Dispersion (Composite) Plating of Precision Parts
Dispersion plating, also known as composite plating, is a specialized surface finishing technique that integrates fine particles into a metallic coating matrix to enhance the functional properties of precision parts. This process is widely utilized in industries such as aerospace, automotive, electronics, and medical devices, where advanced material characteristics such as wear resistance, lubrication, corrosion protection, and specific electrical properties are essential.
Definition and Basic Principles
Dispersion plating combines electroplating or electroless plating with the co-deposition of micron- or nano-sized particles into a metallic layer. These particles, often made of ceramics, polymers, or other engineered materials, are suspended in the plating solution. During the plating process, the particles are embedded into the deposited metal layer, creating a composite material with superior performance characteristics compared to the base metal coating.
The effectiveness of dispersion plating relies on several factors, including particle concentration, particle size distribution, plating bath composition, agitation mechanisms, and plating parameters. By optimizing these variables, manufacturers can produce coatings tailored to specific functional requirements.
Historical Development
The concept of embedding particles into metallic coatings dates back to the early 20th century. Initial efforts focused on enhancing the wear resistance of coatings by incorporating hard particles such as silicon carbide (SiC) and aluminum oxide (Al₂O₃). Over time, advancements in chemical engineering and material science expanded the range of possible particles and plating methods. The development of electroless plating techniques in the mid-20th century marked a significant milestone, enabling more uniform particle distribution and coating thickness.
The increasing demand for high-performance materials in precision engineering applications further accelerated research and development in dispersion plating. Modern techniques now allow for precise control over particle inclusion, enabling the production of coatings with multifunctional properties.
Commonly Used Particles and Coating Materials
Dispersion plating involves a wide array of particles and base metals, each chosen for their unique properties and compatibility with specific applications:
-
Particles:
- Hard particles: Silicon carbide (SiC), diamond, tungsten carbide (WC), and aluminum oxide (Al₂O₃) are used to improve wear resistance.
- Lubricating particles: Polytetrafluoroethylene (PTFE) and graphite provide self-lubricating properties for reduced friction.
- Corrosion inhibitors: Zinc oxide (ZnO) and cerium oxide (CeO₂) are included to enhance corrosion resistance.
- Functional fillers: Conductive particles like silver (Ag) and gold (Au) are used for electrical applications.
-
Metal Matrix Materials:
- Nickel: A versatile choice for its corrosion resistance and compatibility with various particles.
- Copper: Valued for its electrical and thermal conductivity.
- Gold and Silver: Used in high-value applications requiring exceptional electrical conductivity or aesthetic appeal.
- Cobalt: Preferred for high-temperature stability and wear resistance.
Plating Techniques
Dispersion plating can be achieved through several methods, including electroplating and electroless plating. Each method offers distinct advantages and is selected based on the desired coating characteristics.
Electroplating
Electroplating involves using an electric current to deposit a metallic layer onto a substrate. In dispersion electroplating, particles are suspended in the electrolyte solution and incorporated into the coating as the metal ions are reduced onto the substrate. Key parameters such as current density, agitation, and particle concentration must be carefully controlled to ensure uniform particle distribution.
Electroless Plating
Electroless plating is a chemical process that deposits metal onto a substrate without the use of an external electrical current. This method offers superior uniformity, especially for complex geometries, and allows for better particle incorporation due to the consistent chemical reactions across the surface. Nickel-phosphorus and nickel-boron matrices are common in electroless dispersion plating.
Other Techniques
In addition to traditional methods, advanced techniques such as pulse plating and jet plating have been developed to improve particle embedding and coating quality. These methods use intermittent or high-velocity deposition to achieve better control over the microstructure of the composite coating.
Advantages of Dispersion Plating
Dispersion plating offers numerous benefits, making it a preferred choice for enhancing the performance of precision parts:
- Enhanced Wear Resistance: The inclusion of hard particles significantly increases the coating's resistance to abrasion and mechanical wear.
- Improved Lubrication: Embedded lubricating particles reduce friction, extending the lifespan of moving components.
