What Is Rack and Pinion?
Rack and pinion is a type of mechanical linear actuator that converts rotational motion into linear motion. It consists of two primary components: a gear known as the pinion and a flat toothed component known as the rack. When the pinion rotates, its teeth engage with the teeth on the rack, causing the rack to move in a linear direction. This simple but versatile mechanism plays a critical role in a wide range of mechanical systems, from automobiles to industrial machinery.
The rack and pinion system is a fundamental component in various applications, particularly in steering mechanisms for vehicles, where it is used to convert the rotational motion of the steering wheel into the linear motion required to turn the wheels. Other applications include machines for metalworking, robotics, and even certain types of conveyors.
Historical Context and Development
The basic principle of rack and pinion has been known since ancient times, but its practical application in mechanical engineering began to take shape during the Renaissance. The earliest recorded use of a rack and pinion mechanism appears in the writings of the Greek engineer Heron of Alexandria, who described a mechanical system involving rotating gears. However, it was not until the 15th century that the system was fully realized and employed in the form that we recognize today.
Leonardo da Vinci, the famed Renaissance polymath, is credited with having studied and documented the use of gears and mechanical linkages extensively. His sketches of mechanical devices reveal a keen understanding of the fundamental principles that govern the rack and pinion system, even though this technology did not gain widespread use until the Industrial Revolution.
In the 19th century, with the rise of precision manufacturing, rack and pinion systems began to be widely adopted in machines, particularly in automobiles, where they became essential components in steering mechanisms. Today, the mechanism is used in numerous fields, including aerospace, robotics, and material handling.
Basic Components of Rack and Pinion
The rack and pinion system comprises two primary components:
-
Pinion: The pinion is a round gear that meshes with the teeth of the rack. It is usually smaller in diameter compared to other gears in a system and is typically mounted on a rotating shaft. As it turns, its teeth engage the teeth on the rack to produce linear motion. The pinion's teeth are typically designed with specific tooth profiles, such as involute teeth, to ensure smooth engagement with the rack.
-
Rack: The rack is a flat, toothed bar that runs parallel to the motion direction. It typically has a series of teeth cut along its length that correspond to the teeth of the pinion. When the pinion rotates, the teeth of the pinion move along the teeth of the rack, causing the rack to move linearly in the direction of the pinion's rotation.
Both components must be made with precision to ensure the system operates smoothly, with minimal friction and wear. The tooth profiles and materials used for both the rack and pinion are crucial factors in determining the efficiency and lifespan of the mechanism.
How Rack and Pinion Works
The operation of a rack and pinion system is straightforward but effective in converting rotational motion into linear motion. The pinion, when rotated by a driving force (such as an electric motor, manual turning, or hydraulic force), moves its teeth along the length of the rack. The motion of the pinion causes the rack to move in a straight line, proportional to the rotation of the pinion.
This system works due to the engagement of the teeth on the pinion with the teeth on the rack. As the pinion rotates, its teeth push the teeth of the rack forward, causing linear displacement. The direction of the rack’s motion depends on the direction of the pinion's rotation. If the pinion rotates clockwise, the rack moves in one direction, and if the pinion rotates counterclockwise, the rack moves in the opposite direction.
The relationship between the pinion and the rack is typically designed with a ratio that determines the amount of linear displacement for each revolution of the pinion. This ratio is determined by the number of teeth on the pinion and the length of the rack. For example, if a pinion has 20 teeth and a rack has 20 teeth per inch, each full revolution of the pinion will move the rack by one inch.
Applications of Rack and Pinion Systems
Rack and pinion systems are employed in a diverse array of industries due to their versatility and simplicity. Some of the primary applications include:
Automotive Steering Systems
The most well-known application of rack and pinion technology is in automotive steering systems. In a rack and pinion steering system, the steering wheel is connected to the pinion, which is connected to the rack. When the driver turns the steering wheel, the pinion rotates, which moves the rack and, consequently, the wheels of the vehicle.
This system provides a direct, responsive connection between the driver’s input and the wheels of the vehicle, offering both precision and ease of use. The rack and pinion mechanism is known for its reliability and efficiency, which is why it has largely replaced the older worm gear-based steering mechanisms.
