Automation of CNC (Computer Numerical Control) machining sites
The automation of CNC (Computer Numerical Control) machining sites represents a transformative shift in the manufacturing industry, enabling more efficient, precise, and cost-effective production processes. This article explores the concept of CNC machining automation, its key components, the technologies involved, and the significant impacts it has had on various industries. Through examining the evolution of CNC machining, the integration of automation systems, and the future potential of these technologies, this article aims to provide a comprehensive overview of the state of CNC machining automation.
Introduction to CNC Machining
CNC machining is a manufacturing process that utilizes computers to control machine tools such as lathes, mills, routers, and grinders. This process has revolutionized manufacturing, allowing for highly accurate and complex parts to be produced with minimal human intervention. The technology involves the use of a pre-programmed computer code (G-code), which dictates the movements of the machine tool. The precision, repeatability, and flexibility offered by CNC machining have made it indispensable in industries such as aerospace, automotive, electronics, and medical devices.
CNC machines are widely known for their ability to produce parts with very tight tolerances and repeatable quality. However, traditional CNC machining still requires human operators to monitor and manage machine operations. In recent years, there has been a growing push toward the automation of CNC machining sites to further enhance productivity, minimize errors, and reduce the dependency on skilled labor.
Automation in CNC Machining
The automation of CNC machining involves integrating robotic systems, advanced sensors, artificial intelligence (AI), machine learning (ML), and Internet of Things (IoT) technologies to optimize production. These systems can operate CNC machines autonomously, eliminating or reducing the need for human oversight. Automation in CNC machining has led to the development of fully automated machining cells, which can run continuously for extended periods, with minimal human interaction.
Robotic Integration
One of the most significant advancements in CNC machining automation is the integration of robotics. Robots are now used to load and unload parts from machines, transport raw materials, and handle finished components. This eliminates the need for human workers to perform repetitive tasks, allowing them to focus on more complex and value-added activities. The use of robots can also enhance safety by removing operators from potentially dangerous environments, such as around high-speed rotating machinery.
Automated loading and unloading systems are particularly beneficial in applications where high-volume production is required. For instance, in industries such as automotive manufacturing, where thousands of identical parts need to be produced daily, robotic systems can ensure a continuous, uninterrupted flow of work. These robotic systems are often paired with vision systems, which use cameras and sensors to inspect parts for quality and ensure proper placement before the machining process begins.
Advanced Sensors and Feedback Loops
To further enhance automation, CNC machining systems now incorporate advanced sensors and feedback loops that monitor the entire machining process in real-time. These sensors track parameters such as temperature, pressure, vibration, and tool wear, providing valuable data to optimize the machining process. For example, temperature sensors can monitor the heat generated during cutting operations, preventing overheating and tool failure.
Feedback loops allow the machine to adjust its operations based on sensor data, improving accuracy and reducing the likelihood of defects. For example, if a sensor detects that a tool is becoming dull, the system can automatically compensate by adjusting cutting parameters, or it can trigger an alert for the operator to replace the tool. This closed-loop feedback system ensures that machining operations run smoothly and consistently, even without constant human intervention.
Artificial Intelligence and Machine Learning
Artificial intelligence (AI) and machine learning (ML) are increasingly being used to enhance the automation of CNC machining. AI algorithms can analyze large amounts of data generated by CNC machines, identifying patterns and making decisions to optimize performance. For example, AI can predict when a tool will fail based on its wear patterns, scheduling maintenance or tool changes in advance to avoid costly downtime.
Machine learning models can be trained to recognize optimal machining parameters for specific tasks, adjusting cutting speeds, feeds, and tool paths to maximize efficiency and minimize wear. Over time, these AI systems learn from the data they collect, continuously improving their performance and adapting to changes in the manufacturing environment. The use of AI in CNC machining allows for dynamic optimization, where the machine’s performance is constantly fine-tuned based on real-time conditions.
Internet of Things (IoT) and Connectivity
The integration of IoT technology into CNC machining systems has brought about new levels of connectivity and data accessibility. IoT devices, including sensors and smart machines, enable CNC machines to communicate with each other and with central control systems. This connectivity facilitates the monitoring and management of multiple machines across a manufacturing floor from a remote location.
