Choosing the Right Flame Retardant Plastics: A Comprehensive Guide
Flame retardant plastics are engineered materials designed to resist ignition and slow down the spread of fire, offering a crucial line of defense in various industries, including aerospace, automotive, electrical, construction, and consumer electronics. Selecting the appropriate flame retardant plastic for a specific application requires a deep understanding of material properties, regulatory requirements, and performance standards. This comprehensive guide aims to provide a detailed overview of flame retardant plastics, their types, applications, and key considerations in choosing the right material for your needs.
Introduction to Flame Retardant Plastics
Flame retardant plastics are modified polymers that have been chemically treated or compounded with flame retardant additives to reduce their flammability. The primary purpose of flame retardants is to enhance the material's resistance to combustion, thereby preventing or delaying the spread of fire in the event of an ignition. These materials are essential in protecting both people and property from fire hazards, particularly in high-risk environments such as buildings, transportation vehicles, and industrial settings.
Flame retardants can be classified into two main categories: additive flame retardants and reactive flame retardants. Additive flame retardants are incorporated into the plastic during processing and can be easily removed or leached out over time. In contrast, reactive flame retardants chemically bond with the polymer, becoming an integral part of the material's structure and providing longer-lasting fire resistance.
In recent years, the development of flame retardant plastics has focused not only on improving fire resistance but also on minimizing environmental impact and addressing health concerns related to certain flame retardant chemicals. As a result, regulations and standards governing the use of flame retardants have become increasingly stringent, particularly in consumer goods and building materials.
Types of Flame Retardant Plastics
Flame retardant plastics can be categorized based on their polymer base and the type of flame retardant used. The most common types of flame retardant plastics include:
-
Polycarbonate (PC)
Polycarbonate is a versatile engineering plastic known for its high impact strength, optical clarity, and excellent flame resistance. When combined with flame retardant additives, polycarbonate can meet stringent fire safety standards without sacrificing performance or appearance. Polycarbonate is often used in applications such as electrical housings, automotive components, and lighting fixtures. -
Polyamide (PA)
Polyamide, commonly known as nylon, is a high-performance thermoplastic with good mechanical properties and resistance to wear and tear. Flame retardant versions of polyamide are used in a wide range of electrical and automotive applications where durability and fire resistance are paramount. The flame retardant properties of polyamide can be achieved through the use of both additive and reactive flame retardants. -
Polyvinyl Chloride (PVC)
PVC is one of the most widely used plastics in construction and electrical industries due to its low cost, versatility, and ease of processing. Flame retardant PVC is commonly used in electrical cables, flooring, and wall coverings. The incorporation of flame retardants in PVC helps reduce the risk of fire spread in buildings and other infrastructure. -
Polyethylene (PE) and Polypropylene (PP)
Polyethylene and polypropylene are widely used in a variety of applications, from packaging to automotive components. While these polymers are naturally more flammable, the addition of flame retardants allows them to meet fire safety regulations in critical applications. Flame retardant polyethylene and polypropylene are often used in the manufacture of electrical components, insulation materials, and automotive parts. -
Acrylonitrile Butadiene Styrene (ABS)
ABS is a thermoplastic known for its impact resistance, stiffness, and ease of processing. Flame retardant ABS is used in applications where both mechanical strength and fire resistance are required, such as in electrical housings, consumer electronics, and automotive parts. The material can be formulated with different types of flame retardants, depending on the specific performance requirements. -
Polystyrene (PS)
Polystyrene is a low-cost plastic used in a variety of applications, including packaging, insulation, and consumer goods. Flame retardant polystyrene is used where fire resistance is required in low-cost products. However, the use of flame retardants in polystyrene can sometimes compromise its mechanical properties and processing ease, so careful formulation is necessary to balance fire resistance with performance. -
Epoxy Resins
Epoxy resins are widely used in coatings, adhesives, and composite materials due to their excellent adhesion, chemical resistance, and high mechanical strength. Flame retardant epoxy resins are particularly important in the aerospace, automotive, and electronics industries, where fire resistance is critical. These resins can be modified with flame retardant agents to meet the specific needs of demanding applications. -
Polyurethane (PU)
Polyurethane is a versatile polymer used in applications ranging from foams to coatings and adhesives. Flame retardant polyurethanes are used in furniture, insulation materials, and automotive seating. These materials can be formulated to provide both flexibility and fire resistance, making them ideal for a variety of consumer and industrial products.
Flame Retardant Additives and Their Mechanisms
Flame retardant additives are chemicals incorporated into plastics to enhance their fire resistance. These additives work through different mechanisms to inhibit combustion. The two primary mechanisms by which flame retardants act are:
-
Physical Barriers
Some flame retardants form a protective char layer on the surface of the plastic when exposed to heat. This char layer acts as a barrier that prevents further heat from reaching the underlying material, slowing the rate of combustion. Common flame retardants that work through this mechanism include intumescent additives, which expand when heated to form a thick, insulating layer. -
Chemical Interruption
Other flame retardants interfere with the chemical reactions that occur during combustion. These flame retardants release substances that either absorb heat or dilute the flammable gases around the material, thus reducing the material’s ability to catch fire. Halogenated flame retardants, such as brominated and chlorinated compounds, work through this mechanism, although their environmental and health impact has led to increased scrutiny and regulation. -
Heat Absorption
Certain flame retardants absorb heat during the combustion process, reducing the temperature of the plastic and slowing the spread of fire. This can be achieved through the use of inorganic compounds, such as aluminum hydroxide or magnesium hydroxide, which release water vapor when heated, absorbing large amounts of heat in the process. -
Endothermic Decomposition
Some flame retardants decompose in an endothermic reaction, absorbing heat and preventing further combustion. Examples of flame retardants that function via endothermic decomposition include ammonium polyphosphate and melamine.
