TOP 5 Corrosion-Resistant Metals
Corrosion resistance is one of the most critical factors to consider when selecting materials for various applications, particularly in industries like aerospace, automotive, marine, and construction. Metals, when exposed to environmental elements such as moisture, oxygen, and chemicals, undergo deterioration over time. This process, known as corrosion, can significantly reduce the material's mechanical properties, compromising the safety and reliability of structures and components. To mitigate the effects of corrosion, engineers often choose metals and alloys with superior resistance to degradation.
This article explores five metals known for their corrosion resistance: stainless steel, titanium, aluminum, zinc, and nickel. These materials offer a range of properties that make them suitable for diverse applications where corrosion resistance is paramount. The following sections delve into the composition, properties, corrosion resistance mechanisms, and common uses of these metals.
Stainless Steel
Stainless steel is an alloy of iron that contains at least 10.5% chromium by weight. This high chromium content is the key to stainless steel’s exceptional corrosion resistance, as it forms a thin, invisible chromium oxide layer on the surface of the steel. This oxide layer acts as a barrier, preventing further oxidation and protecting the metal from rust and corrosion, even in harsh environments.
Composition and Properties
Stainless steel is typically composed of iron, chromium, nickel, molybdenum, and sometimes other elements such as manganese, silicon, and carbon. The exact composition varies depending on the grade of stainless steel. The three most common types of stainless steel are:
- Austenitic Stainless Steel (Grade 304, 316): These steels are highly resistant to corrosion and are non-magnetic. They contain high amounts of chromium (16-26%) and nickel (8-35%), which impart excellent corrosion resistance, especially in acidic environments.
- Ferritic Stainless Steel (Grade 430, 446): Ferritic steels have lower chromium content (10-30%) and are magnetic. They exhibit good resistance to stress corrosion cracking and are typically used in less aggressive environments.
- Martensitic Stainless Steel (Grade 410, 420): These steels have lower chromium content (12-18%) and higher carbon content, making them stronger but less resistant to corrosion than austenitic or ferritic steels.
The alloying elements in stainless steel provide a balance between mechanical strength and corrosion resistance, making it suitable for a wide range of applications, from kitchen appliances to chemical processing equipment.
Corrosion Resistance Mechanism
The corrosion resistance of stainless steel is primarily attributed to the formation of a stable, passive oxide layer composed of chromium oxide (Cr₂O₃). This layer is self-healing, meaning that if it is damaged or scratched, the chromium in the steel will react with oxygen in the air or water to re-form the protective oxide layer.
One of the main challenges that stainless steel faces is pitting corrosion, which occurs in chloride-rich environments such as seawater. To improve resistance to pitting corrosion, grades such as 316 stainless steel contain molybdenum, which enhances the material's resistance to chlorides.
Applications of Stainless Steel
Stainless steel is used in a variety of industries due to its strength, aesthetic appeal, and ability to resist corrosion. Common applications include:
- Marine Industry: Due to its resistance to saltwater corrosion, stainless steel is widely used in marine vessels, offshore platforms, and naval ships.
- Aerospace: Stainless steel is used in components exposed to high stress and corrosive environments, such as aircraft landing gear, fasteners, and fuel systems.
- Medical Devices: The non-reactive nature of stainless steel makes it ideal for medical instruments and implants, such as surgical tools and joint replacements.
- Construction: Stainless steel is used for building facades, structural supports, and architectural finishes, particularly in coastal areas where the risk of corrosion is high.
Titanium
Titanium is a lightweight, strong, and highly corrosion-resistant metal that has become indispensable in many industries. It is the ninth most abundant element in the Earth's crust, often found in the form of ores such as rutile and ilmenite. The corrosion resistance of titanium is largely due to the formation of a thick, stable oxide layer, titanium dioxide (TiO₂), on its surface, which protects the metal from further degradation.
Composition and Properties
Titanium is often alloyed with other metals, such as aluminum, vanadium, and molybdenum, to enhance its mechanical properties. The pure form of titanium, known as Grade 1, has excellent corrosion resistance, especially in oxidizing environments. However, titanium alloys, such as Grade 5 (Ti-6Al-4V), which contains 6% aluminum and 4% vanadium, are often preferred for structural applications due to their increased strength and toughness.
Some key properties of titanium include:
- Strength-to-Weight Ratio: Titanium is about 45% lighter than steel but is almost as strong, making it highly desirable in applications where weight reduction is critical, such as aerospace.
