nitriding temperature, typically between 450°C and 550°C.
- Plasma Generation: A high voltage is applied to generate a plasma consisting of ionized nitrogen and hydrogen.
- Nitriding: The nitrogen ions diffuse into the steel surface, forming a nitrided case. The depth of the nitrided layer can be controlled by adjusting the process parameters such as temperature, time, and voltage.
- Cooling: After the nitriding process is complete, the steel is cooled down to room temperature.
- Unloading: The nitrided steel is removed from the vacuum chamber.
Benefits of Ion Nitriding for H13 Steel
Ion nitriding offers several benefits for H13 steel, particularly when used in aluminum alloy die casting molds:
- Improved Wear Resistance: The nitrided layer significantly enhances the wear resistance of the steel, reducing the likelihood of surface degradation during die casting.
- Enhanced Corrosion Resistance: The nitrided layer provides a barrier against corrosive elements, extending the lifespan of the mold.
- Increased Surface Hardness: The nitrided case increases the surface hardness of the steel, making it more resistant to abrasion and erosion.
- Reduced Thermal Fatigue: The nitrided layer helps to reduce thermal fatigue, which is a common issue in die casting molds due to repeated heating and cooling cycles.
- Uniform Hardness: The ion nitriding process ensures a uniform hardness distribution across the surface of the steel, even on complex geometries.
Comparison of Ion Nitriding with Other Nitriding Methods
To understand the advantages of ion nitriding, it is useful to compare it with other nitriding methods such as gas nitriding and salt bath nitriding. The following table provides a detailed comparison:
Feature | Ion Nitriding | Gas Nitriding | Salt Bath Nitriding |
---|---|---|---|
Process Medium | Plasma (ionized gas) | Gaseous (ammonia) | Molten salt bath |
Temperature Range | 450°C - 550°C | 490°C - 560°C | 500°C - 590°C |
Uniformity | High | Moderate | Low |
Precision | High | Moderate | Low |
Environmental Impact | Low (no hazardous chemicals) | Moderate (ammonia emissions) | High (hazardous salt disposal) |
Process Time | Short | Moderate | Long |
Surface Finish | Excellent | Good | Fair |
Cost | Moderate | Low | High |
Applications of Ion Nitrided H13 Steel in Die Casting Molds
Ion nitrided H13 steel is widely used in the manufacturing of aluminum alloy die casting molds due to its superior properties. Some of the key applications include:
- Automotive Components: Die casting molds for producing automotive parts such as engine blocks, transmission cases, and structural components.
- Aerospace Industry: Molds for casting aerospace components that require high precision and durability.
- Consumer Electronics: Molds for producing metal housings and structural components for electronic devices.
- Industrial Machinery: Molds for casting machine parts that require high wear resistance and thermal stability.
- Medical Devices: Molds for producing medical instruments and implants that demand precise dimensions and high corrosion resistance.
Case Studies and Industrial Examples
Several case studies and industrial examples highlight the effectiveness of ion nitriding for H13 steel in die casting molds:
- Automotive Industry: A leading automotive manufacturer reported a 30% increase in the lifespan of die casting molds made from ion nitrided H13 steel compared to traditional gas nitrided molds. The improved wear resistance and reduced thermal fatigue contributed to the extended lifespan.
- Aerospace Industry: An aerospace component manufacturer observed a significant reduction in surface defects and improved dimensional stability in die casting molds made from ion nitrided H13 steel. The molds were used to produce critical aerospace components with high precision requirements.
- Consumer Electronics: A consumer electronics company reported a 25% increase in production efficiency due to the reduced downtime and maintenance requirements of ion nitrided H13 steel molds. The molds were used to produce metal housings for high-end electronic devices.
Future Trends and Innovations
The field of ion nitriding for H13 steel is continually evolving, with several future trends and innovations on the horizon:
- Advanced Plasma Technologies: The development of advanced plasma technologies is expected to further enhance the precision and uniformity of the nitrided layer.
- Hybrid Treatments: Combining ion nitriding with other surface treatments such as PVD (Physical Vapor Deposition) coatings can provide additional benefits such as enhanced corrosion resistance and improved tribological properties.
- Automation and Digitalization: The integration of automation and digitalization in the ion nitriding process can improve efficiency, reduce human error, and enable real-time monitoring and control.
- Sustainable Practices: The focus on sustainable practices is driving the development of more environmentally friendly ion nitriding processes, including the use of renewable energy sources and the reduction of waste.
Conclusion
Ion nitriding of H13 steel is a highly effective surface hardening process that significantly enhances the properties of die casting molds used in the production of aluminum alloy components. The process offers numerous benefits, including improved wear resistance, enhanced corrosion resistance, increased surface hardness, and reduced thermal fatigue. Compared to other nitriding methods, ion nitriding provides superior uniformity, precision, and environmental friendliness. The applications of ion nitrided H13 steel in various industries, along with case studies and future trends, highlight the importance and potential of this technology. As the field continues to evolve, the adoption of advanced technologies and sustainable practices will further enhance the capabilities and benefits of ion nitriding for H13 steel.
Reprint Statement: If there are no special instructions, all articles on this site are original. Please indicate the source for reprinting:https://www.cncmachiningptj.com/,thanks!
3, 4 and 5-axis precision CNC machining services for aluminum machining, beryllium, carbon steel, magnesium, titanium machining, Inconel, platinum, superalloy, acetal, polycarbonate, fiberglass, graphite and wood. Capable of machining parts up to 98 in. turning dia. and +/-0.001 in. straightness tolerance. Processes include milling, turning, drilling, boring, threading, tapping, forming, knurling, counterboring, countersinking, reaming and laser cutting. Secondary services such as assembly, centerless grinding, heat treating, plating and welding. Prototype and low to high volume production offered with maximum 50,000 units. Suitable for fluid power, pneumatics, hydraulics and valve applications. Serves the aerospace, aircraft, military, medical and defense industries.PTJ will strategize with you to provide the most cost-effective services to help you reach your target,Welcome to Contact us ( sales@pintejin.com ) directly for your new project.
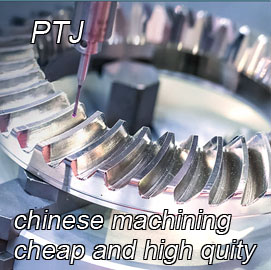
- 5 Axis Machining
- Cnc Milling
- Cnc Turning
- Machining Industries
- Machining Process
- Surface Treatment
- Metal Machining
- Plastic Machining
- Powder Metallurgy Mold
- Die Casting
- Parts Gallery
- Auto Metal Parts
- Machinery Parts
- LED Heatsink
- Building Parts
- Mobile Parts
- Medical Parts
- Electronic Parts
- Tailored Machining
- Bicycle Parts
- Aluminum Machining
- Titanium Machining
- Stainless Steel Machining
- Copper Machining
- Brass Machining
- Super Alloy Machining
- Peek Machining
- UHMW Machining
- Unilate Machining
- PA6 Machining
- PPS Machining
- Teflon Machining
- Inconel Machining
- Tool Steel Machining
- More Material