Key Considerations When Choosing Flame Retardant Plastics
Selecting the right flame retardant plastic for a given application requires careful consideration of various factors. These include the specific fire safety standards and regulations that apply to the product, as well as the material’s mechanical, chemical, and environmental properties.
-
Fire Safety Regulations
Different industries and regions have specific regulations governing fire safety for plastic materials. For example, the International Building Code (IBC), Underwriters Laboratories (UL) standards, and the European Union's REACH regulations all set requirements for the fire performance of plastics. It is essential to ensure that the selected flame retardant plastic complies with the relevant standards for the intended application. -
Mechanical and Thermal Properties
The choice of flame retardant plastic will depend on the mechanical and thermal demands of the application. For instance, materials used in the aerospace industry must not only be fire-resistant but also possess high strength-to-weight ratios and excellent thermal stability. Similarly, automotive components need to withstand high temperatures and mechanical stress while maintaining fire resistance. -
Environmental Impact
Environmental concerns have led to the development of more sustainable and less toxic flame retardants. Manufacturers are increasingly opting for halogen-free flame retardants, which do not release harmful byproducts when exposed to fire. Additionally, flame retardants that do not persist in the environment or bioaccumulate are becoming more desirable. -
Cost Considerations
Cost is always a critical factor in material selection. While flame retardant plastics provide essential safety benefits, the use of flame retardants can increase the cost of production. Balancing fire resistance with cost-effectiveness is important, particularly in industries where margins are tight, such as consumer electronics and automotive manufacturing. -
Compatibility with Other Materials
In many applications, flame retardant plastics are used in conjunction with other materials, such as metals, ceramics, or textiles. Ensuring that the chosen flame retardant plastic is compatible with these materials is essential for maintaining product integrity and performance. Incompatibilities may lead to issues with adhesion, durability, or manufacturing processes.
Flame Retardant Plastics in Specific Industries
-
Aerospace
In the aerospace industry, fire safety is a top priority. Flame retardant plastics are used in various components, including aircraft interiors, wiring, insulation, and electronic housings. The materials must meet stringent fire resistance standards such as the FAA (Federal Aviation Administration) regulations and UL 94 V-0 classification for low flammability. -
Automotive
Flame retardant plastics play a crucial role in the automotive industry, where safety and performance are paramount. Flame retardants are used in components such as dashboards, seat materials, electrical wiring, and under-the-hood parts. Automotive plastics must meet fire safety standards like FMVSS (Federal Motor Vehicle Safety Standards) to ensure occupant protection. -
Electrical and Electronics
In electrical and electronics applications, flame retardant plastics are used in connectors, circuit boards, housings, and cables. These materials need to meet safety standards such as UL 94 and IEC (International Electrotechnical Commission) standards for electrical fire resistance. -
Building and Construction
Flame retardant plastics are commonly used in the construction industry for applications such as window profiles, roofing membranes, electrical wiring insulation, and flooring. These materials must meet building codes and fire safety regulations to ensure the safety of occupants. -
Consumer Goods
Consumer goods, including household appliances, furniture, and toys, often require flame retardant plastics to ensure safety. In this sector, materials must meet consumer product safety regulations, such as those set by the Consumer Product Safety Commission (CPSC) in the United States or similar agencies in other regions.
Reprint Statement: If there are no special instructions, all articles on this site are original. Please indicate the source for reprinting:https://www.cncmachiningptj.com/,thanks!
PTJ® provides a full range of Custom Precision cnc machining china services.ISO 9001:2015 &AS-9100 certified. 3, 4 and 5-axis rapid precision CNC machining services including milling, turning to customer specifications,Capable of metal & plastic machined parts with +/-0.005 mm tolerance.Secondary services include CNC and conventional grinding, drilling,die casting,sheet metal and stamping.Providing prototypes, full production runs, technical support and full inspection.Serves the automotive, aerospace, mold&fixture,led lighting,medical,bicycle, and consumer electronics industries. On-time delivery.Tell us a little about your project's budget and expected delivery time. We will strategize with you to provide the most cost-effective services to help you reach your target,Welcome to Contact us ( sales@pintejin.com ) directly for your new project.
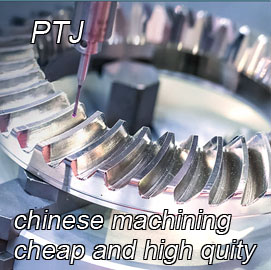
- 5 Axis Machining
- Cnc Milling
- Cnc Turning
- Machining Industries
- Machining Process
- Surface Treatment
- Metal Machining
- Plastic Machining
- Powder Metallurgy Mold
- Die Casting
- Parts Gallery
- Auto Metal Parts
- Machinery Parts
- LED Heatsink
- Building Parts
- Mobile Parts
- Medical Parts
- Electronic Parts
- Tailored Machining
- Bicycle Parts
- Aluminum Machining
- Titanium Machining
- Stainless Steel Machining
- Copper Machining
- Brass Machining
- Super Alloy Machining
- Peek Machining
- UHMW Machining
- Unilate Machining
- PA6 Machining
- PPS Machining
- Teflon Machining
- Inconel Machining
- Tool Steel Machining
- More Material