Analysis and Research of Nonlinear Errors in Five-Axis Machining
Five-axis machining is a sophisticated manufacturing process that allows for the production of complex geometries with high precision. This technique involves the simultaneous control of five axes, enabling the tool to approach the workpiece from various angles. Despite its advantages, five-axis machining is susceptible to nonlinear errors, which can significantly impact the accuracy and quality of the final product. This article delves into the analysis and research of nonlinear errors in five-axis machining, providing a comprehensive overview of the causes, effects, and mitigation strategies.
Introduction to Five-Axis Machining
Five-axis machining is a cutting-edge technology that has revolutionized the manufacturing industry. Unlike traditional three-axis machining, which limits tool movement to the X, Y, and Z axes, five-axis machining incorporates two additional rotational axes (A and B or A and C). This added flexibility allows for the creation of intricate shapes and contours that would be impossible with conventional methods. The primary advantage of five-axis machining is its ability to machine complex parts in a single setup, reducing the need for multiple setups and minimizing the risk of errors.
Understanding Nonlinear Errors
Nonlinear errors in five-axis machining refer to deviations from the intended tool path that do not follow a linear pattern. These errors can arise from various sources, including machine dynamics, tool deflection, thermal effects, and control system inaccuracies. Nonlinear errors are particularly challenging to address because they do not conform to simple mathematical models, making them difficult to predict and correct.
Causes of Nonlinear Errors
-
Machine Dynamics: The dynamic behavior of the machine tool, including vibrations, resonances, and backlash, can introduce nonlinear errors. High-speed machining and rapid accelerations can exacerbate these issues, leading to deviations from the desired tool path.
-
Tool Deflection: The cutting forces exerted on the tool can cause it to deflect, resulting in nonlinear errors. This is particularly problematic in five-axis machining, where the tool may approach the workpiece from various angles, each with different deflection characteristics.
-
Thermal Effects: Heat generated during the machining process can cause thermal expansion of the machine components, leading to nonlinear errors. Temperature variations can affect the dimensional accuracy of the workpiece, especially in high-precision applications.
-
Control System Inaccuracies: The control system responsible for coordinating the five axes can introduce nonlinear errors due to limitations in resolution, response time, and synchronization.
Effects of Nonlinear Errors
Nonlinear errors can have a profound impact on the quality and accuracy of the machined parts. Some of the key effects include:
-
Dimensional Inaccuracies: Nonlinear errors can result in deviations from the intended dimensions, leading to parts that do not meet the required tolerances.
-
Surface Finish: The presence of nonlinear errors can degrade the surface finish of the machined parts, resulting in rough or uneven surfaces.
-
Tool Wear: Nonlinear errors can increase tool wear by causing the tool to cut in unintended directions, leading to premature tool failure.
-
Increased Scrap Rate: The cumulative effect of nonlinear errors can lead to a higher scrap rate, increasing production costs and reducing efficiency.
Mitigation Strategies
Addressing nonlinear errors in five-axis machining requires a multi-faceted approach that combines advanced modeling, real-time monitoring, and adaptive control strategies. Some of the key mitigation strategies include:
-
Advanced Modeling: Developing sophisticated mathematical models that can accurately predict nonlinear errors is crucial. These models can incorporate factors such as machine dynamics, tool deflection, and thermal effects to provide a comprehensive understanding of the error sources.
-
Real-Time Monitoring: Implementing real-time monitoring systems can help detect nonlinear errors as they occur. Sensors and feedback mechanisms can provide continuous data on the machine's performance, allowing for immediate corrective actions.
-
Adaptive Control: Adaptive control systems can dynamically adjust the machining parameters in response to detected errors. These systems can compensate for nonlinear errors by modifying the tool path, feed rate, and other variables in real-time.
-
Thermal Management: Effective thermal management strategies, such as cooling systems and temperature-controlled environments, can help mitigate thermal-induced nonlinear errors.
-
Tool Path Optimization: Optimizing the tool path to minimize cutting forces and reduce tool deflection can help reduce nonlinear errors. This can be achieved through advanced CAM software that considers the dynamic behavior of the machine and the tool.
