Clamping Technology of Aviation Special-Shaped Structural Parts Based on Five-Axis Machining Center
The aerospace industry is characterized by its demand for high precision, reliability, and efficiency in the manufacturing of special-shaped structural parts. These parts often have complex geometries and require advanced machining techniques to meet stringent performance criteria. The five-axis machining center has emerged as a pivotal tool in this domain, offering unparalleled flexibility and accuracy. This article delves into the clamping technology of aviation special-shaped structural parts based on five-axis machining centers, exploring the intricacies, advantages, and challenges associated with this technology.
Introduction to Five-Axis Machining Centers
Five-axis machining centers are advanced computer numerical control (CNC) machines capable of moving a part or a cutting tool along five different axes simultaneously. This capability allows for the machining of complex shapes and contours that would be impossible with traditional three-axis machines. The five axes typically include three linear axes (X, Y, Z) and two rotational axes (A, B, or C). This multi-axis movement enables the machining of intricate geometries with high precision and minimal setup time.
Importance of Clamping in Aviation Manufacturing
Clamping is a critical aspect of machining, particularly in the aerospace industry, where the precision and integrity of parts are paramount. Effective clamping ensures that the workpiece remains securely fixed during the machining process, preventing vibrations, deformations, and other issues that could compromise the quality of the finished part. In the context of special-shaped structural parts, clamping must accommodate the unique geometries and material properties of these components.
Types of Clamping Systems
Several clamping systems are employed in five-axis machining centers to secure aviation special-shaped structural parts. These include:
- Vice Clamps: Traditional vice clamps are used for simpler geometries and smaller parts. They provide a strong grip but may not be suitable for complex shapes.
- Hydraulic Clamps: These clamps use hydraulic pressure to secure the workpiece, offering a high clamping force and uniform pressure distribution.
- Pneumatic Clamps: Similar to hydraulic clamps, pneumatic clamps use compressed air to apply clamping force. They are quicker to operate but may not provide the same level of force as hydraulic systems.
- Vacuum Clamps: Vacuum clamps use suction to hold the workpiece in place. They are ideal for thin or delicate parts but may not be suitable for heavy or irregularly shaped components.
- Magnetic Clamps: These clamps use magnetic force to secure ferromagnetic materials. They are quick and easy to use but are limited to specific materials.
- Custom Fixtures: For highly specialized parts, custom fixtures are designed to fit the exact contours of the workpiece, ensuring optimal clamping and machining accuracy.
Comparison of Clamping Systems
Clamping System | Clamping Force | Suitability for Complex Geometries | Setup Time | Cost |
---|---|---|---|---|
Vice Clamps | High | Low | Moderate | Low |
Hydraulic Clamps | Very High | Moderate | High | High |
Pneumatic Clamps | High | Moderate | Low | Moderate |
Vacuum Clamps | Low | High | Low | Moderate |
Magnetic Clamps | Moderate | Low | Low | Moderate |
Custom Fixtures | Very High | Very High | Very High | Very High |
Advantages of Five-Axis Machining in Aviation
The use of five-axis machining centers in the aerospace industry offers several advantages:
- Precision and Accuracy: The ability to move along five axes allows for the machining of complex geometries with high precision, ensuring that parts meet the stringent tolerances required in aviation.
- Reduced Setup Time: Five-axis machines can often complete a part in a single setup, reducing the need for multiple setups and re-clamping, which can introduce errors.
- Improved Surface Finish: The continuous movement of the cutting tool along multiple axes results in a smoother surface finish, reducing the need for additional finishing processes.
- Increased Flexibility: Five-axis machines can handle a wide range of part geometries and materials, making them versatile tools in the manufacturing process.
- Enhanced Productivity: The ability to machine complex parts in a single setup reduces overall machining time, increasing productivity and efficiency.
Challenges and Considerations
While five-axis machining centers offer numerous benefits, they also present challenges, particularly in the context of clamping special-shaped structural parts:
- Complexity of Setup: The setup for five-axis machining can be complex, requiring skilled operators and precise calibration to ensure accurate machining.
- Cost: Five-axis machines and their associated clamping systems are typically more expensive than traditional three-axis machines, requiring a significant investment.
- Material Considerations: The choice of clamping system must consider the material properties of the workpiece, as some materials may be more susceptible to deformation or damage under certain clamping forces.
