Machining Tools: From Basics to Advanced
Machining tools are essential components in the field of manufacturing and precision engineering. These tools are used to shape and form materials, particularly metals, into desired geometries through various mechanical processes such as cutting, drilling, grinding, and turning. Over time, machining tools have evolved, growing more precise, versatile, and capable of handling increasingly complex tasks. This article provides an in-depth exploration of machining tools, starting with fundamental concepts and progressing to more advanced techniques and specialized tools.
1. Overview of Machining Tools
Machining tools are devices that use mechanical energy to remove material from a workpiece. The purpose of machining is typically to achieve specific shapes, finishes, and dimensions, often for components that require high precision. These tools operate on the principle of material removal, which can be achieved by various processes like cutting, grinding, drilling, milling, and turning.
The choice of machining tool depends on the material being worked on, the complexity of the part, the required precision, and the production volume. Common materials processed with machining tools include metals (such as steel, aluminum, and titanium), plastics, ceramics, and composites.
Machining is an essential process in industries like aerospace, automotive, defense, medical devices, and consumer electronics. It enables the production of intricate parts, including gears, shafts, turbines, housings, and engine components.
2. Types of Machining Tools
Machining tools can be broadly categorized based on the processes they are used for. The primary types of machining tools include turning tools, milling tools, drilling tools, grinding tools, and specialized tools like EDM (electrical discharge machining) and CNC machines. Each category of tool is designed for specific operations, and each has its strengths and limitations.
2.1 Turning Tools
Turning tools are used in a lathe machine, which rotates the workpiece while the tool is fed into it to remove material. The primary function of turning is to create cylindrical or conical shapes. Turning can also be used for operations like facing, threading, and boring.
Key types of turning tools include:
- Cutting Tools: These are the most common tools used for material removal in turning operations. They have sharp edges to cut away material from the workpiece.
- Boring Tools: Boring tools are used to enlarge existing holes or create internal features like bores or cavities.
- Threading Tools: Threading tools are specifically designed for cutting threads into a workpiece. These tools can be single-point or multi-point tools, depending on the thread configuration required.
2.2 Milling Tools
Milling tools are used with milling machines to remove material from a workpiece by feeding it into a rotating cutter. The cutter has multiple cutting edges that perform the material removal. Milling is versatile and can produce complex geometries, slots, pockets, and contours in a wide range of materials.
Key types of milling tools include:
- End Mills: These are the most common cutting tools used in milling. They have cutting edges on both the end and the sides, allowing them to cut in multiple directions.
- Face Mills: These are larger milling cutters used for cutting flat surfaces, often with multiple inserts to increase cutting efficiency.
- Ball Nose Mills: These cutters have a rounded profile, which is ideal for creating curved surfaces or intricate details.
- Slab Mills: These are used for heavy-duty cutting and can produce large, flat surfaces.
2.3 Drilling Tools
Drilling tools are used to create round holes in a workpiece. The most common drilling tool is the drill bit, which rotates and cuts into the material. Drilling operations are widely used in manufacturing processes to create holes for fasteners, pipes, and other components.
Key types of drilling tools include:
- Twist Drills: These are the most common type of drill bits, with helical flutes that allow for the removal of chips while drilling.
- Step Drills: These drills have a stepped profile, enabling them to create holes of varying diameters in a single operation.
- Center Drills: These are used to create a small indentation at the start of a hole, ensuring that the drill bit remains centered during drilling operations.
- Reamers: Reamers are used to enlarge or finish a hole to a precise size and smooth surface finish after drilling.
2.4 Grinding Tools
Grinding tools are used to remove small amounts of material to achieve a fine surface finish or to sharpen other tools. Grinding is generally used for finishing operations after rough machining.
Key types of grinding tools include:
- Surface Grinding Wheels: These are used to grind flat surfaces and achieve high levels of precision.
- Cylindrical Grinding Wheels: These are used for grinding cylindrical shapes, both internally and externally.
- Centerless Grinding Wheels: These wheels are used in centerless grinders to grind workpieces without the need for clamping.
- Diamond Grinding Wheels: These are used for grinding hard materials and achieving extremely fine finishes.
2.5 EDM (Electrical Discharge Machining)
Electrical Discharge Machining (EDM) is a process where material is removed from a workpiece by a series of rapidly recurring electrical discharges between an electrode and the workpiece. The EDM process is highly effective for working with hard metals, alloys, and intricate shapes that are difficult to achieve with traditional machining tools.
Key types of EDM tools include:
- Wire EDM: In this process, a thin wire serves as the electrode, and material is removed through continuous electrical discharges. Wire EDM is often used for cutting intricate profiles and shapes.
- Sinker EDM: This process uses a shaped electrode that sinks into the workpiece to form complex cavities and features.
- Hole Drilling EDM: Used for drilling small holes with high precision in hard materials.
3. Basic Principles of Machining Tool Operation
The fundamental principle behind machining tools is the removal of material from a workpiece to shape it according to specific requirements. The process is generally characterized by the following parameters:
- Cutting Speed: This is the speed at which the cutting tool moves relative to the workpiece. The cutting speed affects the heat generated during machining and, ultimately, the quality of the surface finish.
- Feed Rate: The feed rate refers to the speed at which the cutting tool moves into the workpiece in the direction of the cutting motion. It directly influences the depth of cut and the efficiency of the machining process.
- Depth of Cut: The depth of cut refers to how much material is removed in a single pass of the tool. Larger depths of cut typically result in higher material removal rates but may require higher tool power and lead to more tool wear.
