Can Titanium Be Anodized?
Titanium anodizing is a widely used electrochemical process that enhances the surface properties of titanium alloys, making them more resistant to corrosion, wear, and scratching, while also creating aesthetically attractive colored coatings. This process has applications in various industries, from aerospace to jewelry, and plays a crucial role in enhancing both the functional and decorative qualities of titanium components. This comprehensive guide delves into the science behind titanium anodizing, the various methods employed, its benefits, potential drawbacks, and its applications across different industries.
Overview of Titanium and Its Properties
Titanium is a strong, lightweight, corrosion-resistant metal that has made its mark in a wide range of industries, particularly in aerospace, medical, automotive, and jewelry sectors. Known for its excellent strength-to-weight ratio, titanium is often chosen for components subjected to high stress or extreme environmental conditions. It also boasts remarkable resistance to corrosion, especially in hostile environments such as seawater, making it ideal for marine applications.
The metal’s key advantage is its ability to form a natural oxide layer on its surface when exposed to air. This oxide layer, composed primarily of titanium dioxide (TiO₂), serves as a protective barrier, preventing further corrosion and offering a high degree of biocompatibility. However, this naturally occurring oxide layer is thin, with a thickness of only around 1 to 2 nanometers, and does not provide the desired color or surface enhancement for many applications.
What is Anodizing?
Anodizing is an electrochemical process that thickens the natural oxide layer on the surface of metals, primarily aluminum, titanium, and magnesium. The anodizing process increases the thickness of the oxide layer, thereby improving the material’s corrosion resistance and creating a highly durable, non-reactive surface. This process also offers aesthetic benefits by allowing the creation of a range of colors, primarily on titanium.
The basic anodizing process involves immersing the titanium workpiece in an electrolytic bath, usually containing an acid such as sulfuric acid or phosphoric acid. When an electric current is passed through the electrolyte, oxygen ions are attracted to the surface of the titanium, where they react with the metal to form a thick oxide layer. The color variations that occur during anodizing are a result of interference effects caused by the varying thicknesses of the oxide layer, which refract light in different wavelengths, producing a spectrum of colors.
The Science Behind Titanium Anodizing
The process of anodizing titanium relies on the principle of electrolysis. In this process, titanium is used as the anode (positive electrode) in an electrolytic bath, which contains an acidic solution. The bath is typically sulfuric acid, phosphoric acid, or organic acids, with the exact composition depending on the desired outcome.
When an electric current is applied, the titanium surface reacts with oxygen from the electrolyte, and titanium oxide (TiO₂) is formed. The thickness of the oxide layer can be controlled by adjusting the voltage and the duration of the anodizing process. Higher voltages produce thicker oxide layers, which result in more vibrant colors, ranging from pale gold and blue to purple and green. The colors are not produced by dyes but by interference effects between light and the oxide layer.
The color produced depends on the thickness of the oxide layer, which in turn depends on the voltage applied. For example:
- 10 to 20 volts may produce a colorless or transparent oxide layer.
- 20 to 60 volts typically results in pastel hues like yellow, gold, or pink.
- 60 to 150 volts can produce deeper shades of blue, purple, or green.
- Voltages above 150 volts create darker, more saturated colors, including brown or black.
At the same time, the oxide layer provides a high degree of corrosion resistance. The thickness of the oxide layer can range from a few micrometers to tens of micrometers, depending on the process parameters. The thicker the oxide layer, the better the material’s resistance to environmental factors, including moisture, saltwater, and acids.
Types of Titanium Anodizing
There are several different methods used for anodizing titanium, each with its specific applications and advantages. These include:
-
Sulfuric Acid Anodizing: This is the most common method for anodizing titanium. It provides an excellent balance between thickness and color variety and is typically used in aerospace and industrial applications. The sulfuric acid bath creates a thick, stable oxide layer that is highly resistant to corrosion.
