Pickling: Advantages and Disadvantages
Pickling, in the context of material science and metallurgy, refers to a process used to remove surface contaminants such as scale, rust, or oxides from metal surfaces. This process is achieved by immersing the metal in a bath of acidic solution, typically hydrochloric acid (HCl), sulfuric acid (H2SO4), or a mixture of both, which dissolves the unwanted layers. The pickling process plays a crucial role in preparing metals for further processing, such as coating, welding, or forming, ensuring the integrity and longevity of the finished product. Though pickling offers several advantages in industrial manufacturing, particularly in the steel and aluminum industries, it also carries a range of disadvantages that need to be considered when determining its suitability for a particular application.
Advantages of Pickling
1. Surface Cleaning and Preparation
One of the primary advantages of pickling is its ability to thoroughly clean and prepare metal surfaces. Metals like steel often undergo high-temperature processes such as hot rolling or welding, during which scale or oxide layers form on the surface. These layers can negatively affect the metal's mechanical properties and the adhesion of subsequent coatings or finishes. Pickling removes these layers efficiently, ensuring that the metal is clean and uniform. This is crucial for industries where precision and quality control are paramount, such as aerospace, automotive, and medical device manufacturing.
The chemical reaction during pickling dissolves the oxides and scales that may be difficult to remove through mechanical methods such as abrasive blasting. As a result, pickling allows for a more consistent and thorough cleaning process that would be difficult to replicate with other techniques. This ensures that the metal surface is free from contaminants that could lead to defects in subsequent manufacturing steps.
2. Improved Surface Finish
After pickling, metals often exhibit a smoother, more uniform surface finish. This improvement in surface quality is particularly valuable in applications where the final product requires high precision, such as in the production of stainless steel sheets for food-grade or pharmaceutical environments. Pickling not only removes contaminants but also minimizes the risk of further oxidation, which could mar the aesthetic appearance or functional properties of the metal.
The improved surface finish provided by pickling also enhances the metal’s ability to undergo further processing, such as coating or welding. For instance, a clean, smooth surface ensures better adhesion of paints, coatings, or galvanization layers, contributing to the long-term durability of the metal. This is especially important in industries where corrosion resistance is crucial, such as in the production of infrastructure materials or marine equipment.
3. Corrosion Resistance
Pickling can increase the corrosion resistance of metals, particularly stainless steel, by removing iron oxide (rust) and other contaminants that may inhibit the metal’s resistance to environmental factors. After pickling, metals often undergo a passivation process, where they are treated with a mild acid to further enhance their resistance to corrosion. This is particularly important in industries that require high levels of corrosion resistance, such as in the chemical processing or marine industries.
In stainless steel, pickling removes free iron from the surface, which could lead to localized corrosion. By removing these iron particles, pickling promotes the formation of a more stable oxide layer, thereby increasing the overall longevity of the metal in corrosive environments. The passivation treatment that often follows pickling further improves this corrosion resistance by forming a thin, protective oxide layer that is more resistant to chemical attack.
4. Enhanced Welding and Coating Performance
Pickling plays a critical role in enhancing the performance of metals during welding and coating processes. During welding, the heat generated can cause the formation of heat-affected zones (HAZ), which may have an altered microstructure and, in some cases, may be prone to oxidation. Pickling helps remove these oxidized layers, ensuring that the metal is free from contaminants that could weaken the weld joint.
Similarly, in coating applications, the ability to remove surface contaminants ensures that coatings adhere more securely to the metal surface. Coatings such as paint, galvanization, or powder coating require a clean, roughened surface for optimal bonding. Pickling is an effective means of preparing the metal, ensuring that these coatings perform as intended, both aesthetically and functionally.
5. Cost-Effectiveness
In some cases, pickling is a more cost-effective method for cleaning and preparing metal surfaces than mechanical or abrasive methods. Abrasive cleaning techniques, such as sandblasting or shot peening, can be labor-intensive, require specialized equipment, and produce significant waste. Pickling, on the other hand, uses a chemical solution, which is relatively inexpensive and can be easily replenished or reused. Additionally, the labor requirements for pickling are often lower than for mechanical cleaning methods, contributing to overall cost savings for manufacturers.
