Sharp Corner Transition Processing in CNC Machining
Sharp corner transitions in CNC machining refer to the changes in direction or sharp bends that occur when the tool path transitions from one segment to another. These corners are often formed when machining intricate geometries or parts that have angular features. The challenge in sharp corner transitions arises because sharp changes in direction can cause a variety of issues, such as poor surface finish, tool wear, inaccuracies in the machining process, and even potential damage to the material or the cutting tool itself. As such, special techniques are employed to mitigate these issues, ensuring that sharp corners are processed accurately and efficiently.
Definition of Sharp Corners
In CNC machining, a sharp corner is a corner formed by two straight lines meeting at a defined angle, typically less than 90 degrees, or at a specific acute angle. The nature of the corner can vary depending on the part's geometry and the machining method being used. For example, in the case of milling or turning operations, sharp corners are frequently encountered when machining features like grooves, pockets, or contours that require tight, well-defined edges.
The definition of "sharp" varies depending on the specific machining process and the size and scale of the part being produced. While the term is often associated with angles of less than 90 degrees, in certain CNC applications, "sharp" may refer to transitions that are significantly tighter, such as angles approaching 30 degrees or even smaller.
Issues with Sharp Corner Transitions
Processing sharp corners in CNC machining presents numerous challenges that need to be addressed:
-
Tool Geometry: Most cutting tools are not designed with perfect corner angles in mind. Typically, tools have radii, meaning that when the tool path reaches a sharp corner, the tool may not be able to accurately trace the corner as designed. This can result in either an overcut or an undercut, leading to deviations from the desired geometry.
-
Surface Finish: The surface finish at sharp corners can often be subpar. This is particularly true when the tool enters a corner at a high feed rate or with insufficient dwell time, which prevents the tool from producing a smooth cut.
-
Tool Wear and Chatter: Machining sharp corners requires rapid changes in direction, which can cause the tool to experience uneven wear or even breakage if not properly managed. Additionally, the sharp direction change can induce tool chatter, which negatively impacts both the quality of the finish and the life of the tool.
-
Machining Efficiency: CNC machines may experience a loss of machining efficiency when attempting to process sharp corners, especially if high-speed operations are used. When the tool enters a corner, it must slow down significantly to make the sharp turn, which can increase cycle time and decrease overall productivity.
-
Material Properties: Certain materials, particularly brittle metals or those prone to work hardening (like stainless steel), present additional challenges during sharp corner transitions. These materials are more prone to cracking or chipping when subjected to abrupt tool movements.
Solutions for Sharp Corner Processing
-
Tool Radius Compensation: One of the most common approaches to sharp corner transitions is tool radius compensation. CNC machines are equipped with functions that allow the tool path to be offset by the radius of the tool to avoid overshooting or undercutting sharp corners. This technique is particularly useful in milling operations where the cutting tool is cylindrical, and the corner geometry is significantly smaller than the tool's radius.
-
Corner Radius Milling: Another solution is to intentionally round off sharp corners using a radius cutter, creating a more gradual transition. This is a form of pre-processing where the sharp corners are intentionally modified before proceeding with the main operation. This ensures that the tool has a smoother transition through the corner.
-
Adaptive Machining Strategies: Some advanced CNC systems are programmed to detect sharp corners and adjust the tool path accordingly. These adaptive machining systems modify the feed rate, spindle speed, or cutting parameters to accommodate sharp transitions. By slowing down the machine at critical points or modifying the tool’s approach to the corner, adaptive strategies can reduce the likelihood of poor results.
-
Multiple Passes: In some cases, machining a sharp corner in a single pass may not be effective. To improve the accuracy of the final product, a series of passes with a reduced depth of cut may be used. This gradual approach allows the tool to cut more accurately without overstressing the material or the cutting tool.
-
Tool Path Smoothing Algorithms: Specialized software may be used to smooth out the tool path at sharp corners. These algorithms reduce abrupt changes in direction, allowing the cutting tool to transition more smoothly through corners and reducing the strain on the tool.
-
Use of Specialized Tools: There are cutting tools specifically designed to handle sharp corner transitions more effectively. For example, ball-end mills and corner radius end mills can be used for high-precision work that requires sharp angular transitions. These tools help produce better finishes and minimize the stress on both the material and the cutting tool.
CNC Programming for Sharp Corner Transitions
CNC programming plays a significant role in handling sharp corner transitions. When programming a CNC machine to process sharp corners, several strategies can be applied to optimize the process:
-
Programming Corner Radius: When sharp corners are programmed in the machine, a corner radius is often added to the tool path. This radius compensates for the size of the tool, ensuring that the machine’s movements will not overcut or undercut the corner. This is particularly important when working with materials that require high precision, such as aerospace or medical components.
-
Tool Path Simulation: Before actual machining begins, a tool path simulation is typically performed using CNC software. This simulation helps identify any potential problems with sharp corners, such as tool interference or insufficient clearance. This step is especially important when dealing with complex geometries.
-
Cutting In and Cutting Out Programming
Cutting-In and Cutting-Out Programming in CNC Machining
Cutting-in and cutting-out programming refer to the methods used to control how the cutting tool enters and exits the material during a CNC operation. These techniques are crucial for achieving clean, accurate cuts, minimizing tool wear, and ensuring a smooth surface finish.