- High Melting Point: Titanium has a high melting point of 1,668°C (3,034°F), which makes it suitable for high-temperature applications, including jet engines and turbines.
- Non-Toxicity: Titanium is biocompatible, meaning it does not induce adverse reactions in the human body, making it an ideal material for medical implants.
Corrosion Resistance Mechanism
Titanium’s resistance to corrosion is primarily due to the formation of titanium dioxide (TiO₂), a dense and stable oxide layer that is highly adherent to the metal surface. This oxide layer is capable of withstanding attack from various acids, alkalis, and saltwater. Titanium’s resistance to corrosion is particularly notable in reducing and acidic environments, where other metals might degrade quickly.
Titanium’s exceptional resistance to galvanic corrosion makes it particularly useful when in contact with other metals. In electrochemical environments, titanium does not corrode significantly, even when exposed to highly aggressive chemicals like hydrochloric acid, sulfuric acid, and chlorine.
Applications of Titanium
Titanium is used in a wide array of industries, including aerospace, medical, chemical processing, and marine. Some common applications include:
- Aerospace and Aviation: Titanium is used extensively in aircraft components such as wings, fuselage frames, and engine parts due to its high strength and light weight.
- Medical Implants: Titanium's biocompatibility makes it the material of choice for implants, including joint replacements, dental implants, and pacemaker components.
- Marine and Chemical Industries: Titanium is used in marine environments, such as boat hulls and offshore oil rigs, where resistance to saltwater corrosion is crucial. It is also employed in heat exchangers, desalination plants, and reactors due to its resistance to harsh chemicals.
Aluminum
Aluminum is one of the most widely used metals in the world due to its excellent corrosion resistance, lightweight nature, and versatility. The corrosion resistance of aluminum is primarily attributed to the formation of a thin oxide film (Al₂O₃) that forms on the surface when exposed to oxygen.
Composition and Properties
Pure aluminum has good corrosion resistance, but it is often alloyed with elements like copper, manganese, silicon, and zinc to improve its strength, machinability, and other properties. Some of the most common aluminum alloys include:
- 1000 Series (Pure Aluminum): These alloys contain 99% or more aluminum and are known for their high corrosion resistance, but they are relatively soft and weak.
- 2000 Series (Aluminum-Copper Alloys): These alloys offer high strength but lower corrosion resistance than pure aluminum. They are commonly used in aerospace applications.
- 6000 Series (Aluminum-Magnesium-Silicon Alloys): These alloys are popular in structural applications due to their good balance of strength, corrosion resistance, and formability.
Aluminum is widely used in the form of sheet metal, extrusions, and castings. It is lightweight, has a low density (about one-third that of steel), and is an excellent conductor of heat and electricity.
Corrosion Resistance Mechanism
The corrosion resistance of aluminum is attributed to the natural formation of a passive oxide layer of aluminum oxide (Al₂O₃). This layer forms quickly when aluminum is exposed to air and is highly resistant to further corrosion. The oxide layer is stable in both alkaline and acidic environments, and it protects the underlying metal from corrosion by acting as a physical barrier.
However, aluminum can suffer from pitting corrosion and galvanic corrosion when exposed to saltwater or contact with dissimilar metals. In such environments, the use of protective coatings or anodizing can significantly improve its corrosion resistance.
Applications of Aluminum
Aluminum’s excellent corrosion resistance, combined with its light weight and strength, makes it suitable for a broad range of applications, including:
- Aerospace: Aluminum alloys are used in the manufacture of aircraft structures, including fuselages, wings, and engines.
- Transportation: Aluminum is commonly used in automotive, marine, and railway applications to reduce weight and improve fuel efficiency.
- Construction: Aluminum is used for windows, doors, roofing, and cladding due to its resistance to weathering and corrosion, particularly in coastal environments.
Zinc
Zinc is a widely used metal that exhibits good corrosion resistance, especially when applied as a coating to protect other metals, most notably steel. The corrosion resistance of zinc is due to the formation of a protective patina that forms when the metal reacts with oxygen and moisture.
Composition and Properties
Zinc is typically used in two forms: pure zinc and zinc alloys. Pure zinc is generally used in coatings for steel and iron, while zinc alloys, which often include small amounts of aluminum, copper, and magnesium, are used in die-casting applications.
