Aluminum-Based Castings in the Automotive Sector
Aluminum-based castings are critical components in the automotive industry, playing a vital role in the production of vehicles across various categories, including passenger cars, trucks, and electric vehicles (EVs). As a lightweight, corrosion-resistant, and cost-effective material, aluminum has been widely adopted for various automotive components, contributing to vehicle performance, safety, and fuel efficiency. This article aims to provide an in-depth exploration of aluminum castings in the automotive sector, highlighting their benefits, manufacturing processes, applications, challenges, and emerging trends.
Introduction to Aluminum Casting in Automotive
Aluminum casting refers to the process of pouring molten aluminum into molds to create a variety of parts and components used in various industries. In the automotive sector, aluminum castings are widely employed to fabricate engine blocks, cylinder heads, transmission cases, wheels, and other structural components. The adoption of aluminum as a primary material for casting has significantly increased due to its excellent properties, such as light weight, high strength-to-weight ratio, thermal conductivity, and resistance to corrosion.
The automotive industry's demand for lightweight materials is primarily driven by the need to improve fuel efficiency, reduce emissions, and meet stricter environmental regulations. As a result, aluminum castings are increasingly replacing traditional steel and iron castings in many critical applications. Furthermore, aluminum's ability to be recycled without significant loss of quality makes it an attractive option for sustainable manufacturing practices.
Properties of Aluminum for Casting
Aluminum is a non-ferrous metal with several characteristics that make it ideal for casting in automotive applications. These properties include:
-
Lightweight: Aluminum is approximately one-third the weight of steel, making it an excellent material for reducing the overall weight of vehicles, which in turn enhances fuel efficiency and reduces CO2 emissions. This property is particularly crucial in the context of electric vehicles (EVs), where weight reduction is essential to maximize battery efficiency and driving range.
-
Corrosion Resistance: Aluminum naturally forms a protective oxide layer when exposed to air, which helps prevent further oxidation and corrosion. This property is highly beneficial for automotive components exposed to harsh environments, such as engine parts and undercarriage components, where corrosion resistance is essential for longevity and performance.
-
Strength-to-Weight Ratio: Aluminum possesses a high strength-to-weight ratio, meaning that it can withstand significant stresses while maintaining a lightweight structure. This characteristic is crucial for automotive applications where both durability and weight reduction are required.
-
Thermal Conductivity: Aluminum has excellent thermal conductivity, making it suitable for components that must dissipate heat, such as engine blocks and cylinder heads. This property helps prevent overheating and improves the overall performance and efficiency of the engine.
-
Recyclability: Aluminum is highly recyclable without losing its material properties. This makes it an environmentally sustainable option, as recycled aluminum requires significantly less energy to process than primary aluminum, reducing the environmental impact of aluminum production.
-
Formability: Aluminum can be easily cast, forged, and machined into complex shapes, which is advantageous in the production of intricate automotive components. Its ability to be formed into thin-walled parts allows for lightweight designs without sacrificing structural integrity.
Types of Aluminum Casting Processes
There are several aluminum casting processes used in the automotive industry, each suited to different types of parts, materials, and production volumes. The main casting methods include:
1. Die Casting
Die casting is one of the most widely used methods for producing aluminum castings in the automotive sector. It involves injecting molten aluminum under high pressure into a steel mold (die). This process is ideal for producing high-volume, precision parts with intricate designs, such as engine blocks, cylinder heads, and transmission housings. Die casting offers several advantages, including high dimensional accuracy, smooth surface finishes, and the ability to produce complex geometries.
Die casting is commonly used for components that require high mechanical strength, durability, and thermal conductivity. It is particularly suitable for producing components in large quantities, such as automotive engine parts, transmission cases, and wheels.
2. Sand Casting
Sand casting is another widely used aluminum casting process in the automotive sector. It involves creating a mold from a mixture of sand, clay, and water, into which molten aluminum is poured. Sand casting is highly versatile and can be used for both small and large parts, including engine blocks, transmission housings, and chassis components. While it is not as precise as die casting, sand casting is cost-effective for low to medium-volume production and is particularly useful for large or complex components that cannot be easily produced using other methods.
One of the main advantages of sand casting is its ability to produce parts with large sections and intricate shapes. However, the surface finish and dimensional tolerance may not be as high as those produced by die casting, requiring additional machining or finishing processes.
3. Permanent Mold Casting
Permanent mold casting involves pouring molten aluminum into a reusable metal mold. The mold is typically made from steel, cast iron, or other durable materials. This process is suitable for producing parts that require better dimensional accuracy and surface finish compared to sand casting but are not as intricate as those produced by die casting. Components such as engine blocks, cylinder heads, and structural automotive parts are often produced using permanent mold casting.
Permanent mold casting offers better control over the solidification process, resulting in improved mechanical properties, especially in terms of strength and durability. However, it is generally more expensive than sand casting due to the use of reusable molds and the need for more precise control of the pouring process.
4. Investment Casting (Lost Wax Casting)
Investment casting, also known as lost-wax casting, is a process in which a wax pattern of the part is created and then coated with a ceramic shell. The wax is then melted away, leaving a hollow mold into which molten aluminum is poured. This process is highly accurate and is used for producing complex, high-precision components such as automotive sensors, turbochargers, and suspension parts.
Investment casting is particularly advantageous when producing parts with complex geometries, thin walls, and tight tolerances. However, it is more expensive and time-consuming than other casting methods, making it less suitable for high-volume production.