The ability to scale pickling processes in large batches, particularly in industrial settings, makes it an ideal solution for mass production environments. This is especially true for industries such as automotive manufacturing, where large volumes of metal components must be processed efficiently. The simplicity of the pickling process, combined with its effectiveness, makes it a preferred method in many applications.
6. Versatility in Application
Pickling can be used to treat a wide range of metals, including ferrous and non-ferrous alloys. It is commonly employed in the treatment of carbon steel, stainless steel, aluminum, copper, and titanium, among others. Each of these metals benefits from pickling in different ways. For example, in stainless steel, pickling removes chromium carbide precipitates that may form during welding, while in aluminum, it removes oxide layers that hinder subsequent treatments such as anodizing.
The versatility of pickling makes it suitable for a broad spectrum of industries and applications, from aerospace and defense to food processing and electronics manufacturing. This adaptability is a significant factor in its widespread use across various sectors.
Disadvantages of Pickling
While pickling offers many advantages, there are also notable drawbacks and limitations associated with the process.
1. Environmental Impact
One of the most significant disadvantages of pickling is its environmental impact. The acids used in the pickling process are highly corrosive and can be harmful to both human health and the environment if not handled properly. The spent pickling solution, which contains dissolved metals and acid residues, requires careful disposal to avoid contamination of soil and water. Improper disposal of pickling waste can lead to significant environmental pollution, particularly if the chemicals enter the water supply or contaminate nearby ecosystems.
In recent years, there have been efforts to develop more environmentally friendly alternatives to traditional pickling solutions. These include the use of organic acids or less toxic chemicals, as well as the implementation of closed-loop systems that allow for the recycling of pickling solutions. However, despite these advancements, the environmental concerns surrounding pickling remain a key consideration for manufacturers.
2. Safety Concerns
The chemicals used in the pickling process, particularly strong acids, pose significant safety risks to workers involved in the process. Accidental exposure to pickling acids can result in severe chemical burns, respiratory problems, or eye injuries. The handling and storage of pickling solutions require strict safety protocols, including the use of personal protective equipment (PPE), such as gloves, goggles, and respirators.
Additionally, the fumes generated during pickling can be hazardous, particularly in poorly ventilated areas. Hydrogen chloride (HCl) gas, for example, can be released into the air during pickling, leading to respiratory issues if inhaled in large quantities. To mitigate these risks, pickling operations must be conducted in controlled environments, such as fume hoods or well-ventilated industrial spaces, with regular monitoring of air quality to ensure worker safety.
3. Surface Etching and Damage
Although pickling is effective at removing oxide layers and contaminants, it can also lead to some degree of surface etching, particularly if the acid solution is too strong or the pickling time is too long. This can result in pitting, discoloration, or a roughened surface finish, which may require further processing to correct. In some applications, such as the production of high-quality stainless steel or titanium parts, any form of surface damage can be unacceptable, and manufacturers must take extra care to control the pickling parameters to prevent unwanted effects.
Excessive pickling can also lead to the degradation of the underlying metal, especially if the process is not properly controlled. Over-pickling can cause the metal to become excessively porous or weakened, reducing its mechanical properties and making it more susceptible to corrosion. To prevent such issues, manufacturers must carefully monitor and control the concentration of the acid solution, the immersion time, and the temperature of the pickling bath.
4. Limited Effectiveness on Certain Contaminants
Pickling is highly effective at removing surface oxides and scales, but it is less effective at removing other types of contamination, such as organic residues or lubricants. In some cases, additional cleaning steps, such as ultrasonic cleaning or abrasive blasting, may be required to remove these types of contaminants. For example, in the case of titanium alloys, pickling may remove surface oxide layers but may not be sufficient to clean off oils, grease, or other organic substances. In such cases, a combination of cleaning techniques may be necessary to achieve the desired level of surface cleanliness.
