How to Get Into the Medical CNC Machining Industry
The medical CNC machining industry is a vital part of the global healthcare sector, contributing to the production of precise and reliable medical devices, implants, surgical tools, and other critical components used in healthcare. As medical technology continues to advance, the demand for high-quality, durable, and custom-made parts increases, creating opportunities for CNC (Computer Numerical Control) machinists and manufacturers to enter this specialized market. Whether you're an individual machinist looking to transition into the medical field or a company interested in expanding into medical device manufacturing, understanding the nuances of medical CNC machining is essential to success.
This article will cover the key aspects of entering the medical CNC machining industry, including understanding the regulatory landscape, acquiring the necessary certifications, mastering specialized machining techniques, investing in the right equipment, and building a solid network within the medical device and healthcare industries. Throughout the article, we will explore the various challenges and opportunities that this sector presents and offer guidance on how to navigate the path to success.
1. Understanding the Medical CNC Machining Market
The medical CNC machining industry involves the manufacturing of high-precision parts used in medical devices, equipment, and implants. These parts must meet rigorous quality standards, as they often play a crucial role in patient safety and the efficacy of medical treatments. Components produced through CNC machining for the medical industry include orthopedic implants (such as knee and hip replacements), dental implants, surgical instruments, and diagnostic equipment.
Due to the critical nature of these components, the medical CNC machining market is highly regulated, with manufacturers required to adhere to strict guidelines and certifications to ensure the safety and performance of their products. The industry’s focus on precision, cleanliness, and the use of biocompatible materials makes it a unique and highly specialized field.
Medical devices and instruments must undergo extensive testing, and the manufacturing processes used to produce them must be thoroughly documented and traceable. As such, CNC machining in the medical field involves more than just operating machines—it requires a comprehensive understanding of medical device design, materials, manufacturing processes, and compliance with global standards.
2. Gaining the Necessary Skills and Education
To enter the medical CNC machining industry, individuals must first gain a solid foundation in general CNC machining. This can be achieved through formal education programs, apprenticeships, or hands-on experience. Many vocational schools, community colleges, and technical institutes offer courses in CNC machining, which provide the knowledge and practical skills required to work with CNC machines and automated manufacturing systems.
In addition to general CNC machining knowledge, it is essential to gain an understanding of medical device manufacturing and the specific requirements of the medical industry. Specialized training in medical device regulations, such as FDA guidelines, ISO standards, and Good Manufacturing Practices (GMP), is crucial for success in this field. Many manufacturers offer internal training programs or partner with educational institutions to provide specialized courses focused on medical device manufacturing.
For those already working in the machining industry, gaining certification in medical device manufacturing can help differentiate them from other professionals in the field. Various organizations offer certifications for individuals in specialized areas, such as machining for medical implants, precision machining, and medical device design and manufacturing.
3. Understanding Regulatory Compliance and Certifications
One of the most critical aspects of entering the medical CNC machining industry is navigating the complex regulatory landscape. The production of medical devices is governed by a range of regulations that ensure the safety, effectiveness, and quality of the products. These regulations can vary by country, but there are some common standards that manufacturers and machinists must understand:
3.1. FDA Regulations (United States)
In the United States, the Food and Drug Administration (FDA) regulates the manufacturing of medical devices through its Center for Devices and Radiological Health (CDRH). The FDA requires medical device manufacturers to comply with the Quality System Regulation (QSR), which outlines the requirements for medical device design, manufacturing, testing, and post-market surveillance.
The FDA also requires that all medical devices be classified based on their risk level (Class I, II, or III), with Class III devices being the most critical and subject to the strictest regulations. Manufacturers must submit a premarket notification (510(k)) or a premarket approval (PMA) application for high-risk devices, providing evidence that their products are safe and effective.
For CNC machinists, working within FDA regulations means understanding the requirements for traceability, documentation, and quality control. Parts used in medical devices must be meticulously documented, and manufacturers must maintain comprehensive records of each component’s production history.
3.2. ISO Standards
The International Organization for Standardization (ISO) develops and publishes international standards for various industries, including the medical device sector. ISO 13485 is the primary standard for quality management systems (QMS) in medical device manufacturing, outlining the requirements for maintaining consistent quality in the design, production, and servicing of medical devices.
Manufacturers involved in medical CNC machining must adhere to ISO 13485 standards to ensure their processes meet the necessary quality and safety requirements. This certification is essential for companies that wish to do business with medical device manufacturers or suppliers, as it demonstrates a commitment to quality management and regulatory compliance.
3.3. Good Manufacturing Practices (GMP)
Good Manufacturing Practices (GMP) are guidelines established to ensure that products are consistently produced and controlled according to quality standards. GMP regulations are particularly important in industries such as pharmaceuticals and medical devices, where the integrity and safety of products directly affect public health.
For CNC machinists, GMP requires attention to detail in every stage of the manufacturing process, from the selection of materials to the final inspection of finished parts. GMP guidelines emphasize cleanliness, precision, and the prevention of contamination, which are especially critical in the production of components used in medical applications.
4. Selecting the Right Equipment for Medical CNC Machining
Investing in the right CNC machining equipment is essential for success in the medical industry. The precision required for medical components often demands state-of-the-art machinery and specialized tools. Some of the key factors to consider when selecting equipment for medical CNC machining include:
4.1. Precision and Tolerance
Medical devices require extremely tight tolerances to ensure proper function and safety. A small error in machining can lead to device failure, patient harm, or regulatory non-compliance. Therefore, investing in CNC machines that offer high precision and repeatability is critical.
