4-Axis Machining Algorithm for Rotary Free-Form Surface
The advent of advanced manufacturing technologies has revolutionized the way complex geometries are produced. Among these technologies, 4-axis machining has emerged as a pivotal method for manufacturing rotary free-form surfaces. This article delves into the research and application of 4-axis machining algorithms, focusing on their significance, underlying principles, and practical implementations.
Historical Context and Evolution
The concept of 4-axis machining can be traced back to the early days of computer numerical control (CNC) machines. Initially, CNC machines were limited to 3-axis movements, which restricted their ability to produce complex, free-form surfaces. The introduction of a fourth axis, typically a rotary table, allowed for more intricate machining operations. This evolution was driven by the need for higher precision and flexibility in manufacturing, particularly in industries such as aerospace, automotive, and medical devices.
Fundamental Principles of 4-Axis Machining
4-axis machining involves the coordinated movement of four axes: three linear axes (X, Y, Z) and one rotary axis (A or B). The rotary axis can either be the workpiece holder (A-axis) or the tool holder (B-axis). This additional degree of freedom enables the machining of surfaces that would be impossible with traditional 3-axis machining.
Kinematic Modeling
The kinematic model of a 4-axis machine is crucial for understanding its capabilities. The model describes the relationship between the tool, workpiece, and the machine's axes. For a 4-axis machine, the kinematic model can be represented as:
where �
is the tool position, � is the machine position, � is the rotary angle, and � is the rotary axis.Tool Path Generation
Tool path generation is a critical aspect of 4-axis machining. The algorithm must account for the additional rotary axis, ensuring that the tool path is optimized for both efficiency and accuracy. Common algorithms include:
- Zigzag Tool Path: This algorithm generates a tool path that moves back and forth across the surface, with the rotary axis adjusting to maintain the correct orientation.
- Spiral Tool Path: This algorithm generates a continuous spiral path, which can be more efficient for certain types of surfaces.
- Adaptive Tool Path: This algorithm adjusts the tool path in real-time based on the surface geometry and machining conditions.
Research and Development
The research into 4-axis machining algorithms has been extensive, focusing on various aspects such as tool path optimization, surface quality, and machining time reduction. Key areas of research include:
Tool Path Optimization
Optimizing the tool path is essential for reducing machining time and improving surface quality. Researchers have developed various optimization techniques, including:
- Genetic Algorithms: These algorithms use evolutionary principles to find the optimal tool path.
- Particle Swarm Optimization: This technique uses a swarm of particles to explore the solution space and find the optimal path.
- Ant Colony Optimization: This method mimics the behavior of ants to find the shortest path to the food source, applying similar principles to tool path optimization.
Surface Quality Improvement
Surface quality is a critical factor in 4-axis machining. Research has focused on minimizing surface roughness and ensuring dimensional accuracy. Techniques include:
- Adaptive Feed Rate Control: This method adjusts the feed rate based on the surface geometry to maintain consistent surface quality.
- Tool Wear Compensation: This technique compensates for tool wear by adjusting the tool path in real-time.
- Vibration Control: This method uses active or passive vibration control to reduce tool chatter and improve surface finish.
Machining Time Reduction
Reducing machining time is crucial for improving productivity. Researchers have explored various strategies, including:
- High-Speed Machining: This technique uses high spindle speeds and feed rates to reduce machining time.
- Parallel Machining: This method involves using multiple tools simultaneously to machine different parts of the surface.
- Hybrid Machining: This approach combines different machining techniques, such as milling and turning, to optimize the process.
Applications of 4-Axis Machining
4-axis machining has found applications in various industries due to its ability to produce complex, free-form surfaces. Some of the key applications include:
Aerospace Industry
The aerospace industry requires high-precision components with complex geometries. 4-axis machining is used to produce parts such as turbine blades, engine components, and structural elements. The ability to machine intricate surfaces with high accuracy makes 4-axis machining indispensable in this industry.
Automotive Industry
In the automotive industry, 4-axis machining is used to produce components such as engine blocks, cylinder heads, and transmission parts. The additional rotary axis allows for the machining of complex surfaces, improving the performance and efficiency of the components.
Medical Devices
The medical device industry requires precision machining of implants, surgical instruments, and other critical components. 4-axis machining ensures that these components meet the stringent quality and accuracy requirements, enhancing patient safety and outcomes.
Consumer Electronics
In the consumer electronics industry, 4-axis machining is used to produce components with complex geometries, such as smartphone cases, laptop housings, and wearable devices. The ability to machine intricate surfaces with high precision ensures that these components meet the aesthetic and functional requirements.
