7075 Billet Aluminum vs 4140 Steel: Material Showdown
In the world of material science and manufacturing, selecting the right material for a given application is a critical decision that can greatly influence the performance, cost, and durability of the final product. Among the myriad of materials available to engineers and manufacturers, 7075 billet aluminum and 4140 steel stand out as two of the most commonly used high-performance materials. Each possesses distinct properties that make them ideal for a range of applications, yet their differences are substantial enough to make a head-to-head comparison worthwhile.
This article will explore the key properties, advantages, and disadvantages of both 7075 billet aluminum and 4140 steel, shedding light on their respective characteristics and how they compare in terms of strength, weight, machinability, corrosion resistance, and cost-effectiveness.
1. Introduction to 7075 Billet Aluminum
7075 aluminum is an alloy in the 7000 series of aluminum alloys. This series is known for its high strength-to-weight ratio, which is particularly useful in industries that require lightweight yet durable materials. The 7075 alloy, in particular, is one of the strongest aluminum alloys available, making it a popular choice in applications such as aerospace, military, and automotive industries. The billet form of 7075 aluminum refers to a solid, cast piece of material that is later machined into the final shape, providing high precision and consistency.
The primary alloying elements in 7075 aluminum are zinc, magnesium, and copper. The combination of these elements results in a material that is highly resistant to fatigue and stress, offering exceptional strength while maintaining a relatively low weight compared to steel. However, 7075 aluminum is not without its trade-offs. Its susceptibility to stress corrosion cracking in certain conditions, combined with a lower toughness than some steels, makes it a material that needs to be handled with care in specific applications.
2. Introduction to 4140 Steel
4140 steel is a medium-carbon alloy steel containing chromium, molybdenum, and manganese as its primary alloying elements. It is classified as a low-alloy steel and is known for its toughness, high tensile strength, and good hardenability. This steel is commonly used in applications where high strength, wear resistance, and impact resistance are critical.
4140 steel can be found in both annealed and quenched-and-tempered conditions, depending on the specific requirements of the application. The alloying elements in 4140 steel provide enhanced hardness, wear resistance, and toughness, making it suitable for use in machinery components, automotive parts, and tools. While heavier and denser than aluminum, 4140 steel compensates with superior toughness and resistance to wear and impact, making it an attractive choice for heavy-duty applications.
3. Comparison of Strength
Strength is one of the most critical factors when choosing materials for structural applications. Both 7075 aluminum and 4140 steel are known for their impressive strength properties, but the way they achieve and maintain strength differs significantly.
3.1 Tensile Strength
Tensile strength is a measure of a material's ability to resist breaking under tension. 7075 aluminum, in its billet form, boasts a tensile strength in the range of 74,000 to 78,000 psi (pounds per square inch), depending on the temper and the specific processing of the material. This places it among the strongest aluminum alloys available, but it is still significantly lower than many steels.
In comparison, 4140 steel exhibits a much higher tensile strength, ranging from 95,000 psi to 105,000 psi in its normalized and quenched-and-tempered forms. This makes 4140 steel significantly stronger than 7075 aluminum, making it better suited for applications that require the ability to withstand high tensile forces, such as heavy machinery components and industrial equipment.
3.2 Yield Strength
Yield strength is another important measure of a material's strength, reflecting its ability to resist deformation under stress. 7075 aluminum has a yield strength between 63,000 and 70,000 psi, while 4140 steel can have a yield strength of 85,000 psi to 95,000 psi depending on the tempering process.
This means that 4140 steel can handle greater stress before undergoing permanent deformation compared to 7075 aluminum. As a result, 4140 steel is often preferred in applications requiring resistance to bending, stretching, or other forms of mechanical deformation.
4. Weight Considerations
Weight is an essential factor in many engineering applications, particularly in industries like aerospace and automotive, where reducing mass can lead to improved efficiency and performance. When comparing the two materials, 7075 aluminum clearly has an advantage due to its lighter weight.
