How to Remove Chrome Plating from Sheet Metal
Chrome plating, a process of applying a layer of chromium to a metal surface, is widely used for its aesthetic appeal, corrosion resistance, and enhanced durability. Chrome-plated items are commonly found in automotive parts, household appliances, bathroom fixtures, and various industrial components. However, there are times when chrome plating needs to be removed, such as for restoration, repair, or recycling purposes. Removing chrome plating from sheet metal is a delicate process that requires specific methods and safety precautions to ensure the underlying metal is not damaged.
Overview of Chrome Plating
Chrome plating is typically applied using either electroplating or a process called hard chrome plating, depending on the desired properties. In electroplating, a thin layer of chromium is deposited onto a metal surface through an electrochemical process. Hard chrome plating, on the other hand, is used primarily for enhancing the hardness and wear resistance of a surface and typically involves a thicker layer of chromium. Chrome plating is most commonly applied to metals like steel, aluminum, brass, and copper, which benefit from its corrosion resistance and aesthetic finish.
While chrome plating offers numerous advantages, such as improved wear resistance, reduced friction, and a shiny, reflective finish, it can also become tarnished or damaged over time. When this happens, the removal of chrome plating becomes necessary, especially when the plating is chipped, corroded, or simply no longer desirable.
Safety Precautions for Removing Chrome Plating
Before attempting to remove chrome plating from sheet metal, it is essential to prioritize safety. The chrome removal process can involve the use of harsh chemicals, potentially hazardous equipment, and tools. Here are some general safety precautions to consider:
-
Wear Protective Gear: Always wear gloves, safety goggles, and protective clothing when working with chemicals or abrasive tools. Chrome removal chemicals, such as hydrochloric acid or sulfuric acid, can be corrosive and cause severe burns or eye damage if they come into contact with the skin or eyes.
-
Work in a Well-Ventilated Area: Many chrome removal methods involve the use of caustic chemicals that emit fumes, which can be harmful if inhaled. Ensure that you are working in a well-ventilated area or use a fume hood to avoid inhaling dangerous fumes.
-
Dispose of Waste Properly: Chrome removal often produces toxic waste materials, including acidic solutions or chromium waste. Be sure to dispose of waste properly, according to local regulations, to avoid environmental contamination or injury.
-
Handle Equipment with Care: If using power tools such as sanders or grinders, ensure they are in good working condition. Always follow the manufacturer’s instructions and use the proper technique to avoid injury.
Methods for Removing Chrome Plating from Sheet Metal
Several methods are available for removing chrome plating from sheet metal, ranging from chemical processes to mechanical techniques. The most appropriate method for a particular project depends on the type of chrome plating, the underlying metal, and the desired results. Below are some of the most common methods for removing chrome plating from sheet metal.
1. Chemical Removal Using Acidic Solutions
Chemical removal of chrome plating is one of the most effective methods, as it dissolves the chromium layer without significantly affecting the base metal beneath. Several acids are commonly used for this purpose, including hydrochloric acid, sulfuric acid, and a variety of commercial chrome removal solutions.
a. Using Muriatic Acid (Hydrochloric Acid)
Muriatic acid, a diluted form of hydrochloric acid, is often used for chrome removal. It can be purchased at most hardware stores and is highly effective in breaking down chrome plating. To use muriatic acid for removing chrome from sheet metal, follow these steps:
-
Prepare the Work Area: Ensure you are working in a well-ventilated area or a fume hood. Protect the work surface with plastic sheets or tarps to prevent acid spills from damaging the surrounding environment.
-
Dilute the Acid: Muriatic acid should always be diluted with water to reduce its strength and minimize the risk of damage to the base metal. A typical dilution ratio is 1 part acid to 4 parts water, but it may vary depending on the thickness of the chrome plating.
-
Soak the Metal: Submerge the chrome-plated sheet metal into the diluted acid solution. If the sheet metal is large, you may need to use a container large enough to fully submerge the part. Let it soak for several hours or until the chrome begins to dissolve.