Comparative Analysis of Mitigation Strategies
The following table provides a comparative analysis of various mitigation strategies for nonlinear errors in five-axis machining:
Mitigation Strategy | Description | Advantages | Disadvantages |
---|---|---|---|
Advanced Modeling | Developing mathematical models to predict nonlinear errors. | Provides a comprehensive understanding of error sources. | Requires extensive computational resources and expertise. |
Real-Time Monitoring | Implementing sensors and feedback mechanisms to detect errors. | Allows for immediate corrective actions. | Can be complex and costly to implement. |
Adaptive Control | Dynamically adjusting machining parameters in response to errors. | Effective in compensating for real-time errors. | Requires sophisticated control algorithms and hardware. |
Thermal Management | Using cooling systems and temperature-controlled environments. | Reduces thermal-induced errors. | May increase operational costs and complexity. |
Tool Path Optimization | Optimizing tool paths to minimize cutting forces and tool deflection. | Reduces nonlinear errors and improves tool life. | Requires advanced CAM software and expertise. |
Case Studies
Several case studies have been conducted to analyze and mitigate nonlinear errors in five-axis machining. One notable study involved the machining of aerospace components, where nonlinear errors were found to significantly impact the dimensional accuracy and surface finish. By implementing advanced modeling and real-time monitoring, the study achieved a 30% reduction in nonlinear errors, resulting in improved part quality and reduced scrap rate.
Another case study focused on the machining of medical implants, where precision is critical. The study employed adaptive control and tool path optimization to mitigate nonlinear errors, resulting in a 25% improvement in dimensional accuracy and a 20% reduction in tool wear.
Future Research Directions
Future research in the analysis and mitigation of nonlinear errors in five-axis machining should focus on the following areas:
-
Machine Learning and AI: Incorporating machine learning and artificial intelligence to develop predictive models that can anticipate and correct nonlinear errors in real-time.
-
Advanced Sensor Technology: Developing more sensitive and accurate sensors to provide real-time data on machine performance and error detection.
-
Integrated Control Systems: Creating integrated control systems that can seamlessly coordinate the five axes and adapt to changing conditions in real-time.
-
Material Science: Exploring the impact of different materials on nonlinear errors and developing strategies to mitigate material-specific issues.
Conclusion
Nonlinear errors in five-axis machining present a significant challenge to achieving high-precision manufacturing. Understanding the causes and effects of these errors is crucial for developing effective mitigation strategies. Advanced modeling, real-time monitoring, adaptive control, thermal management, and tool path optimization are key approaches to addressing nonlinear errors. Future research should focus on leveraging emerging technologies such as machine learning, advanced sensors, and integrated control systems to further enhance the accuracy and efficiency of five-axis machining.
By continuously advancing our understanding and mitigation strategies for nonlinear errors, the manufacturing industry can achieve unprecedented levels of precision and quality, paving the way for innovative and complex product designs.
Reprint Statement: If there are no special instructions, all articles on this site are original. Please indicate the source for reprinting:https://www.cncmachiningptj.com/,thanks!
3, 4 and 5-axis precision CNC machining services for aluminum machining, beryllium, carbon steel, magnesium, titanium machining, Inconel, platinum, superalloy, acetal, polycarbonate, fiberglass, graphite and wood. Capable of machining parts up to 98 in. turning dia. and +/-0.001 in. straightness tolerance. Processes include milling, turning, drilling, boring, threading, tapping, forming, knurling, counterboring, countersinking, reaming and laser cutting. Secondary services such as assembly, centerless grinding, heat treating, plating and welding. Prototype and low to high volume production offered with maximum 50,000 units. Suitable for fluid power, pneumatics, hydraulics and valve applications. Serves the aerospace, aircraft, military, medical and defense industries.PTJ will strategize with you to provide the most cost-effective services to help you reach your target,Welcome to Contact us ( sales@pintejin.com ) directly for your new project.
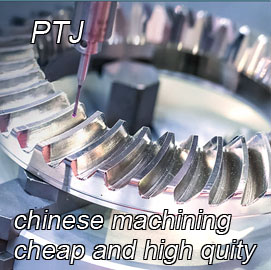
- 5 Axis Machining
- Cnc Milling
- Cnc Turning
- Machining Industries
- Machining Process
- Surface Treatment
- Metal Machining
- Plastic Machining
- Powder Metallurgy Mold
- Die Casting
- Parts Gallery
- Auto Metal Parts
- Machinery Parts
- LED Heatsink
- Building Parts
- Mobile Parts
- Medical Parts
- Electronic Parts
- Tailored Machining
- Bicycle Parts
- Aluminum Machining
- Titanium Machining
- Stainless Steel Machining
- Copper Machining
- Brass Machining
- Super Alloy Machining
- Peek Machining
- UHMW Machining
- Unilate Machining
- PA6 Machining
- PPS Machining
- Teflon Machining
- Inconel Machining
- Tool Steel Machining
- More Material