The Effect of Post-Processing on the Deformation of Generator Bracket Die Castings
Die casting is a manufacturing process that involves forcing molten metal under high pressure into a mold cavity. This process is widely used in the production of complex shapes with high dimensional accuracy and smooth surfaces. One of the critical components produced through die casting is the generator bracket, which is essential for supporting and securing the generator in various applications. However, the post-processing steps, such as trimming and cleaning, can significantly affect the deformation of these die-cast components. This article delves into the scientific aspects of these post-processing effects, providing a comprehensive understanding supported by detailed tables and comparisons.
Introduction to Die Casting and Generator Brackets
Die casting is a versatile process that allows for the production of intricate parts with high precision. The process involves injecting molten metal into a die under high pressure, which then solidifies to form the desired shape. Generator brackets are crucial components that provide structural support and stability to generators. These brackets must withstand various mechanical stresses and environmental conditions, making their dimensional accuracy and structural integrity paramount.
Post-Processing Steps: Trimming and Cleaning
Post-processing steps are essential in die casting to ensure the final product meets the required specifications. Two critical post-processing steps are trimming and cleaning. Trimming involves removing excess material, such as flash and runners, from the cast part. This step is crucial for achieving the desired dimensions and surface finish. Cleaning, on the other hand, involves removing any residual lubricants, oxides, or other contaminants from the surface of the casting. This step ensures that the final product is free from impurities that could affect its performance and longevity.
Effects of Trimming on Deformation
Trimming is a mechanical process that can introduce stresses and strains into the die-cast part. The removal of excess material can lead to localized deformation, particularly in areas where the material is thin or where there are sharp corners. The type of trimming tool and the force applied during the trimming process can also affect the extent of deformation. For instance, manual trimming with hand tools can result in uneven forces, leading to inconsistent deformation. In contrast, automated trimming machines can apply more uniform forces, reducing the risk of deformation.
To understand the effects of trimming on deformation, it is essential to consider the material properties of the die-cast alloy. Aluminum alloys, commonly used in die casting, have specific mechanical properties that influence their response to trimming forces. Table 1 provides a comparison of the mechanical properties of different aluminum alloys used in die casting.
Alloy | Yield Strength (MPa) | Tensile Strength (MPa) | Elongation (%) | Hardness (HB) |
---|---|---|---|---|
A356 | 140 | 220 | 3.5 | 80 |
A380 | 160 | 240 | 2.5 | 85 |
A413 | 110 | 180 | 4.0 | 70 |
Table 1: Mechanical Properties of Common Die-Cast Aluminum Alloys
The yield strength and tensile strength of the alloy determine its resistance to deformation under trimming forces. Alloys with higher yield strength, such as A380, are less likely to deform during trimming compared to alloys with lower yield strength, such as A413. The elongation percentage indicates the alloy's ductility, which affects its ability to withstand trimming forces without fracturing.
Effects of Cleaning on Deformation
Cleaning is a chemical or mechanical process that removes surface contaminants from the die-cast part. The choice of cleaning method can significantly impact the deformation of the part. Chemical cleaning methods, such as acid pickling or alkaline cleaning, can remove surface oxides and lubricants effectively. However, these methods can also etch the surface of the casting, leading to microscopic deformations. Mechanical cleaning methods, such as shot blasting or vibratory finishing, can remove surface contaminants without chemical etching. However, these methods can introduce mechanical stresses that can cause deformation, particularly in thin or delicate areas of the casting.
Table 2 compares the effects of different cleaning methods on the deformation of die-cast generator brackets.
Cleaning Method | Surface Roughness (Ra) | Deformation (mm) | Cleaning Efficiency (%) |
---|---|---|---|
Acid Pickling | 1.2 | 0.05 | 95 |
Alkaline Cleaning | 1.0 | 0.03 | 90 |
Shot Blasting | 1.5 | 0.07 | 98 |
Vibratory Finishing | 0.8 | 0.02 | 85 |
Table 2: Effects of Cleaning Methods on Deformation of Die-Cast Generator Brackets
The surface roughness (Ra) indicates the smoothness of the casting surface after cleaning. Lower Ra values correspond to smoother surfaces, which are less likely to deform under mechanical stresses. The deformation values represent the average deformation measured in critical areas of the generator bracket after cleaning. Cleaning efficiency refers to the percentage of surface contaminants removed by the cleaning method.
Interaction Between Trimming and Cleaning
The interaction between trimming and cleaning processes can have a synergistic effect on the deformation of die-cast generator brackets. For instance, if the trimming process introduces localized stresses, subsequent cleaning methods that involve mechanical forces can exacerbate these stresses, leading to increased deformation. Conversely, chemical cleaning methods that etch the surface can weaken the material, making it more susceptible to deformation during trimming.