5. High Energy Consumption
The pickling process can be energy-intensive, particularly when large-scale pickling baths are used. Heating the pickling solution to the required temperature, maintaining the bath at a consistent temperature, and circulating the solution through the metal parts all contribute to high energy consumption. For manufacturers looking to reduce their energy footprint, this can be a significant drawback, especially when compared to other cleaning or surface preparation techniques that may require less energy.
Moreover, the need for continuous replenishment of pickling chemicals, as well as the energy required for the disposal of spent solutions, can add to the overall environmental and economic cost of the process.
6. Inconsistent Results
In some cases, pickling can yield inconsistent results, particularly when the process parameters (such as temperature, time, and acid concentration) are not carefully controlled. Variations in the surface quality of the metal after pickling can lead to defects in subsequent manufacturing steps, such as coating or welding. For instance, if some areas of the metal are over-pickled while others are under-pickled, it can result in a non-uniform surface finish that may be difficult to correct.
Inconsistencies in the pickling process can also lead to variations in the corrosion resistance of the metal, particularly if the pickling solution is not replenished regularly or if the immersion time is not controlled. This lack of uniformity can be a significant issue in industries where high-quality, consistent results are required, such as in the production of medical devices or food processing equipment.
Conclusion
Pickling remains an essential process in many industries, particularly in the preparation and cleaning of metals for subsequent processing. Its advantages, including effective surface cleaning, improved corrosion resistance, and enhanced welding and coating performance, make it an attractive choice for many manufacturing applications. However, the process is not without its disadvantages, including environmental concerns, safety risks, and potential damage to the metal surface. Manufacturers must carefully weigh these factors when deciding whether pickling is the right choice for their specific needs.
To mitigate the disadvantages, ongoing advancements in pickling technology are focused on improving environmental sustainability, reducing safety risks, and enhancing process control. As industries continue to demand higher standards of surface quality and performance, the future of pickling will likely involve further innovations aimed at making the process more efficient, cost-effective, and environmentally friendly.
Reprint Statement: If there are no special instructions, all articles on this site are original. Please indicate the source for reprinting:https://www.cncmachiningptj.com/,thanks!
3, 4 and 5-axis precision CNC machining services for aluminum machining, beryllium, carbon steel, magnesium, titanium machining, Inconel, platinum, superalloy, acetal, polycarbonate, fiberglass, graphite and wood. Capable of machining parts up to 98 in. turning dia. and +/-0.001 in. straightness tolerance. Processes include milling, turning, drilling, boring, threading, tapping, forming, knurling, counterboring, countersinking, reaming and laser cutting. Secondary services such as assembly, centerless grinding, heat treating, plating and welding. Prototype and low to high volume production offered with maximum 50,000 units. Suitable for fluid power, pneumatics, hydraulics and valve applications. Serves the aerospace, aircraft, military, medical and defense industries.PTJ will strategize with you to provide the most cost-effective services to help you reach your target,Welcome to Contact us ( sales@pintejin.com ) directly for your new project.
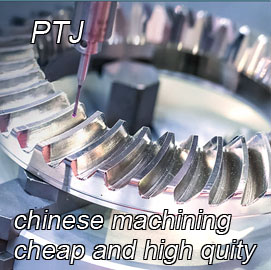
- 5 Axis Machining
- Cnc Milling
- Cnc Turning
- Machining Industries
- Machining Process
- Surface Treatment
- Metal Machining
- Plastic Machining
- Powder Metallurgy Mold
- Die Casting
- Parts Gallery
- Auto Metal Parts
- Machinery Parts
- LED Heatsink
- Building Parts
- Mobile Parts
- Medical Parts
- Electronic Parts
- Tailored Machining
- Bicycle Parts
- Aluminum Machining
- Titanium Machining
- Stainless Steel Machining
- Copper Machining
- Brass Machining
- Super Alloy Machining
- Peek Machining
- UHMW Machining
- Unilate Machining
- PA6 Machining
- PPS Machining
- Teflon Machining
- Inconel Machining
- Tool Steel Machining
- More Material