-
Phosphoric Acid Anodizing: Phosphoric acid anodizing produces a smoother and denser oxide layer compared to sulfuric acid anodizing. This method is often used when a uniform, high-quality finish is required. It is particularly popular in the aerospace industry for creating precise and durable coatings on critical components.
-
Organic Acid Anodizing: Organic acids, such as tartaric or citric acid, are sometimes used to anodize titanium. These acids provide less aggressive anodization processes and are often used for more delicate applications or when a particular aesthetic is desired.
-
Hard Anodizing: Hard anodizing, also known as Type III anodizing, is a more intense process that produces a much thicker oxide layer compared to standard anodizing. This layer is particularly tough, providing additional protection against wear and friction. It is commonly used for parts that will experience high mechanical stresses, such as in military or industrial equipment.
-
Color Anodizing: Color anodizing involves manipulating the thickness of the oxide layer to produce a spectrum of colors, typically using sulfuric acid. The process does not involve dyes or pigments; instead, the colors result from light interference within the oxide film. Color anodizing is often used in jewelry, fashion accessories, and artistic applications.
Benefits of Titanium Anodizing
Titanium anodizing offers numerous benefits, making it one of the most popular methods for enhancing the properties of titanium alloys. These benefits include:
-
Improved Corrosion Resistance: The anodized layer of titanium provides a highly effective barrier against corrosive environments. The thicker the oxide layer, the more resistant the material becomes to environmental degradation, including exposure to seawater, acidic environments, and high temperatures.
-
Aesthetic Appeal: One of the most significant advantages of titanium anodizing is the ability to create vibrant colors on the metal surface. By adjusting the anodizing process, a wide range of colors, from deep blues to purples and greens, can be achieved. This makes anodizing particularly popular in the jewelry and fashion industries.
-
Increased Wear Resistance: The oxide layer formed during anodizing is harder than the titanium substrate itself. This increased hardness makes anodized titanium more resistant to wear and abrasion, which is particularly beneficial for parts subjected to heavy mechanical stress, such as in aerospace, automotive, and medical devices.
-
Biocompatibility: Titanium is known for its excellent biocompatibility, making it ideal for use in medical implants and prosthetics. The anodized layer further enhances the biocompatibility of titanium by creating an inert surface that does not react with body tissues. This property makes anodized titanium widely used in the medical industry, especially in the creation of implants, surgical instruments, and dental devices.
-
Increased Electrical Insulation: The anodized titanium surface acts as an insulating layer, making it useful for electrical and electronic components where electrical conductivity must be minimized.
-
Environmental Benefits: Anodizing is an environmentally friendly process, as it does not require hazardous chemicals or produce toxic byproducts. Unlike other coating methods, anodizing is a dry process and does not generate harmful waste, making it a sustainable option for surface enhancement.
-
Cost-Effectiveness: Compared to other surface treatments like painting or plating, anodizing is relatively cost-effective. The process is efficient, and the resulting surface is highly durable, reducing the need for frequent maintenance or re-coating.
Potential Drawbacks of Titanium Anodizing
While titanium anodizing offers numerous advantages, there are also some potential drawbacks to consider:
-
Limited Thickness Control: While anodizing can increase the thickness of the oxide layer, the process may not always provide precise control over the layer thickness. In some cases, achieving uniform color or specific thickness requirements can be challenging.
-
Surface Preparation: Proper surface preparation is crucial to achieving the desired anodized finish. Titanium parts need to be thoroughly cleaned and free of contaminants, such as oils, oxides, or residues, before anodizing. Inadequate preparation can lead to poor adhesion of the oxide layer, affecting the quality of the final product.
-
Color Limitations: The color produced by anodizing is limited by the thickness of the oxide layer. While a wide range of colors can be achieved, certain colors, such as red or black, are difficult to produce consistently using standard anodizing processes.
-
Post-Anodizing Treatments: In some cases, additional treatments, such as sealing or coating, may be required after anodizing to further enhance the durability or appearance of the surface. For example, sealing the anodized layer can improve its corrosion resistance and color stability.