Cutting-In Programming
Cutting-in refers to the technique where the cutting tool begins its cut at a specific point along the part’s surface. The process starts from an initial point, either on the material’s edge or from within the material itself. The cutting tool then progresses along the designated tool path to remove material. The goal during cutting-in is to minimize stresses on the tool and workpiece, ensuring a smooth and efficient entry into the material.
There are several cutting-in strategies, including:
-
Linear Cutting-In: The tool begins the cut in a straight line along the tool path, moving from the entry point to the desired cutting position. This is a common technique used in milling and turning operations and is favored for its simplicity and effectiveness in straightforward cuts.
-
Helical Cutting-In: In more complex operations, particularly in deep drilling or when machining thick materials, a helical cutting-in approach may be employed. This technique involves the tool entering the material in a spiral pattern, gradually advancing in both the radial and axial directions.
-
Ramp Cutting-In: Ramp cutting-in is frequently used in operations where the cutting tool needs to enter the material at an inclined angle. This is useful for preventing tool chatter and reducing the risk of tool breakage when entering hard materials.
Cutting-Out Programming
Cutting-out refers to the technique where the cutting tool exits the material after completing a cut. Proper cutting-out programming is essential to ensure that the tool does not drag or bind upon exit, as this could lead to a poor surface finish, excessive tool wear, or even damage to the workpiece.
Some cutting-out strategies include:
-
Linear Cutting-Out: Similar to linear cutting-in, this method involves the tool following a straight path as it exits the material. This is often used when the tool must exit along the same path as it entered.
-
Retract Cutting-Out: In certain operations, the tool is retracted from the material in a controlled manner, ensuring that no excess force is applied that could distort the part or damage the material.
-
Ramp or Helical Cutting-Out: When exiting from deep holes or other intricate shapes, the tool may be programmed to exit using a ramp or helical pattern. This allows for a smoother exit, reducing the chances of residual burrs or tool damage.
-
Tool Path Optimization for Cutting-Out: Advanced CNC programming software can optimize the cutting-out sequence, adjusting the tool's exit path to minimize the impact on surface finish and tool longevity.
Advanced Techniques in Cutting-In and Cutting-Out
In modern CNC machining, cutting-in and cutting-out techniques are often enhanced by advanced technologies like 5-axis machining and adaptive tool paths. These advanced systems allow for more flexible and efficient cutting, especially when dealing with complex part geometries or materials that are difficult to machine.
5-axis machining, for example, enables the tool to enter and exit the material from multiple angles, providing greater flexibility in achieving sharp corners, smooth transitions, and complex profiles. Adaptive machining software can automatically adjust cutting parameters in real-time, optimizing the cutting-in and cutting-out processes to ensure the best possible results with minimal tool wear and maximum material removal rates.
Conclusion
Sharp corner transition processing and cutting-in and cutting-out programming are critical aspects of CNC machining that require careful planning, programming, and execution. Whether dealing with sharp corner geometries or ensuring smooth tool entry and exit, mastering these techniques is essential for producing high-quality parts with excellent surface finishes and dimensional accuracy. Through the use of advanced CNC programming methods, specialized tools, and adaptive machining strategies, these challenges can be effectively addressed, leading to improved productivity, reduced tool wear, and enhanced overall machining performance.
Continued advancements in CNC technology and programming software will further enhance the ability to handle complex transitions and tool engagements, contributing to faster production times and more efficient manufacturing processes across a variety of industries.
Reprint Statement: If there are no special instructions, all articles on this site are original. Please indicate the source for reprinting:https://www.cncmachiningptj.com/,thanks!
3, 4 and 5-axis precision CNC machining services for aluminum machining, beryllium, carbon steel, magnesium, titanium machining, Inconel, platinum, superalloy, acetal, polycarbonate, fiberglass, graphite and wood. Capable of machining parts up to 98 in. turning dia. and +/-0.001 in. straightness tolerance. Processes include milling, turning, drilling, boring, threading, tapping, forming, knurling, counterboring, countersinking, reaming and laser cutting. Secondary services such as assembly, centerless grinding, heat treating, plating and welding. Prototype and low to high volume production offered with maximum 50,000 units. Suitable for fluid power, pneumatics, hydraulics and valve applications. Serves the aerospace, aircraft, military, medical and defense industries.PTJ will strategize with you to provide the most cost-effective services to help you reach your target,Welcome to Contact us ( sales@pintejin.com ) directly for your new project.
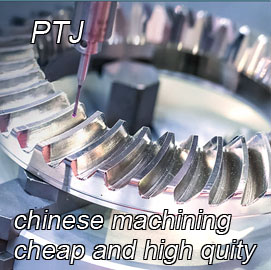
- 5 Axis Machining
- Cnc Milling
- Cnc Turning
- Machining Industries
- Machining Process
- Surface Treatment
- Metal Machining
- Plastic Machining
- Powder Metallurgy Mold
- Die Casting
- Parts Gallery
- Auto Metal Parts
- Machinery Parts
- LED Heatsink
- Building Parts
- Mobile Parts
- Medical Parts
- Electronic Parts
- Tailored Machining
- Bicycle Parts
- Aluminum Machining
- Titanium Machining
- Stainless Steel Machining
- Copper Machining
- Brass Machining
- Super Alloy Machining
- Peek Machining
- UHMW Machining
- Unilate Machining
- PA6 Machining
- PPS Machining
- Teflon Machining
- Inconel Machining
- Tool Steel Machining
- More Material