-
Scrub the Chrome Plating: After soaking, use a wire brush or abrasive pad to scrub the chrome-plated surface. The plating should start to flake off or peel away. Use a plastic or nylon brush to avoid damaging the base metal.
-
Rinse and Neutralize: Once the chrome has been removed, rinse the metal thoroughly with water to remove any remaining acid. Neutralize the acid by washing the metal with a mixture of water and baking soda or sodium bicarbonate.
b. Using Sulfuric Acid
Sulfuric acid is another commonly used acid for chrome removal. It works similarly to muriatic acid but is often considered less aggressive. Sulfuric acid is preferred in situations where the base metal is more sensitive to damage. The process for using sulfuric acid is similar to that of muriatic acid: dilute the acid, soak the part, scrub the plating, and rinse and neutralize.
c. Using Commercial Chrome Removal Solutions
For a less hazardous method, there are commercial chrome removal solutions available that are specifically formulated to dissolve chrome plating. These products are often less corrosive than muriatic or sulfuric acid, making them a safer choice for handling and disposal.
To use a commercial chrome removal solution, follow the manufacturer’s instructions, which will typically involve applying the solution to the chrome surface and allowing it to sit for a specific period. After the plating begins to dissolve, scrub the surface to remove the remaining chrome. These solutions are usually designed to work quickly and are less likely to damage the underlying metal.
2. Mechanical Methods for Chrome Removal
Mechanical methods involve using physical tools and abrasives to remove the chrome plating from the surface of the sheet metal. These techniques are ideal when you need to remove the chrome more quickly or if chemical methods are not effective. Mechanical methods can be labor-intensive and may result in some damage to the base metal if not done carefully.
a. Grinding or Sanding
Grinding or sanding is one of the most effective mechanical methods for removing chrome plating. This method involves using abrasive materials such as sandpaper, grinding wheels, or power tools to physically strip away the chrome layer.
-
Choose the Right Abrasive: Select an abrasive that is hard enough to remove the chrome but soft enough to avoid excessive damage to the underlying metal. Coarse sandpaper or a grinding wheel is usually effective for removing chrome plating.
-
Use Power Tools: A power sander or a rotary tool equipped with abrasive discs can speed up the process, especially for larger sheet metal parts. Be sure to use a consistent and even pressure to avoid gouging the surface.
-
Clean and Polish: After removing the chrome plating, the underlying metal may need to be polished to restore its appearance. Use finer abrasives or a polishing wheel to smooth the surface.
b. Media Blasting (Sandblasting)
Media blasting, or sandblasting, is a process that uses compressed air to force abrasive particles (such as sand, glass beads, or walnut shells) against the chrome-plated surface. The abrasive particles remove the chrome plating without damaging the base metal. Sandblasting is ideal for removing chrome from larger or more intricate parts.
To perform media blasting, follow these steps:
-
Choose an Appropriate Abrasive: Select an abrasive that will effectively remove the chrome without damaging the underlying metal. Coarse sand or aluminum oxide is commonly used for heavy chrome removal, while finer media like glass beads may be used for a smoother finish.
-
Set up the Blasting Equipment: Media blasting requires specialized equipment, including a blasting cabinet or portable sandblasting unit, and a supply of compressed air. Ensure that the equipment is properly set up and adjusted to avoid over-blasting the surface.
-
Blast the Surface: Using steady, controlled motions, direct the blast at the chrome-plated surface. Be cautious not to focus on one area for too long, as this can result in pitting or other damage to the base metal.
c. Wire Brushing
Wire brushing is a simpler and less aggressive mechanical method for removing chrome plating. It involves using a wire brush to scrape away the chrome layer. While this method is slower than grinding or sandblasting, it is less likely to cause damage to delicate parts.
To use wire brushing effectively:
-
Select the Right Brush: Choose a wire brush that is designed for metalworking, typically with stainless steel or brass bristles.
-
Brush the Surface: Apply moderate pressure and work in circular or linear motions to remove the chrome layer. This method is most effective for light to moderate chrome plating.