Applications of Titanium Anodizing
Titanium anodizing is used in various industries, including aerospace, medical, automotive, jewelry, and consumer electronics. Below are some of the key applications of anodized titanium:
-
Aerospace: Titanium is widely used in the aerospace industry due to its high strength, low weight, and corrosion resistance. Anodized titanium parts are used in aircraft components, landing gears, engine parts, and other critical systems that require durable, corrosion-resistant materials.
-
Medical Devices: Titanium’s biocompatibility makes it ideal for medical implants and prosthetics. Anodized titanium is used in dental implants, surgical instruments, joint replacements, and pacemaker casings. The anodized surface provides additional protection against corrosion and enhances the longevity of these medical devices.
-
Jewelry and Fashion: One of the most visually striking applications of anodizing is in the creation of colorful titanium jewelry. The ability to produce vibrant, durable colors has made anodized titanium a popular choice in the jewelry industry for rings, necklaces, bracelets, and other accessories.
-
Automotive: Titanium components in the automotive industry benefit from anodizing due to the increased resistance to wear and corrosion. Anodized titanium parts are used in exhaust systems, suspension components, and engine parts, where durability and resistance to extreme conditions are paramount.
-
Electronics: Titanium anodizing is used in electronics for creating insulating surfaces on components like connectors, fasteners, and housings. The anodized layer helps to prevent electrical conductivity and corrosion, ensuring the longevity and reliability of electronic devices.
-
Art and Design: The aesthetic appeal of anodized titanium has led to its use in various artistic and design applications. Sculptures, decorative panels, and architectural elements can be anodized to achieve a wide range of colors and finishes.
Conclusion
Titanium anodizing is a versatile and effective process that not only improves the material's durability but also enhances its aesthetic appeal. By increasing the thickness of the natural oxide layer on titanium, anodizing improves corrosion resistance, wear resistance, and biocompatibility, making it ideal for critical applications in aerospace, medical devices, and other high-performance industries. Whether for functional or decorative purposes, anodized titanium continues to play a key role in various sectors, offering both practical benefits and striking visual effects.
Reprint Statement: If there are no special instructions, all articles on this site are original. Please indicate the source for reprinting:https://www.cncmachiningptj.com/,thanks!
PTJ® provides a full range of Custom Precision cnc machining china services.ISO 9001:2015 &AS-9100 certified. 3, 4 and 5-axis rapid precision CNC machining services including milling, turning to customer specifications,Capable of metal & plastic machined parts with +/-0.005 mm tolerance.Secondary services include CNC and conventional grinding, drilling,die casting,sheet metal and stamping.Providing prototypes, full production runs, technical support and full inspection.Serves the automotive, aerospace, mold&fixture,led lighting,medical,bicycle, and consumer electronics industries. On-time delivery.Tell us a little about your project's budget and expected delivery time. We will strategize with you to provide the most cost-effective services to help you reach your target,Welcome to Contact us ( sales@pintejin.com ) directly for your new project.
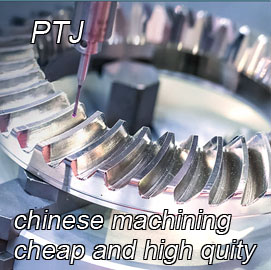
- 5 Axis Machining
- Cnc Milling
- Cnc Turning
- Machining Industries
- Machining Process
- Surface Treatment
- Metal Machining
- Plastic Machining
- Powder Metallurgy Mold
- Die Casting
- Parts Gallery
- Auto Metal Parts
- Machinery Parts
- LED Heatsink
- Building Parts
- Mobile Parts
- Medical Parts
- Electronic Parts
- Tailored Machining
- Bicycle Parts
- Aluminum Machining
- Titanium Machining
- Stainless Steel Machining
- Copper Machining
- Brass Machining
- Super Alloy Machining
- Peek Machining
- UHMW Machining
- Unilate Machining
- PA6 Machining
- PPS Machining
- Teflon Machining
- Inconel Machining
- Tool Steel Machining
- More Material