4.1 Density
7075 aluminum has a density of approximately 2.81 g/cm³, while 4140 steel has a density of around 7.85 g/cm³. This means that 4140 steel is nearly three times denser than 7075 aluminum. The lower density of 7075 aluminum allows it to achieve significant strength without the added weight, making it an excellent choice for applications where reducing mass is a priority, such as in aircraft structures or high-performance automotive components.
While the higher density of 4140 steel may seem like a disadvantage in applications where weight is crucial, it is important to note that the added weight is often offset by the material's superior strength and toughness. In many heavy-duty applications, the benefits of increased strength and resistance to wear and impact outweigh the importance of weight.
5. Machinability and Workability
Both 7075 aluminum and 4140 steel are known for their excellent machinability, but each material presents its own challenges and advantages when it comes to processing.
5.1 Machinability of 7075 Aluminum
7075 aluminum is relatively easy to machine due to its relatively soft composition compared to steel. It can be easily cut, drilled, milled, and turned, and it responds well to a variety of machining processes, including CNC milling, turning, and shaping. The high machinability of 7075 aluminum, combined with its high strength, makes it an attractive choice for industries that require precision machining and tight tolerances.
However, one potential downside of machining 7075 aluminum is that it can be prone to work hardening, meaning that the material's surface can become harder during machining. This requires the use of sharp tools and proper machining parameters to prevent premature tool wear and to achieve smooth, high-quality finishes.
5.2 Machinability of 4140 Steel
4140 steel, while also machinable, presents a greater challenge than 7075 aluminum due to its higher strength and hardness. Depending on the heat treatment and alloy composition, machining 4140 steel can be more difficult and require more robust equipment and tooling. In general, 4140 steel is harder to machine compared to 7075 aluminum, and the machining process can produce more heat and wear on cutting tools.
However, 4140 steel is known for its excellent toughness, which makes it less likely to crack or break under stress during machining. This allows for the production of intricate and complex parts, though the machining process typically requires slower feeds and higher cutting forces.
6. Corrosion Resistance
Corrosion resistance is a critical factor in many applications, particularly in environments where the material will be exposed to moisture, salt, or other corrosive elements. Both 7075 aluminum and 4140 steel exhibit good corrosion resistance, but their performance in this area differs due to their material compositions.
6.1 Corrosion Resistance of 7075 Aluminum
7075 aluminum is highly resistant to corrosion in most environments, particularly when anodized. The presence of zinc and magnesium in the alloy provides some protection against corrosion, but 7075 aluminum is susceptible to stress corrosion cracking, particularly in high-stress environments. This makes it less suitable for use in certain marine applications, where continuous exposure to saltwater could lead to degradation over time.
When anodized, 7075 aluminum develops a protective oxide layer that enhances its resistance to corrosion. Anodizing also improves the material's appearance and increases its resistance to wear. Despite these benefits, 7075 aluminum still has limitations in extremely harsh environments and may require additional protective coatings or treatments.
6.2 Corrosion Resistance of 4140 Steel
4140 steel, being a low-alloy steel, does not have the inherent corrosion resistance of aluminum alloys. While it can resist corrosion to some extent in mild environments, it is much more susceptible to rusting and degradation when exposed to moisture or corrosive chemicals. To mitigate this, 4140 steel is often coated or plated with materials such as chromium, nickel, or zinc to provide a protective barrier.
In environments where corrosion is a concern, 4140 steel may require regular maintenance, coating, or treatment to ensure its longevity and performance. In contrast, 7075 aluminum’s natural corrosion resistance, especially when anodized, often provides superior performance in less extreme conditions.
7. Cost Considerations
When it comes to cost, both 7075 aluminum and 4140 steel present unique pricing dynamics that depend on the form, quantity, and processing required for each material.
7.1 Cost of 7075 Aluminum
7075 aluminum is typically more expensive than standard aluminum alloys due to its higher strength and specialized manufacturing processes. The billet form of 7075 aluminum is generally more costly compared to other forms of aluminum, such as castings or extrusions. The alloy's processing, including heat treatment and potential anodization, adds further costs. However, the overall cost is still generally lower than many steels, especially in applications where weight reduction is a priority.