5. Gravity Die Casting
Gravity die casting, also known as chill casting, involves pouring molten aluminum into a mold under the influence of gravity. Unlike die casting, which uses pressure to inject the molten metal into the mold, gravity die casting relies on the natural force of gravity to fill the mold cavity. This process is used for producing smaller, less complex parts, such as transmission cases, differential housings, and small engine components.
Gravity die casting offers good dimensional accuracy, minimal porosity, and a smooth surface finish. It is also relatively inexpensive compared to other casting methods, making it suitable for medium to low production volumes.
6. Low-Pressure Die Casting
Low-pressure die casting is similar to traditional die casting but uses lower pressure to inject the molten aluminum into the mold. This process is particularly suitable for producing thin-walled components with high mechanical strength and dimensional accuracy. Low-pressure die casting is commonly used in the automotive industry for parts such as engine blocks, cylinder heads, and other structural components that require both high strength and lightweight characteristics.
Applications of Aluminum Castings in Automotive
Aluminum castings are used in a wide variety of automotive applications due to their unique properties. Some of the most common applications include:
1. Engine Blocks and Cylinder Heads
Engine blocks and cylinder heads are some of the most critical components in internal combustion engines. Aluminum is widely used in the casting of engine blocks and cylinder heads due to its excellent thermal conductivity, lightweight, and corrosion resistance. The use of aluminum in these components helps reduce the overall weight of the engine, improving fuel efficiency and performance.
Aluminum engine blocks offer better heat dissipation, which is crucial for preventing overheating and ensuring the engine operates efficiently. The use of aluminum also allows for the creation of thinner, lighter parts, contributing to weight reduction without compromising strength and durability.
2. Transmission Cases and Housings
Transmission cases and housings are another key application of aluminum castings in the automotive sector. Aluminum transmission cases offer several advantages, including reduced weight, improved thermal conductivity, and increased resistance to corrosion. These properties help enhance the performance and durability of the transmission system, as well as improve fuel efficiency by reducing the overall weight of the vehicle.
3. Wheels
Aluminum cast wheels are commonly used in passenger vehicles, trucks, and high-performance cars. Aluminum wheels are lighter than steel wheels, which contributes to overall weight reduction and improved fuel efficiency. Additionally, aluminum wheels provide better heat dissipation, which can improve brake performance and reduce the risk of overheating.
The lightweight nature of aluminum wheels also helps improve handling and ride quality, making them an ideal choice for performance vehicles. Aluminum wheels can be cast using various methods, including die casting and gravity die casting, depending on the desired shape, strength, and surface finish.
4. Suspension Components
Suspension components such as control arms, strut mounts, and shock absorber housings are often made from aluminum castings. Aluminum's lightweight and high-strength properties make it an ideal material for these components, which must withstand high loads and stresses while contributing to the overall weight reduction of the vehicle.
By using aluminum for suspension components, automakers can improve fuel efficiency, handling, and ride comfort without sacrificing durability or performance.
5. Structural and Body Components
Aluminum castings are increasingly being used in the production of structural and body components, including bumpers, crash beams, and other safety-related parts. These components require a combination of strength, impact resistance, and lightweight properties, all of which are offered by aluminum.
In the case of electric vehicles, aluminum castings are essential for producing lightweight, high-strength structures that help offset the weight of the battery packs. This contributes to the overall efficiency and driving range of the vehicle.
Reprint Statement: If there are no special instructions, all articles on this site are original. Please indicate the source for reprinting:https://www.cncmachiningptj.com/,thanks!
PTJ® provides a full range of Custom Precision cnc machining china services.ISO 9001:2015 &AS-9100 certified. 3, 4 and 5-axis rapid precision CNC machining services including milling, turning to customer specifications,Capable of metal & plastic machined parts with +/-0.005 mm tolerance.Secondary services include CNC and conventional grinding, drilling,die casting,sheet metal and stamping.Providing prototypes, full production runs, technical support and full inspection.Serves the automotive, aerospace, mold&fixture,led lighting,medical,bicycle, and consumer electronics industries. On-time delivery.Tell us a little about your project's budget and expected delivery time. We will strategize with you to provide the most cost-effective services to help you reach your target,Welcome to Contact us ( sales@pintejin.com ) directly for your new project.
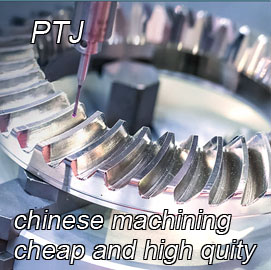
- 5 Axis Machining
- Cnc Milling
- Cnc Turning
- Machining Industries
- Machining Process
- Surface Treatment
- Metal Machining
- Plastic Machining
- Powder Metallurgy Mold
- Die Casting
- Parts Gallery
- Auto Metal Parts
- Machinery Parts
- LED Heatsink
- Building Parts
- Mobile Parts
- Medical Parts
- Electronic Parts
- Tailored Machining
- Bicycle Parts
- Aluminum Machining
- Titanium Machining
- Stainless Steel Machining
- Copper Machining
- Brass Machining
- Super Alloy Machining
- Peek Machining
- UHMW Machining
- Unilate Machining
- PA6 Machining
- PPS Machining
- Teflon Machining
- Inconel Machining
- Tool Steel Machining
- More Material