3. Electrolytic Stripping
Electrolytic stripping is a process that uses an electrical current to reverse the electroplating process, effectively removing the chrome from the sheet metal. This method is highly effective for precision applications and can be used to remove chrome without causing significant damage to the underlying metal.
To perform electrolytic stripping, follow these general steps:
-
Prepare the Electrolyte Solution: The electrolyte solution typically consists of a mixture of sulfuric acid and water, though some variations may use different solutions depending on the base metal.
-
Set Up the Electrolytic Cell: The sheet metal part serves as the cathode in the electrolytic cell, while a suitable anode (such as a lead or stainless steel electrode) is placed in the solution. The parts should be connected to a power supply that can deliver a low current.
-
Run the Electrolytic Process: Apply a low voltage current to the system, causing the chromium to dissolve and deposit onto the anode. This process can take several hours, depending on the thickness of the chrome plating.
4. Thermal Methods
Thermal methods for removing chrome plating are less common but can be effective in certain situations. These methods involve applying heat to the chrome-plated part to break the bond between the chrome and the base metal.
- Oven Heating: One thermal method involves heating the part in an oven to a temperature that will cause the chrome to expand and crack, making it easier to remove. This method works best with thin layers of chrome and should be carefully monitored to avoid damage to the underlying metal.
Conclusion
Removing chrome plating from sheet metal is a multi-faceted process that can be accomplished through a variety of methods. The choice of method depends on the specific requirements of the project, the type of chrome plating, and the nature of the underlying metal. Chemical methods, mechanical techniques, electrolytic stripping, and thermal methods all offer viable solutions, each with its advantages and limitations.
When undertaking the removal of chrome plating, it is crucial to prioritize safety by using appropriate protective gear and ensuring that waste materials are disposed of responsibly. Regardless of the method chosen, the goal is to restore the base metal to its original condition while minimizing damage. With the right tools, techniques, and precautions, removing chrome plating from sheet metal can be achieved effectively and safely.
Reprint Statement: If there are no special instructions, all articles on this site are original. Please indicate the source for reprinting:https://www.cncmachiningptj.com/,thanks!
3, 4 and 5-axis precision CNC machining services for aluminum machining, beryllium, carbon steel, magnesium, titanium machining, Inconel, platinum, superalloy, acetal, polycarbonate, fiberglass, graphite and wood. Capable of machining parts up to 98 in. turning dia. and +/-0.001 in. straightness tolerance. Processes include milling, turning, drilling, boring, threading, tapping, forming, knurling, counterboring, countersinking, reaming and laser cutting. Secondary services such as assembly, centerless grinding, heat treating, plating and welding. Prototype and low to high volume production offered with maximum 50,000 units. Suitable for fluid power, pneumatics, hydraulics and valve applications. Serves the aerospace, aircraft, military, medical and defense industries.PTJ will strategize with you to provide the most cost-effective services to help you reach your target,Welcome to Contact us ( sales@pintejin.com ) directly for your new project.
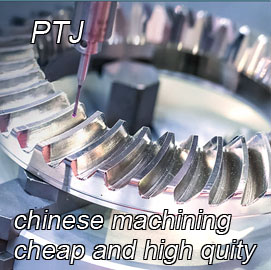
- 5 Axis Machining
- Cnc Milling
- Cnc Turning
- Machining Industries
- Machining Process
- Surface Treatment
- Metal Machining
- Plastic Machining
- Powder Metallurgy Mold
- Die Casting
- Parts Gallery
- Auto Metal Parts
- Machinery Parts
- LED Heatsink
- Building Parts
- Mobile Parts
- Medical Parts
- Electronic Parts
- Tailored Machining
- Bicycle Parts
- Aluminum Machining
- Titanium Machining
- Stainless Steel Machining
- Copper Machining
- Brass Machining
- Super Alloy Machining
- Peek Machining
- UHMW Machining
- Unilate Machining
- PA6 Machining
- PPS Machining
- Teflon Machining
- Inconel Machining
- Tool Steel Machining
- More Material