Industrial Machinery and Automation
In industrial machinery, rack and pinion systems are often used to control the linear motion of parts or workpieces. For example, in CNC machines, a rack and pinion can be used to move the cutting head or table along a designated axis. The smooth linear motion provided by the rack and pinion system is essential in maintaining the high precision required in manufacturing processes.
In automation, rack and pinion systems are used in robotic arms and conveyor systems, where the need for precise and continuous linear motion is paramount. The ability to control both the speed and position of components in these systems makes the rack and pinion a valuable tool in modern automation.
Elevators and Lifts
Rack and pinion systems are also used in the operation of some elevator and lift systems. In these systems, the pinion is typically driven by a motor, and the rack is fixed to the elevator or lift car. As the pinion rotates, the elevator moves along the vertical rail, allowing it to ascend or descend.
Rack and pinion elevators are often used in environments that require high vertical lifts, such as in mines or for large construction equipment. Their ability to handle heavy loads and provide stable, precise control of movement makes them an excellent choice for such applications.
Material Handling Systems
In material handling, rack and pinion mechanisms are commonly found in systems that require linear motion to move goods or materials from one place to another. Automated guided vehicles (AGVs), cranes, and other types of heavy machinery often use rack and pinion technology to achieve precise positioning and movement along a defined path.
Types of Rack and Pinion Systems
Rack and pinion systems can be categorized based on various factors, such as the type of application, the construction of the components, and the materials used. Some common types of rack and pinion systems include:
Standard Rack and Pinion
This is the most common type of rack and pinion system, used in many general applications. The pinion has a cylindrical shape, and its teeth are designed to mesh with the teeth on the flat, linear rack. This type of system is typically used in automobile steering, conveyor systems, and other machinery requiring straightforward linear motion.
Helical Rack and Pinion
In a helical rack and pinion system, the teeth on the pinion and the rack are cut at an angle to the axis of rotation. This design allows for smoother engagement between the teeth, resulting in reduced noise, vibration, and wear. Helical rack and pinion systems are often used in applications where higher precision and smoother motion are required, such as in CNC machines and high-precision manufacturing.
Straight Tooth Rack and Pinion
In this system, the teeth on both the pinion and the rack are cut straight, or parallel, to the axis of motion. Straight tooth rack and pinion systems are typically simpler and more cost-effective to manufacture, but they may generate more noise and vibration compared to helical systems. They are used in applications where cost is a key factor and the level of precision required is not extremely high.
Planetary Rack and Pinion
A planetary rack and pinion system is a variation that uses multiple pinions that engage with the rack simultaneously. This system is often used to distribute the load more evenly and achieve higher torque output with reduced wear. Planetary rack and pinion systems are found in applications requiring high-load handling or when space is constrained.
Materials Used in Rack and Pinion Systems
The materials chosen for the rack and pinion system are crucial to ensuring long-lasting, reliable performance. Common materials used in rack and pinion systems include:
-
Steel: High-strength steel is the most common material used in rack and pinion systems. Steel is known for its durability, resistance to wear, and ability to withstand high loads. For particularly demanding applications, hardened steel may be used to improve wear resistance.
-
Stainless Steel: Stainless steel is used in rack and pinion systems where corrosion resistance is essential, such as in marine environments or chemical processing industries. Stainless steel components are resistant to rust and corrosion, making them suitable for use in harsh conditions.
-
Aluminum: Lightweight aluminum is sometimes used in rack and pinion systems, particularly in applications where weight reduction is important. Aluminum is less durable than steel but is suitable for less demanding applications or where corrosion resistance is needed.
-
Bronze and Brass: In some applications, bronze or brass is used for the rack or pinion to reduce friction and wear. These materials are often found in systems where low friction is important, such as in precision machinery or where lubrication is difficult.
-
Plastic: For lightweight applications or in environments where noise reduction is critical, plastic materials such as nylon or acetal may be used. These materials are less durable than metals but offer advantages in terms of reduced weight, noise, and cost.
