Ultra-Precision Processing Equipment and Technology for Aspheric Curved Optical Parts
Ultra-precision processing of aspheric curved optical parts is a critical field in modern optics and manufacturing. Aspheric lenses and mirrors are essential components in a wide range of optical systems, including telescopes, microscopes, cameras, and medical imaging devices. Unlike spherical lenses, which have a constant radius of curvature, aspheric lenses have a varying curvature that allows for the correction of optical aberrations, leading to superior image quality and performance.
The manufacturing of aspheric optical parts requires ultra-precision processing techniques to achieve the necessary surface accuracy and finish. This article delves into the various ultra-precision processing equipment and technologies employed in the production of aspheric curved optical parts, providing a comprehensive overview of the methods, tools, and advancements in this field.
Historical Background
The development of aspheric optical parts dates back to the early 20th century, but it was not until the advent of advanced manufacturing technologies in the latter half of the century that their production became feasible. Traditional lens manufacturing techniques, such as grinding and polishing, were initially adapted for aspheric surfaces, but these methods were limited in their ability to achieve the required precision.
With the introduction of computer numerical control (CNC) machines and other advanced manufacturing technologies, the production of aspheric optical parts became more precise and efficient. Today, ultra-precision processing equipment and technologies have reached a level of sophistication that allows for the manufacture of aspheric lenses with sub-nanometer surface accuracy.
Ultra-Precision Processing Equipment
Ultra-precision processing equipment for aspheric curved optical parts includes a variety of specialized machines and tools designed to achieve high levels of accuracy and surface finish. The following sections discuss some of the key equipment used in this field.
Computer Numerical Control (CNC) Machines
CNC machines are essential tools in the ultra-precision processing of aspheric optical parts. These machines use computer-controlled tools to shape and finish optical surfaces with high precision. CNC machines can be programmed to follow complex aspheric profiles, ensuring that the final product meets the required specifications.
There are several types of CNC machines used in the production of aspheric optical parts, including:
-
CNC Grinding Machines: These machines use diamond or other hard abrasive tools to grind the optical surface to the desired shape. CNC grinding machines can achieve high levels of precision and are often used for initial shaping and rough grinding.
-
CNC Polishing Machines: After grinding, the optical surface is polished to achieve a smooth finish. CNC polishing machines use soft abrasive tools and polishing compounds to remove any remaining surface irregularities and achieve the desired surface finish.
-
CNC Milling Machines: These machines use rotating cutting tools to remove material from the optical surface. CNC milling machines are particularly useful for creating complex aspheric profiles and can achieve high levels of precision.
Ultra-Precision Lathes
Ultra-precision lathes are specialized machines designed for turning and shaping optical surfaces with high precision. These lathes use diamond turning tools to cut the optical surface to the desired shape. Ultra-precision lathes can achieve sub-nanometer surface accuracy and are often used for the production of high-precision aspheric lenses and mirrors.
Magnetorheological Finishing (MRF) Machines
Magnetorheological finishing (MRF) is a advanced polishing technique that uses a magnetorheological fluid to polish optical surfaces. The fluid contains magnetic particles that can be controlled using a magnetic field, allowing for precise control of the polishing process. MRF machines can achieve high levels of surface finish and are particularly useful for correcting surface irregularities and achieving the desired aspheric profile.
Ion Beam Figuring (IBF) Machines
Ion beam figuring (IBF) is a non-contact polishing technique that uses a focused ion beam to remove material from the optical surface. IBF machines can achieve high levels of precision and are particularly useful for correcting surface irregularities and achieving the desired aspheric profile. The non-contact nature of IBF makes it ideal for polishing delicate optical surfaces without introducing additional stress or damage.
Ultra-Precision Processing Technologies
In addition to the specialized equipment discussed above, several advanced processing technologies are employed in the ultra-precision manufacturing of aspheric curved optical parts. These technologies include:
Diamond Turning
Diamond turning is a precision machining technique that uses a single-point diamond tool to cut the optical surface to the desired shape. Diamond turning can achieve sub-nanometer surface accuracy and is often used for the production of high-precision aspheric lenses and mirrors. The process involves rotating the optical part on a precision spindle while the diamond tool cuts the surface to the desired profile.
Magnetorheological Finishing (MRF)
Magnetorheological finishing (MRF) is a advanced polishing technique that uses a magnetorheological fluid to polish optical surfaces. The fluid contains magnetic particles that can be controlled using a magnetic field, allowing for precise control of the polishing process. MRF can achieve high levels of surface finish and is particularly useful for correcting surface irregularities and achieving the desired aspheric profile.
Ion Beam Figuring (IBF)
Ion beam figuring (IBF) is a non-contact polishing technique that uses a focused ion beam to remove material from the optical surface. IBF can achieve high levels of precision and is particularly useful for correcting surface irregularities and achieving the desired aspheric profile. The non-contact nature of IBF makes it ideal for polishing delicate optical surfaces without introducing additional stress or damage.
