Optimization Design of Free-Form Surface Ultra-Precision Turning Machining Path
The optimization design of free-form surface ultra-precision turning machining path is a critical aspect of modern manufacturing, particularly in industries requiring high precision and complex geometries. Free-form surfaces, characterized by their irregular and non-uniform shapes, present unique challenges in machining. Ultra-precision turning, a subset of precision machining, demands extremely high accuracy and surface finish, often in the sub-micron range. This article delves into the intricacies of optimizing the machining path for free-form surfaces, covering various aspects such as tool path generation, error compensation, and surface quality assessment.
Historical Context
The evolution of precision machining can be traced back to the early 20th century, with significant advancements occurring in the latter half of the century. The advent of computer numerical control (CNC) machines in the 1950s revolutionized manufacturing by enabling automated and precise control over machining processes. Ultra-precision machining, specifically, gained prominence in the 1980s with the development of diamond turning machines capable of achieving nanometer-level precision.
Free-form surfaces, which are prevalent in aerospace, automotive, and optical industries, require sophisticated machining techniques. Traditional machining methods, such as milling and grinding, often fall short in achieving the required precision and surface quality for free-form surfaces. Ultra-precision turning, with its ability to produce highly accurate and smooth surfaces, has emerged as a viable solution.
Tool Path Generation
Tool path generation is the cornerstone of ultra-precision turning for free-form surfaces. The goal is to create a path that minimizes machining time, reduces tool wear, and ensures high surface quality. Several algorithms and techniques have been developed to optimize tool path generation.
Parametric Surface Representation
Free-form surfaces are often represented using parametric equations, such as Non-Uniform Rational B-Splines (NURBS). NURBS provide a flexible and accurate way to describe complex surfaces, making them ideal for CNC machining. The parametric representation allows for precise control over the surface geometry, enabling the generation of smooth and continuous tool paths.
Discretization Methods
Discretization involves converting the continuous parametric surface into a discrete set of points that the tool can follow. Common discretization methods include:
- Uniform Sampling: This method involves sampling points at regular intervals along the surface. While simple, it may not capture the intricacies of complex surfaces, leading to inaccuracies.
- Adaptive Sampling: This technique adjusts the sampling density based on the surface curvature. Areas with high curvature are sampled more densely, ensuring better accuracy.
- Isoparametric Methods: These methods generate tool paths along isoparametric curves, which are curves of constant parameter values. This approach ensures that the tool path follows the natural contours of the surface.
Tool Path Strategies
Several tool path strategies have been developed to optimize the machining process:
- Contour Parallel: In this strategy, the tool follows paths that are parallel to the surface contours. This method is effective for surfaces with gentle curvatures but may struggle with highly irregular surfaces.
- Zigzag: The zigzag strategy involves moving the tool back and forth across the surface. This method is efficient for surfaces with uniform curvature but may result in tool marks on highly irregular surfaces.
- Spiral: The spiral strategy generates a continuous spiral path that covers the entire surface. This method is particularly effective for surfaces with radial symmetry.
Error Compensation
Error compensation is crucial in ultra-precision turning to achieve the desired surface quality. Errors can arise from various sources, including machine tool inaccuracies, tool wear, and material deformation.
Machine Tool Errors
Machine tool errors include geometric errors, such as axis misalignment, and kinematic errors, such as backlash. Compensation techniques involve:
- Calibration: Regular calibration of the machine tool can reduce geometric errors. Laser interferometers and other precision measurement tools are used for calibration.
- Error Mapping: Error mapping involves creating a detailed map of the machine tool's errors and using this map to compensate for errors during machining.
Tool Wear Compensation
Tool wear can significantly affect the surface quality. Compensation techniques include:
- Tool Condition Monitoring: Sensors and algorithms monitor the tool's condition in real-time, allowing for timely tool changes and adjustments.
- Adaptive Control: Adaptive control systems adjust the machining parameters, such as feed rate and spindle speed, based on the tool's condition to maintain consistent surface quality.
Material Deformation Compensation
Material deformation, particularly in soft materials, can lead to inaccuracies. Compensation techniques include:
- Pre-deformation Analysis: Finite element analysis (FEA) is used to predict material deformation and adjust the tool path accordingly.
- In-process Measurement: In-process measurement systems, such as laser scanners, monitor the surface during machining and make real-time adjustments to compensate for deformation.
Surface Quality Assessment
Surface quality assessment is essential to ensure that the machined surface meets the required specifications. Key metrics for surface quality include:
- Surface Roughness: Measured using parameters such as Ra (average roughness) and Rz (maximum height of the profile).
- Form Accuracy: The deviation of the machined surface from the desired shape.
- Waviness: The long-wavelength component of the surface profile, which can affect optical and mechanical properties.
Measurement Techniques
Several measurement techniques are used to assess surface quality:
- Contact Profilometry: Involves using a stylus to trace the surface profile. This method is accurate but can be time-consuming.
