CNC Motion Control and Three Common Types
Computer Numerical Control (CNC) is a method used to automate machine tools through the use of computers executing pre-programmed sequences of machine control commands. CNC motion control plays a pivotal role in ensuring precision, accuracy, and efficiency in modern manufacturing processes, particularly in machining operations. The motion control system in a CNC machine is responsible for translating the digital commands generated by the machine’s program into mechanical movement that drives the machine tool. It involves controlling the movement of various machine components, including axes, spindles, and tool changers, to perform tasks such as milling, turning, drilling, and cutting.
The main goal of CNC motion control is to ensure that the machine tool follows the exact path specified by the design or program, ensuring that the final part is fabricated to precise tolerances. The movement of machine components is typically achieved using motors, servos, encoders, and other electronic control components that work together to move the mechanical parts with high speed and accuracy.
This article delves into the basics of CNC motion control, its importance, and the three common types of motion control systems used in CNC machines: point-to-point control, continuous path control, and simultaneous multi-axis control.
Overview of CNC Motion Control Systems
A CNC machine operates by following a set of instructions that dictate the position, speed, and path the tool will take to shape the material being worked on. These instructions are often represented in the form of G-codes (geometric codes) and M-codes (miscellaneous functions) that are interpreted by the machine’s controller. The motion control system interprets these commands and coordinates the machine’s various movements, ensuring that each part of the machine functions in unison.
In general, CNC machines use a combination of electrical, mechanical, and software systems to control the movements. This interaction between hardware and software is vital for the accurate movement of the machine parts. The motion control system typically uses an interface, such as a computer or an embedded control unit, to process the instructions and send signals to the relevant actuators (motors, servos, etc.) to initiate movement. Sensors and feedback systems are incorporated to monitor and adjust these movements, ensuring that the machine stays on course throughout the process.
Types of Motion Control in CNC
There are three fundamental types of motion control systems used in CNC machines: point-to-point control, continuous path control, and simultaneous multi-axis control. Each type has distinct characteristics and is suited for different applications depending on the complexity of the machining task.
1. Point-to-Point Control
Point-to-point control, also known as single-axis control, is the simplest and most straightforward motion control type. In this system, the machine tool moves from one designated point to another without the need to follow a continuous path. It is often used in applications where the workpiece does not require complex shaping or contouring but needs precise placement at specific locations.
In point-to-point control, the motion of the tool typically occurs along a straight line, and the tool’s movement from one point to another can be performed at a rapid speed. Once the tool reaches the designated point, the control system will stop, and the tool performs the machining operation, such as drilling, before moving on to the next point.
One of the most common examples of point-to-point control is in drilling machines, where the tool needs to travel from one hole location to another. The movement is typically linear, and once the tool reaches the designated position, it performs the drilling operation.
Advantages:
- Simple to implement and use.
- Low computational and control demands.
- Ideal for operations such as drilling, punching, or simple milling.
Disadvantages:
- Limited to simple applications.
- Does not provide continuous movement or smooth contouring.
- Inefficient for operations requiring intricate toolpaths or complex geometry.
2. Continuous Path Control
Continuous path control, also known as contouring or multi-axis control, is a more advanced form of motion control compared to point-to-point. In this system, the tool moves continuously along a specified path, typically along curved or angled surfaces, while maintaining a constant feedrate. This allows for more complex machining operations, where the tool follows a continuous and often intricate path to shape the workpiece.
Continuous path control is often used in milling, turning, and other machining operations where the tool needs to move smoothly along multiple axes in a coordinated manner. The key distinction between point-to-point and continuous path control is that in the latter, the motion is not interrupted at each point; instead, the tool follows a continuous and fluid path from start to finish.
In practice, continuous path control is typically employed in CNC milling machines, where the tool must follow a curved or intricate geometry. The controller coordinates the movement of multiple axes simultaneously to create a smooth, continuous cutting path.
Advantages:
- Allows for the machining of complex shapes and contours.
- Ideal for operations that require smooth, continuous cuts, such as surface milling.
- Provides greater flexibility for a wide range of machining operations.
Disadvantages:
- Requires more sophisticated software and hardware.
- Can be computationally intensive and requires advanced controllers.
- More challenging to implement and program compared to point-to-point control.
3. Simultaneous Multi-Axis Control
Simultaneous multi-axis control is the most advanced form of CNC motion control and is used for highly complex machining operations. In this system, the machine tool moves in multiple directions simultaneously, controlling several axes at once. This allows for the creation of highly intricate and complex geometries that cannot be achieved using simpler control types.
Simultaneous multi-axis control is commonly used in applications such as 3D machining, complex surface machining, and the production of parts with complex geometries, such as molds and dies. It is typically employed in CNC milling machines, CNC lathes, and other advanced manufacturing equipment that require the ability to move multiple axes at once with high precision.
