What is Nickel Alloy: Properties, Composition, and Uses
Nickel alloys are a broad category of metallic materials composed predominantly of nickel, often combined with other elements to enhance their properties and extend their applicability across various industries. Nickel itself is a transition metal, symbolized as Ni on the periodic table, and possesses a range of unique physical and chemical characteristics that make it suitable for alloying. This article explores the properties, composition, and uses of nickel alloys in detail, aiming to provide a comprehensive understanding of these versatile materials.
Properties of Nickel Alloys
Nickel alloys exhibit a range of properties that make them valuable in numerous applications. Key properties include:
-
Corrosion Resistance: One of the standout features of nickel alloys is their exceptional resistance to corrosion. This is largely due to the formation of a passive oxide layer on their surface, which protects against aggressive environments. Nickel alloys are particularly effective in resisting oxidation, sulfidation, and various forms of pitting and crevice corrosion.
-
Mechanical Strength: Nickel alloys possess high tensile strength and yield strength, making them suitable for applications that require materials to withstand significant loads. The addition of elements such as chromium, molybdenum, and titanium can further enhance the mechanical properties of the alloy.
-
Ductility and Malleability: Nickel alloys maintain good ductility, allowing them to be formed and shaped without cracking. This property is particularly important in applications where components must be fabricated into complex shapes.
-
Temperature Resistance: Many nickel alloys can perform well at elevated temperatures, making them ideal for applications in high-heat environments. They retain their mechanical properties and resist thermal fatigue, which is crucial in industries like aerospace and power generation.
-
Magnetic Properties: Certain nickel alloys possess unique magnetic properties, including ferromagnetism. This characteristic can be manipulated for applications in electrical and electronic components, including transformers and inductors.
-
Weldability: Nickel alloys generally have good weldability, which allows for the construction of complex structures without compromising the integrity of the material. Special care may be required in selecting welding processes and filler materials to ensure compatibility.
Composition of Nickel Alloys
Nickel alloys are typically categorized based on their composition and the primary alloying elements used. The most common types of nickel alloys include:
-
Monel: Composed primarily of nickel and copper, Monel alloys are known for their resistance to seawater and other corrosive environments. They often contain small amounts of iron, manganese, and silicon, enhancing their mechanical properties.
-
Inconel: Inconel is a family of nickel-chromium alloys that provide excellent oxidation and corrosion resistance at high temperatures. The high nickel content, along with the addition of chromium and sometimes molybdenum, enhances the material’s ability to withstand extreme environments.
-
Invar: This nickel-iron alloy is notable for its very low coefficient of thermal expansion. The composition typically includes around 36% nickel and is primarily used in applications where dimensional stability with temperature changes is critical.
-
Hastelloy: Hastelloy is a group of high-performance nickel alloys designed for severe environments. Composed of nickel, chromium, and molybdenum, these alloys are resistant to pitting and stress corrosion cracking, making them ideal for chemical processing applications.
-
Nickel-Copper Alloys: These alloys, such as CuproNickel, are known for their resistance to corrosion and biofouling, particularly in marine environments. They contain nickel and copper in varying proportions, often supplemented with iron and manganese.
-
Nickel-Chromium Alloys: These alloys combine nickel and chromium in varying ratios to enhance resistance to oxidation and high-temperature corrosion. They are widely used in turbine components and other high-stress applications.
The exact composition of nickel alloys can vary significantly depending on the desired properties and intended applications. By adjusting the concentrations of alloying elements, manufacturers can tailor the material's performance to meet specific requirements.
Uses of Nickel Alloys
Nickel alloys are employed across a diverse range of industries due to their unique properties. Some key applications include:
-
Aerospace Industry: Nickel alloys are extensively used in aerospace applications due to their high strength-to-weight ratio and resistance to extreme temperatures. Components such as turbine blades, combustion chambers, and exhaust systems often utilize superalloys, which are nickel-based.
-
Chemical Processing: The chemical industry employs nickel alloys for their resistance to corrosion and high temperatures. They are used in reactors, heat exchangers, and piping systems, particularly when handling aggressive chemicals.