- Optical Profilometry: Uses optical methods, such as interferometry, to measure the surface profile. This method is non-contact and can provide high-resolution data.
- Scanning Electron Microscopy (SEM): Provides high-resolution images of the surface, allowing for detailed analysis of surface features.
Comparative Analysis
Table 1: Comparison of Surface Quality Measurement Techniques
Technique | Resolution | Speed | Non-Contact | Cost |
---|---|---|---|---|
Contact Profilometry | High | Slow | No | Moderate |
Optical Profilometry | Very High | Fast | Yes | High |
Scanning Electron Microscopy (SEM) | Extremely High | Slow | Yes | Very High |
Case Studies
Aerospace Industry
In the aerospace industry, free-form surfaces are common in components such as turbine blades and aircraft wings. Ultra-precision turning is used to achieve the required aerodynamic properties and structural integrity. A case study involving the machining of a turbine blade demonstrated a significant reduction in machining time and improved surface quality using adaptive sampling and spiral tool path strategies.
Optical Industry
The optical industry requires ultra-precision machining for components such as lenses and mirrors. A case study on the machining of an aspheric lens showed that error mapping and adaptive control techniques resulted in a surface roughness of less than 10 nm, meeting the stringent requirements for optical performance.
Automotive Industry
In the automotive industry, free-form surfaces are found in components such as engine blocks and cylinder heads. A case study on the machining of a cylinder head highlighted the importance of tool wear compensation and in-process measurement in achieving the desired surface quality and dimensional accuracy.
Future Directions
The field of ultra-precision turning for free-form surfaces is continually evolving, driven by advancements in technology and increasing demands for precision and complexity. Future directions include:
- Advanced Materials: The development of new materials, such as composites and advanced alloys, will require innovative machining techniques to achieve the desired surface quality.
- Hybrid Machining: Combining ultra-precision turning with other machining processes, such as laser machining and electrochemical machining, can offer unique advantages in terms of precision and efficiency.
- Artificial Intelligence: The integration of artificial intelligence (AI) and machine learning (ML) can enhance tool path generation, error compensation, and surface quality assessment. AI algorithms can analyze vast amounts of data to optimize machining parameters and predict tool wear and material deformation.
Conclusion
The optimization design of free-form surface ultra-precision turning machining path is a multifaceted challenge that requires a deep understanding of tool path generation, error compensation, and surface quality assessment. Advances in parametric surface representation, discretization methods, and tool path strategies have significantly improved the precision and efficiency of ultra-precision turning. Error compensation techniques, including machine tool calibration, tool wear monitoring, and material deformation analysis, are crucial for achieving the desired surface quality.
As the demand for complex and precise components continues to grow, the field of ultra-precision turning will play an increasingly important role. Future advancements in advanced materials, hybrid machining, and artificial intelligence promise to further enhance the capabilities and applications of ultra-precision turning, ensuring that it remains at the forefront of modern manufacturing technology.
Reprint Statement: If there are no special instructions, all articles on this site are original. Please indicate the source for reprinting:https://www.cncmachiningptj.com/,thanks!
3, 4 and 5-axis precision CNC machining services for aluminum machining, beryllium, carbon steel, magnesium, titanium machining, Inconel, platinum, superalloy, acetal, polycarbonate, fiberglass, graphite and wood. Capable of machining parts up to 98 in. turning dia. and +/-0.001 in. straightness tolerance. Processes include milling, turning, drilling, boring, threading, tapping, forming, knurling, counterboring, countersinking, reaming and laser cutting. Secondary services such as assembly, centerless grinding, heat treating, plating and welding. Prototype and low to high volume production offered with maximum 50,000 units. Suitable for fluid power, pneumatics, hydraulics and valve applications. Serves the aerospace, aircraft, military, medical and defense industries.PTJ will strategize with you to provide the most cost-effective services to help you reach your target,Welcome to Contact us ( sales@pintejin.com ) directly for your new project.
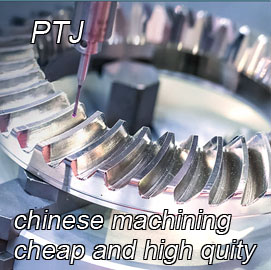
- 5 Axis Machining
- Cnc Milling
- Cnc Turning
- Machining Industries
- Machining Process
- Surface Treatment
- Metal Machining
- Plastic Machining
- Powder Metallurgy Mold
- Die Casting
- Parts Gallery
- Auto Metal Parts
- Machinery Parts
- LED Heatsink
- Building Parts
- Mobile Parts
- Medical Parts
- Electronic Parts
- Tailored Machining
- Bicycle Parts
- Aluminum Machining
- Titanium Machining
- Stainless Steel Machining
- Copper Machining
- Brass Machining
- Super Alloy Machining
- Peek Machining
- UHMW Machining
- Unilate Machining
- PA6 Machining
- PPS Machining
- Teflon Machining
- Inconel Machining
- Tool Steel Machining
- More Material