Manufacturers can use IoT platforms to gather data from various machines, analyze performance metrics, and identify inefficiencies. IoT technology also allows for predictive maintenance, where machine performance data is analyzed to predict when a component is likely to fail, enabling proactive repairs or part replacements. This reduces unexpected downtime and helps ensure that production schedules are met.
Cloud-based systems have also become an integral part of CNC machining automation, allowing for real-time data sharing, remote monitoring, and centralized control. Manufacturers can access detailed performance reports from anywhere, allowing them to make informed decisions about their operations.
Benefits of CNC Machining Automation
The automation of CNC machining provides numerous benefits to manufacturers, ranging from cost reductions to improved quality and productivity.
Increased Productivity
One of the primary advantages of automating CNC machining processes is increased productivity. Automated systems can operate around the clock, significantly extending the hours of operation and reducing downtime. This leads to higher throughput, as machines can continue machining parts during off-hours without the need for human operators to be present.
Furthermore, automation reduces the time required for part loading and unloading, as well as tool changes. Robotic systems can handle these tasks more quickly and efficiently than human workers, reducing cycle times and accelerating production. Automated systems also help eliminate bottlenecks caused by manual interventions, ensuring a smoother and more efficient workflow.
Enhanced Precision and Quality Control
CNC machines, by their nature, are highly accurate and repeatable. However, human error can still introduce inconsistencies in the machining process. By automating CNC machining, manufacturers can further reduce the potential for human error, ensuring that parts are produced with consistent precision.
Automation systems equipped with advanced sensors and vision systems can also perform real-time quality checks, ensuring that parts meet the required specifications. This continuous quality monitoring helps identify defects early in the process, preventing defective parts from progressing through the production line.
Cost Reduction
Although the initial investment in automation technology can be significant, the long-term cost savings are substantial. Automated CNC machining systems reduce labor costs by minimizing the need for operators to perform repetitive tasks. The ability to operate machines without human intervention also reduces the likelihood of mistakes caused by operator fatigue or oversight.
Additionally, automated systems improve resource utilization by optimizing machine and tool performance. With the ability to adjust cutting parameters in real-time based on sensor data, the system can reduce material waste and prolong tool life, further contributing to cost savings.
Greater Flexibility
Automated CNC machining systems can be easily reprogrammed to accommodate different part designs and production runs. This level of flexibility is especially beneficial in industries that require frequent changes to product designs or short production runs. Automated systems can quickly adapt to new part specifications, enabling manufacturers to meet changing customer demands without significant downtime or retooling costs.
Safety Improvements
Automation also plays a key role in improving workplace safety. By removing operators from direct contact with machine tools, automation reduces the risk of injury. Robotic systems can handle hazardous tasks, such as loading and unloading parts from high-speed machines or handling toxic materials, while human workers can focus on more strategic tasks.
Moreover, automated systems are designed with safety features, such as emergency stop mechanisms and protective barriers, to prevent accidents. Machine learning and AI systems can also analyze safety data in real-time, identifying potential hazards and alerting operators before an incident occurs.
Challenges of CNC Machining Automation
While the automation of CNC machining offers numerous advantages, it also presents certain challenges that need to be addressed for successful implementation.
High Initial Investment
The cost of implementing automated CNC machining systems can be prohibitively high for some manufacturers. This includes the cost of purchasing robots, sensors, AI systems, and IoT infrastructure. Additionally, companies may need to invest in specialized training for employees to operate and maintain the new systems. For small- and medium-sized enterprises (SMEs), the upfront costs of automation can be a significant barrier.
Integration with Existing Systems
Integrating automation into existing CNC machining sites can be a complex process. Many legacy machines and systems may not be compatible with newer automation technologies. Retrofitting older machines with sensors and robotic systems can require significant engineering work, which can be time-consuming and costly.
To overcome this challenge, manufacturers may need to implement phased automation, gradually upgrading their machines and systems over time. This allows for a smoother transition and reduces the risk of disrupting ongoing production processes.
Skills Gap and Workforce Transition
As CNC machining becomes more automated, there is a growing need for workers with specialized skills in robotics, AI, and machine learning. The shift towards automation may lead to a reduction in demand for traditional machinists and operators, requiring retraining and reskilling initiatives.