7.2 Cost of 4140 Steel
4140 steel is generally more affordable than 7075 aluminum, particularly when considering the initial cost of raw material. However, the cost of processing 4140 steel can be higher, especially when machining and heat treating are involved. In general, 4140 steel offers a good balance of performance and price, making it suitable for heavy-duty applications where strength and toughness are paramount.
8. Applications of 7075 Aluminum and 4140 Steel
Both 7075 aluminum and 4140 steel have a wide range of applications, but each material is better suited for specific uses due to its unique properties.
8.1 Applications of 7075 Aluminum
Due to its high strength-to-weight ratio, 7075 aluminum is commonly used in aerospace applications, including aircraft and spacecraft structures, where reducing weight without sacrificing strength is critical. It is also used in military applications, such as in weaponry, and in the manufacturing of high-performance sports equipment, including bicycles and skateboards.
8.2 Applications of 4140 Steel
4140 steel, with its exceptional toughness and resistance to wear and impact, is often used in the manufacturing of heavy-duty components such as crankshafts, gears, axles, and industrial machinery parts. It is also common in the automotive and construction industries for applications requiring high strength and durability, such as frame components and heavy-duty fasteners.
9. Conclusion
The choice between 7075 billet aluminum and 4140 steel largely depends on the specific requirements of the application. 7075 aluminum is an excellent choice for applications where weight reduction and strength are paramount, particularly in industries like aerospace and military. However, its susceptibility to stress corrosion cracking and lower toughness compared to steel may limit its use in certain applications.
On the other hand, 4140 steel excels in applications requiring superior strength, toughness, and wear resistance. While it is heavier and more difficult to machine than 7075 aluminum, its higher tensile strength and ability to resist impact make it ideal for heavy-duty applications.
Ultimately, both materials have their place in engineering and manufacturing, and the decision between 7075 billet aluminum and 4140 steel should be made based on factors such as strength, weight, machinability, corrosion resistance, and cost, as well as the specific demands of the end-use application.
Reprint Statement: If there are no special instructions, all articles on this site are original. Please indicate the source for reprinting:https://www.cncmachiningptj.com/,thanks!
PTJ® provides a full range of Custom Precision cnc machining china services.ISO 9001:2015 &AS-9100 certified. 3, 4 and 5-axis rapid precision CNC machining services including milling, turning to customer specifications,Capable of metal & plastic machined parts with +/-0.005 mm tolerance.Secondary services include CNC and conventional grinding, drilling,die casting,sheet metal and stamping.Providing prototypes, full production runs, technical support and full inspection.Serves the automotive, aerospace, mold&fixture,led lighting,medical,bicycle, and consumer electronics industries. On-time delivery.Tell us a little about your project's budget and expected delivery time. We will strategize with you to provide the most cost-effective services to help you reach your target,Welcome to Contact us ( sales@pintejin.com ) directly for your new project.
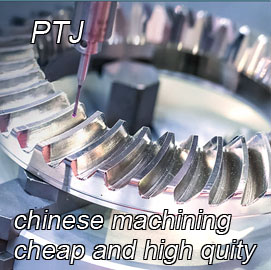
- 5 Axis Machining
- Cnc Milling
- Cnc Turning
- Machining Industries
- Machining Process
- Surface Treatment
- Metal Machining
- Plastic Machining
- Powder Metallurgy Mold
- Die Casting
- Parts Gallery
- Auto Metal Parts
- Machinery Parts
- LED Heatsink
- Building Parts
- Mobile Parts
- Medical Parts
- Electronic Parts
- Tailored Machining
- Bicycle Parts
- Aluminum Machining
- Titanium Machining
- Stainless Steel Machining
- Copper Machining
- Brass Machining
- Super Alloy Machining
- Peek Machining
- UHMW Machining
- Unilate Machining
- PA6 Machining
- PPS Machining
- Teflon Machining
- Inconel Machining
- Tool Steel Machining
- More Material