Chemical Mechanical Polishing (CMP)
Chemical mechanical polishing (CMP) is a polishing technique that combines chemical and mechanical processes to achieve a smooth surface finish. CMP uses a polishing slurry containing abrasive particles and chemical agents to remove material from the optical surface. The process can achieve high levels of surface finish and is particularly useful for polishing complex aspheric profiles.
Reactive Atom Plasma (RAP)
Reactive atom plasma (RAP) is a advanced polishing technique that uses a plasma of reactive atoms to remove material from the optical surface. RAP can achieve high levels of precision and is particularly useful for correcting surface irregularities and achieving the desired aspheric profile. The non-contact nature of RAP makes it ideal for polishing delicate optical surfaces without introducing additional stress or damage.
Comparison of Ultra-Precision Processing Techniques
The following table provides a comparison of the various ultra-precision processing techniques used in the manufacturing of aspheric curved optical parts:
Technique | Precision | Surface Finish | Material Removal Rate | Suitability for Complex Profiles | Non-Contact |
---|---|---|---|---|---|
Diamond Turning | Sub-nanometer | High | Moderate | High | No |
Magnetorheological Finishing (MRF) | High | Very High | Low | High | No |
Ion Beam Figuring (IBF) | High | Very High | Low | High | Yes |
Chemical Mechanical Polishing (CMP) | High | Very High | Moderate | High | No |
Reactive Atom Plasma (RAP) | High | Very High | Low | High | Yes |
Advancements in Ultra-Precision Processing
The field of ultra-precision processing for aspheric curved optical parts has seen significant advancements in recent years. These advancements include:
Nanoscale Precision
Advances in nanotechnology have enabled the development of ultra-precision processing techniques that can achieve nanoscale precision. These techniques allow for the manufacture of aspheric optical parts with sub-nanometer surface accuracy, leading to improved optical performance and image quality.
Automation and Robotics
The integration of automation and robotics in ultra-precision processing has greatly enhanced the efficiency and consistency of manufacturing processes. Automated CNC machines and robotic systems can perform complex manufacturing tasks with high precision and repeatability, reducing the need for manual intervention and minimizing human error.
Advanced Materials
The development of advanced materials, such as ultra-low expansion (ULE) glass and silicon carbide, has expanded the range of applications for aspheric optical parts. These materials offer superior optical properties and durability, making them ideal for use in high-performance optical systems.
In-Process Metrology
In-process metrology involves the use of advanced measurement techniques to monitor and control the manufacturing process in real-time. This allows for the detection and correction of any deviations from the desired specifications, ensuring that the final product meets the required standards. In-process metrology techniques include interferometry, profilometry, and coordinate measuring machines (CMMs).
Machine Learning and AI
The application of machine learning and artificial intelligence (AI) in ultra-precision processing has opened up new possibilities for optimizing manufacturing processes. AI algorithms can analyze large datasets to identify patterns and optimize processing parameters, leading to improved efficiency and accuracy. Machine learning can also be used to predict and correct for potential errors in the manufacturing process, further enhancing the quality of the final product.
Applications of Aspheric Curved Optical Parts
Aspheric curved optical parts are used in a wide range of applications, including:
Telescopes and Astronomy
Aspheric lenses and mirrors are essential components in modern telescopes and astronomical instruments. Their ability to correct optical aberrations and improve image quality makes them ideal for use in high-resolution imaging and spectroscopy. Aspheric optical parts are used in both ground-based and space-based telescopes, enabling astronomers to explore the universe with unprecedented detail.
Microscopy
Aspheric lenses are used in various types of microscopes, including optical microscopes, electron microscopes, and scanning probe microscopes. Their ability to correct optical aberrations and improve image quality makes them ideal for use in high-resolution imaging and analysis of biological and material samples.
Cameras and Imaging Systems
Aspheric lenses are used in a wide range of cameras and imaging systems, including digital cameras, video cameras, and medical imaging devices. Their ability to correct optical aberrations and improve image quality makes them ideal for use in high-resolution photography and videography.
Medical Imaging
Aspheric optical parts are used in various medical imaging devices, including endoscopes, laparoscopes, and ophthalmic instruments. Their ability to correct optical aberrations and improve image quality makes them ideal for use in diagnostic and surgical procedures, enabling doctors to visualize internal structures with high precision.
Defense and Aerospace
Aspheric optical parts are used in a variety of defense and aerospace applications, including surveillance systems, targeting systems, and satellite imaging. Their ability to correct optical aberrations and improve image quality makes them ideal for use in high-resolution imaging and analysis of military and aerospace targets.
Challenges and Future Directions
Despite the significant advancements in ultra-precision processing for aspheric curved optical parts, several challenges remain. These challenges include:
Material Limitations
The selection of appropriate materials for aspheric optical parts is a critical factor in their performance and durability. While advanced materials such as ULE glass and silicon carbide offer superior optical properties, they can be challenging to process and may require specialized manufacturing techniques.
Cost and Efficiency
The production of high-precision aspheric optical parts can be costly and time-consuming. Advances in automation, robotics, and machine learning can help to improve the efficiency and reduce the cost of manufacturing processes, but further research and development are needed to fully realize these benefits.