Companies must invest in workforce development programs to ensure that employees can adapt to the changing landscape of manufacturing. This includes offering training in robotics, data analysis, and machine programming, as well as fostering a culture of continuous learning to keep pace with technological advancements.
Future Trends in CNC Machining Automation
The future of CNC machining automation is shaped by ongoing advancements in robotics, AI, IoT, and machine learning. As these technologies continue to evolve, manufacturers can expect even greater levels of precision, efficiency, and flexibility.
Autonomous CNC Machining Cells
One of the key trends in CNC machining automation is the development of fully autonomous machining cells. These systems will be able to operate without any human intervention, from part loading to quality inspection and maintenance. Autonomous cells will be capable of adapting to changes in production requirements, handling different materials, and performing complex machining tasks.
Collaborative Robots (Cobots)
Collaborative robots, or cobots, are designed to work alongside human operators in a shared workspace. Unlike traditional industrial robots, which are often enclosed in safety cages, cobots are equipped with advanced sensors and AI systems that enable them to work safely in close proximity to humans. In the future, cobots will play an increasingly important role in CNC machining, assisting operators with tasks such as part handling and tool changes.
Integration with Digital Twins
The concept of digital twins, which involves creating virtual replicas of physical machines, is gaining traction in the CNC machining industry. These digital models can simulate machining processes, enabling manufacturers to optimize machine performance and predict potential failures before they occur. As digital twin technology advances, it will become increasingly integrated into CNC machining automation systems, further enhancing their efficiency and predictive capabilities.
Conclusion
The automation of CNC machining sites is a powerful trend that is reshaping the manufacturing industry. By incorporating robotics, AI, sensors, and IoT technologies, manufacturers can achieve higher productivity, improved quality control, and significant cost savings. While challenges such as high initial investment and workforce transitions remain, the long-term benefits of CNC machining automation are undeniable. As technology continues to evolve, the future of CNC machining looks increasingly autonomous, efficient, and interconnected, offering new opportunities for innovation and growth across industries.
Reprint Statement: If there are no special instructions, all articles on this site are original. Please indicate the source for reprinting:https://www.cncmachiningptj.com/,thanks!
3, 4 and 5-axis precision CNC machining services for aluminum machining, beryllium, carbon steel, magnesium, titanium machining, Inconel, platinum, superalloy, acetal, polycarbonate, fiberglass, graphite and wood. Capable of machining parts up to 98 in. turning dia. and +/-0.001 in. straightness tolerance. Processes include milling, turning, drilling, boring, threading, tapping, forming, knurling, counterboring, countersinking, reaming and laser cutting. Secondary services such as assembly, centerless grinding, heat treating, plating and welding. Prototype and low to high volume production offered with maximum 50,000 units. Suitable for fluid power, pneumatics, hydraulics and valve applications. Serves the aerospace, aircraft, military, medical and defense industries.PTJ will strategize with you to provide the most cost-effective services to help you reach your target,Welcome to Contact us ( sales@pintejin.com ) directly for your new project.
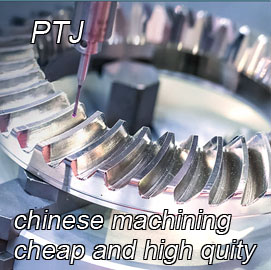
- 5 Axis Machining
- Cnc Milling
- Cnc Turning
- Machining Industries
- Machining Process
- Surface Treatment
- Metal Machining
- Plastic Machining
- Powder Metallurgy Mold
- Die Casting
- Parts Gallery
- Auto Metal Parts
- Machinery Parts
- LED Heatsink
- Building Parts
- Mobile Parts
- Medical Parts
- Electronic Parts
- Tailored Machining
- Bicycle Parts
- Aluminum Machining
- Titanium Machining
- Stainless Steel Machining
- Copper Machining
- Brass Machining
- Super Alloy Machining
- Peek Machining
- UHMW Machining
- Unilate Machining
- PA6 Machining
- PPS Machining
- Teflon Machining
- Inconel Machining
- Tool Steel Machining
- More Material