- Vibration and Stability: Ensuring stability and minimizing vibrations is crucial, as any movement of the workpiece during machining can compromise the quality of the finished part.
Case Studies and Applications
Several case studies highlight the successful application of five-axis machining centers in the aerospace industry:
- Aircraft Wing Components: The machining of aircraft wing components, such as ribs and spars, requires high precision and complex contouring. Five-axis machines with custom fixtures have been used to achieve the necessary accuracy and surface finish.
- Engine Components: Turbine blades and other engine components often have intricate geometries that demand precise machining. Hydraulic and pneumatic clamps have been effectively used to secure these parts during machining.
- Structural Frameworks: The manufacturing of structural frameworks for aircraft, such as fuselage sections, benefits from the flexibility and precision of five-axis machines. Vacuum clamps have been employed to hold thin, delicate parts securely.
Future Trends and Innovations
The field of five-axis machining is continually evolving, with several emerging trends and innovations:
- Automation and Robotics: The integration of automation and robotics in five-axis machining centers is enhancing productivity and reducing human error. Automated clamping systems are being developed to streamline the setup process.
- Advanced Materials: The development of new materials, such as composites and advanced alloys, is driving the need for more sophisticated clamping solutions. Research is ongoing to develop clamping systems that can handle these materials effectively.
- Digital Twins and Simulation: The use of digital twins and simulation software is helping to optimize the machining process, including clamping strategies. These tools allow for virtual testing and optimization before actual machining, reducing the risk of errors.
- Additive Manufacturing: The combination of additive manufacturing and five-axis machining is opening new possibilities for the creation of complex, lightweight parts. Clamping systems are being adapted to accommodate the unique requirements of additively manufactured components.
Conclusion
The clamping technology of aviation special-shaped structural parts based on five-axis machining centers is a critical aspect of modern aerospace manufacturing. The ability to machine complex geometries with high precision and efficiency is essential for meeting the stringent requirements of the industry. While challenges exist, ongoing innovations and advancements in technology are continually improving the capabilities and effectiveness of five-axis machining centers. As the demand for precision and efficiency in aerospace manufacturing continues to grow, the role of five-axis machining and advanced clamping systems will become even more pivotal.
Reprint Statement: If there are no special instructions, all articles on this site are original. Please indicate the source for reprinting:https://www.cncmachiningptj.com/,thanks!
3, 4 and 5-axis precision CNC machining services for aluminum machining, beryllium, carbon steel, magnesium, titanium machining, Inconel, platinum, superalloy, acetal, polycarbonate, fiberglass, graphite and wood. Capable of machining parts up to 98 in. turning dia. and +/-0.001 in. straightness tolerance. Processes include milling, turning, drilling, boring, threading, tapping, forming, knurling, counterboring, countersinking, reaming and laser cutting. Secondary services such as assembly, centerless grinding, heat treating, plating and welding. Prototype and low to high volume production offered with maximum 50,000 units. Suitable for fluid power, pneumatics, hydraulics and valve applications. Serves the aerospace, aircraft, military, medical and defense industries.PTJ will strategize with you to provide the most cost-effective services to help you reach your target,Welcome to Contact us ( sales@pintejin.com ) directly for your new project.
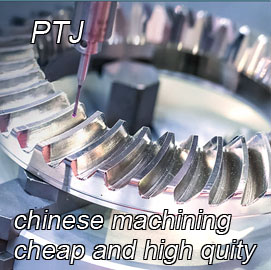
- 5 Axis Machining
- Cnc Milling
- Cnc Turning
- Machining Industries
- Machining Process
- Surface Treatment
- Metal Machining
- Plastic Machining
- Powder Metallurgy Mold
- Die Casting
- Parts Gallery
- Auto Metal Parts
- Machinery Parts
- LED Heatsink
- Building Parts
- Mobile Parts
- Medical Parts
- Electronic Parts
- Tailored Machining
- Bicycle Parts
- Aluminum Machining
- Titanium Machining
- Stainless Steel Machining
- Copper Machining
- Brass Machining
- Super Alloy Machining
- Peek Machining
- UHMW Machining
- Unilate Machining
- PA6 Machining
- PPS Machining
- Teflon Machining
- Inconel Machining
- Tool Steel Machining
- More Material