What Is the Difference Between Calcined Alumina and Aluminum Oxide?
Aluminum oxide and calcined alumina are two terms frequently encountered in materials science and industrial applications. While both are derived from aluminum, they differ significantly in terms of their processing, physical properties, and applications. Understanding these differences is crucial for industries that utilize these materials for various purposes, such as ceramics, refractories, electronics, and abrasives.
Aluminum Oxide: A Fundamental Overview
Aluminum oxide, also known as alumina, is a chemical compound with the formula Al2O3\text{Al}_2\text{O}_3
. It occurs naturally in the form of the mineral corundum, which includes gemstones such as sapphire and ruby when impurities are present. Aluminum oxide is characterized by its hardness, thermal stability, and electrical insulating properties, making it a versatile material in numerous industries.Properties of Aluminum Oxide
- Chemical Stability: Aluminum oxide is highly resistant to chemical reactions, particularly with acids and alkalis, under standard conditions.
- High Hardness: On the Mohs scale, aluminum oxide ranks at 9, just below diamond, making it suitable for abrasive applications.
- Thermal Resistance: With a melting point of approximately 2,072°C (3,762°F), it is ideal for high-temperature environments.
- Electrical Insulation: It serves as an excellent electrical insulator, a property widely utilized in the electronics industry.
Forms of Aluminum Oxide
Aluminum oxide exists in several phases, including alpha (α), gamma (γ), delta (δ), and theta (θ), among others. The alpha phase is the most stable and crystalline, while the other phases are typically transitional and convert to the alpha phase upon heating.
- Alpha Alumina: This is the most thermodynamically stable form and is used in ceramics, refractories, and abrasives.
- Gamma Alumina: Known for its high surface area, gamma alumina is employed as a catalyst or catalyst support.
- Other Phases: Transitional phases such as delta and theta alumina exist under specific conditions and are primarily intermediates during thermal treatment.
Calcined Alumina: Definition and Characteristics
Calcined alumina is a specific type of aluminum oxide that has undergone calcination, a thermal treatment process. This process involves heating aluminum hydroxide, or other forms of hydrated alumina, to remove chemically bonded water. The resulting material is a highly pure form of aluminum oxide with enhanced properties tailored for specific industrial applications.
Production Process of Calcined Alumina
- Source Material: Calcined alumina is produced from aluminum hydroxide (Al(OH)3\text{Al(OH)}_3 ) through the Bayer process.
- Calcination: The aluminum hydroxide is heated to temperatures ranging from 1,000°C to 1,300°C. This process removes water molecules, transforming the hydroxide into anhydrous aluminum oxide.
- Tailored Properties: By controlling the calcination temperature and duration, manufacturers can customize the physical properties of calcined alumina, such as particle size, surface area, and density.
Properties of Calcined Alumina
Calcined alumina exhibits distinct characteristics compared to untreated aluminum oxide:
- Controlled Crystallinity: The calcination process ensures a uniform crystalline structure, typically in the alpha phase.
- Enhanced Hardness: The removal of water increases the material's hardness, making it suitable for high-wear applications.
- High Purity: Calcined alumina often exceeds 99% purity, a requirement for applications in electronics and advanced ceramics.
Applications of Calcined Alumina
Calcined alumina finds use in industries where precision and high performance are critical:
- Refractories: Its high melting point and chemical inertness make it ideal for linings in furnaces and kilns.
- Ceramics: Calcined alumina is used as a raw material for producing fine ceramics, including spark plug insulators and substrates for electronic devices.
- Abrasives: Its hardness makes it an effective abrasive material for cutting, grinding, and polishing.
- Polishing Agents: The fine particle size of calcined alumina allows it to be used as a polishing agent for metals and glass.
Comparing Calcined Alumina and Aluminum Oxide
While calcined alumina is a specific form of aluminum oxide, the two terms are not interchangeable. The differences arise from the processing, physical properties, and end-use applications.
Chemical Composition
- Aluminum Oxide: Composed of Al2O3\text{Al}_2\text{O}_3 , it may contain impurities depending on its source.
