Stainless Steel Vacuum Seal Processing Flow
Vacuum sealing technology plays a pivotal role in various industries, particularly in packaging, preservation, and product protection. Stainless steel, known for its durability, resistance to corrosion, and aesthetic appeal, is often the material of choice for vacuum seal applications, particularly where hygiene, strength, and long-term reliability are paramount. The process of creating stainless steel vacuum seals involves a series of sophisticated steps to ensure that the seal is airtight, tamper-resistant, and capable of maintaining the integrity of the contained product for extended periods. This article explores the detailed processing flow for stainless steel vacuum seals, encompassing material selection, manufacturing techniques, sealing technologies, quality control, and applications across different industries.
Material Selection
The selection of stainless steel for vacuum sealing is a critical factor in the process, as it dictates the performance and longevity of the final product. Stainless steel is preferred for vacuum sealing due to its excellent resistance to corrosion, heat, and chemicals, making it ideal for applications in environments where cleanliness and longevity are critical. The most commonly used grades of stainless steel for vacuum seals are 304 and 316, both of which offer superior resistance to oxidation and corrosion.
Grade 304 stainless steel is typically used in food and beverage packaging, while Grade 316 is often employed in more specialized applications, such as in pharmaceutical, chemical processing, or medical industries, where resistance to a wider range of corrosive substances is required. Both materials are highly malleable, allowing them to be easily formed into the required shape and size without compromising their integrity.
Manufacturing Process
1. Metal Fabrication
The first step in the production of stainless steel vacuum seals is the fabrication of the metal components. This process generally involves cutting, bending, and shaping stainless steel sheets or coils into the required dimensions. Cutting is typically carried out using a variety of methods, including laser cutting, water jet cutting, and shearing, depending on the thickness and complexity of the material. Laser cutting is often preferred for its precision and ability to handle intricate designs, while water jet cutting is more commonly used for thicker materials.
Once the metal is cut, it is bent and shaped into the desired configuration using press brakes or other specialized bending equipment. The use of high-precision machinery ensures that the resulting components will meet the stringent tolerances required for vacuum sealing.
2. Surface Preparation
Surface preparation is a crucial step in stainless steel vacuum seal processing. Stainless steel, although resistant to corrosion, can still develop surface contaminants that may interfere with the sealing process. As such, the stainless steel components undergo a series of cleaning procedures to remove oil, grease, and any other foreign particles that may have accumulated during fabrication.
Methods such as ultrasonic cleaning, acid pickling, and abrasive blasting are commonly used to achieve the necessary level of cleanliness. Ultrasonic cleaning involves immersing the stainless steel in a cleaning solution that is agitated by ultrasonic waves, effectively removing microscopic particles from the surface. Acid pickling is another popular method, where the stainless steel is treated with a mild acid solution to remove oxides and other impurities. Abrasive blasting is used to achieve a smooth, uniform surface finish, ensuring that the stainless steel will bond effectively during the sealing process.
3. Forming and Molding
Once the stainless steel has been cleaned and prepared, it undergoes forming and molding to create the necessary components for the vacuum seal. This typically involves deep drawing or stamping processes, where a metal sheet is drawn into a mold to create the desired shape. In the case of vacuum seals, the components may include lids, flanges, or base containers, all of which need to be precisely formed to ensure an effective seal.
Deep drawing involves the use of a punch and die to stretch the metal sheet into the required shape. This process requires high precision, as any deformation or imperfection in the metal can result in leaks or failure of the vacuum seal. After the parts are formed, they are inspected for quality to ensure that they meet the design specifications.
4. Welding and Joining
Once the components are fabricated, the next step is welding and joining the stainless steel parts together. This is particularly important for creating airtight seals. Welding techniques such as TIG (Tungsten Inert Gas) welding or MIG (Metal Inert Gas) welding are commonly employed to join the metal components.
TIG welding is favored for its ability to produce high-quality, clean welds with minimal distortion, making it ideal for stainless steel vacuum seals. MIG welding, on the other hand, is typically used for thicker materials or in applications where speed is more critical than the aesthetic quality of the weld. During the welding process, it is crucial to maintain precise control over the heat to avoid any changes in the metal’s properties that could affect the integrity of the seal.
5. Vacuum Seal Formation
The core of the process is the actual vacuum sealing, which involves creating an airtight seal around the container or component. This is typically achieved using a variety of sealing methods, including heat sealing, ultrasonic welding, or vacuum-forming.
In heat sealing, the stainless steel parts are heated to a specific temperature, at which point they are pressed together under controlled pressure to form a strong, uniform bond. The heat causes the metal to soften and fuse together, forming a hermetically sealed junction. This method is commonly used for creating seals in vacuum packaging applications, where the need for airtightness is paramount.
Ultrasonic welding, on the other hand, uses high-frequency sound waves to generate heat at the interface of the materials being joined. The intense vibration causes the stainless steel to melt and bond, creating a clean and strong seal. This method is particularly effective for thin-walled stainless steel components, where traditional welding methods may not be suitable.