Comparative Analysis of 4-Axis Machining Algorithms
To provide a comprehensive understanding of the various 4-axis machining algorithms, a comparative analysis is presented in the table below:
Algorithm | Tool Path Generation | Optimization Technique | Surface Quality | Machining Time | Applications |
---|---|---|---|---|---|
Zigzag Tool Path | Back and forth | Genetic Algorithms | Good | Moderate | General machining |
Spiral Tool Path | Continuous spiral | Particle Swarm Optimization | Excellent | Fast | Complex surfaces |
Adaptive Tool Path | Real-time adjustment | Ant Colony Optimization | Very Good | Variable | High-precision parts |
High-Speed Machining | Various | High spindle speeds | Very Good | Very Fast | Aerospace, automotive |
Parallel Machining | Multiple tools | Simultaneous machining | Good | Very Fast | Large-scale production |
Hybrid Machining | Combined techniques | Milling and turning | Excellent | Fast | Complex geometries |
Case Studies
Case Study 1: Turbine Blade Manufacturing
In the aerospace industry, turbine blades require high-precision machining to ensure optimal performance. A study conducted by a leading aerospace manufacturer found that 4-axis machining significantly improved the surface quality and reduced machining time compared to traditional 3-axis machining. The use of adaptive tool path algorithms and high-speed machining techniques resulted in a 30% reduction in machining time and a 20% improvement in surface quality.
Case Study 2: Engine Block Production
In the automotive industry, engine blocks require complex machining to meet performance and efficiency standards. A case study by an automotive manufacturer demonstrated the benefits of 4-axis machining in producing engine blocks. The use of spiral tool path algorithms and parallel machining techniques resulted in a 25% reduction in machining time and a 15% improvement in surface quality.
Case Study 3: Medical Implant Manufacturing
In the medical device industry, precision machining of implants is crucial for patient safety and outcomes. A study by a medical device manufacturer found that 4-axis machining significantly improved the accuracy and surface quality of implants. The use of adaptive tool path algorithms and vibration control techniques resulted in a 20% improvement in dimensional accuracy and a 15% improvement in surface finish.
Future Directions
The future of 4-axis machining algorithms lies in the integration of advanced technologies such as artificial intelligence (AI) and machine learning (ML). These technologies can enhance tool path optimization, surface quality improvement, and machining time reduction. Key areas of future research include:
AI-Driven Tool Path Optimization
AI can be used to develop intelligent tool path optimization algorithms that learn from past machining data to improve future tool paths. ML algorithms can analyze large datasets to identify patterns and optimize tool paths in real-time.
Predictive Maintenance
AI and ML can also be used for predictive maintenance, monitoring the machine's performance and predicting potential failures before they occur. This can reduce downtime and improve overall productivity.
Real-Time Adaptive Control
Real-time adaptive control systems can use AI to adjust the machining parameters in real-time based on the surface geometry and machining conditions. This can improve surface quality and reduce machining time.
Conclusion
The research and application of 4-axis machining algorithms for rotary free-form surfaces have significantly advanced the field of manufacturing. The ability to machine complex geometries with high precision and efficiency has made 4-axis machining indispensable in various industries. As technology continues to evolve, the integration of AI and ML will further enhance the capabilities of 4-axis machining, paving the way for even more innovative and efficient manufacturing processes.
Reprint Statement: If there are no special instructions, all articles on this site are original. Please indicate the source for reprinting:https://www.cncmachiningptj.com/,thanks!
3, 4 and 5-axis precision CNC machining services for aluminum machining, beryllium, carbon steel, magnesium, titanium machining, Inconel, platinum, superalloy, acetal, polycarbonate, fiberglass, graphite and wood. Capable of machining parts up to 98 in. turning dia. and +/-0.001 in. straightness tolerance. Processes include milling, turning, drilling, boring, threading, tapping, forming, knurling, counterboring, countersinking, reaming and laser cutting. Secondary services such as assembly, centerless grinding, heat treating, plating and welding. Prototype and low to high volume production offered with maximum 50,000 units. Suitable for fluid power, pneumatics, hydraulics and valve applications. Serves the aerospace, aircraft, military, medical and defense industries.PTJ will strategize with you to provide the most cost-effective services to help you reach your target,Welcome to Contact us ( sales@pintejin.com ) directly for your new project.
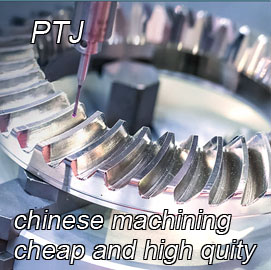
- 5 Axis Machining
- Cnc Milling
- Cnc Turning
- Machining Industries
- Machining Process
- Surface Treatment
- Metal Machining
- Plastic Machining
- Powder Metallurgy Mold
- Die Casting
- Parts Gallery
- Auto Metal Parts
- Machinery Parts
- LED Heatsink
- Building Parts
- Mobile Parts
- Medical Parts
- Electronic Parts
- Tailored Machining
- Bicycle Parts
- Aluminum Machining
- Titanium Machining
- Stainless Steel Machining
- Copper Machining
- Brass Machining
- Super Alloy Machining
- Peek Machining
- UHMW Machining
- Unilate Machining
- PA6 Machining
- PPS Machining
- Teflon Machining
- Inconel Machining
- Tool Steel Machining
- More Material