Tool Axis Vector Optimization Method for Five-Axis CNC Machining of Complex Surfaces
Five-axis CNC machining is widely used in the production of complex geometric parts across various industries, including aerospace, automotive, medical, and mold manufacturing. This technique enables the machining of complex surfaces with high precision, which is often difficult or impossible with conventional three-axis machining. One of the key challenges in five-axis CNC machining is the optimization of the tool axis vector, which plays a critical role in ensuring high-quality surface finishes, reducing tool wear, minimizing machining time, and enhancing overall machining efficiency.
The tool axis vector optimization method is employed to solve the problem of determining the optimal orientation of the cutting tool relative to the workpiece surface during the machining process. This method seeks to improve the accuracy and efficiency of the machining operation while maintaining the necessary machining constraints, such as surface quality, tool path continuity, and stability. The tool axis vector is defined as the direction in which the cutting tool's axis is oriented during the machining process. Proper optimization of this vector can significantly impact the precision of the machined surface, the life span of the cutting tool, and the overall productivity of the machining operation.
Importance of Tool Axis Vector Optimization
In five-axis CNC machining, the tool is mounted on a rotating spindle that can move along both the X, Y, and Z axes, as well as around the tool’s axis (A and B axes). This flexibility allows the tool to be positioned at virtually any angle relative to the workpiece, offering a significant advantage in machining complex parts. However, with this flexibility comes the challenge of determining the best tool axis orientation for each point on the workpiece’s surface.
The optimization of the tool axis vector is important for several reasons:
-
Surface Quality: The orientation of the tool relative to the surface affects the cutting forces and the quality of the surface finish. Suboptimal tool axis orientations may result in excessive tool deflection, vibration, or an undesirable surface finish.
-
Tool Life: Inappropriate tool axis orientations can cause uneven tool wear, leading to premature tool failure. By optimizing the tool axis vector, the tool wear is minimized, increasing its operational lifespan.
-
Machining Efficiency: The optimization process aims to reduce the time spent on unnecessary movements and reduce the time needed to reposition the tool. This contributes to overall efficiency, helping manufacturers reduce production costs and increase throughput.
-
Stability and Safety: In certain machining operations, particularly those involving hard materials or deep cuts, stability is paramount. An optimized tool axis vector helps in maintaining the stability of the tool, preventing undesired collisions and ensuring safety during machining.
-
Minimizing Toolpath Complexity: An optimal tool axis vector can reduce the complexity of tool paths, making the machining process smoother and requiring fewer reorientations, which can minimize machining time.
Methods for Tool Axis Vector Optimization
Several approaches are used to optimize the tool axis vector in five-axis CNC machining. These methods focus on the geometric relationship between the tool, the workpiece surface, and the machining conditions. The optimization process typically involves either analytic or heuristic algorithms, each with distinct advantages and limitations.
1. Geometric-Based Optimization
Geometric-based methods primarily rely on the shape of the workpiece and the geometry of the tool. These methods aim to find an optimal tool axis orientation by minimizing certain objective functions related to the geometry of the toolpath.
-
Normal Vector Method: One of the simplest approaches is to align the tool axis with the surface normal vector of the workpiece at each point of contact. The normal vector represents the direction that is perpendicular to the surface at a given point. While this method is computationally simple, it may not always lead to the most efficient toolpath or optimal cutting conditions, especially for complex surfaces or when avoiding obstacles is crucial.
-
Tool-Workpiece Angle Method: In this method, the tool axis is optimized by adjusting the angle between the tool and the workpiece surface. The goal is to find a balance between cutting forces, tool wear, and surface finish by minimizing the angle deviations.
2. Optimization Using Numerical Methods
Numerical optimization methods rely on mathematical models to iteratively search for the best tool axis orientation. These methods are highly flexible and can handle a wide variety of optimization criteria.
-
Gradient Descent Algorithms: In gradient-based methods, the tool axis vector is adjusted iteratively to minimize an objective function, such as cutting forces or tool wear. The algorithm uses the gradient of the function with respect to the tool axis orientation to determine the direction of change at each iteration.
-
Genetic Algorithms: Genetic algorithms (GAs) are a type of evolutionary algorithm that can be used to optimize tool axis vectors. These algorithms use a population-based approach, where a group of candidate solutions evolves over generations through selection, crossover, and mutation. GAs are particularly useful for solving complex, non-linear optimization problems, and they can handle multiple conflicting objectives.
-
Simulated Annealing: This optimization method mimics the physical process of heating and then slowly cooling a material to find the optimal state. In the context of tool axis optimization, simulated annealing explores different tool orientations by accepting changes that improve the objective function and occasionally accepting changes that worsen the solution to escape local optima.
3. Artificial Intelligence-Based Methods
Artificial intelligence (AI)-based approaches, particularly machine learning algorithms, have gained attention in the field of tool axis vector optimization. These methods can handle large datasets and identify complex patterns that traditional methods may overlook.