Zinc has a relatively low melting point (419°C or 786°F), which makes it easy to work with in casting and galvanizing processes. It is also relatively abundant and inexpensive, making it an attractive option for corrosion protection.
Corrosion Resistance Mechanism
Zinc protects underlying metals primarily through the process of sacrificial anode corrosion. When zinc is used as a coating, it corrodes preferentially to the metal it protects, thereby preventing the base metal from corroding. This is particularly effective in protecting steel from rusting. Over time, zinc develops a patina of zinc carbonate (ZnCO₃), which further enhances its corrosion resistance.
Zinc’s effectiveness in protecting steel is demonstrated in the process of galvanization, where a thin layer of zinc is applied to steel to protect it from corrosion. This method is widely used in the production of galvanized steel, which is used in construction, automotive, and appliance industries.
Applications of Zinc
Zinc is commonly used in the following applications:
- Galvanizing: The process of coating steel with zinc to protect it from corrosion, particularly in the automotive, construction, and infrastructure sectors.
- Die-Casting: Zinc alloys are used in die-casting to produce components for automotive, electronics, and hardware applications.
- Batteries: Zinc is used in the production of zinc-carbon and alkaline batteries, as well as in newer zinc-air batteries.
Nickel
Nickel is a highly corrosion-resistant metal that is often used as a base for alloys and coatings. It is resistant to oxidation and many forms of chemical corrosion, including attack by acids and alkalis.
Composition and Properties
Nickel is a transition metal that is widely alloyed with other elements, including chromium, iron, and copper, to produce alloys with enhanced properties. Some notable nickel alloys include:
- Inconel: A group of high-performance alloys made primarily from nickel and chromium, known for their exceptional heat and corrosion resistance.
- Monel: An alloy of nickel and copper, known for its resistance to corrosion in seawater and acidic environments.
Nickel’s resistance to corrosion, combined with its high melting point (1,453°C or 2,647°F), makes it useful in high-temperature applications such as in aerospace and chemical processing.
Corrosion Resistance Mechanism
Nickel’s corrosion resistance stems from the formation of a passive oxide layer, which protects the metal from further oxidation. This oxide layer is stable in a wide range of environments, including acids, alkalis, and saline solutions.
In addition to its natural corrosion resistance, nickel alloys like Inconel and Monel offer superior resistance to high-temperature oxidation, pitting, and stress corrosion cracking, making them ideal for extreme environments.
Applications of Nickel
Nickel is used in a wide range of applications, including:
- Alloy Production: Nickel is a critical component in the production of high-performance alloys for aerospace, power generation, and chemical processing industries.
- Batteries: Nickel is used in the manufacture of rechargeable batteries, including nickel-cadmium (NiCd) and nickel-metal hydride (NiMH) batteries.
- Plating and Coatings: Nickel plating is used to protect other metals from corrosion and to enhance their appearance, particularly in automotive and electrical industries.
Pre-hardened steel refers to a category of steels that have been heat-treated to a specific hardness level prior to their final use in various applications. This steel is particularly notable for its ability to retain hardness and strength while still maintaining sufficient ductility to facilitate machining and fabrication. Unlike fully hardened steels, which often require additional heat treatments or surface treatments post-fabrication, pre-hardened steels are ready for direct use once processed, making them a valuable material for numerous industrial applications.
Properties of Pre-Hardened Steel
The most defining characteristic of pre-hardened steel is its hardness, achieved through a controlled heat treatment process. Typically, the steel is subjected to quenching and tempering processes, resulting in a hardness level between 30 and 45 HRC (Hardness Rockwell C). This hardness level allows the steel to maintain a good balance between strength, toughness, and machinability. The specific hardness can be adjusted based on the alloy composition, tempering temperature, and cooling rates during processing.
The hardness of pre-hardened steel ensures that it offers excellent wear resistance, which makes it an ideal choice for manufacturing components that are exposed to high friction, such as molds, dies, and certain machine parts. However, the material retains some degree of toughness and flexibility, which is important for applications that require resilience against cracking or failure under stress.
Another key property of pre-hardened steel is its good machinability, particularly when compared to fully hardened steels. The material is harder than unhardened steels but still soft enough to allow for machining processes such as turning, milling, drilling, and grinding. This makes pre-hardened steel an attractive choice for parts that require precise machining but cannot undergo further heat treatment due to design constraints or cost limitations.