Advantages of Rack and Pinion Systems
The rack and pinion mechanism offers several advantages, which is why it has been widely adopted in various industries:
-
Simplicity: Rack and pinion systems are relatively simple in design and easy to maintain. Their straightforward mechanism, consisting of only a few parts, makes them highly reliable.
-
Efficiency: Rack and pinion systems convert rotational motion into linear motion with a high degree of efficiency. This makes them ideal for applications where precision and smooth motion are critical.
-
Precision: With the proper design and materials, rack and pinion systems can provide extremely precise control of linear motion. This is particularly important in industries such as aerospace, robotics, and manufacturing.
-
Compactness: The system is relatively compact compared to other types of linear actuators, making it suitable for applications where space is limited.
-
Cost-Effective: Rack and pinion systems are generally cost-effective, particularly when compared to other linear motion solutions such as lead screws or ball screws. Their durability and low maintenance costs also contribute to their overall affordability.
Disadvantages of Rack and Pinion Systems
While rack and pinion systems offer many advantages, there are also some limitations:
-
Wear and Tear: Over time, the teeth of the pinion and rack can wear down due to friction, particularly in high-load or high-speed applications. Regular maintenance and lubrication are necessary to reduce wear and extend the life of the system.
-
Noise: Depending on the tooth profile and material used, rack and pinion systems can generate noise during operation. Helical rack and pinion systems tend to be quieter than straight-tooth designs, but noise reduction can be an issue in certain applications.
-
Limited Load Capacity: Although rack and pinion systems can handle moderate loads, they may not be suitable for applications requiring extremely high forces. In such cases, other linear motion solutions, such as ball screws or linear actuators, may be more appropriate.
Conclusion
Rack and pinion systems are integral to a wide range of applications where the conversion of rotational motion into linear motion is required. From automotive steering to industrial machinery, these systems provide a reliable, efficient, and cost-effective solution. Despite some challenges, such as wear and noise, the simplicity and versatility of rack and pinion systems make them an indispensable tool in mechanical engineering. Their continued development and optimization ensure their place in the modern industrial landscape for many years to come.
Reprint Statement: If there are no special instructions, all articles on this site are original. Please indicate the source for reprinting:https://www.cncmachiningptj.com/,thanks!
3, 4 and 5-axis precision CNC machining services for aluminum machining, beryllium, carbon steel, magnesium, titanium machining, Inconel, platinum, superalloy, acetal, polycarbonate, fiberglass, graphite and wood. Capable of machining parts up to 98 in. turning dia. and +/-0.001 in. straightness tolerance. Processes include milling, turning, drilling, boring, threading, tapping, forming, knurling, counterboring, countersinking, reaming and laser cutting. Secondary services such as assembly, centerless grinding, heat treating, plating and welding. Prototype and low to high volume production offered with maximum 50,000 units. Suitable for fluid power, pneumatics, hydraulics and valve applications. Serves the aerospace, aircraft, military, medical and defense industries.PTJ will strategize with you to provide the most cost-effective services to help you reach your target,Welcome to Contact us ( sales@pintejin.com ) directly for your new project.
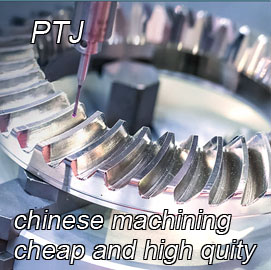
- 5 Axis Machining
- Cnc Milling
- Cnc Turning
- Machining Industries
- Machining Process
- Surface Treatment
- Metal Machining
- Plastic Machining
- Powder Metallurgy Mold
- Die Casting
- Parts Gallery
- Auto Metal Parts
- Machinery Parts
- LED Heatsink
- Building Parts
- Mobile Parts
- Medical Parts
- Electronic Parts
- Tailored Machining
- Bicycle Parts
- Aluminum Machining
- Titanium Machining
- Stainless Steel Machining
- Copper Machining
- Brass Machining
- Super Alloy Machining
- Peek Machining
- UHMW Machining
- Unilate Machining
- PA6 Machining
- PPS Machining
- Teflon Machining
- Inconel Machining
- Tool Steel Machining
- More Material