-
Neural Networks: Artificial neural networks (ANNs) can be trained on a set of input parameters (e.g., workpiece geometry, cutting conditions) and output the optimal tool axis vector. These networks are capable of learning complex relationships and can generalize well to new, unseen machining conditions.
-
Reinforcement Learning: Reinforcement learning (RL) is a type of machine learning where the optimization agent learns by interacting with its environment and receiving feedback in the form of rewards. RL has been used for tool path planning and optimization, where the agent learns to adjust the tool orientation based on the feedback from simulated or real-world machining operations.
4. Multi-Objective Optimization
In real-world machining, the tool axis vector optimization often involves balancing multiple conflicting objectives, such as minimizing cutting forces, improving surface finish, and reducing machining time. Multi-objective optimization methods seek to find a solution that offers the best trade-offs between these objectives.
-
Pareto Front Optimization: One common approach is to generate a Pareto front, which represents a set of optimal solutions where no objective can be improved without worsening another. The Pareto front helps engineers choose the best tool axis vector based on their specific priorities.
-
Weighting Method: Another approach is to assign weights to each objective based on its relative importance. The optimization algorithm then tries to minimize a weighted sum of the objective functions.
5. Hybrid Approaches
Hybrid optimization techniques combine two or more of the methods described above. For example, a genetic algorithm might be used in combination with a gradient-based method, or a neural network could be used to predict the outcomes of different tool orientations in a simulation environment.
Hybrid methods have proven effective in addressing the limitations of individual approaches, providing more robust and reliable optimization solutions.
Applications of Tool Axis Vector Optimization
Tool axis vector optimization methods have wide applications in industries where precision and efficiency are critical. These include:
-
Aerospace Manufacturing: The aerospace industry often requires the machining of highly complex parts, such as turbine blades and airframe components, with tight tolerances and high surface quality. The tool axis vector optimization method is crucial in these applications to ensure the part's performance and safety.
-
Automotive Industry: Complex surfaces in engine components, transmission parts, and body structures can be efficiently machined using five-axis CNC machines with optimized tool axis vectors.
-
Medical Device Manufacturing: The production of medical implants, prosthetics, and surgical tools demands precise machining of intricate surfaces. Tool axis vector optimization is essential to achieve the necessary accuracy and finish.
-
Mold and Die Manufacturing: The creation of molds and dies for injection molding, casting, and other manufacturing processes requires the machining of highly detailed surfaces. Optimization techniques ensure that the tool is positioned at the best angle to achieve the desired part geometry and surface quality.
Conclusion
The optimization of the tool axis vector in five-axis CNC machining is a critical aspect of producing high-quality, precision parts. By employing various optimization techniques, manufacturers can improve surface finishes, extend tool life, reduce machining time, and enhance overall efficiency. As computational power increases and optimization algorithms continue to evolve, the role of tool axis vector optimization will become even more crucial in the manufacturing of complex parts across diverse industries. This area of research holds the potential to significantly advance the capabilities of modern CNC machining, allowing for the production of even more intricate, high-performance components.
Reprint Statement: If there are no special instructions, all articles on this site are original. Please indicate the source for reprinting:https://www.cncmachiningptj.com/,thanks!
3, 4 and 5-axis precision CNC machining services for aluminum machining, beryllium, carbon steel, magnesium, titanium machining, Inconel, platinum, superalloy, acetal, polycarbonate, fiberglass, graphite and wood. Capable of machining parts up to 98 in. turning dia. and +/-0.001 in. straightness tolerance. Processes include milling, turning, drilling, boring, threading, tapping, forming, knurling, counterboring, countersinking, reaming and laser cutting. Secondary services such as assembly, centerless grinding, heat treating, plating and welding. Prototype and low to high volume production offered with maximum 50,000 units. Suitable for fluid power, pneumatics, hydraulics and valve applications. Serves the aerospace, aircraft, military, medical and defense industries.PTJ will strategize with you to provide the most cost-effective services to help you reach your target,Welcome to Contact us ( sales@pintejin.com ) directly for your new project.
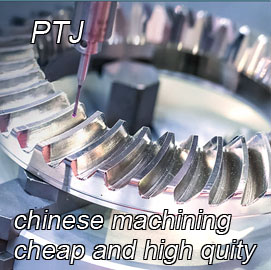
- 5 Axis Machining
- Cnc Milling
- Cnc Turning
- Machining Industries
- Machining Process
- Surface Treatment
- Metal Machining
- Plastic Machining
- Powder Metallurgy Mold
- Die Casting
- Parts Gallery
- Auto Metal Parts
- Machinery Parts
- LED Heatsink
- Building Parts
- Mobile Parts
- Medical Parts
- Electronic Parts
- Tailored Machining
- Bicycle Parts
- Aluminum Machining
- Titanium Machining
- Stainless Steel Machining
- Copper Machining
- Brass Machining
- Super Alloy Machining
- Peek Machining
- UHMW Machining
- Unilate Machining
- PA6 Machining
- PPS Machining
- Teflon Machining
- Inconel Machining
- Tool Steel Machining
- More Material