- Cutting Force: This is the force exerted by the tool on the workpiece to remove material. It depends on factors such as cutting speed, feed rate, and tool geometry.
4. Tool Materials
The material from which machining tools are made plays a critical role in their performance. Tool materials need to withstand high temperatures, wear, and corrosion during the machining process.
Common tool materials include:
- High-Speed Steel (HSS): HSS is one of the most common materials used for cutting tools due to its ability to maintain hardness even at high temperatures. It is used for drills, taps, and end mills.
- Carbide: Tungsten carbide tools are known for their hardness and wear resistance, making them ideal for high-speed machining of tough materials. Carbide tools are used in CNC machines and turning operations.
- Ceramics: Ceramic tools are used for high-temperature applications and for machining hard materials like cast iron and heat-treated steels.
- Cobalt Alloys: Cobalt-based tool steels are known for their ability to retain hardness at high temperatures and are used for cutting tools that operate at elevated speeds.
5. Advanced Machining Tools and Technologies
As machining technology continues to evolve, advanced tools and methods have emerged to meet the demands of more precise and efficient manufacturing.
5.1 CNC (Computer Numerical Control) Machines
CNC machines represent a significant advancement in machining technology. These machines use computerized controls to operate the machining tool automatically, increasing precision, repeatability, and speed. CNC machining includes a wide range of operations, including milling, turning, and drilling.
CNC machines are equipped with multi-axis capabilities, which allow for more complex part geometries and precise movements. They are used extensively in industries like aerospace and medical device manufacturing.
5.2 Additive Manufacturing Tools
Additive manufacturing (AM) technologies, such as 3D printing, are considered the opposite of traditional machining. AM involves the layer-by-layer addition of material to create a part, rather than removing material. Some advanced machining centers combine subtractive and additive processes to create hybrid solutions for manufacturing complex parts.
5.3 Laser Cutting and Laser Machining
Laser cutting uses focused laser beams to cut or etch materials. The high precision and ability to cut through various materials make it a valuable tool for industries requiring intricate patterns or precise cuts. Laser machining includes drilling, welding, and engraving, with applications in aerospace, electronics, and medical device manufacturing.
5.4 Water Jet Cutting
Water jet cutting uses a high-pressure stream of water, sometimes mixed with abrasive materials, to cut through a variety of materials, including metals, plastics, and ceramics. Water jet cutting offers advantages like reduced thermal distortion and the ability to cut through thicker materials without compromising material integrity.
5.5 Hybrid Machining Tools
Hybrid machining tools combine traditional machining methods with newer technologies. For instance, a hybrid machine may combine laser cutting with milling or EDM processes, allowing manufacturers to achieve higher precision in parts with complex geometries. Hybrid systems increase flexibility and reduce the need for multiple setups.
6. Conclusion
Machining tools are indispensable to the manufacturing industry, playing a crucial role in shaping the world’s most complex and precise components. From traditional tools like lathes and milling machines to advanced technologies such as CNC, EDM, and hybrid machining systems, the diversity of machining tools ensures that manufacturers can meet the ever-growing demands of innovation and precision. The ongoing development of machining technologies continues to push the boundaries of what is possible, enabling the production of highly sophisticated and customized parts across a wide range of industries.
Whether for small-scale precision parts or large-volume production runs, machining tools remain central to the global manufacturing landscape, driving progress and fostering innovation in countless applications.
Reprint Statement: If there are no special instructions, all articles on this site are original. Please indicate the source for reprinting:https://www.cncmachiningptj.com/,thanks!
3, 4 and 5-axis precision CNC machining services for aluminum machining, beryllium, carbon steel, magnesium, titanium machining, Inconel, platinum, superalloy, acetal, polycarbonate, fiberglass, graphite and wood. Capable of machining parts up to 98 in. turning dia. and +/-0.001 in. straightness tolerance. Processes include milling, turning, drilling, boring, threading, tapping, forming, knurling, counterboring, countersinking, reaming and laser cutting. Secondary services such as assembly, centerless grinding, heat treating, plating and welding. Prototype and low to high volume production offered with maximum 50,000 units. Suitable for fluid power, pneumatics, hydraulics and valve applications. Serves the aerospace, aircraft, military, medical and defense industries.PTJ will strategize with you to provide the most cost-effective services to help you reach your target,Welcome to Contact us ( sales@pintejin.com ) directly for your new project.
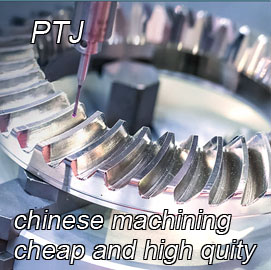
- 5 Axis Machining
- Cnc Milling
- Cnc Turning
- Machining Industries
- Machining Process
- Surface Treatment
- Metal Machining
- Plastic Machining
- Powder Metallurgy Mold
- Die Casting
- Parts Gallery
- Auto Metal Parts
- Machinery Parts
- LED Heatsink
- Building Parts
- Mobile Parts
- Medical Parts
- Electronic Parts
- Tailored Machining
- Bicycle Parts
- Aluminum Machining
- Titanium Machining
- Stainless Steel Machining
- Copper Machining
- Brass Machining
- Super Alloy Machining
- Peek Machining
- UHMW Machining
- Unilate Machining
- PA6 Machining
- PPS Machining
- Teflon Machining
- Inconel Machining
- Tool Steel Machining
- More Material