3-Axis Machining Trajectory Generation Method for Various Types of Tools on Free-Form Surfaces Based on Wireframe Models
The field of computer-aided manufacturing (CAM) has witnessed significant advancements, particularly in the realm of 3-axis machining. This process involves the use of computer numerical control (CNC) machines to create complex shapes and surfaces from raw materials. One of the critical aspects of 3-axis machining is the generation of toolpaths, which define the trajectory that the cutting tool follows to shape the workpiece accurately. This article delves into the intricacies of 3-axis machining trajectory generation methods for various types of tools on free-form surfaces based on wireframe models.
Understanding Free-Form Surfaces and Wireframe Models
Free-form surfaces are complex, non-uniform shapes that cannot be described by simple geometric primitives such as planes, cylinders, or spheres. These surfaces are commonly used in industries like aerospace, automotive, and consumer goods, where aesthetic and functional requirements demand intricate designs. Wireframe models, on the other hand, represent the edges and vertices of a 3D object, providing a skeletal framework that can be used to generate the toolpath.
Types of Tools in 3-Axis Machining
In 3-axis machining, various types of tools are employed to achieve different machining objectives. The most common tools include:
- End Mills: These are versatile tools used for milling flat surfaces, contours, and slots. They come in various shapes and sizes, including flat end mills, ball end mills, and bull nose end mills.
- Drills: Primarily used for creating holes, drills can also be employed for spot drilling and countersinking.
- Reamers: These tools are used to enlarge existing holes to precise dimensions.
- Taps: Used for creating internal threads in holes.
- Boring Tools: Employed for enlarging and finishing holes to precise dimensions.
Trajectory Generation Methods
The generation of toolpaths for 3-axis machining on free-form surfaces involves several steps, each requiring precise calculations and considerations. The following sections outline the key methods and considerations for trajectory generation.
1. Surface Discretization
The first step in generating a toolpath is the discretization of the free-form surface. This process involves breaking down the continuous surface into a finite number of points or segments that can be processed by the CNC machine. Common methods for surface discretization include:
- Triangulation: The surface is divided into a mesh of triangles, each representing a small section of the surface.
- Quadrilateral Meshing: Similar to triangulation, but the surface is divided into quadrilateral segments.
- NURBS (Non-Uniform Rational B-Splines): A mathematical representation of the surface that allows for precise control over the shape and curvature.
2. Toolpath Planning
Once the surface is discretized, the next step is to plan the toolpath. This involves determining the sequence of movements that the tool will follow to machine the surface accurately. Key considerations in toolpath planning include:
- Tool Orientation: The angle and direction of the tool relative to the surface.
- Feed Rate: The speed at which the tool moves along the surface.
- Depth of Cut: The amount of material removed in each pass.
- Stepover: The distance between adjacent toolpaths.
3. Toolpath Optimization
Optimization of the toolpath is crucial for ensuring efficiency and accuracy in the machining process. Various optimization techniques can be employed, including:
- Minimizing Tool Wear: Adjusting the toolpath to reduce the wear and tear on the cutting tool.
- Reducing Machining Time: Optimizing the feed rate and depth of cut to minimize the overall machining time.
- Ensuring Surface Quality: Adjusting the toolpath to achieve the desired surface finish and accuracy.
4. Collision Avoidance
Collision avoidance is a critical aspect of toolpath generation, especially for complex free-form surfaces. This involves ensuring that the tool does not collide with the workpiece or other parts of the machine during the machining process. Techniques for collision avoidance include:
- Clearance Planes: Defining clearance planes that the tool must stay above to avoid collisions.
- Tool Retraction: Programming the tool to retract from the surface at specific points to avoid collisions.
- Simulation: Using simulation software to visualize and verify the toolpath before actual machining.
