What is Pre-Hardened Steel?
Pre-hardened steel refers to a category of steels that have been heat-treated to a specific hardness level prior to their final use in various applications. This steel is particularly notable for its ability to retain hardness and strength while still maintaining sufficient ductility to facilitate machining and fabrication. Unlike fully hardened steels, which often require additional heat treatments or surface treatments post-fabrication, pre-hardened steels are ready for direct use once processed, making them a valuable material for numerous industrial applications.
Properties of Pre-Hardened Steel
The most defining characteristic of pre-hardened steel is its hardness, achieved through a controlled heat treatment process. Typically, the steel is subjected to quenching and tempering processes, resulting in a hardness level between 30 and 45 HRC (Hardness Rockwell C). This hardness level allows the steel to maintain a good balance between strength, toughness, and machinability. The specific hardness can be adjusted based on the alloy composition, tempering temperature, and cooling rates during processing.
The hardness of pre-hardened steel ensures that it offers excellent wear resistance, which makes it an ideal choice for manufacturing components that are exposed to high friction, such as molds, dies, and certain machine parts. However, the material retains some degree of toughness and flexibility, which is important for applications that require resilience against cracking or failure under stress.
Another key property of pre-hardened steel is its good machinability, particularly when compared to fully hardened steels. The material is harder than unhardened steels but still soft enough to allow for machining processes such as turning, milling, drilling, and grinding. This makes pre-hardened steel an attractive choice for parts that require precise machining but cannot undergo further heat treatment due to design constraints or cost limitations.
Pre-hardened steels are also characterized by good dimensional stability, which means that they maintain their shape and size under conditions of heat, stress, and strain. This is particularly beneficial in applications where high precision and repeatability are required.
Composition of Pre-Hardened Steel
The composition of pre-hardened steel can vary depending on the specific requirements of the intended application. However, pre-hardened steels generally contain a combination of elements that provide the desired mechanical properties. The alloying elements typically include carbon, chromium, nickel, molybdenum, and sometimes vanadium or tungsten.
-
Carbon: Carbon is a primary alloying element in steel, and its content plays a crucial role in determining the hardness and strength of the steel. In pre-hardened steels, carbon content is typically in the range of 0.30% to 0.60%. Higher carbon content increases hardness but may reduce the material’s ductility and weldability.
-
Chromium: Chromium is added to improve the corrosion resistance and hardenability of the steel. It also enhances the steel's strength and wear resistance, making it an important element in pre-hardened steels used for applications in harsh environments.
-
Nickel: Nickel is known for improving the toughness and impact strength of steel. It also enhances the material's ability to resist corrosion and oxidation, which makes it an important alloying element in pre-hardened steels used in industrial equipment that is exposed to moisture or other corrosive elements.
-
Molybdenum: Molybdenum enhances the steel’s resistance to wear and high-temperature strength. It is particularly useful in pre-hardened steels used for tooling and machinery components that must maintain their strength at elevated temperatures.
-
Vanadium and Tungsten: Vanadium and tungsten are sometimes added to improve the steel’s resistance to abrasion, wear, and fatigue. These elements also enhance the material's overall strength and hardness.
The specific combination of these alloying elements determines the mechanical properties, including hardness, strength, and wear resistance, of the pre-hardened steel. For example, tool steels and die steels, which fall under the category of pre-hardened steels, may have higher amounts of carbon, chromium, and vanadium to meet the demanding requirements of mold-making and metal forming.
Heat Treatment Process for Pre-Hardened Steel
Pre-hardened steel undergoes a controlled heat treatment process to achieve its characteristic hardness. The heat treatment generally involves the following steps:
-
Heating: The steel is heated to a temperature above its critical point, typically between 800°C and 900°C, depending on the alloy composition. This heat treatment process is designed to transform the microstructure of the steel into austenite, a high-temperature phase of steel.
-
Quenching: The steel is then rapidly cooled, usually by immersion in water or oil, to transform the austenite into martensite, a hard, brittle phase of steel. This rapid cooling process increases the hardness of the material but also makes it more brittle.
-
Tempering: To reduce the brittleness and improve the toughness of the steel, it undergoes a tempering process. This involves reheating the steel to a lower temperature, typically between 200°C and 600°C, and then allowing it to cool slowly. The tempering process reduces internal stresses and refines the steel’s microstructure, resulting in a more balanced set of mechanical properties.
The hardness of pre-hardened steel can be controlled by adjusting the parameters of the heat treatment process, including the quenching medium, tempering temperature, and time. By tailoring these factors, manufacturers can produce pre-hardened steels with varying degrees of hardness and toughness to suit specific application requirements.
Applications of Pre-Hardened Steel
Pre-hardened steels are used in a wide range of applications where a balance of hardness, strength, machinability, and toughness is required. Some of the key industries and applications include:
-
Tooling and Die Manufacturing: Pre-hardened steels are commonly used for manufacturing molds, dies, and punches, particularly in injection molding, die-casting, and stamping operations. The hardness of pre-hardened steels provides excellent wear resistance, while their machinability allows for intricate designs and precise tolerances.