- Corrosion Protection: Composite coatings provide superior resistance to corrosion in harsh environments, prolonging the service life of parts.
- Tailored Properties: By selecting appropriate particles, manufacturers can customize coatings for specific applications, such as electrical conductivity, magnetic properties, or thermal stability.
- Uniform Coatings: Electroless dispersion plating ensures consistent coating thickness, even on complex shapes.
Applications in Precision Engineering
Dispersion plating is employed across various industries to address the stringent performance requirements of precision parts. Key applications include:
- Aerospace: Enhanced wear resistance and lubrication for turbine blades, bearings, and hydraulic components.
- Automotive: Corrosion-resistant and self-lubricating coatings for engine parts, pistons, and gears.
- Electronics: Improved conductivity and thermal management for connectors, circuit boards, and heat sinks.
- Medical Devices: Biocompatible and wear-resistant coatings for surgical instruments and implants.
- Oil and Gas: Protective coatings for drilling tools and equipment exposed to abrasive and corrosive environments.
Challenges and Limitations
While dispersion plating offers significant advantages, it also presents challenges:
- Particle Agglomeration: Ensuring uniform dispersion of particles in the plating solution is critical to achieving consistent coating quality.
- Cost: The process can be more expensive than conventional plating due to the complexity of the setup and the cost of specialized particles.
- Process Control: Precise control over plating parameters is required to avoid defects and achieve the desired properties.
Future Trends and Innovations
The field of dispersion plating continues to evolve, driven by advances in nanotechnology and material science. Emerging trends include:
- Nanoparticle Incorporation: The use of nanoparticles allows for coatings with enhanced mechanical, electrical, and thermal properties.
- Green Chemistry: Development of environmentally friendly plating solutions and processes to reduce the environmental impact.
- Additive Manufacturing Integration: Combining dispersion plating with 3D printing techniques to create multifunctional components.
Conclusion
Dispersion plating represents a powerful technique for enhancing the performance of precision parts across a wide range of industries. Its ability to integrate functional particles into metallic coatings enables the creation of materials with tailored properties, meeting the demands of modern engineering applications. As technological advancements continue, dispersion plating is poised to play an increasingly vital role in the development of high-performance materials.
Reprint Statement: If there are no special instructions, all articles on this site are original. Please indicate the source for reprinting:https://www.cncmachiningptj.com/,thanks!
PTJ® provides a full range of Custom Precision cnc machining china services.ISO 9001:2015 &AS-9100 certified. 3, 4 and 5-axis rapid precision CNC machining services including milling, turning to customer specifications,Capable of metal & plastic machined parts with +/-0.005 mm tolerance.Secondary services include CNC and conventional grinding, drilling,die casting,sheet metal and stamping.Providing prototypes, full production runs, technical support and full inspection.Serves the automotive, aerospace, mold&fixture,led lighting,medical,bicycle, and consumer electronics industries. On-time delivery.Tell us a little about your project's budget and expected delivery time. We will strategize with you to provide the most cost-effective services to help you reach your target,Welcome to Contact us ( sales@pintejin.com ) directly for your new project.
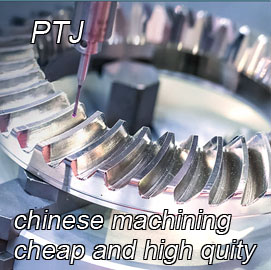
- 5 Axis Machining
- Cnc Milling
- Cnc Turning
- Machining Industries
- Machining Process
- Surface Treatment
- Metal Machining
- Plastic Machining
- Powder Metallurgy Mold
- Die Casting
- Parts Gallery
- Auto Metal Parts
- Machinery Parts
- LED Heatsink
- Building Parts
- Mobile Parts
- Medical Parts
- Electronic Parts
- Tailored Machining
- Bicycle Parts
- Aluminum Machining
- Titanium Machining
- Stainless Steel Machining
- Copper Machining
- Brass Machining
- Super Alloy Machining
- Peek Machining
- UHMW Machining
- Unilate Machining
- PA6 Machining
- PPS Machining
- Teflon Machining
- Inconel Machining
- Tool Steel Machining
- More Material