Pre-hardened steels are also characterized by good dimensional stability, which means that they maintain their shape and size under conditions of heat, stress, and strain. This is particularly beneficial in applications where high precision and repeatability are required.
Composition of Pre-Hardened Steel
The composition of pre-hardened steel can vary depending on the specific requirements of the intended application. However, pre-hardened steels generally contain a combination of elements that provide the desired mechanical properties. The alloying elements typically include carbon, chromium, nickel, molybdenum, and sometimes vanadium or tungsten.
-
Carbon: Carbon is a primary alloying element in steel, and its content plays a crucial role in determining the hardness and strength of the steel. In pre-hardened steels, carbon content is typically in the range of 0.30% to 0.60%. Higher carbon content increases hardness but may reduce the material's ductility and weldability.
-
Chromium: Chromium is added to improve the corrosion resistance and hardenability of the steel. It also enhances the steel's strength and wear resistance, making it an important element in pre-hardened steels used for applications in harsh environments.
-
Nickel: Nickel is known for improving the toughness and impact strength of steel. It also enhances the material's ability to resist corrosion and oxidation, which makes it an important alloying element in pre-hardened steels used in industrial equipment that is exposed to moisture or other corrosive elements.
-
Molybdenum: Molybdenum enhances the steel's resistance to wear and high-temperature strength. It is particularly useful in pre-hardened steels used for tooling and machinery components that must maintain their strength at elevated temperatures.
-
Vanadium and Tungsten: Vanadium and tungsten are sometimes added to improve the steel's resistance to abrasion, wear, and fatigue. These elements also enhance the material's overall strength and hardness.
The specific combination of these alloying elements determines the mechanical properties, including hardness, strength, and wear resistance, of the pre-hardened steel. For example, tool steels and die steels, which fall under the category of pre-hardened steels, may have higher amounts of carbon, chromium, and vanadium to meet the demanding requirements of mold-making and metal forming.
Heat Treatment Process for Pre-Hardened Steel
Pre-hardened steel undergoes a controlled heat treatment process to achieve its characteristic hardness. The heat treatment generally involves the following steps:
-
Heating: The steel is heated to a temperature above its critical point, typically between 800°C and 900°C, depending on the alloy composition. This heat treatment process is designed to transform the microstructure of the steel into austenite, a high-temperature phase of steel.
-
Quenching: The steel is then rapidly cooled, usually by immersion in water or oil, to transform the austenite into martensite, a hard, brittle phase of steel. This rapid cooling process increases the hardness of the material but also makes it more brittle.
-
Tempering: To reduce the brittleness and improve the toughness of the steel, it undergoes a tempering process. This involves reheating the steel to a lower temperature, typically between 200°C and 600°C, and then allowing it to cool slowly. The tempering process reduces internal stresses and refines the steel's microstructure, resulting in a more balanced set of mechanical properties.
The hardness of pre-hardened steel can be controlled by adjusting the parameters of the heat treatment process, including the quenching medium, tempering temperature, and time. By tailoring these factors, manufacturers can produce pre-hardened steels with varying degrees of hardness and toughness to suit specific application requirements.
Applications of Pre-Hardened Steel
Pre-hardened steels are used in a wide range of applications where a balance of hardness, strength, machinability, and toughness is required. Some of the key industries and applications include:
-
Tooling and Die Manufacturing: Pre-hardened steels are commonly used for manufacturing molds, dies, and punches, particularly in injection molding, die-casting, and stamping operations. The hardness of pre-hardened steels provides excellent wear resistance, while their machinability allows for intricate designs and precise tolerances.
-
Automotive Industry: Pre-hardened steels are widely used in the production of automotive components, including gears, shafts, and other machine parts. These components are subjected to high stresses and wear, making the hardness and durability of pre-hardened steel an ideal choice.
-
Aerospace and Defense: In the aerospace and defense industries, pre-hardened steels are used for manufacturing structural components, fasteners, and engine parts that must withstand extreme temperatures and mechanical stresses. The excellent strength-to-weight ratio of pre-hardened steels makes them particularly valuable for these demanding applications.
-
Heavy Equipment: Pre-hardened steels are used in the production of parts for heavy machinery, such as bulldozers, excavators, and mining equipment. These parts often need to resist wear and abrasion from harsh working conditions, and pre-hardened steels offer the right combination of properties for such applications.