The most common types of multi-axis CNC machines include 5-axis machines, where the tool moves along the X, Y, and Z axes while also rotating around two additional axes, usually the A and B axes. These machines are capable of creating complex shapes, cutting at multiple angles, and producing high-precision parts in one setup.
Advantages:
- Ideal for complex geometries and 3D machining tasks.
- Reduces the need for multiple setups and tool changes.
- Provides higher precision and more flexible machining capabilities.
Disadvantages:
- Requires high-end CNC controllers and sophisticated programming skills.
- Expensive in terms of both initial cost and maintenance.
- More complex to operate and program compared to simpler control types.
Factors Affecting CNC Motion Control Performance
The performance of a CNC motion control system can be influenced by several factors, including the type of machine, the complexity of the motion path, and the material being worked on. Below are some of the key factors that impact motion control performance:
1. Servo Systems and Feedback
Servo systems, which are used to control the movement of CNC machine tools, play a critical role in ensuring precise motion control. The servos receive commands from the CNC controller and adjust the position of the tool accordingly. Feedback mechanisms, such as encoders and resolvers, provide real-time position data, allowing the control system to make adjustments as needed.
High-precision servo systems are essential for maintaining accuracy, especially in multi-axis control applications where small errors can compound quickly.
2. Control Algorithms
The algorithms used by the CNC controller to process motion control commands can significantly affect the machine’s performance. Advanced controllers use sophisticated algorithms to calculate and adjust the movements in real-time, optimizing feed rates and tool paths for greater efficiency and precision.
For example, look-ahead algorithms allow the controller to anticipate future movements and adjust the speed and acceleration to minimize errors during the machining process.
3. Motion Coordination
In multi-axis machines, effective motion coordination is essential for achieving smooth, simultaneous movement along multiple axes. This requires careful synchronization of the motors, servos, and controllers to ensure that the machine moves precisely according to the desired toolpath.
4. Machine Rigidity
The overall rigidity of the CNC machine is another important factor that affects motion control. Machines with high rigidity can better maintain precision during movement, especially at higher feed rates or during cutting operations that produce significant forces. Less rigid machines may experience deflection or vibration, leading to inaccuracies in the final part.
Conclusion
CNC motion control is a critical component in the automation of manufacturing processes, ensuring that machines can produce parts with high precision and repeatability. The three common types of motion control—point-to-point, continuous path, and simultaneous multi-axis control—each offer distinct advantages depending on the complexity of the machining task. While point-to-point control is suitable for simpler operations, continuous path control and simultaneous multi-axis control are necessary for more advanced machining operations that require smooth, continuous movement along intricate paths or multi-dimensional shapes.
As CNC technology continues to evolve, motion control systems are becoming increasingly sophisticated, allowing for even greater levels of precision, speed, and flexibility in machining operations. Whether it’s in aerospace, automotive, medical, or consumer goods manufacturing, CNC motion control systems are integral to the production of high-quality parts with ever-increasing levels of complexity. Understanding the different types of motion control and the factors that influence their performance is essential for optimizing CNC machining operations and achieving the desired outcomes.
Reprint Statement: If there are no special instructions, all articles on this site are original. Please indicate the source for reprinting:https://www.cncmachiningptj.com/,thanks!
PTJ® provides a full range of Custom Precision cnc machining china services.ISO 9001:2015 &AS-9100 certified. 3, 4 and 5-axis rapid precision CNC machining services including milling, turning to customer specifications,Capable of metal & plastic machined parts with +/-0.005 mm tolerance.Secondary services include CNC and conventional grinding, drilling,die casting,sheet metal and stamping.Providing prototypes, full production runs, technical support and full inspection.Serves the automotive, aerospace, mold&fixture,led lighting,medical,bicycle, and consumer electronics industries. On-time delivery.Tell us a little about your project's budget and expected delivery time. We will strategize with you to provide the most cost-effective services to help you reach your target,Welcome to Contact us ( sales@pintejin.com ) directly for your new project.
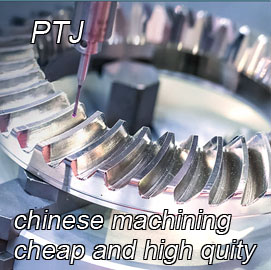
- 5 Axis Machining
- Cnc Milling
- Cnc Turning
- Machining Industries
- Machining Process
- Surface Treatment
- Metal Machining
- Plastic Machining
- Powder Metallurgy Mold
- Die Casting
- Parts Gallery
- Auto Metal Parts
- Machinery Parts
- LED Heatsink
- Building Parts
- Mobile Parts
- Medical Parts
- Electronic Parts
- Tailored Machining
- Bicycle Parts
- Aluminum Machining
- Titanium Machining
- Stainless Steel Machining
- Copper Machining
- Brass Machining
- Super Alloy Machining
- Peek Machining
- UHMW Machining
- Unilate Machining
- PA6 Machining
- PPS Machining
- Teflon Machining
- Inconel Machining
- Tool Steel Machining
- More Material