Curved Cams and Five-Axis Linkage Machining Centers
Curved cams are essential components in various mechanical systems, serving to convert rotational motion into linear or reciprocating motion. Their intricate shapes and precise requirements make them challenging to manufacture using traditional machining methods. The advent of five-axis linkage machining centers has revolutionized the production of curved cams, offering unparalleled precision, flexibility, and efficiency. This article delves into the processing of curved cams using five-axis linkage machining centers, exploring the technology, advantages, applications, and detailed comparisons with other machining methods.
Understanding Curved Cams
Curved cams are mechanical elements that use a rotating or sliding piece to create a specified output motion in a follower. The cam profile is designed to achieve a specific motion pattern, which can be linear, oscillating, or a combination of both. The complexity of the cam profile often requires high-precision machining to ensure accurate and reliable performance.
Types of Curved Cams
- Disk Cams: These are flat, circular cams with a groove or edge that guides the follower.
- Cylindrical Cams: These have a cylindrical shape with a groove or edge that guides the follower.
- Face Cams: These are similar to disk cams but have a more complex profile on the face of the cam.
- Linear Cams: These are straight cams that guide the follower in a linear motion.
Five-Axis Linkage Machining Centers
Five-axis linkage machining centers are advanced CNC (Computer Numerical Control) machines capable of moving the cutting tool or workpiece in five different axes simultaneously. This capability allows for the machining of complex shapes, including curved cams, with high precision and efficiency. The five axes typically include three linear axes (X, Y, Z) and two rotational axes (A, B).
Components of a Five-Axis Machining Center
- Spindle: The rotating part that holds the cutting tool.
- Worktable: The surface on which the workpiece is mounted.
- Linear Axes: X, Y, and Z axes for linear movement.
- Rotational Axes: A and B axes for rotational movement.
- Control System: The CNC system that controls the movement of the axes.
Advantages of Five-Axis Linkage Machining
- Precision: The ability to move in five axes simultaneously allows for highly precise machining of complex shapes.
- Flexibility: Can handle a wide range of materials and shapes, making it versatile for various applications.
- Efficiency: Reduces the need for multiple setups and tool changes, speeding up the production process.
- Quality: Ensures consistent and high-quality output, reducing the need for post-processing.
Processing Curved Cams with Five-Axis Linkage Machining Centers
The processing of curved cams using a five-axis linkage machining center involves several key steps:
- Design and CAM Programming: The cam profile is designed using CAD (Computer-Aided Design) software and then converted into a CAM (Computer-Aided Manufacturing) program.
- Material Selection: The appropriate material for the cam is selected based on the application requirements.
- Setup: The workpiece is mounted on the worktable, and the cutting tool is installed in the spindle.
- Machining: The CNC system controls the movement of the axes to machine the cam profile according to the CAM program.
- Finishing: Post-processing steps such as polishing or heat treatment may be applied to achieve the final surface finish and mechanical properties.
Detailed Comparison with Other Machining Methods
To understand the superiority of five-axis linkage machining centers, it is essential to compare them with other machining methods commonly used for curved cams.
Traditional Milling
Feature | Five-Axis Linkage Machining Center | Traditional Milling |
---|---|---|
Precision | High | Moderate |
Flexibility | High | Low |
Efficiency | High | Moderate |
Quality | High | Moderate |
Complexity Handling | High | Low |
Setup Time | Low | High |
Tool Changes | Minimal | Frequent |
Turning
Feature | Five-Axis Linkage Machining Center | Turning |
---|---|---|
Precision | High | Moderate |
Flexibility | High | Low |
Efficiency | High | Moderate |
Quality | High | Moderate |
Complexity Handling | High | Low |
Setup Time | Low | High |
Tool Changes | Minimal | Frequent |
EDM (Electrical Discharge Machining)
Feature | Five-Axis Linkage Machining Center | EDM |
---|---|---|
Precision | High | Very High |
Flexibility | High | Moderate |
Efficiency | High | Low |
Quality | High | Very High |
Complexity Handling | High | High |
Setup Time | Low | High |
Tool Changes | Minimal | Minimal |
Applications of Curved Cams Processed by Five-Axis Linkage Machining Centers
Curved cams processed by five-axis linkage machining centers find applications in various industries, including:
- Automotive: Used in engine valve trains, fuel injection systems, and transmission mechanisms.