-
Medical Devices: In the medical industry, pre-hardened steels are used for the manufacture of surgical instruments, dental tools, and implants. These components require high precision, strength, and wear resistance, which makes pre-hardened steel an ideal material choice.
-
Manufacturing and Processing Equipment: Pre-hardened steels are used in the construction of various manufacturing and processing equipment, such as presses, conveyors, and cutters. These steels can withstand wear and tear while maintaining their functionality over long periods of operation.
The versatility of pre-hardened steel makes it suitable for any application that requires a material with a high level of hardness and wear resistance, but without the need for extensive post-fabrication heat treatments or surface treatments.
Advantages and Disadvantages of Pre-Hardened Steel
Advantages:
-
Improved Efficiency: One of the major advantages of pre-hardened steel is that it eliminates the need for additional heat treatments after the part is fabricated. This can significantly reduce production time and costs, especially for high-volume manufacturing processes.
-
Enhanced Durability: The hardness of pre-hardened steel provides excellent resistance to wear, making it ideal for applications that involve high friction or abrasive conditions.
-
Machinability: Pre-hardened steels are softer than fully hardened steels, which makes them easier to machine. This allows for intricate designs and precise tolerances to be achieved during the manufacturing process.
-
Cost-Effectiveness: Pre-hardened steel is often more cost-effective than fully hardened steels because it reduces the need for additional heat treatment processes, which can be expensive and time-consuming.
Disadvantages:
-
Lower Toughness: Although pre-hardened steel is tough enough for many applications, it may not be suitable for applications requiring extremely high levels of toughness, such as in heavy impact or shock loading conditions. In such cases, further heat treatment may be necessary.
-
Limited Customization: Pre-hardened steels are available in a range of hardness levels, but the customization options may be more limited compared to fully hardened steels that can undergo further treatments to achieve specific mechanical properties.
-
Cost for Special Grades: While pre-hardened steels are generally cost-effective, the use of certain alloying elements or special grades for specific applications can increase the cost of production.
Conclusion
Pre-hardened steel is an essential material in modern manufacturing, offering a unique combination of hardness, machinability, and strength. Its ability to retain hardness while maintaining sufficient ductility for machining makes it a versatile material choice across industries ranging from automotive and aerospace to medical and tooling applications. By eliminating the need for additional heat treatments, pre-hardened steel enhances manufacturing efficiency and reduces costs, making it a valuable material in both high-volume and precision manufacturing environments. While it may not be suitable for every application, the material offers significant benefits for parts requiring wear resistance, strength, and ease of machining.
Reprint Statement: If there are no special instructions, all articles on this site are original. Please indicate the source for reprinting:https://www.cncmachiningptj.com/,thanks!
PTJ® provides a full range of Custom Precision cnc machining china services.ISO 9001:2015 &AS-9100 certified. 3, 4 and 5-axis rapid precision CNC machining services including milling, turning to customer specifications,Capable of metal & plastic machined parts with +/-0.005 mm tolerance.Secondary services include CNC and conventional grinding, drilling,die casting,sheet metal and stamping.Providing prototypes, full production runs, technical support and full inspection.Serves the automotive, aerospace, mold&fixture,led lighting,medical,bicycle, and consumer electronics industries. On-time delivery.Tell us a little about your project's budget and expected delivery time. We will strategize with you to provide the most cost-effective services to help you reach your target,Welcome to Contact us ( sales@pintejin.com ) directly for your new project.
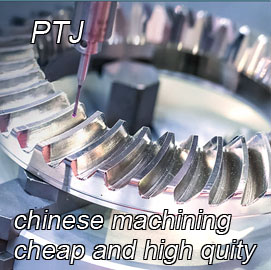
- 5 Axis Machining
- Cnc Milling
- Cnc Turning
- Machining Industries
- Machining Process
- Surface Treatment
- Metal Machining
- Plastic Machining
- Powder Metallurgy Mold
- Die Casting
- Parts Gallery
- Auto Metal Parts
- Machinery Parts
- LED Heatsink
- Building Parts
- Mobile Parts
- Medical Parts
- Electronic Parts
- Tailored Machining
- Bicycle Parts
- Aluminum Machining
- Titanium Machining
- Stainless Steel Machining
- Copper Machining
- Brass Machining
- Super Alloy Machining
- Peek Machining
- UHMW Machining
- Unilate Machining
- PA6 Machining
- PPS Machining
- Teflon Machining
- Inconel Machining
- Tool Steel Machining
- More Material