-
Marine Applications: Nickel-copper alloys are commonly used in marine environments, where they resist seawater corrosion. Applications include shipbuilding, offshore oil drilling, and marine hardware.
-
Oil and Gas: Nickel alloys are critical in the oil and gas industry, especially in downhole applications where corrosion resistance and strength are paramount. They are used in valves, pumps, and piping systems in both upstream and downstream processes.
-
Power Generation: Nickel alloys are used in nuclear reactors and fossil fuel power plants, where they must withstand high temperatures and corrosive environments. They are often found in components like steam generators, heat exchangers, and turbine blades.
-
Electrical and Electronics: Nickel alloys with specific magnetic properties are used in electrical components, including transformers, inductors, and electrical contacts. Their conductivity and resistance to thermal expansion make them suitable for high-performance applications.
-
Medical Devices: The biocompatibility and corrosion resistance of nickel alloys make them ideal for medical implants and devices. They are often used in surgical instruments, stents, and prosthetics.
-
Consumer Products: Nickel alloys are also present in various consumer goods, including jewelry, watches, and kitchen utensils. Their aesthetic appeal, along with durability and resistance to tarnish, makes them popular in the manufacturing of high-quality products.
Conclusion
Nickel alloys are a diverse and essential category of materials that play a critical role in various industries. Their unique combination of properties, including corrosion resistance, mechanical strength, and high-temperature performance, makes them invaluable in demanding applications. By understanding the composition and characteristics of these alloys, engineers and designers can make informed decisions about material selection to optimize performance and ensure longevity in their products. As technology advances, the development of new nickel alloys and innovations in processing techniques will continue to expand their applications, further solidifying their importance in modern engineering and manufacturing.
Through this exploration of nickel alloys, their properties, composition, and uses, it is evident that these materials are integral to many sectors, contributing significantly to advancements in technology and industry. The ongoing research and development in the field of metallurgy will undoubtedly lead to new discoveries and enhancements in the performance of nickel alloys, ensuring their relevance for years to come.
3, 4 and 5-axis precision CNC machining services for aluminum machining, beryllium, carbon steel, magnesium, titanium machining, Inconel, platinum, superalloy, acetal, polycarbonate, fiberglass, graphite and wood. Capable of machining parts up to 98 in. turning dia. and +/-0.001 in. straightness tolerance. Processes include milling, turning, drilling, boring, threading, tapping, forming, knurling, counterboring, countersinking, reaming and laser cutting. Secondary services such as assembly, centerless grinding, heat treating, plating and welding. Prototype and low to high volume production offered with maximum 50,000 units. Suitable for fluid power, pneumatics, hydraulics and valve applications. Serves the aerospace, aircraft, military, medical and defense industries.PTJ will strategize with you to provide the most cost-effective services to help you reach your target,Welcome to Contact us ( sales@pintejin.com ) directly for your new project.
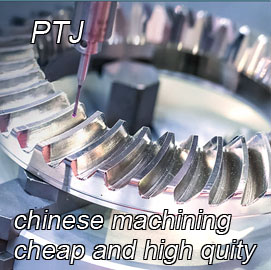
- 5 Axis Machining
- Cnc Milling
- Cnc Turning
- Machining Industries
- Machining Process
- Surface Treatment
- Metal Machining
- Plastic Machining
- Powder Metallurgy Mold
- Die Casting
- Parts Gallery
- Auto Metal Parts
- Machinery Parts
- LED Heatsink
- Building Parts
- Mobile Parts
- Medical Parts
- Electronic Parts
- Tailored Machining
- Bicycle Parts
- Aluminum Machining
- Titanium Machining
- Stainless Steel Machining
- Copper Machining
- Brass Machining
- Super Alloy Machining
- Peek Machining
- UHMW Machining
- Unilate Machining
- PA6 Machining
- PPS Machining
- Teflon Machining
- Inconel Machining
- Tool Steel Machining
- More Material