Comparative Analysis of Trajectory Generation Methods
The following table provides a comparative analysis of different trajectory generation methods for 3-axis machining on free-form surfaces:
Method | Description | Advantages | Disadvantages |
---|---|---|---|
Triangulation | Surface is divided into a mesh of triangles. | Simple and easy to implement. | May result in less accurate representation of complex surfaces. |
Quadrilateral Meshing | Surface is divided into quadrilateral segments. | Provides a more accurate representation of the surface. | More complex to implement than triangulation. |
NURBS | Mathematical representation of the surface. | High precision and control over surface shape and curvature. | Requires advanced mathematical knowledge and computational resources. |
Zigzag Toolpath | Tool moves in a zigzag pattern across the surface. | Simple and efficient for flat surfaces. | May result in poor surface finish and accuracy for complex surfaces. |
Contour Toolpath | Tool follows the contour of the surface. | Provides high accuracy and surface finish. | May result in longer machining times. |
Spiral Toolpath | Tool moves in a spiral pattern from the center outwards. | Efficient for circular and spiral surfaces. | May result in poor surface finish for non-circular surfaces. |
Adaptive Toolpath | Toolpath adapts to the surface geometry in real-time. | Provides high accuracy and efficiency for complex surfaces. | Requires advanced algorithms and computational resources. |
Case Studies
Case Study 1: Aerospace Component Machining
In the aerospace industry, precision and accuracy are paramount. The machining of complex free-form surfaces, such as turbine blades and fuselage components, requires advanced trajectory generation methods. For example, the use of NURBS for surface discretization and adaptive toolpaths for machining can ensure high precision and surface quality.
Case Study 2: Automotive Part Machining
The automotive industry demands both precision and efficiency in machining. The use of contour toolpaths and optimization techniques can reduce machining time while maintaining high surface quality. For instance, the machining of engine blocks and cylinder heads can benefit from these methods.
Case Study 3: Consumer Goods Manufacturing
In the consumer goods industry, aesthetic appeal and functional performance are crucial. The use of spiral toolpaths and collision avoidance techniques can ensure efficient and accurate machining of complex shapes, such as plastic molds and electronic housings.
Future Trends
The field of 3-axis machining trajectory generation is continually evolving, driven by advancements in technology and increasing demands for precision and efficiency. Future trends include:
- Artificial Intelligence (AI) and Machine Learning (ML): The use of AI and ML algorithms to optimize toolpaths and predict machining outcomes.
- Additive Manufacturing: Integration of additive manufacturing techniques with traditional machining to create complex parts with intricate internal structures.
- Industry 4.0: The adoption of Industry 4.0 principles, such as the Internet of Things (IoT) and cloud computing, to enhance machining processes and improve productivity.
Conclusion
The generation of 3-axis machining trajectories for various types of tools on free-form surfaces based on wireframe models is a complex and multifaceted process. It involves surface discretization, toolpath planning, optimization, and collision avoidance. By employing advanced methods and technologies, manufacturers can achieve high precision, efficiency, and surface quality in their machining processes. As the field continues to evolve, the integration of AI, ML, and Industry 4.0 principles will further enhance the capabilities and outcomes of 3-axis machining.
Reprint Statement: If there are no special instructions, all articles on this site are original. Please indicate the source for reprinting:https://www.cncmachiningptj.com/,thanks!
3, 4 and 5-axis precision CNC machining services for aluminum machining, beryllium, carbon steel, magnesium, titanium machining, Inconel, platinum, superalloy, acetal, polycarbonate, fiberglass, graphite and wood. Capable of machining parts up to 98 in. turning dia. and +/-0.001 in. straightness tolerance. Processes include milling, turning, drilling, boring, threading, tapping, forming, knurling, counterboring, countersinking, reaming and laser cutting. Secondary services such as assembly, centerless grinding, heat treating, plating and welding. Prototype and low to high volume production offered with maximum 50,000 units. Suitable for fluid power, pneumatics, hydraulics and valve applications. Serves the aerospace, aircraft, military, medical and defense industries.PTJ will strategize with you to provide the most cost-effective services to help you reach your target,Welcome to Contact us ( sales@pintejin.com ) directly for your new project.
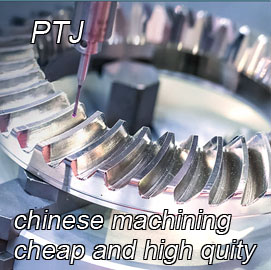
- 5 Axis Machining
- Cnc Milling
- Cnc Turning
- Machining Industries
- Machining Process
- Surface Treatment
- Metal Machining
- Plastic Machining
- Powder Metallurgy Mold
- Die Casting
- Parts Gallery
- Auto Metal Parts
- Machinery Parts
- LED Heatsink
- Building Parts
- Mobile Parts
- Medical Parts
- Electronic Parts
- Tailored Machining
- Bicycle Parts
- Aluminum Machining
- Titanium Machining
- Stainless Steel Machining
- Copper Machining
- Brass Machining
- Super Alloy Machining
- Peek Machining
- UHMW Machining
- Unilate Machining
- PA6 Machining
- PPS Machining
- Teflon Machining
- Inconel Machining
- Tool Steel Machining
- More Material