Vacuum-forming is used when the stainless steel needs to be molded into a specific shape and then sealed under vacuum. This process involves heating the material until it becomes pliable and then forming it over a mold. Once the desired shape is achieved, the air is evacuated, and the seal is formed by cooling the metal under pressure.
Quality Control and Testing
Quality control is a vital part of the stainless steel vacuum seal processing flow. Given the critical nature of the seal, especially in applications like food packaging or pharmaceutical containers, ensuring the airtightness and durability of the seal is paramount. Various testing methods are employed to verify the quality of the vacuum seals.
1. Leak Testing
Leak testing is one of the most common methods used to assess the effectiveness of the vacuum seal. This can be carried out using techniques such as pressure decay testing, helium leak testing, or bubble testing. In pressure decay testing, the sealed container is pressurized, and any drop in pressure indicates a leak. Helium leak testing involves introducing helium into the sealed container and using a mass spectrometer to detect any escaping gas, while bubble testing involves submerging the sealed container in water and observing the formation of bubbles to detect leaks.
2. Visual and Dimensional Inspection
In addition to leak testing, stainless steel vacuum seals are subject to visual and dimensional inspections. Visual inspections are carried out to detect any surface defects, such as cracks, scratches, or discoloration, which may compromise the integrity of the seal. Dimensional inspection ensures that the parts meet the required specifications in terms of size, shape, and tolerance. Precision measuring instruments such as micrometers, calipers, and coordinate measuring machines (CMMs) are used to verify the dimensions of the components.
3. Pressure and Strength Testing
Pressure testing is used to simulate the conditions the vacuum seal will experience in its intended application. The sealed components are subjected to different levels of pressure to ensure they can withstand the external forces without compromising the vacuum seal. Similarly, strength testing ensures that the stainless steel components will maintain their structural integrity under stress.
Applications of Stainless Steel Vacuum Seals
Stainless steel vacuum seals are used in a wide variety of applications across many industries. Some of the most common applications include:
- Food Packaging: Stainless steel vacuum seals are commonly used in the food industry for packaging perishable goods, as they extend the shelf life of the product by preventing oxidation and contamination.
- Pharmaceuticals: In the pharmaceutical industry, stainless steel vacuum seals are used to ensure the safety and sterility of products, such as vials, syringes, and medical instruments.
- Electronics: Stainless steel vacuum seals are employed in the electronics industry to protect sensitive components from moisture and dust.
- Automotive and Aerospace: In these industries, stainless steel vacuum seals are used to protect components from contamination and to maintain precise conditions in sensitive equipment.
Conclusion
The stainless steel vacuum seal processing flow is a complex, multi-step procedure that requires precision, attention to detail, and advanced technology to ensure the production of high-quality, airtight seals. The process begins with material selection and fabrication, followed by cleaning, forming, welding, and sealing. Rigorous quality control and testing procedures ensure that the final product meets the stringent requirements of industries such as food packaging, pharmaceuticals, and electronics. As technology continues to evolve, the demand for stainless steel vacuum seals will likely increase, driving further advancements in manufacturing processes and materials.
Reprint Statement: If there are no special instructions, all articles on this site are original. Please indicate the source for reprinting:https://www.cncmachiningptj.com/,thanks!
3, 4 and 5-axis precision CNC machining services for aluminum machining, beryllium, carbon steel, magnesium, titanium machining, Inconel, platinum, superalloy, acetal, polycarbonate, fiberglass, graphite and wood. Capable of machining parts up to 98 in. turning dia. and +/-0.001 in. straightness tolerance. Processes include milling, turning, drilling, boring, threading, tapping, forming, knurling, counterboring, countersinking, reaming and laser cutting. Secondary services such as assembly, centerless grinding, heat treating, plating and welding. Prototype and low to high volume production offered with maximum 50,000 units. Suitable for fluid power, pneumatics, hydraulics and valve applications. Serves the aerospace, aircraft, military, medical and defense industries.PTJ will strategize with you to provide the most cost-effective services to help you reach your target,Welcome to Contact us ( sales@pintejin.com ) directly for your new project.
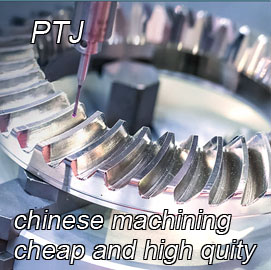
- 5 Axis Machining
- Cnc Milling
- Cnc Turning
- Machining Industries
- Machining Process
- Surface Treatment
- Metal Machining
- Plastic Machining
- Powder Metallurgy Mold
- Die Casting
- Parts Gallery
- Auto Metal Parts
- Machinery Parts
- LED Heatsink
- Building Parts
- Mobile Parts
- Medical Parts
- Electronic Parts
- Tailored Machining
- Bicycle Parts
- Aluminum Machining
- Titanium Machining
- Stainless Steel Machining
- Copper Machining
- Brass Machining
- Super Alloy Machining
- Peek Machining
- UHMW Machining
- Unilate Machining
- PA6 Machining
- PPS Machining
- Teflon Machining
- Inconel Machining
- Tool Steel Machining
- More Material