Environmental Factors
The manufacturing of aspheric optical parts is sensitive to environmental factors such as temperature, humidity, and vibration. Controlling these factors is essential for achieving the required precision and surface finish, but can be challenging in real-world manufacturing environments.
Regulatory and Standards Compliance
The production of aspheric optical parts must comply with various regulatory standards and industry specifications. Ensuring compliance with these standards can be complex and requires careful attention to detail in the manufacturing process.
Future Directions
The future of ultra-precision processing for aspheric curved optical parts holds great promise. Advances in nanotechnology, automation, robotics, and machine learning are expected to continue to drive innovation in this field, leading to the development of new manufacturing techniques and improved optical performance.
Research and development efforts are focused on several key areas, including:
Advanced Materials
The development of new materials with superior optical properties and durability will expand the range of applications for aspheric optical parts. Research is ongoing to identify and develop new materials that can meet the demanding requirements of modern optical systems.
Nanoscale Precision
Advances in nanotechnology will enable the development of ultra-precision processing techniques that can achieve even higher levels of nanoscale precision. This will lead to the manufacture of aspheric optical parts with even greater optical performance and image quality.
Automation and Robotics
The integration of advanced automation and robotics in ultra-precision processing will continue to enhance the efficiency and consistency of manufacturing processes. Automated CNC machines and robotic systems will become increasingly sophisticated, allowing for the production of high-precision aspheric optical parts with minimal human intervention.
Machine Learning and AI
The application of machine learning and AI in ultra-precision processing will continue to open up new possibilities for optimizing manufacturing processes. AI algorithms will become more advanced, enabling the analysis of even larger datasets and the identification of more complex patterns. This will lead to improved efficiency, accuracy, and quality in the production of aspheric optical parts.
In-Process Metrology
Advances in in-process metrology will enable even more precise monitoring and control of the manufacturing process. New measurement techniques and technologies will be developed, allowing for the detection and correction of even smaller deviations from the desired specifications. This will ensure that the final product meets the required standards with even greater precision.
Conclusion
Ultra-precision processing of aspheric curved optical parts is a critical field in modern optics and manufacturing. The development of advanced processing equipment and technologies has enabled the production of high-precision aspheric lenses and mirrors with superior optical performance and image quality. As research and development efforts continue to drive innovation in this field, the future of ultra-precision processing for aspheric optical parts holds great promise.
The integration of advanced materials, nanoscale precision, automation, robotics, machine learning, and in-process metrology will lead to the development of new manufacturing techniques and improved optical performance. These advancements will expand the range of applications for aspheric optical parts, enabling the development of new optical systems and technologies that will benefit a wide range of industries and applications.
In conclusion, the field of ultra-precision processing for aspheric curved optical parts is poised for significant growth and innovation. As researchers and engineers continue to push the boundaries of what is possible, the future of optics and manufacturing will be shaped by the development of new technologies and techniques that will enable the production of high-precision optical parts with unprecedented performance and quality.
Reprint Statement: If there are no special instructions, all articles on this site are original. Please indicate the source for reprinting:https://www.cncmachiningptj.com/,thanks!
3, 4 and 5-axis precision CNC machining services for aluminum machining, beryllium, carbon steel, magnesium, titanium machining, Inconel, platinum, superalloy, acetal, polycarbonate, fiberglass, graphite and wood. Capable of machining parts up to 98 in. turning dia. and +/-0.001 in. straightness tolerance. Processes include milling, turning, drilling, boring, threading, tapping, forming, knurling, counterboring, countersinking, reaming and laser cutting. Secondary services such as assembly, centerless grinding, heat treating, plating and welding. Prototype and low to high volume production offered with maximum 50,000 units. Suitable for fluid power, pneumatics, hydraulics and valve applications. Serves the aerospace, aircraft, military, medical and defense industries.PTJ will strategize with you to provide the most cost-effective services to help you reach your target,Welcome to Contact us ( sales@pintejin.com ) directly for your new project.
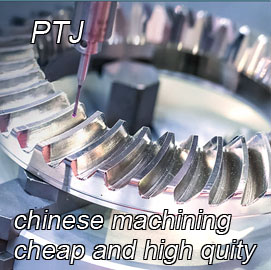
- 5 Axis Machining
- Cnc Milling
- Cnc Turning
- Machining Industries
- Machining Process
- Surface Treatment
- Metal Machining
- Plastic Machining
- Powder Metallurgy Mold
- Die Casting
- Parts Gallery
- Auto Metal Parts
- Machinery Parts
- LED Heatsink
- Building Parts
- Mobile Parts
- Medical Parts
- Electronic Parts
- Tailored Machining
- Bicycle Parts
- Aluminum Machining
- Titanium Machining
- Stainless Steel Machining
- Copper Machining
- Brass Machining
- Super Alloy Machining
- Peek Machining
- UHMW Machining
- Unilate Machining
- PA6 Machining
- PPS Machining
- Teflon Machining
- Inconel Machining
- Tool Steel Machining
- More Material