-
Automotive Industry: Pre-hardened steels are widely used in the production of automotive components, including gears, shafts, and other machine parts. These components are subjected to high stresses and wear, making the hardness and durability of pre-hardened steel an ideal choice.
-
Aerospace and Defense: In the aerospace and defense industries, pre-hardened steels are used for manufacturing structural components, fasteners, and engine parts that must withstand extreme temperatures and mechanical stresses. The excellent strength-to-weight ratio of pre-hardened steels makes them particularly valuable for these demanding applications.
-
Heavy Equipment: Pre-hardened steels are used in the production of parts for heavy machinery, such as bulldozers, excavators, and mining equipment. These parts often need to resist wear and abrasion from harsh working conditions, and pre-hardened steels offer the right combination of properties for such applications.
-
Medical Devices: In the medical industry, pre-hardened steels are used for the manufacture of surgical instruments, dental tools, and implants. These components require high precision, strength, and wear resistance, which makes pre-hardened steel an ideal material choice.
-
Manufacturing and Processing Equipment: Pre-hardened steels are used in the construction of various manufacturing and processing equipment, such as presses, conveyors, and cutters. These steels can withstand wear and tear while maintaining their functionality over long periods of operation.
The versatility of pre-hardened steel makes it suitable for any application that requires a material with a high level of hardness and wear resistance, but without the need for extensive post-fabrication heat treatments or surface treatments.
Advantages and Disadvantages of Pre-Hardened Steel
Advantages:
-
Improved Efficiency: One of the major advantages of pre-hardened steel is that it eliminates the need for additional heat treatments after the part is fabricated. This can significantly reduce production time and costs, especially for high-volume manufacturing processes.
-
Enhanced Durability: The hardness of pre-hardened steel provides excellent resistance to wear, making it ideal for applications that involve high friction or abrasive conditions.
-
Machinability: Pre-hardened steels are softer than fully hardened steels, which makes them easier to machine. This allows for intricate designs and precise tolerances to be achieved during the manufacturing process.
-
Cost-Effectiveness: Pre-hardened steel is often more cost-effective than fully hardened steels because it reduces the need for additional heat treatment processes, which can be expensive and time-consuming.
Disadvantages:
-
Lower Toughness: Although pre-hardened steel is tough enough for many applications, it may not be suitable for applications requiring extremely high levels of toughness, such as in heavy impact or shock loading conditions. In such cases, further heat treatment may be necessary.
-
Limited Customization: Pre-hardened steels are available in a range of hardness levels, but the customization options may be more limited compared to fully hardened steels that can undergo further treatments to achieve specific mechanical properties.
-
Cost for Special Grades: While pre-hardened steels are generally cost-effective, the use of certain alloying elements or special grades for specific applications can increase the cost of production.
Conclusion
Pre-hardened steel is an essential material in modern manufacturing, offering a unique combination of hardness, machinability, and strength. Its ability to retain hardness while maintaining sufficient ductility for machining makes it a versatile material choice across industries ranging from automotive and aerospace to medical and tooling applications. By eliminating the need for additional heat treatments, pre-hardened steel enhances manufacturing efficiency and reduces costs, making it a valuable material in both high-volume and precision manufacturing environments. While it may not be suitable for every application, the material offers significant benefits for parts requiring wear resistance, strength, and ease of machining.
Reprint Statement: If there are no special instructions, all articles on this site are original. Please indicate the source for reprinting:https://www.cncmachiningptj.com/,thanks!
PTJ® provides a full range of Custom Precision cnc machining china services.ISO 9001:2015 &AS-9100 certified. 3, 4 and 5-axis rapid precision CNC machining services including milling, turning to customer specifications,Capable of metal & plastic machined parts with +/-0.005 mm tolerance.Secondary services include CNC and conventional grinding, drilling,die casting,sheet metal and stamping.Providing prototypes, full production runs, technical support and full inspection.Serves the automotive, aerospace, mold&fixture,led lighting,medical,bicycle, and consumer electronics industries. On-time delivery.Tell us a little about your project's budget and expected delivery time. We will strategize with you to provide the most cost-effective services to help you reach your target,Welcome to Contact us ( sales@pintejin.com ) directly for your new project.
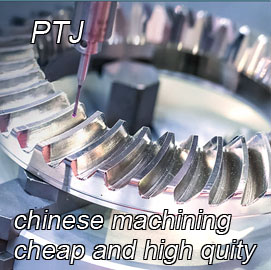
- 5 Axis Machining
- Cnc Milling
- Cnc Turning
- Machining Industries
- Machining Process
- Surface Treatment
- Metal Machining
- Plastic Machining
- Powder Metallurgy Mold
- Die Casting
- Parts Gallery
- Auto Metal Parts
- Machinery Parts
- LED Heatsink
- Building Parts
- Mobile Parts
- Medical Parts
- Electronic Parts
- Tailored Machining
- Bicycle Parts
- Aluminum Machining
- Titanium Machining
- Stainless Steel Machining
- Copper Machining
- Brass Machining
- Super Alloy Machining
- Peek Machining
- UHMW Machining
- Unilate Machining
- PA6 Machining
- PPS Machining
- Teflon Machining
- Inconel Machining
- Tool Steel Machining
- More Material