- Aerospace: Employed in aircraft control systems, landing gear mechanisms, and engine components.
- Manufacturing: Utilized in automated machinery, robotics, and assembly lines.
- Medical: Applied in surgical instruments, prosthetics, and medical devices.
- Consumer Goods: Found in appliances, toys, and electronic devices.
Case Studies
Case Study 1: Automotive Valve Train
In the automotive industry, curved cams are crucial for engine valve trains. A leading automotive manufacturer utilized a five-axis linkage machining center to produce high-precision camshafts. The results showed a significant improvement in engine performance and fuel efficiency, with a reduction in production time by 30%.
Case Study 2: Aerospace Control System
An aerospace company employed a five-axis linkage machining center to manufacture curved cams for aircraft control systems. The precision and flexibility of the machining center allowed for the production of complex cam profiles, ensuring reliable and accurate control of the aircraft. The project resulted in a 25% increase in production efficiency and a 15% reduction in material waste.
Future Trends
The future of curved cam processing with five-axis linkage machining centers is promising. Advances in CNC technology, materials science, and automation are expected to further enhance the precision, efficiency, and flexibility of these machining centers. Key trends include:
- Integration of AI and Machine Learning: To optimize machining parameters and improve production efficiency.
- Advanced Materials: Development of new materials with superior mechanical properties for cam applications.
- Automation: Increased use of robotic systems for automated loading and unloading of workpieces.
- Sustainability: Focus on eco-friendly machining practices and reduction of material waste.
Conclusion
The processing of curved cams using five-axis linkage machining centers represents a significant advancement in manufacturing technology. The high precision, flexibility, and efficiency offered by these machining centers make them ideal for producing complex cam profiles with consistent quality. As technology continues to evolve, the capabilities of five-axis linkage machining centers are expected to expand, further enhancing their applications in various industries. The detailed comparisons and case studies presented in this article highlight the superiority of five-axis linkage machining centers over traditional machining methods, underscoring their importance in modern manufacturing.
Reprint Statement: If there are no special instructions, all articles on this site are original. Please indicate the source for reprinting:https://www.cncmachiningptj.com/,thanks!
3, 4 and 5-axis precision CNC machining services for aluminum machining, beryllium, carbon steel, magnesium, titanium machining, Inconel, platinum, superalloy, acetal, polycarbonate, fiberglass, graphite and wood. Capable of machining parts up to 98 in. turning dia. and +/-0.001 in. straightness tolerance. Processes include milling, turning, drilling, boring, threading, tapping, forming, knurling, counterboring, countersinking, reaming and laser cutting. Secondary services such as assembly, centerless grinding, heat treating, plating and welding. Prototype and low to high volume production offered with maximum 50,000 units. Suitable for fluid power, pneumatics, hydraulics and valve applications. Serves the aerospace, aircraft, military, medical and defense industries.PTJ will strategize with you to provide the most cost-effective services to help you reach your target,Welcome to Contact us ( sales@pintejin.com ) directly for your new project.
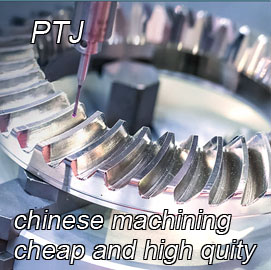
- 5 Axis Machining
- Cnc Milling
- Cnc Turning
- Machining Industries
- Machining Process
- Surface Treatment
- Metal Machining
- Plastic Machining
- Powder Metallurgy Mold
- Die Casting
- Parts Gallery
- Auto Metal Parts
- Machinery Parts
- LED Heatsink
- Building Parts
- Mobile Parts
- Medical Parts
- Electronic Parts
- Tailored Machining
- Bicycle Parts
- Aluminum Machining
- Titanium Machining
- Stainless Steel Machining
- Copper Machining
- Brass Machining
- Super Alloy Machining
- Peek Machining
- UHMW Machining
- Unilate Machining
- PA6 Machining
- PPS Machining
- Teflon Machining
- Inconel Machining
- Tool Steel Machining
- More Material