- Calcined Alumina: A highly pure form of aluminum oxide obtained through the calcination process.
Physical Properties
- Hardness: Both materials are hard, but calcined alumina's controlled crystallinity gives it an edge in certain applications.
- Thermal Stability: Aluminum oxide is naturally thermally stable, but calcined alumina is optimized for high-temperature environments.
Surface Area and Particle Size
- Aluminum Oxide: Available in a range of particle sizes and surface areas, depending on its form (e.g., gamma or alpha alumina).
- Calcined Alumina: Tailored to have specific particle sizes and surface areas, often smaller and more uniform than untreated aluminum oxide.
Applications
- Aluminum Oxide: Broadly used in abrasive materials, ceramics, and as a catalyst support.
- Calcined Alumina: Preferred for high-performance applications requiring precise control over material properties.
Industrial Implications
The distinction between aluminum oxide and calcined alumina has practical implications in manufacturing and material selection. For example, industries requiring high purity and specific physical properties often favor calcined alumina, while aluminum oxide is sufficient for general-purpose applications.
Abrasives Industry
- Aluminum Oxide: Widely used as a general-purpose abrasive for metalworking, woodworking, and surface preparation.
- Calcined Alumina: Employed in high-precision abrasive applications, such as semiconductor polishing.
Electronics Industry
- Aluminum Oxide: Acts as an insulating layer in electronic components.
- Calcined Alumina: Used in advanced ceramics for electronic substrates and thermal management.
Environmental and Economic Considerations
The production and use of both materials have environmental and economic impacts. The calcination process requires significant energy, which contributes to its cost and carbon footprint. However, the high performance of calcined alumina can justify these costs in specialized applications.
Conclusion
In summary, while calcined alumina and aluminum oxide share the same base chemical composition, their differences lie in processing, properties, and applications. Calcined alumina, being a refined and tailored form of aluminum oxide, offers enhanced properties for high-performance industrial uses. Understanding these distinctions allows industries to make informed decisions, optimizing material performance and cost-effectiveness for their specific needs.
Reprint Statement: If there are no special instructions, all articles on this site are original. Please indicate the source for reprinting:https://www.cncmachiningptj.com/,thanks!
3, 4 and 5-axis precision CNC machining services for aluminum machining, beryllium, carbon steel, magnesium, titanium machining, Inconel, platinum, superalloy, acetal, polycarbonate, fiberglass, graphite and wood. Capable of machining parts up to 98 in. turning dia. and +/-0.001 in. straightness tolerance. Processes include milling, turning, drilling, boring, threading, tapping, forming, knurling, counterboring, countersinking, reaming and laser cutting. Secondary services such as assembly, centerless grinding, heat treating, plating and welding. Prototype and low to high volume production offered with maximum 50,000 units. Suitable for fluid power, pneumatics, hydraulics and valve applications. Serves the aerospace, aircraft, military, medical and defense industries.PTJ will strategize with you to provide the most cost-effective services to help you reach your target,Welcome to Contact us ( sales@pintejin.com ) directly for your new project.
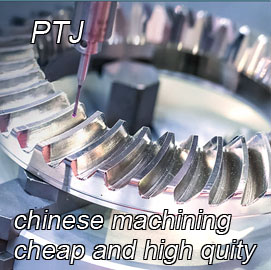
- 5 Axis Machining
- Cnc Milling
- Cnc Turning
- Machining Industries
- Machining Process
- Surface Treatment
- Metal Machining
- Plastic Machining
- Powder Metallurgy Mold
- Die Casting
- Parts Gallery
- Auto Metal Parts
- Machinery Parts
- LED Heatsink
- Building Parts
- Mobile Parts
- Medical Parts
- Electronic Parts
- Tailored Machining
- Bicycle Parts
- Aluminum Machining
- Titanium Machining
- Stainless Steel Machining
- Copper Machining
- Brass Machining
- Super Alloy Machining
- Peek Machining
- UHMW Machining
- Unilate Machining
- PA6 Machining
- PPS Machining
- Teflon Machining
- Inconel Machining
- Tool Steel Machining
- More Material