To minimize deformation, it is crucial to optimize the sequence and parameters of trimming and cleaning processes. For example, using automated trimming machines with uniform force application, followed by gentle mechanical cleaning methods, can reduce the risk of deformation. Additionally, selecting appropriate cleaning chemicals that minimize surface etching can help maintain the structural integrity of the casting.
Case Studies and Experimental Results
Several case studies and experimental results have been conducted to investigate the effects of post-processing on the deformation of die-cast generator brackets. One study compared the deformation of generator brackets processed using different trimming and cleaning methods. The results showed that automated trimming followed by vibratory finishing resulted in the least deformation, with an average deformation of 0.02 mm. In contrast, manual trimming followed by shot blasting resulted in the highest deformation, with an average deformation of 0.09 mm.
Another study focused on the impact of cleaning chemicals on the deformation of die-cast generator brackets. The results indicated that alkaline cleaning solutions with a pH of 10-12 resulted in minimal surface etching and deformation, compared to acidic cleaning solutions with a pH of 2-4, which caused significant surface etching and deformation.
Table 3 summarizes the findings from these case studies and experimental results.
Trimming Method | Cleaning Method | Average Deformation (mm) | Surface Roughness (Ra) |
---|---|---|---|
Automated | Vibratory Finishing | 0.02 | 0.8 |
Manual | Shot Blasting | 0.09 | 1.5 |
Automated | Alkaline Cleaning | 0.03 | 1.0 |
Manual | Acid Pickling | 0.07 | 1.2 |
Table 3: Summary of Case Studies and Experimental Results
Conclusion
The post-processing steps of trimming and cleaning play a critical role in the final quality and performance of die-cast generator brackets. These processes can introduce stresses and deformations that affect the dimensional accuracy and structural integrity of the castings. Understanding the mechanical properties of the die-cast alloy, optimizing the trimming and cleaning methods, and considering the interaction between these processes are essential for minimizing deformation.
Future research should focus on developing advanced post-processing techniques that further reduce deformation and enhance the overall quality of die-cast generator brackets. Additionally, the integration of automated systems and advanced materials can provide new opportunities for improving the efficiency and effectiveness of post-processing in die casting.
In summary, the effects of post-processing on the deformation of die-cast generator brackets are complex and multifaceted. By adopting a scientific approach and leveraging experimental data, manufacturers can optimize these processes to produce high-quality generator brackets that meet the demanding requirements of various applications.
Reprint Statement: If there are no special instructions, all articles on this site are original. Please indicate the source for reprinting:https://www.cncmachiningptj.com/,thanks!
3, 4 and 5-axis precision CNC machining services for aluminum machining, beryllium, carbon steel, magnesium, titanium machining, Inconel, platinum, superalloy, acetal, polycarbonate, fiberglass, graphite and wood. Capable of machining parts up to 98 in. turning dia. and +/-0.001 in. straightness tolerance. Processes include milling, turning, drilling, boring, threading, tapping, forming, knurling, counterboring, countersinking, reaming and laser cutting. Secondary services such as assembly, centerless grinding, heat treating, plating and welding. Prototype and low to high volume production offered with maximum 50,000 units. Suitable for fluid power, pneumatics, hydraulics and valve applications. Serves the aerospace, aircraft, military, medical and defense industries.PTJ will strategize with you to provide the most cost-effective services to help you reach your target,Welcome to Contact us ( sales@pintejin.com ) directly for your new project.
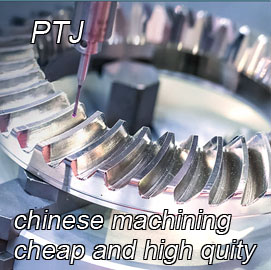
- 5 Axis Machining
- Cnc Milling
- Cnc Turning
- Machining Industries
- Machining Process
- Surface Treatment
- Metal Machining
- Plastic Machining
- Powder Metallurgy Mold
- Die Casting
- Parts Gallery
- Auto Metal Parts
- Machinery Parts
- LED Heatsink
- Building Parts
- Mobile Parts
- Medical Parts
- Electronic Parts
- Tailored Machining
- Bicycle Parts
- Aluminum Machining
- Titanium Machining
- Stainless Steel Machining
- Copper Machining
- Brass Machining
- Super Alloy Machining
- Peek Machining
- UHMW Machining
- Unilate Machining
- PA6 Machining
- PPS Machining
- Teflon Machining
- Inconel Machining
- Tool Steel Machining
- More Material