Machines such as multi-axis CNC mills, lathes, and Swiss-type lathes are commonly used in medical machining due to their ability to handle complex geometries and tight tolerances. Additionally, some specialized machines, like electrical discharge machines (EDMs), may be required for producing intricate features or working with hard-to-machine materials.
4.2. Materials Selection
The choice of materials is also crucial in medical CNC machining. Medical-grade materials must be biocompatible, meaning they do not cause adverse reactions when in contact with human tissue. Common materials used in medical device manufacturing include stainless steel, titanium, cobalt-chromium alloys, and polymers such as PEEK (Polyetheretherketone).
Machinists working in the medical industry must be familiar with the characteristics of these materials, as well as the specific machining techniques required to work with them. Some materials, such as titanium, require specialized tooling and cutting strategies to achieve the desired surface finish and dimensional accuracy.
4.3. Cleanliness and Contamination Control
The cleanliness of medical parts is paramount, as even the smallest amount of contamination can compromise the safety of the final product. CNC machining centers used in medical device manufacturing must be equipped with advanced cleaning systems and adhere to strict contamination control protocols.
Many medical CNC machining facilities use Class 100 or ISO 5 cleanroom environments to ensure that parts are produced in a contamination-free space. These controlled environments are equipped with air filtration systems, humidity controls, and other features to maintain the cleanliness of the workspace.
5. Building Relationships with Medical Device Manufacturers
Networking and establishing strong relationships with medical device manufacturers is a key strategy for entering the medical CNC machining industry. Many medical device companies outsource the production of certain components, including custom parts, to specialized CNC machinists and manufacturers. By building connections with these companies, machinists can gain access to high-value contracts and grow their presence in the industry.
Attending industry conferences, trade shows, and medical device expos is an excellent way to meet potential clients and learn more about the latest trends and innovations in medical manufacturing. Industry events also offer opportunities to network with regulatory experts, quality control professionals, and other key stakeholders in the medical device sector.
6. Challenges and Opportunities in the Medical CNC Machining Industry
6.1. Challenges
The medical CNC machining industry presents several challenges for newcomers, including the complex regulatory environment, the high cost of equipment and certifications, and the need to stay current with advances in medical technology. The high cost of compliance with regulations, such as ISO certifications and FDA approvals, can be a significant barrier to entry for small and medium-sized businesses.
6.2. Opportunities
Despite the challenges, the medical CNC machining industry offers significant opportunities for growth. With an aging population and increasing demand for medical devices, there is a growing need for high-quality, precision-manufactured parts. Technological advancements in medical imaging, robotics, and implantable devices are also creating new opportunities for CNC machinists to contribute to cutting-edge innovations in healthcare.
Conclusion
Entering the medical CNC machining industry requires a combination of technical expertise, regulatory knowledge, and a commitment to quality. By gaining the necessary skills and certifications, investing in the right equipment, and building strong relationships with medical device manufacturers, machinists and companies can establish themselves in this critical and lucrative market. With the right approach, the medical CNC machining industry offers a wealth of opportunities to those willing to navigate its complexities and meet the stringent demands of the healthcare sector.
Reprint Statement: If there are no special instructions, all articles on this site are original. Please indicate the source for reprinting:https://www.cncmachiningptj.com/,thanks!
3, 4 and 5-axis precision CNC machining services for aluminum machining, beryllium, carbon steel, magnesium, titanium machining, Inconel, platinum, superalloy, acetal, polycarbonate, fiberglass, graphite and wood. Capable of machining parts up to 98 in. turning dia. and +/-0.001 in. straightness tolerance. Processes include milling, turning, drilling, boring, threading, tapping, forming, knurling, counterboring, countersinking, reaming and laser cutting. Secondary services such as assembly, centerless grinding, heat treating, plating and welding. Prototype and low to high volume production offered with maximum 50,000 units. Suitable for fluid power, pneumatics, hydraulics and valve applications. Serves the aerospace, aircraft, military, medical and defense industries.PTJ will strategize with you to provide the most cost-effective services to help you reach your target,Welcome to Contact us ( sales@pintejin.com ) directly for your new project.
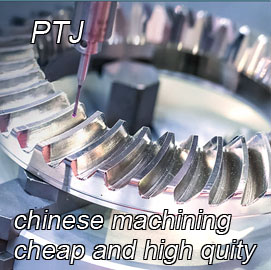
- 5 Axis Machining
- Cnc Milling
- Cnc Turning
- Machining Industries
- Machining Process
- Surface Treatment
- Metal Machining
- Plastic Machining
- Powder Metallurgy Mold
- Die Casting
- Parts Gallery
- Auto Metal Parts
- Machinery Parts
- LED Heatsink
- Building Parts
- Mobile Parts
- Medical Parts
- Electronic Parts
- Tailored Machining
- Bicycle Parts
- Aluminum Machining
- Titanium Machining
- Stainless Steel Machining
- Copper Machining
- Brass Machining
- Super Alloy Machining
- Peek Machining
- UHMW Machining
- Unilate Machining
- PA6 Machining
- PPS Machining
- Teflon Machining
- Inconel Machining
- Tool Steel Machining
- More Material